Processing Benefits of Aluminum and Titanium
When you think of an excellent combination of material properties for a part, you think of lightness and strength. This is true of aluminum and titanium, of course. Both materials meet other important criteria, such as excellent corrosion and heat resistance. Through 3D printing or precision CNC machining, both metals have proven to be extremely versatile in parts for a wide range of industries.
Both aluminum and titanium are light, but for different reasons. Aluminum has a lower specific gravity (2.7 g/cm3), which means it is much lighter than steel, which is about three times heavier. Although titanium is two-thirds heavier than aluminum, its inherent strength means that less titanium is needed. In fact, only a fraction of titanium is needed to achieve the same physical strength as aluminum. Titanium is used in aircraft engines, for example, and also in spacecraft. Its strength and light weight can reduce fuel costs.
1.Aluminum and Titanium
Since both materials are strong and lightweight, it is important to consider other significant features when deciding which alloy to use to make a part.
1) Strength/Weight
In critical situations where every gram counts but a strong part is still needed, titanium is the first choice. Titanium medical parts, complex satellite components, fixtures and brackets are so successful for this very reason.
2) Cost
Aluminum is the most cost-effective metal to machine or 3D print prototypes. Titanium, while adding cost, can also add value. Lighter parts save fuel in transportation, and secondly, parts made of titanium last longer.
3) Thermal Properties
Aluminum is great for applications that require high thermal conductivity, such as heat sinks. In high-temperature applications, titanium’s high melting point is beneficial for applications that require high heat resistance, such as aircraft engine parts.
4) Corrosion Resistance
Both aluminum and titanium have excellent corrosion resistance. Due to its corrosion resistance and low reactivity, titanium is the most biocompatible metal, making it ideal for medical applications, such as surgical instruments. Ti 6-4 can also withstand salt environments and is often used in marine applications.
2.Applications of Aluminum
Aluminum is everywhere – it is the most common metal on earth. Aluminum forms a thin layer of aluminum oxide when exposed to air, so it basically does not corrode, and its low weight helps prevent parts from acting like anchors. While aluminum does not typically react to acids, it corrodes easily in alkaline environments.
In general, aluminum is used in aircraft and building materials, such as non-load-bearing frame structures. In particular, 6082 is the top choice for bicycle frames, scuba tanks, fishing reels, boats, and vehicle frames. The stronger properties of 7075 make it ideal for plastic and tool molds, as well as aircraft frames. If you are looking for a good conductor of electricity, aluminum is the way to go. It transfers heat optimally, making it an excellent material for heat sinks.
The aluminum alloy AlSi10Mg that we use in our DMLS (Direct Metal Laser Sintering) process also contains silicon and magnesium. It is commonly used for casting and is most similar to the 3000 series alloys in that it contains magnesium as the main alloying element. 3D printed aluminum has better properties than die cast aluminum, but has a lower elongation at break.
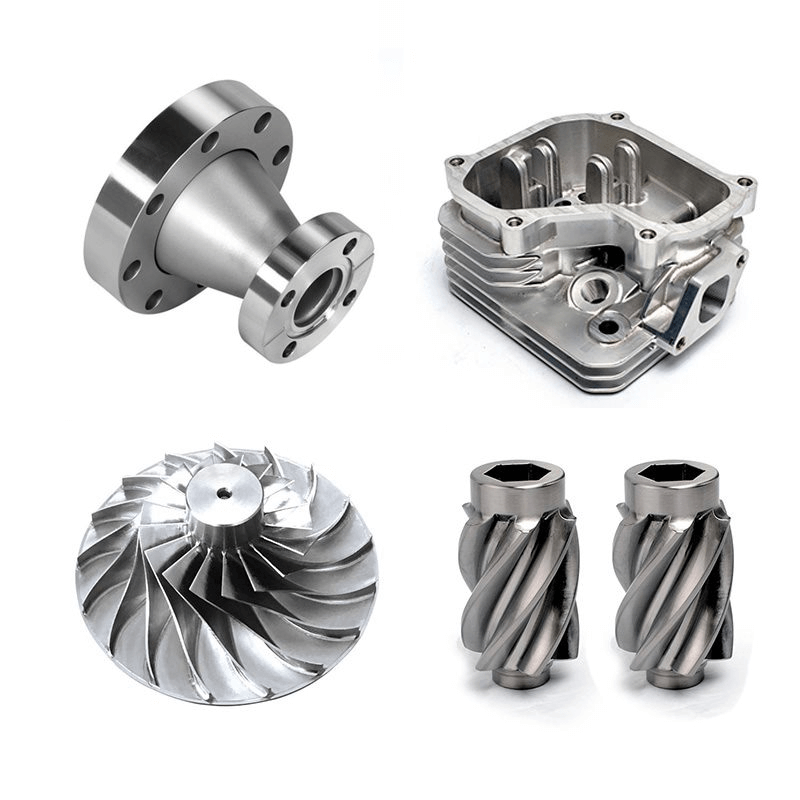
3.Applications of Titanium
Titanium is also one of the most common metals on earth, but it has a high melting point and is difficult to process into a usable product. This is a key reason why it is more expensive than other metals. Parts made with titanium add to the cost because they are difficult to process. Titanium is known for its strength and has a good strength-to-weight ratio. It also has excellent corrosion resistance and is a similarly poor conductor of electricity.
One of the advantages of titanium is its low thermal expansion. Titanium has a melting point of about 1,660 degrees Celsius, so it holds its shape better when heated. Also, titanium does not absorb heat, but reflects it. For this reason, you see titanium in low-e windows, which reflect the sun’s warm infrared rays.
As for appearance, the color of titanium depends on how much it has been altered. Its color ranges from a dull gray in its raw state to a shiny silver in its smooth state. The titanium used in our DMLS process is Ti 6Al4V, better known as Ti 6-4. It has similar mechanical properties to Ti Grade 23 in the annealed state and has excellent tensile strength.
4.Reasons to Machining Aluminum and Titanium
CNC milling and CNC turning are established processes for producing aluminum and titanium parts. These processes are fast – typically producing a part in less than a day – and hold tolerances to +/-0.1 mm. If you need to make rapid prototype parts, aluminum stands out for its low cost and high quality. However, machining is somewhat limited in terms of geometry, so extremely complex designs require a different solution, such as DMLS, no matter which material you choose.
One factor you might not think about when choosing a material is machining waste. While milling away excess material is fine for inexpensive aluminum, it’s not an ideal solution for expensive titanium. For this reason, engineers often choose to prototype in aluminum first and then switch to titanium to produce the part. Aluminum machining is popular in the automotive industry, where lightweighting is key to improving fuel economy and minimizing performance impact.
5.Reasons to 3D Print Aluminum and Titanium
DMLS is an additive manufacturing process. A fusion laser is used to weld powdered metal and shape it into a part layer by layer. The main advantage of DMLS is that you can create parts with extremely complex geometries, such as honeycomb and lattice structures. No matter which metal you choose, machining can’t match the design flexibility of DMLS.
If you need a part made of titanium alloy, the cost advantage of this material may be something you haven’t thought about. Using powder means you have almost no metal waste. Furthermore, while manufacturing costs are slightly higher using DMLS, the parts combine strength and weight reduction, providing added value.