Aluminum CNC Machining: Benefits, Processing, and Applications
Aluminum CNC machining is a key process in modern manufacturing, and it offers many advantages due to aluminum’s unique properties. In this guide, Xavier will explore the benefits, processes, and applications of aluminum CNC machining to help readers understand its importance.
1. What is aluminum CNC machining?
Aluminum CNC machining uses CNC machines to shape and form aluminum parts. Aluminum is a very useful metal that is used in a wide range of industries. It starts out soft and easy to shape, and when mixed with other metals such as magnesium or copper, it becomes stronger and can be used for different purposes.
CNC machining of aluminum is a popular method because it is easy to operate. Manufacturers use it to create precision aluminum parts for specific jobs. They do this using CNC routers (machines that shape aluminum into the desired shape).
2. Advantages of Aluminum CNC Machining
1) Good Machinability
Aluminum is easier to process than many other metals, which can reduce production time and processing costs.
2) Ideal strength-to-weight ratio
Aluminum has a superior strength-to-weight ratio. It is well suited for the aerospace industry where lightweighting is critical.
3) Cost-effective
Compared to other metals such as titanium or stainless steel, aluminum is considered relatively cost-effective. Therefore, aluminum is an affordable option for many projects.
4) Corrosion resistance
Aluminum naturally forms a protective oxide layer that helps prevent corrosion and prolong the service life of mechanical parts.
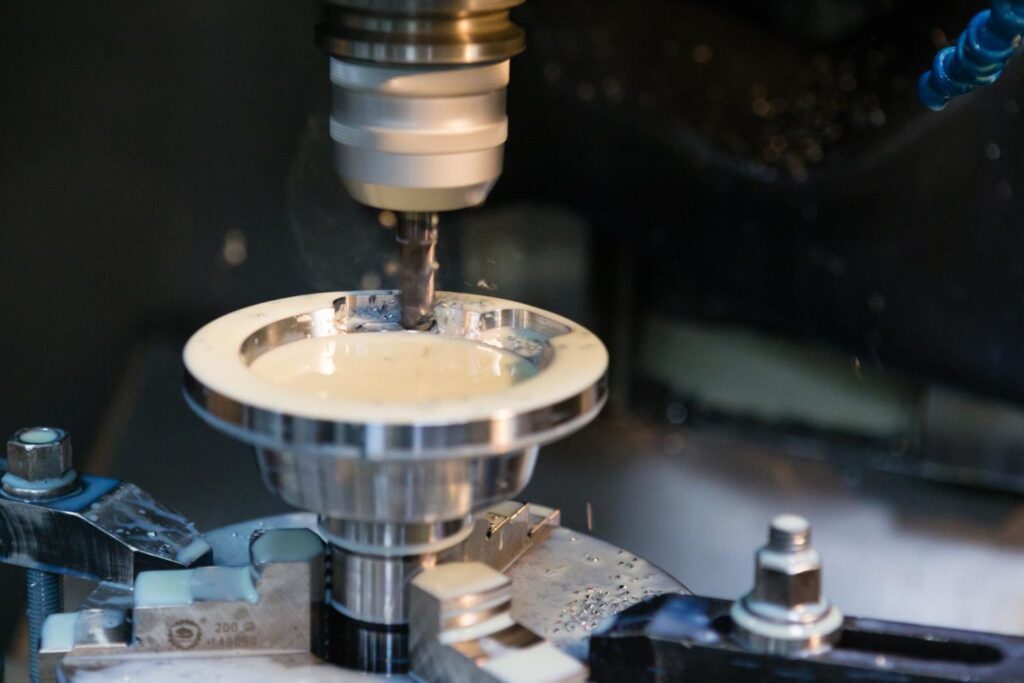
3. Common aluminum alloys for CNC machining
1) Aluminum 2024
2024 aluminum alloy is a high-strength material with copper as the main alloying element. It is widely recognized for its excellent strength-to-weight ratio and good fatigue resistance.
– Industry: automotive, aerospace, transportation, electronics
– Products: automotive parts, aircraft parts, structural parts, electronics, wheels, wing skins
2) 6061 aluminum
It has magnesium and silicon as alloying elements. Its weldable and heat-treatable properties further enhance its flexibility and are the first choice for extrusions.
– Industries: Marine, Automotive, Aerospace, Consumer Goods
– Products: Structural parts, Steps, Platforms, Valves, Pipes, Engine blocks, Bicycle frames
3) Aluminum 7075
7075 aluminum alloy is a heat-treatable alloy known for its high strength-to-weight ratio and excellent mechanical properties. Zinc is the primary alloying element in 7075 aluminum alloy, which contributes to its strength and toughness.
– Industries: Aerospace, Transportation, Bicycle Parts, Archery Equipment
– Products: Aircraft Parts, Bicycles, Golf Clubs, Weapons
4) Aluminum 3003
3003 aluminum alloy is a popular alloy in the wrought aluminum-manganese series (3xxx series). It is known for its moderate strength, workability, and corrosion resistance. 3003 aluminum can be cold worked to increase its strength, but cannot be heat treated like other aluminum alloys.
– Industries: Household Goods, Chemicals, Construction
– Products: Tubes, Pipes, Roofing Materials, Cookware, Kitchen Equipment, Office Equipment
5) Aluminum 5052
Made primarily of magnesium and chromium, 5052 aluminum alloy is a versatile and versatile material. While it is not heat treatable, it can be hardened by cold working.
– Industries: Marine, Aerospace, Construction
– Products: Wires, Rivets, Marine Components, Heat Exchangers, Fuel Tanks, Sheet Metal
4. CNC Machining: Aluminum vs. Steel
Aluminum and steel are the top choices for CNC machining. Choosing between them depends on five key factors:
• Cost:
Steel, especially mild steel, tends to be cheaper than aluminum alloys. However, stainless steel is more expensive. Factors such as global demand and production costs affect metal prices. It is critical to weigh upfront costs against long-term durability.
• Corrosion Resistance:
Both aluminum and stainless steel have good rust resistance. Stainless steel has better rust resistance, but it costs more. Other types of steel require additional protection, which increases weight and coating costs.
• Weight:
Aluminum is much lighter than steel, making it a good choice for heavier parts. This trend toward lighter materials often leads to better product performance.
• Strength:
Steel is heavier than aluminum, but stronger. Steel is less likely to bend or scratch, making it more durable than aluminum.
• Machinability:
Compared to steel, aluminum has a lower density, making it easier to machine. This means shorter production times, less tool wear, and the ability to use smaller, more cost-effective CNC machines.
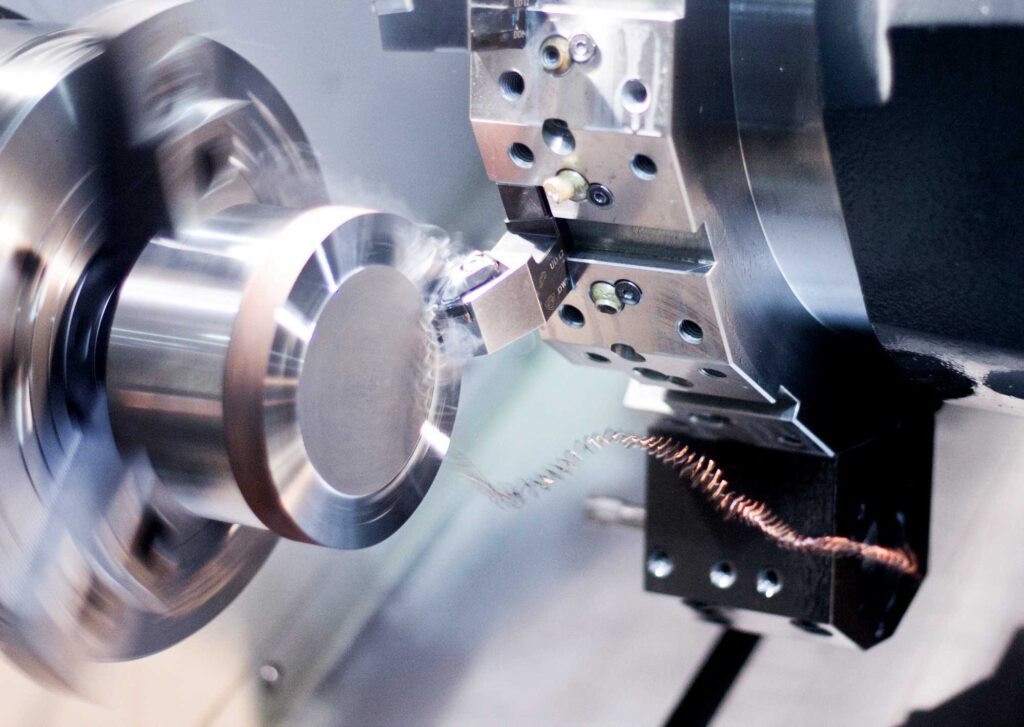
5. Common aluminum alloy CNC machining and processing processes
1) Different processing processes for aluminum CNC machining
• CNC milling: CNC milling automatically shapes aluminum CNC machining parts by rotating cutting tools while the workpiece remains stationary. The process removes material from aluminum parts in incremental and precise steps, allowing for higher tolerances.
• CNC drilling: CNC drilling is commonly used to drill holes in aluminum. It uses a rotating cutting tool to penetrate the material vertically, making it ideal for products that require screws or bolts.
• CNC turning: In aluminum CNC turning, the workpiece rotates while a fixed cutting tool shapes it. This process effectively removes material and precisely forms the desired shape.
2) CNC post-processing procedures
Once aluminum CNC machining parts are machined, certain steps can be taken to improve their physical, mechanical, and appearance qualities. The most common post-processing methods include:
• Sandblasting and shot peening: Sandblasting involves using high-pressure air to spray small glass beads onto aluminum parts, cleaning the surface and ensuring a smooth surface. Sandblasting uses high-pressure sand for a similar cleaning process. Other finishing processes include polishing and painting
• Coating: Aluminum parts can be coated with materials such as zinc, nickel, or chrome to improve processing and improve appearance. The process is achieved through an electrochemical reaction.
• Anodizing: Anodizing immerses aluminum parts in a sulfuric acid solution and applies a voltage to form a hard, non-conductive aluminum oxide coating. The thickness and color of the coating can be controlled according to process parameters.
• Powder coating: Powder coating uses an electrostatic spray gun to spray colored polymer powder onto the part, which is then cured at high temperature (200°C). This method can improve
• Heat treatment: Parts made of heat-treatable aluminum alloys are heat treated to enhance their mechanical properties.
6. Challenges and solutions faced by aluminum alloy CNC machining
1) Surface oxidation
Challenge: Aluminum forms a hard oxide layer that hinders machining and tool life.
Solution: Use carbide or diamond-coated tools to effectively cut the oxide layer. Check and replace tools regularly to maintain optimal cutting performance.
2) Tool vibration and chatter
Challenge: Vibration and chatter affect the accuracy and quality of machined parts.
Solution: Optimize cutting parameters (speed, feed rate, depth of cut) and check whether the machine tool is set up firmly. Use a vibration-damping tool holder and balance the cutting tool to minimize vibration.
3) Ductility of aluminum
Challenge: Poor surface finish, burrs and chip formation.
Solution: Use cutting tools designed for aluminum and appropriate cutting fluids.
4) Thermal issues during machining
Challenge: Thermal deformation of the workpiece and tool wear.
Solution: Use a high-pressure coolant system and reduce cutting speeds.
5) Maintaining Tight Tolerances
Challenges: Achieving and maintaining tight tolerances on aluminum parts can be challenging due to thermal expansion and tool wear.
Solutions: Employ precise temperature control during machining and use advanced CNC machines with high-precision capabilities. Regular calibration and maintenance of the machines are also important.
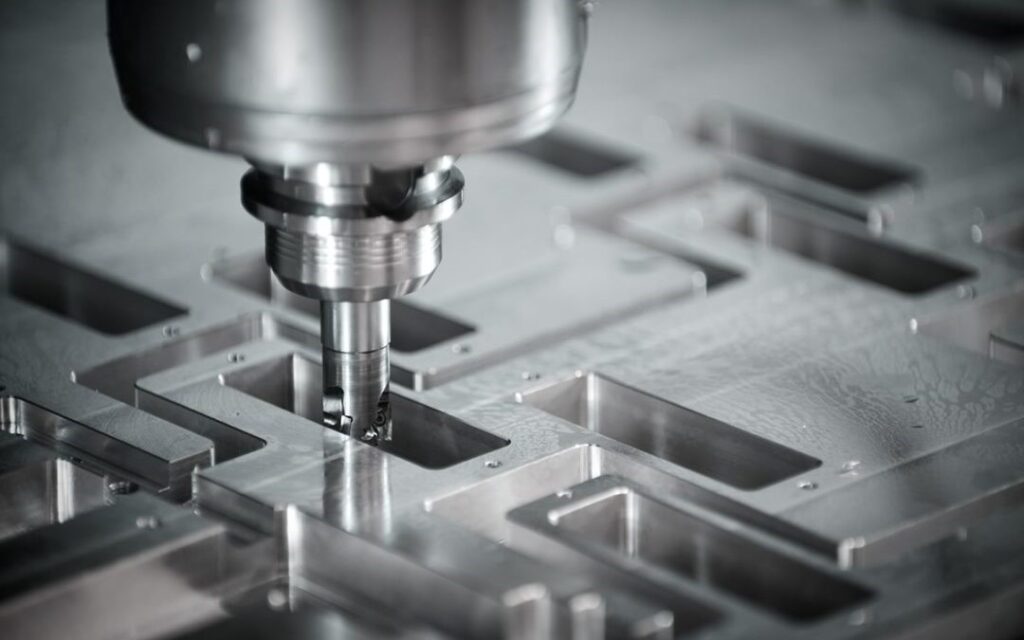
7. Applications of Aluminum Alloy CNC Machined Parts
Here are some of the industries that make extensive use of aluminum CNC machining applications:
• Aerospace Industry:
Aluminum CNC parts are widely used in the aerospace sector due to their lightweight and durability. Aircraft parts benefit from the strength of aluminum and the precision of CNC machining, which allows for complex shapes and tight tolerances.
• Automotive Industry:
The automotive industry uses aluminum CNC parts to manufacture engine and suspension components. The quality of aluminum combined with the precision of CNC machining ensures that automotive parts are reliable and perform well.
• Medical Industry:
Aluminum CNC parts are used in the medical field because aluminum is biocompatible and can be sterilized. Custom manufacturing through CNC machining can tailor medical implants and devices to the needs of each patient, ensuring compatibility and sterilizability.
• Marine Industry:
Aluminum CNC machined parts are essential in shipbuilding due to their corrosion resistance and light weight.
• Electronics Industry:
The electronics industry uses aluminum CNC parts for a variety of components due to aluminum’s excellent thermal conductivity and light weight.
• Agricultural Machinery:
Aluminum CNC machined parts are used in agricultural machinery due to their durability and resistance to harsh environmental conditions. CNC machining allows for precise and efficient manufacturing of agricultural components such as frame structures, gearbox housings, and hydraulic components.
8. Looking for Aluminum CNC Machining Services?
Aluminum CNC machining is an efficient process with many advantages that can be applied across a variety of industries. Whether you require high precision, complex shapes, or cost-effective production, aluminum CNC machining can meet your needs.
If you are looking for an experienced xavier If you are looking for an experienced CNC machining manufacturer, Xavier is your ideal choice. The Xavier team is well-equipped to provide high-quality CNC machining solutions. If you need more information or to discuss your machining needs with us, please feel free to contact us.