Aluminum Alloy Surface Treatment: Comprehensive Guide to Common Processes
Aluminum alloys are easy to process, and there are many ways to treat aluminum alloy surface treatment , with good visual effects, and a wide range of applications. Different surface treatment processes can make the product present different textures. So this article will introduce the common processes for aluminum alloy surface treatment.
Overview of surface treatment
Surface treatment is a process that forms a protective layer on the surface of the product to protect the body after mechanical and chemical treatment. It can reach a stable state in nature, increase the corrosion resistance of the body and increase the beauty of the product, thereby enhancing the value of the product.
The process of surface treatment includes pre-treatment, film formation, and post-film treatment. Packaging, warehousing, and shipping processes, among which pre-treatment includes mechanical treatment and chemical treatment.
Mechanical treatment includes spraying, shot blasting, grinding, polishing, waxing and other processes. The purpose of mechanical treatment is to remove unevenness on the surface of the product and remedy other surface defects.
Chemical treatment removes oil and rust from the surface of the product and forms a layer that allows the film-forming material to better combine or chemically react with the active metal body, ensuring that the coating has a stable state and increasing the bonding strength of the protective layer, thereby achieving the function of protecting the body.
Aluminum alloy surface treatment
Common surface treatments for aluminum alloys include spraying, anodizing, sandblasting, passivation, polishing, coloring and oxide film treatment.
1.Aluminum alloy surface treatment process 1: chromization
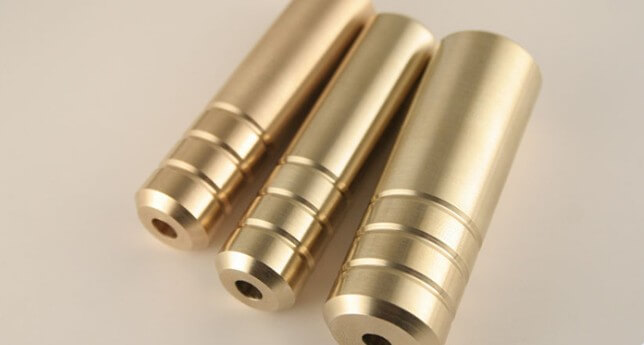
(1) Function
Chromization will form a layer of chemical conversion film on the surface of the product with a thickness of 0.5-4um. This chemical conversion film has good adsorption and is mainly used as a coating base. The chemical conversion film has good conductivity and is the best option for electronic products, such as conductive strips in mobile phone batteries, magnetoelectric equipment, etc.
(2) Chromization process flow:
Degreasing -> Aluminum acid degreasing -> Chromization -> Packaging -> Storage
Chromization is suitable for aluminum and aluminum alloys, magnesium and magnesium alloys.
2.Aluminum alloy surface treatment process 2: Anodizing
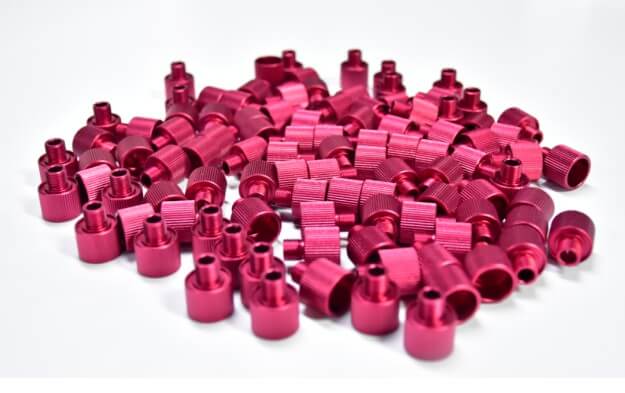
(1) Function
Anodizing can form a uniform and dense oxide layer on the surface of the product. This film can make the surface hardness of the product reach (200-300HV). And hard anodizing, the surface hardness of the product can even reach 400-1200HV.
(2) Use
Hard anodizing is an indispensable surface treatment process for oil cylinders and transmissions. In addition, this product has excellent wear resistance and can be used as a necessary process for aviation and aerospace related products.
(3) Anodizing process flow
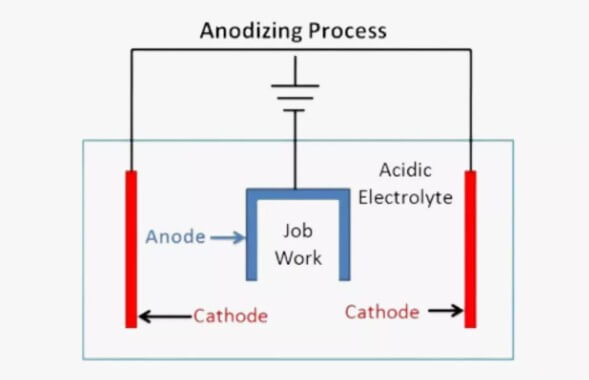
Single color, gradient color: polishing/sandblasting/brushing → degreasing → anodizing → neutralization → dyeing → sealing → drying
Dual color: ① polishing/sandblasting/brushing → degreasing → masking → anodizing 1 → anodizing 2 → sealing → drying
② polishing/sandblasting/brushing → degreasing → anodizing 1 → laser engraving → anodizing 2 → sealing → drying
(4) Advantages
1) Improve strength;
2) Achieve any color except white;
3) Achieve nickel-free sealing, meeting the requirement for nickel-free.
(5) Aluminum alloy anodizing composition, performance and application
•1) 1000 series (pure aluminum)
Composition: This series of alloys contains 99% aluminum and impurities such as iron and silicon.
Performance: High conductivity, excellent corrosion resistance and flexibility. Anodizing pure aluminum alloys produces a transparent or translucent coating and improves its hardness and corrosion resistance.
Application: Suitable for manufacturing electrical components (such as connectors, wiring), nameplates and signs.
•2) 2000 Series (Aluminum-Copper Alloys)
Composition: 2000 series alloys contain aluminum and copper (2% to 7%). They may also contain small amounts of manganese and magnesium.
Properties; The alloy is strong, machinable and has moderate corrosion resistance. Anodizing the alloy will improve corrosion and wear resistance.
Application: It provides a better decorative finish and is therefore suitable for architectural and automotive applications.
•3) 3000 Series (Aluminum-Manganese Alloys)
Composition: This series contains aluminum and manganese (1% to 1.5%).
Properties: They have good formability, moderate strength and excellent corrosion resistance.
Anodizing the parts enhances corrosion resistance.
Application: Better suited for manufacturing parts such as heat exchangers, building panels and facades.
•4) 5000 Series (Aluminum-Magnesium Alloys)
Composition: This series of alloys consists of aluminum and magnesium (2% to 6%).
Properties: They have a high strength-to-weight ratio and excellent corrosion resistance. Anodizing the parts will improve their corrosion resistance and durability,
Applications: They are suitable for manufacturing marine parts such as building window frames and ship hulls.
•5) 6000 Series (Aluminum-Magnesium-Silicon Alloys)
Composition: They are alloys of aluminum, magnesium (0.6% to 1.2%) and silicon (0.4% to 1.2%).
Properties: They have good extrusion properties, high strength-to-weight ratio and excellent corrosion resistance.
Applications: Common applications are building profiles such as window frames, door frames, and automotive parts such as body panels and wheels.
•6) 7000 Series (Aluminum-Zinc Alloys)
Composition: 7000 alloys are a mixture of aluminum and zinc (5% to 8%).
Performance: They have high strength-to-weight ratio, fatigue resistance and corrosion resistance. Anodizing can improve corrosion resistance and enhance decoration.
Application: Surface finish in aerospace applications (such as aircraft skins and structural components).
3.Aluminum alloy surface treatment process three: electroplating
(1) Reasons for using electroplating process for aluminum alloy surface treatment
Aluminum and aluminum alloys have advantages such as good electrical conductivity, fast heat transfer, light specific gravity, and easy molding, but their low hardness, poor wear resistance, easy intergranular corrosion, and difficult welding have disadvantages that affect the scope of use. Therefore, in modern manufacturing, electroplating is used to solve this problem.
(2) Advantages of aluminum electroplating
1) Improve decoration,
2) Improve surface hardness and wear resistance
3) Reduce friction coefficient and improve lubricity.
4) Improve surface conductivity.
5) Improve corrosion resistance
6) Easy to weld
7) Improve bonding strength during hot pressing.
8) Improve reflectivity
9) Repair dimensional tolerance
(3) The process flow of aluminum alloy surface treatment electroplating is
Degreasing->Alkaline etching->Activation->Zinc replacement->Activation->Electroplating (such as nickel, zinc, copper, etc.)->Chrome plating or passivation->Drying.
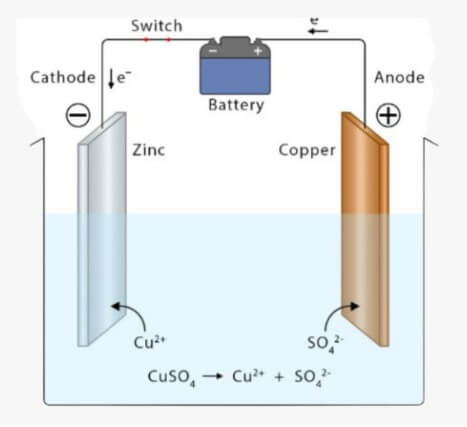
(4) Common types of aluminum electroplating
Nickel plating (pearl nickel, sand nickel, black nickel);
Silver plating (surface silver, thick silver);
Gold plating, zinc plating (color zinc, black zinc, blue zinc);
Copper plating (green drum copper, white copper, alkaline copper, coke copper, acid copper);
Chrome plating (white chrome, hard chrome, black chrome), etc.(5) Precautions for electroplating operation of aluminum alloy surface treatment
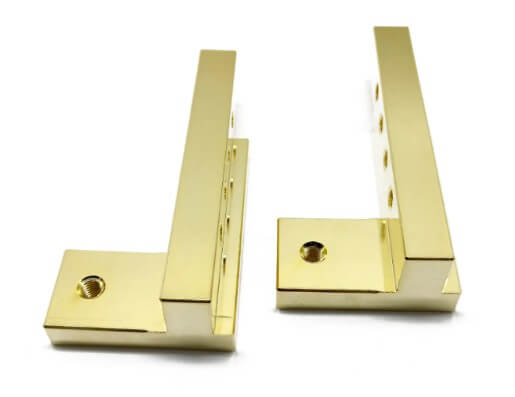
(5) Precautions for electroplating operation of aluminum alloy surface treatment
1) Aluminum alloy should be used as a hanger for electroplating of aluminum parts;
2) Each process after etching of aluminum and aluminum alloy must be carried out quickly, and the interval time between processes should be as short as possible to avoid re-oxidation;
3) The second zinc immersion time should not be too long to avoid over-corrosion;
4) The water washing must be clean;
5) Avoid power failure during the electroplating process.
4.Aluminum alloy surface treatment process four: powder spraying
(1) Function
Powder spraying uses powder spraying equipment (electrostatic spraying machine) to spray powder coating onto the surface of the workpiece. Under the action of static electricity, the powder will be evenly adsorbed on the surface of the workpiece to form a powder coating; the powder coating is leveled and solidified after high-temperature baking to become a final coating with different effects (different types of powder coating effects).
(2) Powder spraying process:
Putting → Electrostatic dust removal → Spraying → Low temperature leveling → Baking
(3) Advantages
1) Rich colors, high gloss and matte optional;
2) Low cost, suitable for architectural furniture products and heat sink shells, etc.;
3) High utilization rate, 100% utilization, environmentally friendly;
4) Strong ability to mask defects;
5) Can imitate wood grain effect.
5.Aluminum alloy surface treatment process five: Sandblasting
(1) Function
Sandblasting is a process that uses compressed air as a power to form a high-speed jet beam to spray the spray material at high speed onto the surface of the workpiece to be treated, so that the appearance or shape of the outer surface of the workpiece surface changes, and obtains a certain degree of cleanliness and different roughness.
(2) Advantages
1) Achieve different reflections or matte.
2) Can clean the tiny burrs on the surface of the workpiece and make the surface of the workpiece smoother and more advanced.
3) The workpiece has high finish, uniform metal color, and beautiful appearance.
6.Aluminum alloy surface treatment process six: polishing
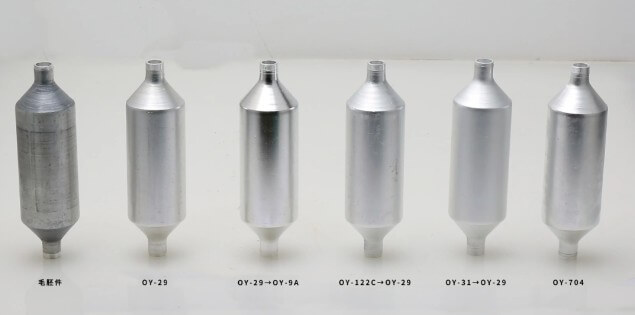
(1) Function
Polishing process mainly reduces the roughness of the metal surface through mechanical polishing or chemical polishing, improves the dimensional accuracy or geometric shape accuracy of the workpiece, and obtains a bright and flat surface.
(2) Classification of polishing process
Polishing process is mainly divided into: mechanical polishing, chemical polishing, and electrolytic polishing. The surface treatment of aluminum alloy using mechanical polishing + electrolytic polishing can be close to the mirror effect of stainless steel, giving people a high-end, simple, fashionable and futuristic feeling.
7.Aluminum alloy surface treatment process seven: electrophoresis
(1) Function
Electrophoresis can make the product present various colors and maintain the metallic luster, while enhancing the surface performance and having good anti-corrosion performance.
(2) Process flow
Pretreatment → electrophoresis → drying
(3) Advantages
1) Rich colors;
2) No metallic texture, can be used with sandblasting, polishing, brushing, etc.;
3) Processing in a liquid environment can achieve aluminum alloy surface treatment with complex structures;
4) Mature technology and mass production.
8.Aluminum alloy surface treatment process eight: brushing
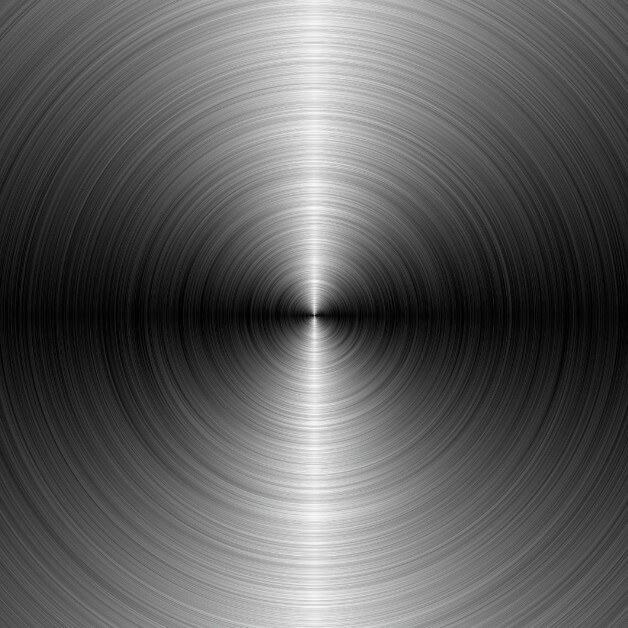
(1) Function
Brushing is a surface treatment method that forms lines on the surface of the workpiece by grinding the product to achieve a decorative effect. Wire drawing can give the metal surface a non-mirror-like metallic luster, and at the same time, wire drawing can also eliminate subtle flaws on the metal surface.
(2) Classification
According to the different lines after wire drawing, it can be divided into: straight wire drawing, random wire drawing, corrugation, and spiral line.
(3) Applications
Aluminum alloy surface treatment wire drawing process is very common in product design, such as notebooks and headphones in electronic products; refrigerators and air purifiers in household products; it is also used in car interiors, and the center console with wire drawing panel can also enhance the quality of the car.
Summary:
The above are common processes for aluminum alloy surface treatment. We have analyzed the functions and advantages of different surface treatment processes, and then we can get the best aluminum alloy surface treatment solution according to your project needs.