Alodine coating: an indispensable surface treatment technology
One of the main causes of damage and failure of precision mechanical parts today is corrosion and surface damage. The application of alodine coating can solve this problem. This oxide film can provide unparalleled protection against corrosion, wear and tear. The application of alodine coating improves the durability and service life of the product and simplifies the manufacturing process with its efficiency and simplicity. This article will explore the surface treatment technology, coating types, application areas and advantages of alodine coating.
1.What is alodine coating?
Alodine coating refers to the technology of forming an oxide film on the surface of aluminum and aluminum alloys through various oxidation treatment methods. This technology can not only improve the wear resistance and corrosion resistance of aluminum, but also improve its insulation and decorative properties. This technology mainly includes the following methods:
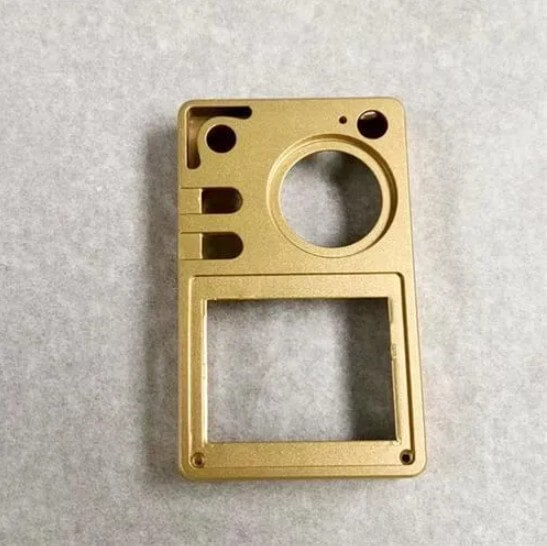
(1) Natural oxidation:
Aluminum will naturally form a thin oxide film in the air with a thickness of about 0.01 to 0.1 microns. This film is porous, soft, and has a certain adsorption capacity, but its wear resistance and corrosion resistance are poor.
(2) Chemical oxidation:
Aluminum is immersed in a specific chemical solution for treatment to form an oxide film. Chemical oxidation equipment is simple, easy to operate and has a wide range of applications. The properties of the solution can be divided into alkaline and acidic oxidation, and the properties of the film layer can be divided into oxide film, phosphate film, chromate film, etc.
(3) Electrochemical oxidation (anodization):
The aluminum product is placed in the electrolyte as an anode, and an oxide film is formed on its surface under the action of an external current. The anodized film is thicker and has high hardness, and has good heat resistance, insulation and corrosion resistance. Depending on the electrolyte, anodization can be divided into sulfuric acid anodization, chromic acid anodization, oxalic acid anodization, etc.
(4) Hard anodization:
A special anodizing method, the resulting oxide film thickness can reach 60 to 200 microns, with extremely high hardness, suitable for occasions requiring high wear resistance.
(5) Porcelain anodizing:
Through specific process conditions, a porcelain-like oxide film is formed on the aluminum surface, which has good decorative and functional properties.
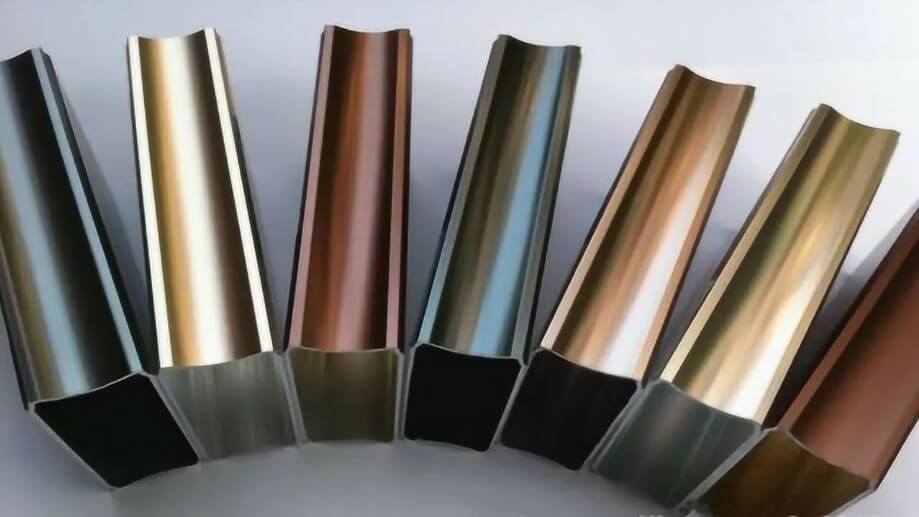
2.Coating types of aluminum oxide film
The performance of aluminum oxide film can be significantly enhanced through different coating treatments. The following are several common types of alodine coatings:
(1) Fluorocarbon coating (FC)
Features: Excellent weather resistance and corrosion resistance, and can resist erosion by ultraviolet rays, acid rain, salt spray, etc.
Application: Mainly used for outdoor curtain walls, with a service life of more than 10-20 years.
(2) Polyester coating (PET)
Features: Rich and bright colors, good surface flatness, and certain anti-ultraviolet and anti-corrosion capabilities.
Application: Suitable for indoor curtain walls and ceilings, etc., with a service life of 3-5 years.
(3) Acrylic coating (AC)
Features: Good color retention, gloss retention and anti-pollution, excellent weather resistance, and strong metal adhesion.
Application: Suitable for decorative powder coatings, room temperature curing, and easy construction.
(4) Ceramic coating (CC)
Features: high hardness, good scratch resistance, easy to clean, good weather resistance, and a ceramic-like coating is formed by curing at low temperature.
Application: Commonly used in places with high wear resistance and easy cleaning.
(5) Anodized film (AF)
Features: thicker than natural oxide film, strong hardness, good anti-fouling, excellent wear resistance and corrosion resistance, strong insulation and decorative properties.
Application: Suitable for places requiring high wear resistance and high corrosion resistance, but the price is relatively expensive.
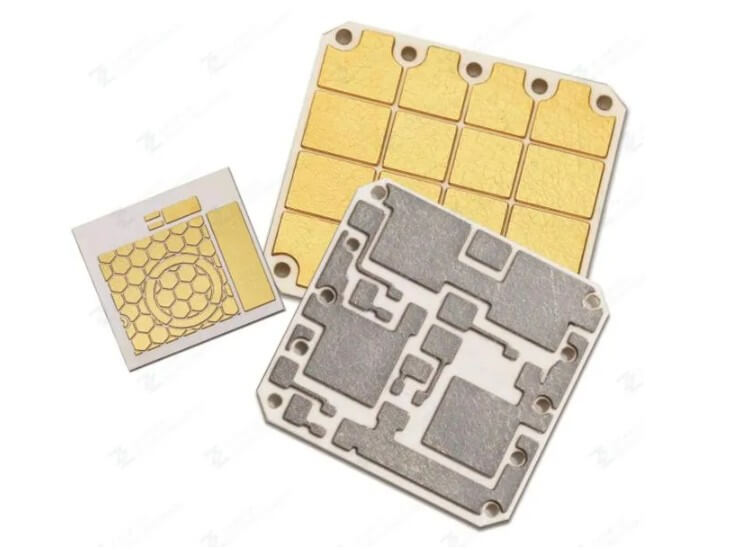
Summary:
These alodine coatings not only improve the aesthetics of aluminum, but more importantly, extend its service life, making it perform well under different environmental conditions. It is widely used in construction, aerospace, automobile, electronics and other fields.
3.What are the benefits of alodine coatings?
Alodine coatings significantly improve the performance of materials by forming a hard oxide film on the surface of aluminum and are widely used in many fields. The following are the main application benefits of alodine coating:
(1) Enhanced corrosion resistance:
Alodine coating forms a uniform and dense oxide film on the surface of aluminum, which effectively isolates air and corrosive media, greatly improving the corrosion resistance of aluminum. This allows aluminum products to maintain stable performance in various harsh environments and extend their service life.
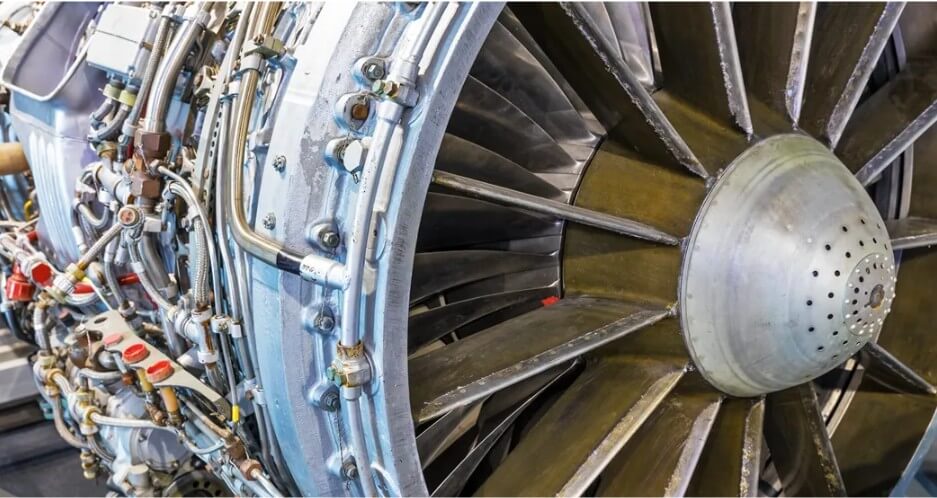
(2) Improved wear resistance:
The high hardness of alodine coating makes it excellent in improving the wear resistance of materials. Whether it is mechanical wear or friction, alodine coating can effectively reduce material loss and extend the service life of parts. For example, in automobile braking systems, alodine coating is widely used in the surface treatment of brake discs and brake pads to improve their wear resistance and braking performance.
(3) Enhanced insulation:
Aluminum itself has good conductivity, but insulation is required in some application scenarios. The oxide film formed by alodine coating is not conductive, which can effectively improve the insulation performance of aluminum and ensure the safe operation of electronic components.
(4) Increase surface hardness:
After aluminum oxidation treatment, the hardness of the oxide film formed on its surface is significantly improved, reaching 200-400HV, which is much higher than the hardness of the aluminum itself. This hard oxide film effectively protects the surface of the aluminum, increases the overall hardness and strength of the material, extends the service life of the parts and improves their stability.
(5) High temperature resistance:
Alodine coating has excellent high temperature resistance. When exposed to high temperature environment, the oxide layer can form a protective layer, effectively inhibiting the combustion of aluminum, so that it can continue to bear safe loads. This feature enables it to perform well in high temperature environments such as aerospace and automobile engines.
(6) Improve decorativeness:
The surface of alodine coating has a porous structure, which is easy to absorb dyes and colored substances. It can be dyed to achieve a variety of colors and patterns, which significantly improves the decorativeness of aluminum products and meets the aesthetic needs of different customers.
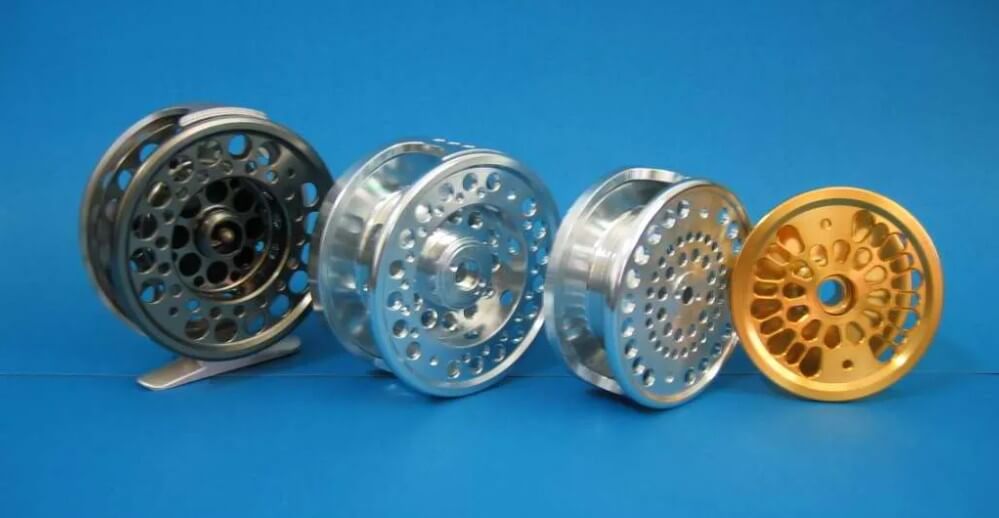
(7) Primer for spray painting:
Some industrial aluminum materials need to be painted. The surface of anodized aluminum materials has a strong adsorption capacity, which can make the coating more uniform and beautiful, and enhance the adhesion and durability of the coating.
4.Related application fields of alodine coatings
(1) Construction industry:
Alodine coatings are commonly used in curtain walls, door and window frames and interior decoration materials in the construction field. This coating is not only beautiful and durable, but also can significantly improve the weather resistance and corrosion resistance of aluminum materials, extending the service life of building materials. The multi-color selection of oxide films also meets the diverse needs of architectural design.
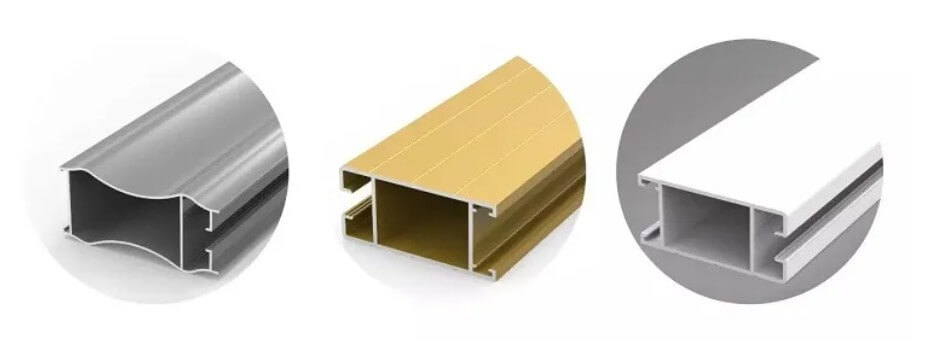
(2) Automobile industry:
In automobile manufacturing, alodine coatings are used in engine parts, wheels and body panels. This coating has excellent wear resistance and high temperature resistance, which helps to improve the service life and reliability of automobile parts, while reducing the overall weight of the vehicle and improving fuel efficiency.
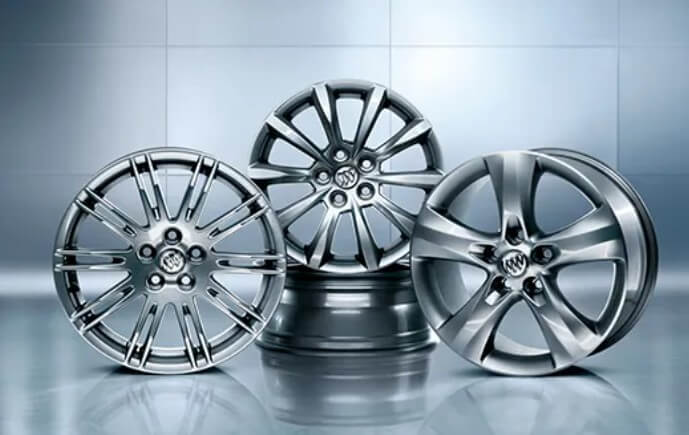
(3) Aerospace industry:
Aerospace vehicles have extremely stringent requirements on materials. Alodine coatings are ideal for manufacturing aircraft and spacecraft due to their light weight, high strength and excellent corrosion resistance. This coating can maintain stability in extreme environments and ensure flight safety.
(4) Electronics industry:
The application of alodine coating in the electronics field is mainly concentrated on radiators, housings and internal structural parts. The good heat dissipation and insulation properties of the coating help improve the stability and service life of electronic products. At the same time, its beautiful surface can also enhance the market competitiveness of products.
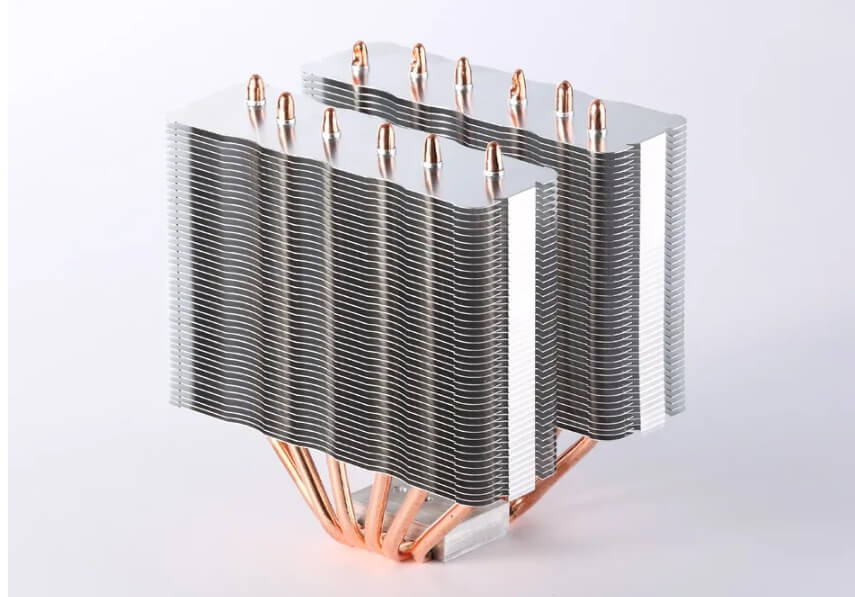
(5) Medical device field:
Because alodine coating has good biocompatibility and corrosion resistance, it has been widely used in the manufacture of medical devices, such as surgical instruments and prostheses. This coating not only ensures the safety and durability of medical devices, but also improves the recognition of devices through coloring.
5.What is the difference between aluminum chemical oxidation and aluminum anodizing? How to choose between the two?
(1) Difference analysis
Aluminum chemical oxidation and aluminum anodizing are two common aluminum surface treatment methods. They have significant differences in principles, film properties, and application fields. The following is a detailed comparison of the two methods:
Comparison Item | Chemical Oxidation | Anodic Oxidation |
Process | Chemical reaction without electricity | Electrochemical reaction under high voltage |
Time Required | Short, typically seconds | Longer, typically minutes |
Membrane Thickness | Thin, 0.01 – 0.15 μm | Thicker, 5 – 20 μm (up to 60 – 200 μm for hard anodic oxidation) |
Hardness | Soft | Higher, depending on alloy and process |
Wear Resistance | Poor | Better |
Corrosion Resistance | Lower | Higher |
Conductivity | Conductive (due to thin film) | Non – conductive (insulating oxide layer) |
Porosity | Less porous | Porous, with good adsorption capacity |
Treatment Media | Chemical solutions | Electrolytic solutions |
Application | Primarily for decorative or thin protection layers | Wide range of applications, including high durability and protection |
Post – Treatment | Usually not required | Sealing treatment often performed to enhance properties |
(2) How to choose
When choosing between aluminum chemical oxidation and aluminum anodizing, it is necessary to comprehensively consider factors such as specific application requirements, cost budget and processing efficiency:
1) Film performance requirements:
If higher film hardness, wear resistance and corrosion resistance are required, aluminum anodizing should be selected. If the film thickness and hardness requirements are not high, but good conductivity needs to be maintained, aluminum chemical oxidation is more suitable.
2) Processing efficiency and cost:
Aluminum chemical oxidation has a short processing time and low cost, which is suitable for large-scale production. Aluminum anodizing has a longer processing time and higher cost, but can provide better film performance.
3) Application areas:
In the fields of construction, aviation, electronics, etc., higher corrosion resistance and decorative properties are usually required, so aluminum anodizing is more widely used. In some special occasions, such as aluminum products that require conductivity, aluminum chemical oxidation is more suitable.
5.Summary
Alodine coatings are essential for CNC machined parts because they can provide a corrosion protection layer without changing the precise dimensions of the part. This is particularly important in applications where strict tolerances must be maintained. Additionally, the alodine coating improves paint adhesion and maintains electrical conductivity, making it ideal for components that require both durability and high performance in demanding environments.
2 Comments