Advantages of Aluminum CNC Machining
CNC machining has revolutionized the manufacturing industry, making the production of a wide range of parts precise and efficient. Aluminum is a popular material for CNC machining. Aluminum is the top choice for many manufacturers due to its unique properties and numerous benefits.
In this article, we will explore the benefits of aluminum CNC machining and discuss possible alternatives for various parts.
1.Lightweight
One of the main advantages of aluminum CNC machining is its light weight. As such, aluminum is known for its low density, making it an ideal material for applications where weight reduction is critical. Industries such as aerospace, automotive, and electronics have benefited greatly from the use of aluminum components as they help reduce overall weight, improve fuel efficiency, and enhance performance.
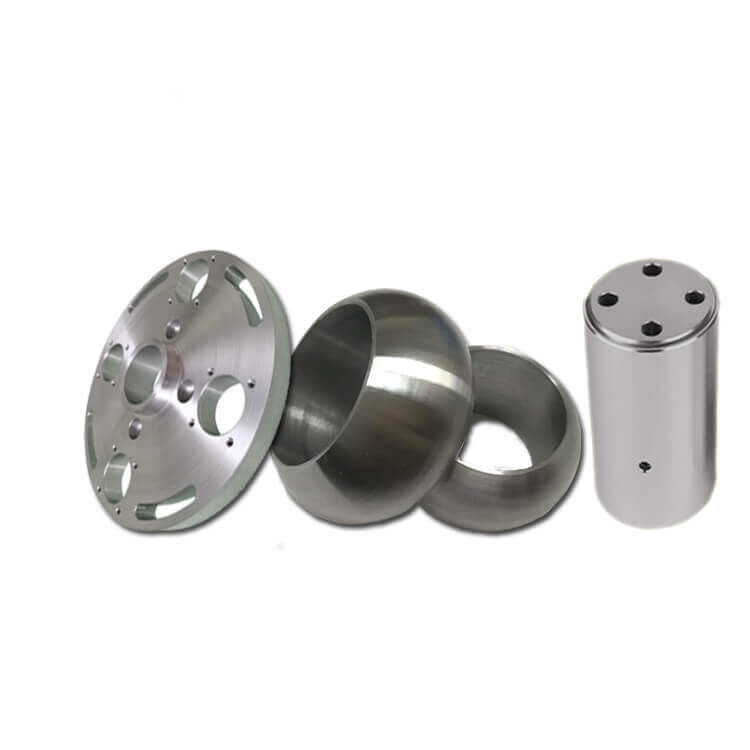
2.Strength-to-weight ratio
Despite its light weight, aluminum has excellent strength, making it ideal for applications that require strength and durability. This unique combination of properties allows manufacturers to create strong components without compromising weight or performance.
3.Corrosion resistance
Another notable benefit of aluminum CNC machining is its excellent corrosion resistance. Aluminum naturally forms a protective oxide layer when exposed to air, which prevents further oxidation and corrosion. This inherent corrosion resistance makes aluminum parts extremely durable and long-lasting, even in harsh environments.
Industries such as marine, construction, and outdoor equipment benefit greatly from the use of aluminum due to its corrosion resistance.
4.Excellent Conductor
This property makes it ideal for applications that require efficient heat dissipation or electrical conductivity. Industries such as electronics and power transmission rely on aluminum components to ensure optimal performance and prevent overheating.
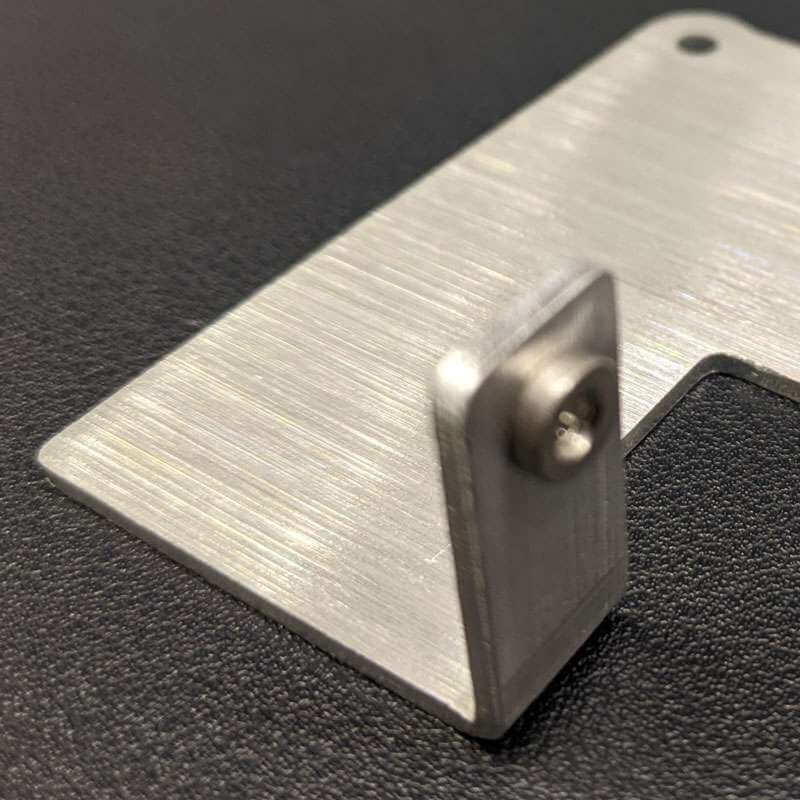
5.Excellent Machinability
Aluminum CNC machining also offers excellent machinability. Aluminum is a relatively soft material that is easy to cut, drill, and shape during machining. This easy-to-machine property not only increases productivity, but also reduces tool wear and extends tool life.
Manufacturers can achieve high precision and intricate designs using aluminum components, making it a versatile material for a wide range of applications.
Despite the numerous benefits of aluminum CNC machining, there are some situations where alternative materials may be more appropriate. For applications that require higher strength or high temperature resistance, materials such as steel or titanium may be preferred. These materials have excellent strength and can withstand extreme conditions, making them ideal for heavy-duty applications.
In addition, for applications that require specific properties, such as electrical insulation or chemical resistance, alternative materials such as plastics or composites may be more appropriate. These materials have a wide range of properties and can be tailored to specific requirements.
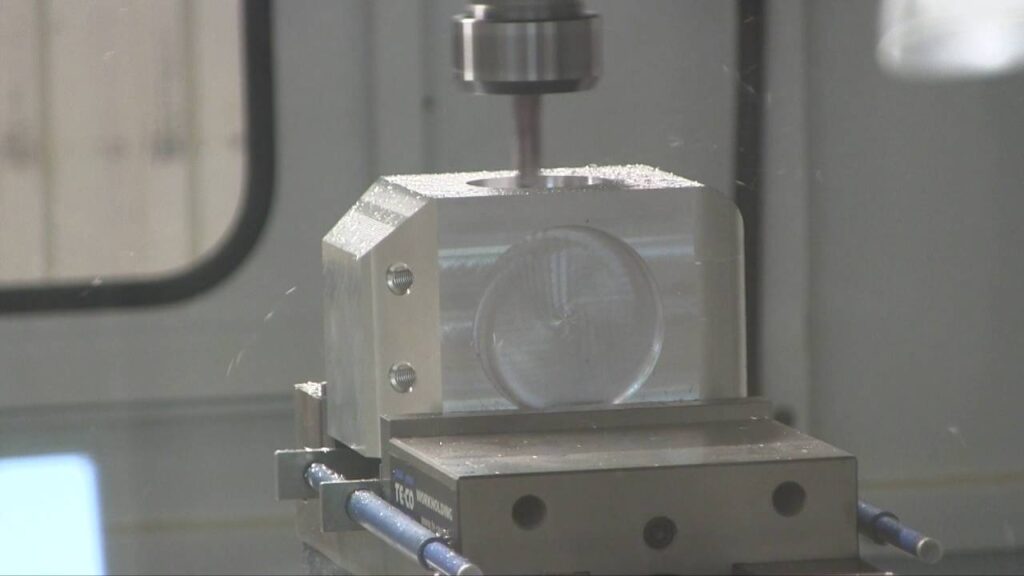
In summary, aluminum CNC machining offers numerous advantages that make it a top choice for many manufacturers. Its light weight, excellent strength-to-weight ratio, corrosion resistance, and machinability make it suitable for a wide range of applications. However, in certain situations where specific properties or higher strength are required, alternative materials must be considered. By understanding the advantages and possible alternatives to aluminum CNC machining, manufacturers can make an informed decision and select the most appropriate material for their specific needs.