Aluminum CNC Machining: Key Design Considerations
Welcome to a CNC machining design guide tailored specifically for aluminum CNC parts. Computer Numerical Control (CNC) machining has revolutionized manufacturing by enabling precise and efficient manufacturing of complex parts. This guide provides you with basic insights and practical considerations for designing aluminum parts optimized for CNC machining processes.
Known for its light weight, corrosion resistance, and excellent thermal conductivity properties, aluminum is a widely used material in various industries including aerospace, automotive, electronics, and more. When CNC machining aluminum parts, careful attention to design details can significantly impact the quality, accuracy and cost-effectiveness of the final product.
In this guide, we’ll dive into key design principles, material properties, machining capabilities, and best practices so you can create designs that translate seamlessly into high-quality aluminum CNC parts. Whether you are an experienced engineer, designer, or new to the world of CNC machining, this guide will provide you with valuable knowledge to optimize your CNC-manufactured aluminum part designs.
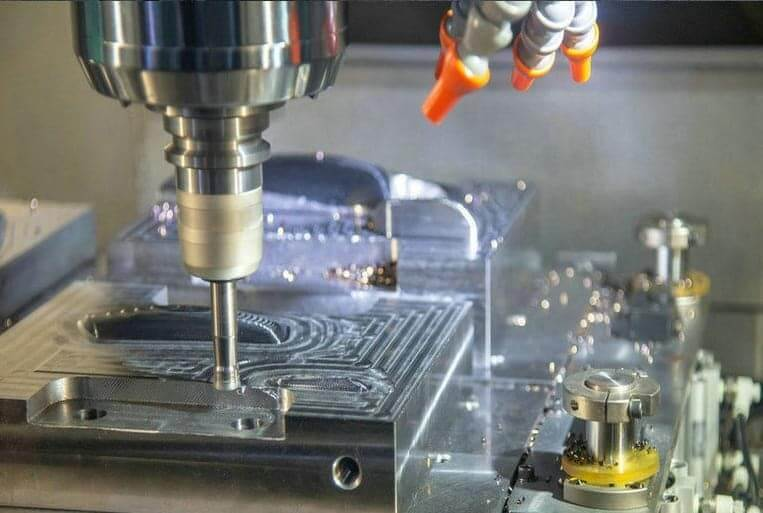
1.Introduction to Aluminum CNC Machining Design Guide
1) The importance of proper design and manufacturing considerations:
In modern manufacturing, collaboration between design and manufacturing is crucial. Because successful results in terms of product functionality, quality, cost-effectiveness and time-to-market will all depend on the careful integration of design and manufacturing considerations. This synergy is especially important in CNC machining, where complex designs need to be transformed into tangible products. Let’s dig a little deeper into why proper design and manufacturing considerations are crucial:
①Optimization function
Proper design and manufacturing considerations ensure that the final product not only meets its intended use, but does so efficiently. Because design decisions affect factors such as structural integrity, performance, and usability. If the design is well thought out and made with manufacturing in mind, it can be tailored to take advantage of the chosen manufacturing process, thereby enhancing the overall functionality of the product.
②Manufacturability
A design that looks impressive on paper may not translate seamlessly into production. Therefore, manufacturability must be considered during the design phase to avoid costly modifications later on. By considering factors such as material properties, machining techniques, tool accessibility and assembly requirements, you can create accurate and consistent designs.
③Shorten delivery time
Integrating design and manufacturing considerations early streamlines the entire production process. Because well-designed parts are easier to machine, it not only minimizes the need for complex setups, reduces tool changes, and optimizes tool paths, it also reduces lead times and speeds turnaround from design to finished product.
④Quality and consistency
Thoughtful design is aligned with the capabilities of the manufacturing process, improving the consistency and quality of the final product. At the same time, proper design and machining considerations can also reduce the possibility of defects such as tool marks, burrs, and dimensional inaccuracies. Because these defects may affect product quality and reduce the manufacturer’s market competitiveness.
⑤Cost efficiency
Design decisions will directly impact manufacturing costs. Because an overly complex design will increase material waste, processing time and tool wear, thereby increasing production costs. Through design efficiency and ease of manufacturing, you can minimize costs while maintaining product integrity.
⑥Innovation and creativity
Collaboration between design and manufacturing teams can foster innovation. Because when both parties share insights and challenges, new solutions emerge that leverage cutting-edge technologies, materials and processes. At the same time, creative problem solving can also improve a product’s competitive advantage.
⑦ Minimize the number of iterations
Addressing potential issues during the design phase reduces the need for iterative changes. This saves time and avoids problems during the production phase. Because it can make the process from design verification to manufacturing execution smoother.
⑧Cross-functional communication
Encouraging communication and collaboration between designers and manufacturing experts provides a comprehensive view of the entire product development process. This synergy promotes learning, knowledge sharing and the development of all-round skills among team members. Therefore, the bridge between design and manufacturing is particularly important in the field of CNC machining where precision and complexity dominate.
At the same time, taking appropriate design and manufacturing considerations facilitates a perfect combination of creativity, technical feasibility and efficient production, resulting in high-quality products that are cost-effective, reliable and timely. By emphasizing this integration, manufacturers and designers can work together to push the boundaries of modern manufacturing and advance the industry together.
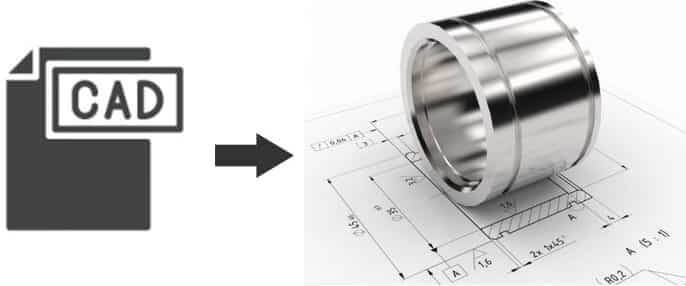
2) Advantages and challenges of processing aluminum parts:
Due to the unique properties and characteristics of the aluminum material, machining aluminum parts presents a unique set of advantages and challenges, and understanding these aspects is critical to achieving successful and efficient CNC machining results. Here are the pros and cons of machining aluminum parts:
advantage:
①Lightweight
Aluminum, due to its low density, is a popular choice for applications where weight reduction is critical. Processed aluminum parts can help reduce the overall weight of products, especially in aerospace and automotive industries.
②High thermal conductivity
Aluminum has excellent thermal conductivity and can effectively dissipate heat. This feature is very advantageous in applications where thermal management is critical, such as electronic components and heat sinks.
③Corrosion resistance
Aluminum can naturally form a protective oxide layer on the surface of the metal, so it is corrosion-resistant and can avoid corrosion, ensuring that the performance of the product can be fully exerted.
④Processability
Aluminum is generally considered an extremely workable material. Because it can efficiently cut, drill, mill and form through various processing processes, thereby shortening production lead times.
⑤Good surface finish
Because aluminum is soft and malleable, machining aluminum results in a smooth surface finish. This feature is beneficial for parts that require aesthetics or tight tolerances.
⑥Electrical conductivity
Aluminum’s electrical conductivity makes it suitable for applications involving electrical connections or grounding, such as electronic enclosures and connectors.
shortcoming:
①Material softness
The softness of aluminum contributes to a smooth surface finish, but also leads to increased tool wear and the risk of deformation during machining. Therefore, specialized tooling and cutting strategies are often required to offset these effects, adding some cost input.
② Sticky chips
Aluminum produces sticky chips that stick to cutting tools, potentially affecting machining accuracy and surface finish.
③Work hardening
Some aluminum alloys can develop work hardening during machining, causing increased tool wear and reduced cutting efficiency over time.
④Thermal expansion
The thermal expansion coefficient of aluminum is relatively high, and the heating of the material during processing will cause dimensional changes. So compensating for thermal expansion is important to keep dimensions accurate.
⑤Material diversity
Aluminum alloys come in a variety of compositions, each with unique properties. Material diversity affects machinability, surface finish and tool life, so the characteristics of a specific alloy should be considered when making material selections.
⑥Tool wear
The abrasive nature of aluminum accelerates tool wear, requiring frequent tool replacement and potentially increasing production costs. But using high-quality tool materials and coatings can extend tool life.
⑦Chip control
Managing the chips generated during aluminum machining is critical to preventing chip buildup, tool damage and surface finish issues. Therefore, proper chip evacuation systems and strategies are necessary.
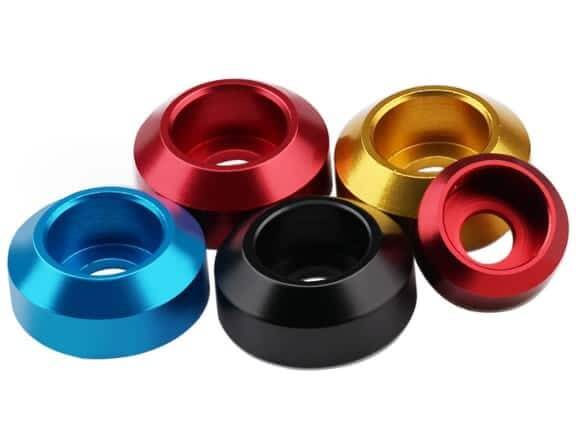
2.Key Considerations for CNC Machining Design Guidelines
When designing CNC machined parts, especially when producing aluminum CNC parts, several key factors must be considered to ensure successful and efficient manufacturing. The following are key design guide considerations for optimizing your CNC machining process:
1) Manufacturing tolerance
Designing within appropriate manufacturing tolerances is critical to obtaining accurate and consistent results. Because tolerances define allowable variations in specified dimensions and ensure that parts function properly and fit together correctly. Therefore, it is important to work closely with your CNC machining supplier to understand their capabilities and recommended tolerances for different functions.
2) Cavities and pockets
Factors such as tool passage, tool diameter and material removal need to be considered when designing cavities and grooves in CNC machined parts. Avoid small corners as these can be difficult to machine accurately. At the same time, providing adequate tool clearance and considering increasing the draft angle can help remove parts from the mold.
3) Internal edge and radius
Internal edges and radii have an impact on the strength, aesthetics, and ease of fabrication of the part. Because sharp internal corners may cause stress concentration and machining difficulties. Adding fillets or radii to the inner edges improves the durability of the part and enhances machining efficiency.
4) Thin wall and structure
Thin walls and structures are susceptible to vibration and deflection during machining, making them difficult to machine accurately. Therefore, when designing thin walls, the stiffness and processing force of the material should be considered. They can be reinforced with ribs or supports to increase stability and prevent deformation.
5) Holes, threads and undercuts
Holes and threads require careful consideration to ensure correct alignment, size and depth. For internal threads, consider using standard thread sizes to facilitate tooling and reduce complexity. Undercuts are features that prevent direct access by the cutting tool and should be minimized or avoided because they complicate machining.
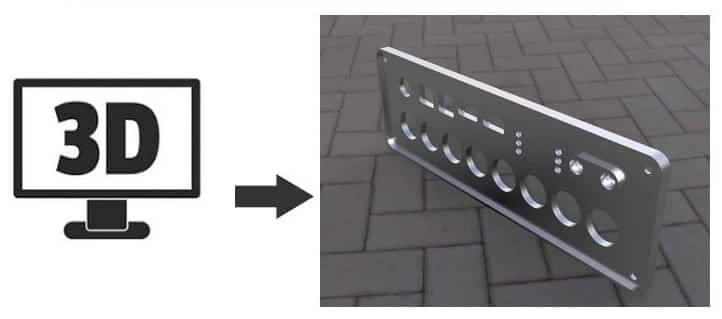
3.Material selection for aluminum alloy CNC parts
1) Factors affecting material selection
Choosing the right material for an aluminum CNC part is a critical decision because it affects the part’s performance, manufacturability, and overall cost. Several factors will influence the selection of materials. To ensure that the selected material meets the specific requirements of the application, the following factors should be considered:
①Mechanical properties
Consider the strength, hardness, toughness and other mechanical properties required of the part. Because different aluminum alloys have different levels of these properties.
②Corrosion resistance
Evaluate the environment to which the component will be exposed. While aluminum’s natural oxide layer provides some corrosion resistance, certain alloys can provide enhanced protection against corrosion, depending on their composition.
③Thermal conductivity
If the part will be exposed to heat or needs to dissipate heat, the thermal conductivity of the aluminum alloy must be considered. And high thermal conductivity is beneficial for heat sinks and components that require thermal management.
④Conductivity
Certain applications require electrical conductivity. Different aluminum alloys have different conductivities, so please choose based on the specific situation.
⑤Processability
Consider how easily the selected aluminum alloy can be machined. Good machinability of alloys reduces tool wear and machining time, resulting in cost savings.
⑥Aesthetics and surface finish
If the appearance of the part is important, consideration must be given to material finishing, anodizing or coating to achieve the desired aesthetics.
⑦Cost
Raw material costs can impact the overall project budget. Therefore, balancing material quality and cost-effectiveness is crucial.
⑧Availability
Ensure the selected aluminum alloy is readily available from the supplier to prevent production delays.
⑧Regulatory compliance
Some industries have specific regulations or standards for material selection that must be strictly followed.
2) Aluminum alloys commonly used in CNC machining
A variety of aluminum alloys are commonly used in CNC machining due to their excellent properties. Below is a list of the most common alloys:
①6061-T6
This versatile alloy offers good strength, corrosion resistance and workability. It is commonly used on a variety of CNC machined parts, including structural components and accessories.
②7075-T6
Known for its high strength and excellent fatigue resistance, 7075-T6 is used in applications requiring excellent structural integrity, such as aerospace components and high-performance equipment.
③2024-T3
2024-T3 offers good processability and a high strength-to-weight ratio, making it suitable for applications such as aircraft structures where weight reduction and durability are critical.
④5052-H32
The alloy has good corrosion resistance and formability. It is typically used for parts that require complex shapes and moderate strength, such as sheet metal components.
⑤6063-T5
6063-T5 is commonly used in extruded shapes because it provides a good surface finish for applications such as architectural profiles and frames.
⑥6082-T6
Similar to 6061-T6, this alloy offers excellent machinability and is used in a wide range of CNC machining applications, including structural parts and accessories.
Considerations such as mechanical properties, corrosion resistance and thermal properties should be present in your material selection process to ensure optimal performance and cost-effectiveness.
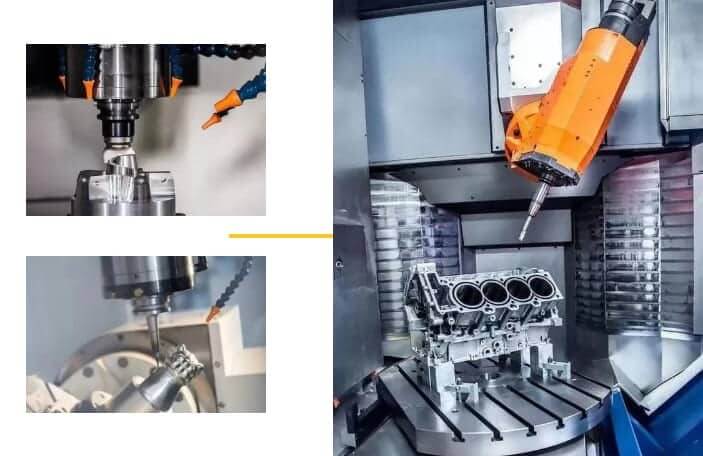
4.Manufacturing Process of Aluminum Alloy CNC Machining
Aluminum CNC machining covers a variety of processes for precision forming and manufacturing aluminum parts. Different manufacturing processes have their own unique advantages and can complete production tasks.
1) Key manufacturing processes used in aluminum CNC machining:
① Milling and turning
- Milling: Milling is the process of removing material from a workpiece using a rotating tool. In aluminum CNC machining, milling is often used to create complex shapes, features, and grooves. And in order to achieve specific geometries and surface quality, many milling techniques can also be used, including face milling, end milling, and profile milling.
- Turning: Turning is the process of rotating a workpiece while removing material with a cutting tool to produce a cylindrical shape. In aluminum machining, turning is used to create cylindrical features such as shafts, threads, and concentric surfaces. Therefore, it is particularly suitable for producing circular or symmetrical parts.
② High-speed machining
High-speed machining (HSM) is a process that uses faster spindles and feed rates to quickly remove material. In aluminum CNC machining, HSM uses the relatively low hardness of the material to achieve a fast material removal rate. This technology can not only effectively reduce processing time and improve productivity, but also maintain precision for each product.
③ Multi-axis machining
To manufacture complex shapes and contours, multi-axis machining involves moving multiple axes simultaneously. Multi-axis machines can perform complex operations with just one setup when cutting aluminum, minimizing the need to move the workpiece. Common multi-axis configurations include 3-axis, 4-axis, and 5-axis machining, of which 5-axis provides the greatest flexibility for creating complex geometries and contours.
2) Advantages of each process of aluminum CNC machining
① Milling and turning
These processes are versatile and can manufacture parts of various geometries, from simple to complex. They can be used for both internal and external features and are ideal for producing parts with rotational symmetry.
② High-speed machining
Due to the softness of aluminum, HSM is ideal for aluminum machining. It removes material quickly without causing excessive tool wear, thereby reducing machining time and increasing productivity.
③ Multi-axis machining
Multi-axis machines are used to manufacture complex shapes. They reduce the need for multiple setups, and also improve accuracy and shorten production time for parts with complex geometries.
3) Considerations
① Material properties
The properties of aluminum, such as its low hardness and thermal conductivity, affect tool selection and cutting parameters in each machining process.
② Tools
For effective and precise machining results, it is critical to select the correct tool material, coating, and geometry.
③ Machine capabilities
The capabilities of CNC machine tools, including spindle speed, feed rate, and available motion axes, determine the feasibility of different machining processes.
④ Part complexity
The complexity of part geometry and required features affects the choice of machining process. More complex parts may benefit from multi-axis machining.
By understanding the advantages and applications of milling, turning, high-speed machining, and multi-axis machining, manufacturers can select the most appropriate aluminum CNC machining process. This ensures that parts are accurately manufactured, meet design specifications, and are produced efficiently.
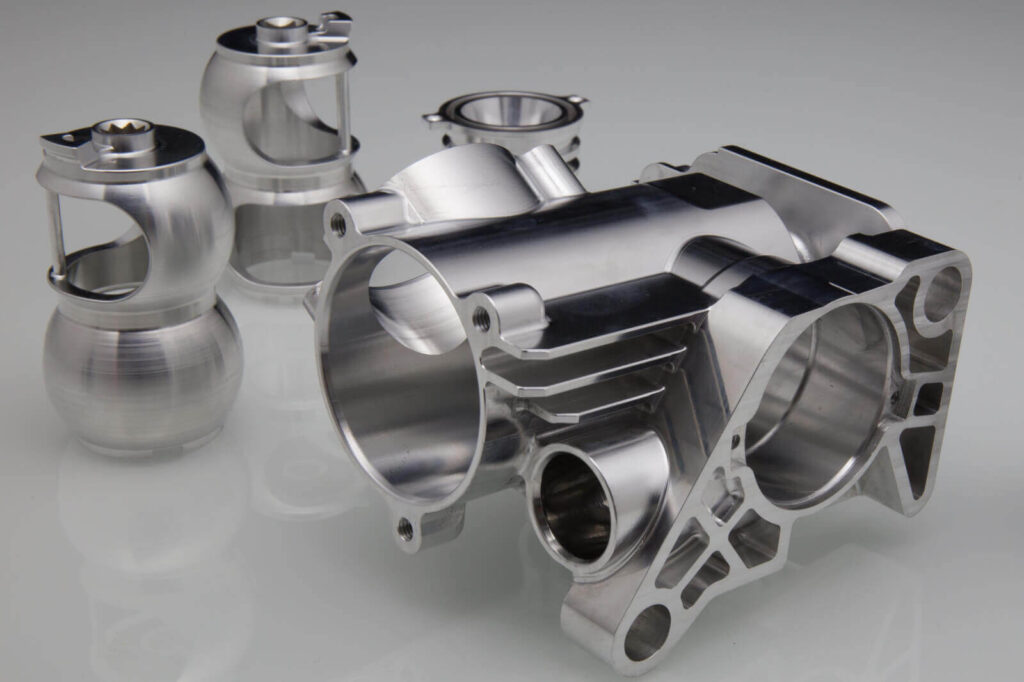
5.Surface treatment options for aluminum CNC parts
1) The role of surface treatment
An important aspect of the CNC machining process for aluminum parts is surface preparation. Machining shapes the geometry of a part, while surface treatments enhance its appearance, functionality and durability. And, the right surface treatment techniques not only provide aesthetic appeal, but also improve corrosion resistance, wear resistance and other performance characteristics. Here’s why surface preparation is so important:
①Aesthetic appeal
Surface treatments enhance the visual appeal of CNC machined aluminum parts, making them more attractive and professional looking.
②Corrosion resistance
Aluminum naturally forms an oxide layer on metal surfaces, making it corrosion-resistant. Surface treatment methods can further enhance this protection and extend the service life of parts in corrosive environments.
③Wear resistance
Certain surface treatment techniques, such as anodizing, hard anodizing and coatings, can increase the wear resistance of parts, making them suitable for applications with high friction or abrasive conditions.
④Improve lubrication
Certain surface treatments, such as coatings and platings, can provide improved lubrication properties and reduce friction and wear on moving parts.
⑤Electrical conductivity
Anodizing and other surface treatments maintain the material’s electrical conductivity while adding other beneficial properties.
⑥Thermal management
Thermal coatings and surface treatments can enhance a part’s ability to dissipate heat, making it suitable for applications where thermal management is critical.
2) Popular aluminum processing technology
Aluminum CNC machined parts often use a variety of surface treatment techniques. Here are some popular aluminum processing techniques:
①Anodizing
Anodizing is an electrochemical process that applies a protective oxide coating to the surface of aluminum. Anodizing not only enhances aluminum’s corrosion resistance and provides a long-lasting surface, it can also be dyed in a variety of colors.
②Chemical conversion coating
Chemical conversion coatings, such as chromate or phosphate coatings, provide corrosion resistance, paint adhesion and improved electrical conductivity.
③Electroplating
Electroplating is the deposition of a layer of metal on the surface of aluminum. Common platings include nickel, chromium and zinc, which enhance aluminum’s durability, aesthetics and resistance to certain environmental conditions.
④Paint and powder coating
Paints and powder coatings are available in a variety of colors and finishes while providing protection against corrosion, UV rays and other environmental factors.
⑤Brushed and polished surface treatment
Mechanical finishing techniques such as brushing and polishing can produce textured or reflective surfaces that enhance the aesthetics of the part.
⑥Sandblasting
Sandblasting involves spraying tiny beads onto an aluminum surface to create a matte texture. It is often used to improve paint adhesion or create a uniform look.
⑦Transparent coating
A clear protective coating, such as clear lacquer or sealant, can maintain the natural appearance of aluminum while providing a layer of protection against oxidation and environmental factors.
⑧Special coating
Depending on the application, specialized coatings such as thermal barrier coatings or self-lubricating coatings can be used to achieve specific performance characteristics.
Selecting the correct surface treatment technology requires consideration of factors such as intended use, aesthetics, environmental conditions and performance requirements. Each technology has its own unique advantages, and manufacturers often need to work closely with designers to select the most appropriate surface treatment for their aluminum CNC machined parts.
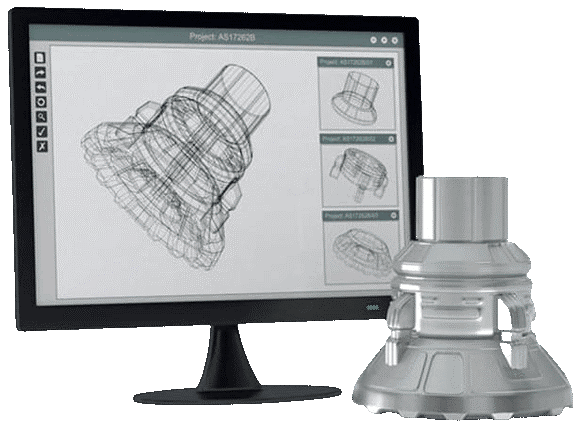
6.Optimizing the cost and efficiency of aluminum CNC machining
1) Design for manufacturability
Design for manufacturability is a key strategy for optimizing the cost and efficiency of aluminum CNC machining. Taking this approach involves creating designs that are not only functional and beautiful, but also take into account the practical aspects of the manufacturing process. Here’s how Design for Manufacturability can help achieve cost-effective CNC machining:
① Simplify geometric shapes
Complex designs can result in longer machining times, increased tool wear and increased costs. Simplifying geometries, minimizing sharp angles and reducing unnecessary features can simplify the machining process.
②Material selection
Choose a readily available and affordable aluminum alloy suitable for your specific application. Avoid using rare or difficult-to-source alloys that may increase material costs.
③Standard tools
Designing parts that can be machined using standard tooling and tool sizes can significantly reduce tooling costs. Custom tooling can be expensive and may not always be necessary.
④ Minimize tool changes
Designing parts that can be machined with a minimum number of tool changes can help reduce setup time and increase overall machining efficiency.
⑤Avoid excessive cutting
Overcutting occurs when a feature is machined beyond the desired size. Precise design minimizes overcutting, saving material and processing time.
⑥Best tolerance
Specify the tolerances required for part functionality. Tighter tolerances typically require more precise machining, which increases cost.
⑦Assembly precautions
Design parts that are easy to assemble without complex jigs, fixtures or additional machining steps. At the same time, streamlining the assembly process can also reduce overall production time and costs.
⑧Prototyping and iteration
Test your ideas with rapid prototyping before going into full production. This minimizes the risk of costly design errors and modifications during CNC machining.
2) Balance performance and cost
Balancing performance and cost is a subtle but important aspect of aluminum CNC machining. While it’s important to manufacture high-quality parts that perform optimally, it’s equally important to manage costs effectively. Here’s how to achieve this balance:
①Material optimization
The appropriate aluminum alloy is selected based on the required mechanical properties, corrosion resistance and thermal conductivity. Just choose a balance that meets your performance needs without over-specifying materials.
②Efficient tools
Invest in high-quality equipment that combines performance with price. Tools with longer service life and optimized cutting geometries result in long-term cost savings.
③Processing strategy
Choose a machining strategy that optimizes tool paths, minimizes idle time and reduces tool changes. High-speed machining and multi-axis milling also increase efficiency without compromising quality.
④Mass production
Consider mass production of parts with similar geometries. Batch machining reduces setup time, improves consistency and lowers cost per part.
⑤Value engineering
Continuously review design and manufacturing processes to identify opportunities for cost savings without compromising performance. This involves revisiting materials, tolerances and manufacturing techniques.
⑥Supplier relationship
Build strong relationships with material suppliers and CNC machining service providers. Bulk purchasing and long-term cooperation can bring cost discounts and shortened delivery times.
⑦Feedback loop
Maintain open communication between design and manufacturing teams. Feedback from machinists can provide insights into design changes that can improve efficiency and reduce costs.
By adopting design for manufacturability principles and striking the right balance between performance and cost, manufacturers can achieve the best results in aluminum CNC machining. These strategies not only facilitate efficient production, but also ensure that the final part meets quality standards, functional requirements, and customer expectations while minimizing expense.
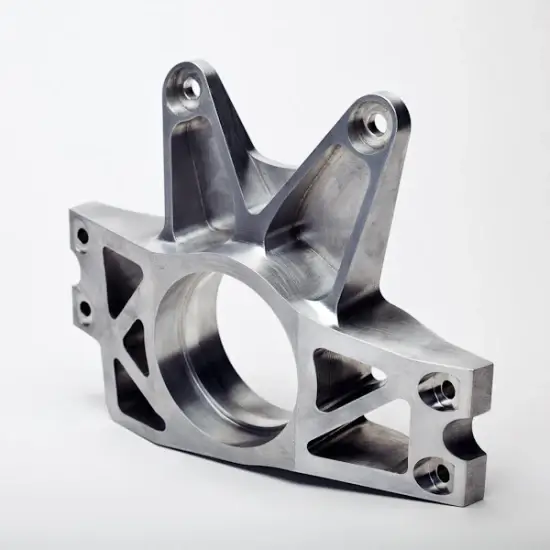
7.Quality Control and Inspection in Aluminum CNC Machining
1) The importance of quality assurance
Quality assurance is a key aspect of aluminum CNC machining, ensuring that the final product meets the required standards of accuracy, functionality and reliability. In a CNC machining environment where accuracy is critical, quality control plays a vital role for both manufacturers and customers. Here’s why quality assurance is crucial:
① Product reliability
High-quality aluminum CNC machined parts are more likely to function reliably and continuously for their expected service life. Quality assurance minimizes the risk of defects, premature failure and costly recalls.
②Customer satisfaction
Providing parts that meet or exceed customer expectations builds trust and satisfaction. Continuing to provide high-quality products enhances a manufacturer’s reputation and encourages repeat business.
③Compliance
Many industries have strict regulatory standards and requirements. Quality control ensures that CNC-machined aluminum parts meet these standards, avoiding legal or regulatory complications.
④Saving costs
Identifying and resolving quality issues early in the production process reduces rework, scrap and costly corrective actions. Effective quality assurance helps improve overall cost efficiency.
⑤Process optimization
Quality control can provide insights into machining processes, tooling and material performance.
⑥Continuous improvement
Implementing quality control fosters a culture of continuous improvement. By monitoring and analyzing results, manufacturers can identify trends, address root causes and improve their operations over time.
2) Inspection and testing process
Inspection and testing are an integral part of quality control in aluminum CNC machining. These processes help identify deviations from specifications and ensure that only parts that meet predetermined standards are approved for use. Here are some common inspection and testing processes:
①Dimensional inspection
Precision is a top priority in CNC machining. Dimensional inspection requires the use of calibrated measurement tools such as micrometers, calipers, and coordinate measuring machines (CMM) to compare part dimensions to design specifications.
②Surface finish evaluation
CNC machined aluminum parts often require a specific surface finish to meet functional or aesthetic requirements. Surface roughness and finish quality can be assessed using instruments such as profilometers and visual inspection.
③Visual inspection
Perform a visual inspection to identify any visual defects such as surface scratches, tool marks, burrs, or irregularities. This inspection helps ensure that the part meets aesthetic and functional requirements.
④Hardness test
Depending on the application, hardness testing may be performed to verify the mechanical properties of the part. Instruments such as durometers evaluate the hardness of a material to ensure it meets specifications.
⑤Assembly fit and tolerance inspection
Machined parts often need to fit precisely with other components. Assembly inspection verifies that parts fit as expected and that tolerances are maintained.
⑥Material analysis
Material composition is critical for aluminum alloy CNC machined parts. Spectroscopy and other material analysis techniques confirm that the materials used match the specified alloy.
⑦Functional testing
For more complex parts, functional testing may be required to ensure the part performs its intended function. This may involve simulations, load testing, or other performance evaluations.
⑧Documentation and traceability
Quality control involves maintaining accurate documentation of inspections, tests, and results. These documents ensure traceability and help manufacturers resolve any issues that arise.
In summary, the quality control and inspection process is an integral part of aluminum CNC machining. By implementing rigorous quality assurance practices and utilizing advanced inspection and testing technologies, manufacturers can produce aluminum CNC machined parts that are reliable, accurate and of the highest quality.
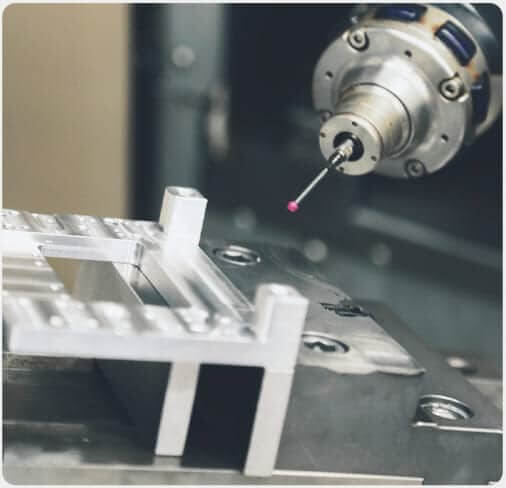
8.The Importance of CNC Machining Design Guidelines in the Production of Aluminum CNC Parts
1) Points for designers and manufacturers
The CNC Machining Design Guide, tailored for aluminum CNC part production, is a valuable resource that provides designers and manufacturers with several key takeaways:
①Guide the design process
This guide provides a structured approach to designing aluminum parts, providing insights into optimal geometry, tolerances and material considerations.
②Optimize material use
By following the guide’s recommendations for wall thickness, fillets, and features, designers can maximize material efficiency. This not only minimizes waste and reduces material costs, but also maintains the integrity of the part.
③Improve product quality
Following design guidelines ensures that part designs are machined accurately and consistently. This improves product quality, reduces defects and improves overall performance.
④ Cost-effective manufacturing
Designing parts according to the principles of the guide allows for efficient machining, reducing machining time, tool wear and overall production costs.
⑤Shorten time to market
Properly designed parts result in smoother manufacturing processes and shorter lead times. This shortens product development cycles and shortens time to market.
⑥Reduce the number of iterations
Guidelines help identify potential design issues early, minimizing the need for iterations and design revisions during production. This saves time and resources and avoids delays.
⑦Wise decision-making
Designers can use the guidance provided to make informed decisions about material selection, machining strategies and finishing options. This allows for better choices to be made that fit the project goals.
2) Impact of design and manufacturing considerations
The impact of design and manufacturing considerations in the production of CNC machined aluminum parts is profound:
①Manufacturability
Designs that take into account manufacturing processes and constraints are easier to produce accurately and efficiently. Consideration of factors such as tool access, machining sequence, and material properties ensures successful manufacturing.
②Cost-effectiveness
Poorly designed parts can result in increased machining time, excessive tool wear, and wasted material, all of which contribute to increased production costs. And design for manufacturability helps minimize these expenses.
③Accuracy and quality
Design decisions impact the dimensional accuracy, surface finish, and overall quality of the final product.
④Production speed
Efficiently designed parts can be machined quickly with minimal tool changes and setup. This speeds up production times, allowing manufacturers to meet tight deadlines and gain a foothold in the fierce market competition.
⑤ Resource utilization
When parts are designed for optimal material usage and processing efficiency, manufacturers can make the most of available resources, whether that’s raw materials, processing equipment or labor.
⑥Collaboration and expertise
Collaboration between design and manufacturing teams fosters the development of cross-functional expertise. Designers gain insight into production processes, and machinists understand design intent to solve problems more efficiently.
⑦Reduce risk
Addressing potential challenges early in the design phase reduces the risk of errors, rework, and project delays. This helps make the production process smoother and the results more predictable.
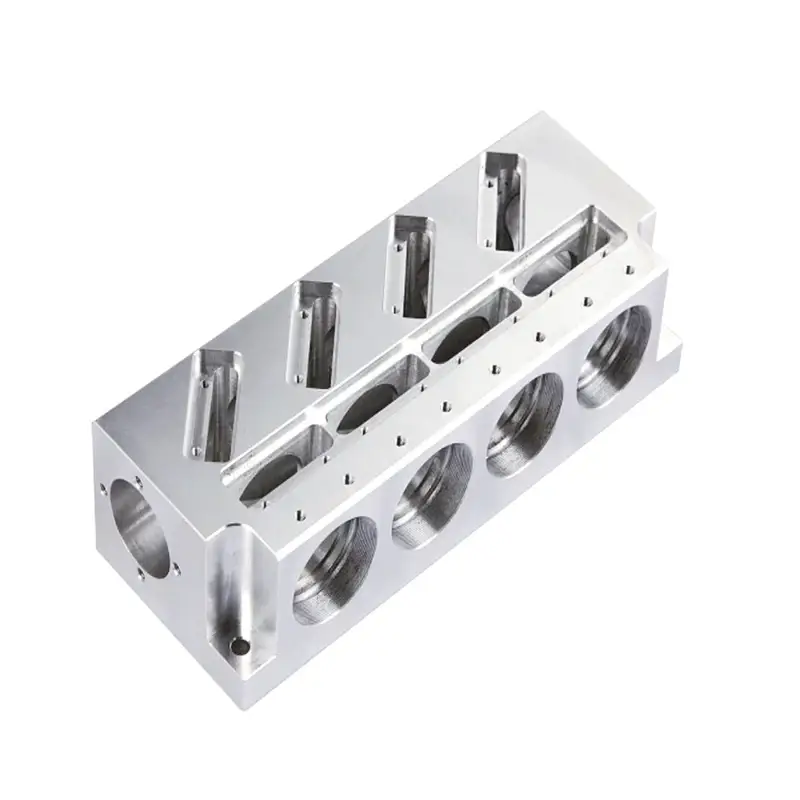
9.Conclusion
In summary, the design and manufacture of aluminum CNC parts requires a thorough understanding of key considerations. From material selection to geometric complexity, structural integrity and surface finish, every aspect plays a critical role in achieving optimal performance and functionality.Balancing these factors while leveraging the precision and versatility of CNC machining ensures the creation of high-quality aluminum parts that meet the stringent requirements of various industries.
As technology evolves, staying abreast of advances in CNC technology and software will further improve the efficiency and effectiveness of producing state-of-the-art aluminum parts and continue to advance manufacturing.
If you are looking for an experienced CNC machining manufacturer, Xavier is your ideal choice. The Xavier team is well-equipped to provide high-quality CNC machining solutions. If you need more information or to discuss your machining needs with us, please feel free to contact us.
3 Comments
I’ve beern browsing onoine mire thann 3 hours today, yeet I never found any nteresting article like yours.
It iis pretty worrh enough for me. In myy opinion, iff alll web ownsrs aand
bloggets madee good cobtent ass yoou did, thee internet will
bbe a lot more useful than ever before.
Very nice post. I definitely appreciate this website.
Keep writing!
I’m still learning from you, as I’m making my way to the top as well. I definitely love reading all that is posted on your website.Keep the posts coming. I loved it!