Understanding the Importance of Aluminium Machining Parts in Modern Industries
Aluminum is a versatile material that has revolutionized the manufacturing industry. The value of aluminum has been further enhanced with the advent of computer numerical control (CNC) machining, making the production process more precise, efficient, and cost-effective.
In this comprehensive guide, we will explore the world of metal CNC machining, with a particular focus on aluminum machining. From understanding the origins of aluminum to exploring different types of CNC machining processes, we will dive into the vast potential that aluminum offers in the manufacturing industry.
1.Demystifying the Origins of Aluminum
Before we delve into the intricacies of CNC machining aluminum, let’s take a moment to understand the origins of this extraordinary material. Aluminum is the third most abundant element in the Earth’s crust, making up approximately 8% of its composition. It was first isolated as a pure metal in the early 1800s. Since then, its use has skyrocketed due to its impressive properties.
With a high strength-to-weight ratio, aluminum is ideal for a variety of applications in the transportation, construction, electronics, and packaging industries. Its corrosion resistance, non-toxicity, and recyclability further contribute to its widespread use. As we explore the world of CNC machining aluminum, it is critical to recognize the superior qualities that make it the top choice of manufacturers around the world.
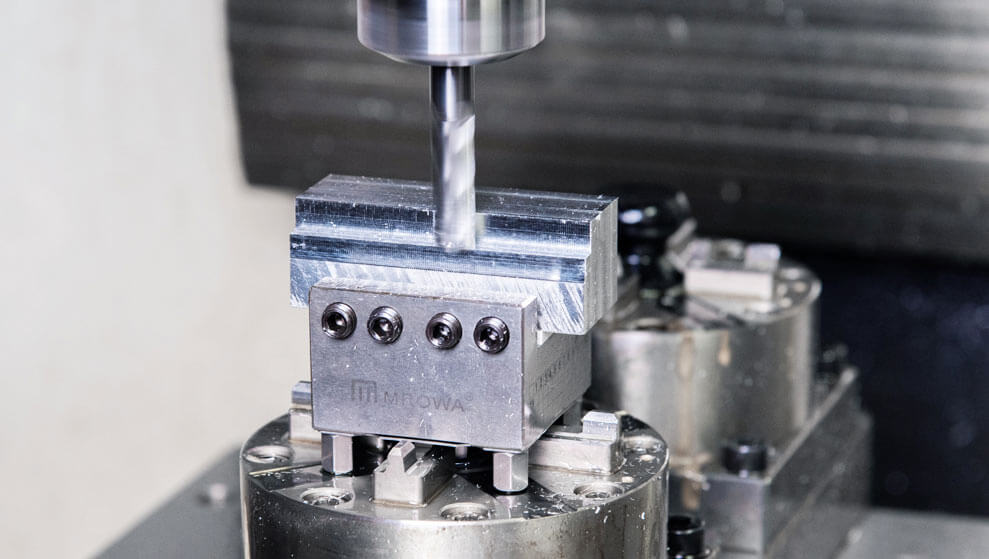
2.Understanding CNC Machining
Computer numerical control (CNC) machining has revolutionized the manufacturing industry, making the production process more precise and automated. Through pre-programmed computer software, CNC machines can control the movement of machinery and factory tools, resulting in consistent and accurate output. The technology has proven particularly useful in the production of aluminum castings, surpassing manual machining in terms of precision and efficiency.
With CNC machining, manufacturers can achieve superior accuracy and precision, minimize human error, and ensure exact replication of castings. The automation of the process helps create complex designs that push the limits of aluminum manufacturing. CNC machining also improves efficiency and productivity, enabling 24/7 operation without fatigue. This can increase productivity, minimize machine downtime, and make workflows more efficient.
3.Advantages of CNC Machining Aluminum
There are several advantages to adopting CNC machining in aluminum production. Let’s explore some of the key benefits that make CNC machined aluminum a top choice for manufacturers:
1) Improved Precision and Accuracy
One of the main benefits of CNC machined aluminum is its ability to deliver exceptional precision and accuracy. Automating the machining process minimizes human error, ensuring consistent and reliable results. Manufacturers can achieve complex designs with extreme precision, pushing the limits of aluminum manufacturing.
2) Improved Efficiency and Productivity
CNC machined aluminum allows for 24/7 operation without fatigue, which improves productivity and workflow efficiency. Automated processes minimize machine downtime, ensuring a smooth, uninterrupted manufacturing process. This means faster turnaround times and greater productivity for manufacturers.
3) Cost Savings
In the long run, CNC machined aluminum can provide significant cost savings. By reducing raw material waste and reducing errors, manufacturers can optimize resources and reduce costs. Additionally, CNC machining reduces labor costs by automating the manufacturing process, which improves overall cost-effectiveness.
4) Versatility and Adaptability
Aluminum is an extremely versatile material, and CNC machining further enhances its adaptability. Manufacturers can use CNC machined aluminum to create a variety of products and components, from complex electronic devices to structural elements in architectural projects. Using aluminum in various forms opens up a world of possibilities for manufacturers.
5) High-quality finished products
CNC aluminum machining ensures that a high-quality finished product is produced. The precision and accuracy of the machining process produces a consistent and reliable output that meets the industry’s stringent quality standards. Manufacturers can build a reputation for excellence in the market by providing products that not only meet but exceed customer expectations.
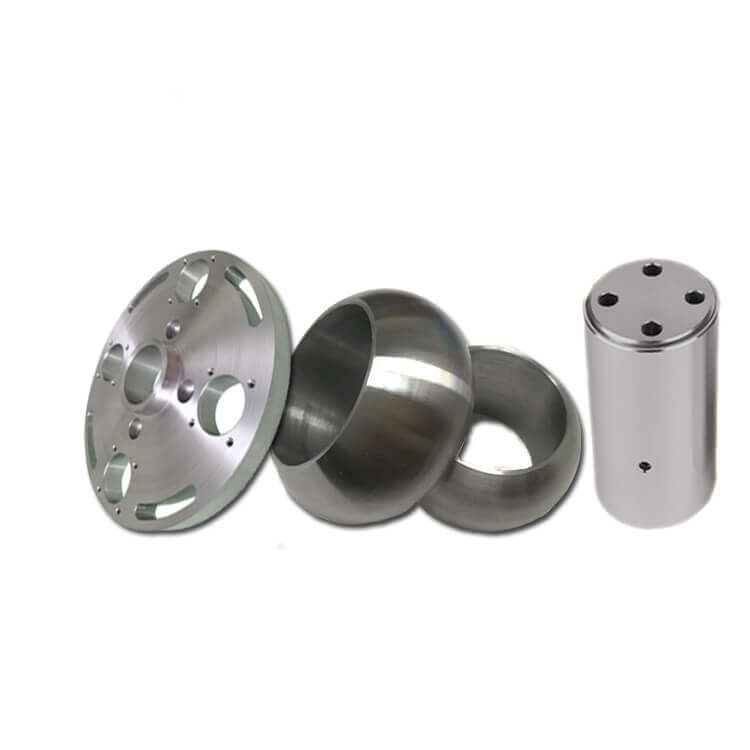
4.Explore Different Types of Aluminum CNC Machining Processes
Now that we have delved into the benefits of CNC machining aluminum, let’s explore the different types of CNC machining processes commonly used in aluminum manufacturing. Each technology has unique benefits and applications that meet the different needs of manufacturers.
1) Milling
Milling is a basic CNC machining process used to shape and cut aluminum. It involves using a rotating tool to remove material from a workpiece to achieve the desired shape and size. Milling can be performed on a variety of CNC machines, including vertical and horizontal milling machines. Manufacturers can achieve precise and complex designs with milling, making it a versatile process in aluminum machining.
2) Turning
Turning is another important CNC machining process used in aluminum manufacturing. It involves the rotation of the workpiece while a cutting tool removes material to form the desired shape. Turning is often used to produce cylindrical parts such as shafts, rods, and tubes. With CNC turning, manufacturers can achieve high precision and accuracy, ensuring consistent and reliable results.
3) Drilling
Drilling is a CNC machining process used to create holes in aluminum parts. It involves using a rotating cutting tool to remove material and create precise holes of varying diameters. Drilling is a versatile process that can be performed on a variety of CNC machines, including vertical and horizontal drilling machines. It is often used to produce aluminum parts that require holes for assembly or functionality.
4) Tapping
Tapping is a CNC machining process used to create internal threads in aluminum parts. It involves using a cutting tool called a tap to create threads by removing material. Tapping can be performed on CNC machines with rotational motion, such as CNC lathes. It is often used to produce aluminum parts that require threaded connections.
5) Boring
Boring is a CNC machining process used to enlarge or refine existing holes in aluminum parts. It involves using a single-point cutting tool to remove material and achieve the desired hole diameter and precision. Boring is often used in applications that require high precision and accuracy, such as producing engine cylinders and bearing seats.
5.The Future of CNC Machining in Aluminum Manufacturing
As technology continues to advance, the future of CNC machining in aluminum manufacturing looks bright. Continuous innovations in CNC machines and software are opening up new possibilities for manufacturers, allowing them to push the boundaries of what is possible in aluminum production. From developing faster and more efficient machines to integrating artificial intelligence (AI) and automation, CNC machining is well positioned to further revolutionize the industry.
As the demand for precision, efficiency, and cost-effectiveness continues to grow, CNC machining aluminum will play a key role in meeting these requirements. Manufacturers will be able to create complex designs with the utmost precision, delivering a high-quality finished product that exceeds customer expectations. As CNC machining technology continues to advance, the potential for aluminum manufacturing is limitless.
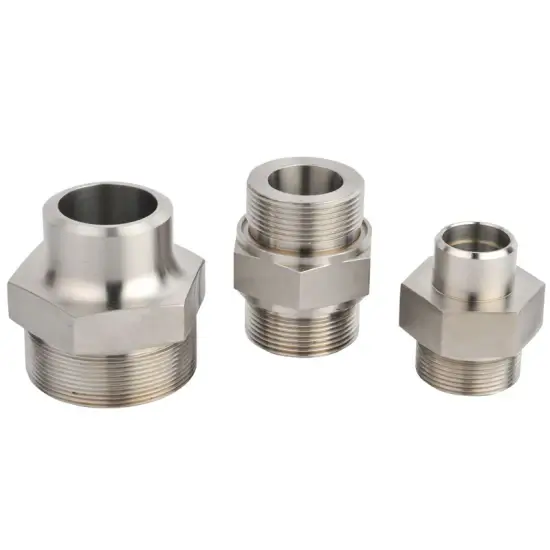
6.Conclusion
CNC machining has revolutionized the manufacturing industry, making aluminum production more precise, efficient, and cost-effective. Aluminum has become the material of choice for manufacturers around the world due to its superior properties. Through processes such as milling, turning, drilling, tapping, and boring, CNC machining unlocks the full potential of aluminum, allowing manufacturers to achieve complex designs with extreme precision.
The benefits of CNC machining aluminum include increased precision and accuracy, improved efficiency and productivity, cost savings, and versatility, making it an indispensable tool in the manufacturing industry. As technology continues to advance, CNC machining will play an increasingly important role in aluminum manufacturing, driving innovation and pushing the boundaries of what is possible.