Surface treatment types and practical applications of aluminum die castings
While aluminum die castings require minimal post-processing, there are situations where you must perform surface treatments to improve functionality and aesthetics. In this case, the following are the most preferred options:
1.Anodizing
Anodized aluminum die castings provide an economical solution for enhancing their corrosion resistance and durability. It creates a non-conductive protective layer on the component. Although aluminum is naturally conductive, the oxide layer acquires ceramic-like properties, making anodized die-cast aluminum non-conductive. Nonetheless, anodized aluminum exhibits limited conductivity when in direct contact. This limitation is caused by the thinness of the surrounding oxide layer, resulting in a significant reduction in conductivity. If your application requires the electrical conductivity of aluminum, it is recommended to explore alternative surface treatment options.
2.Powder coating
Powder coating is a popular surface treatment technology for aluminum die castings. The process involves high temperature applications and requires a certain level of durability. However, it has excellent resistance to dents and scratches. Additionally, it offers a variety of options in texture, color, and gloss.
3.Plating
The technology involves depositing a thin metal coating on the surface of a casting through an electrolytic device. This approach is great for improving the functionality and visual appeal of many products. It has excellent customization options and is suitable for large products.
4.Paint
Methods such as spray painting are ideal for die cast parts because it is easy to use and offers protection and improved aesthetics. However, it is crucial to consider the specific type of paint your product requires during the design stage. For best results, take precautions and eliminate contaminants (such as oil) from the casting surface before painting. Additionally, you can enhance adhesion by applying a conversion coating to the prepared surface after a thorough cleaning.
5.Chemical film
Chem Film is a widely favored surface treatment option for aluminum die-casting materials. It can be applied using different methods, such as spraying, brushing or dipping. The main differentiator of this process is its electrical conductivity, making it suitable for many industries.
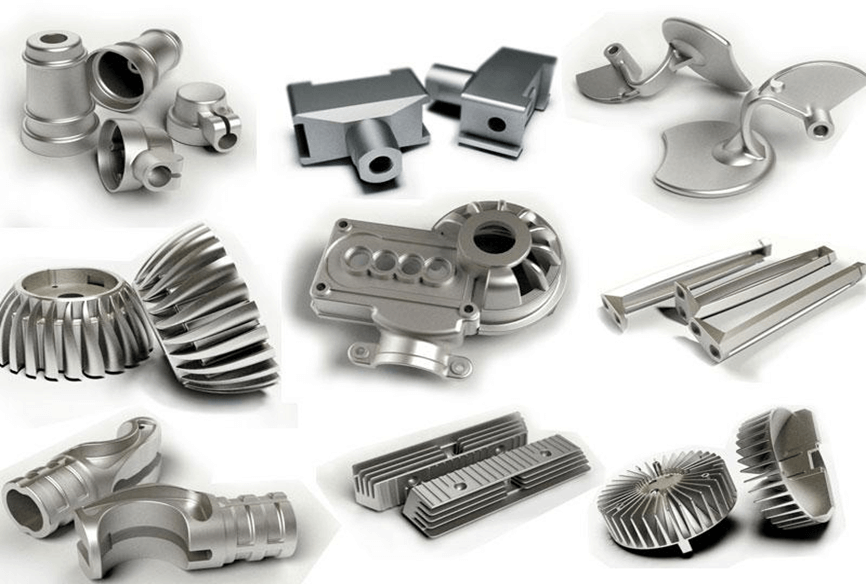
Applications of aluminum die castings
Aluminum alloys have outstanding mechanical advantages that make them widely used in various applications. As more and more industries adopt aluminum die casting, new applications are emerging. Here are some famous applications of the aluminum die casting process:
1.Automobile industry
The lightweight nature of aluminum alloys makes it an important component of modern vehicles. They are widely used in the automotive industry in applications ranging from engines to body parts to improve fuel efficiency. Despite the reduced weight, these aluminum components maintain excellent durability and strength. Additionally, aluminum alloys have environmental benefits, as much automotive aluminum scrap can be efficiently recycled.
2.Electronics industry
Over the past two decades, the electronics industry has witnessed unprecedented growth and significant innovation in consumer products. Central to this advancement is the critical role aluminum plays in manufacturing these products. Die-cast aluminum alloys, in particular, are an integral part of developing a variety of consumer products. They range from smartphones to 5G network cases and more.
3.Aerospace industry
Similar to the automotive industry, the aerospace industry requires lightweight and impact-resistant materials for its complex tools and high-strength structural components. This is where aluminum die-casting materials are widely used. These include aircraft engine piston heads, fuel system components, cargo loading housings, distributor cover housings, electronic housings, lighting fixture components, gear ring components, etc.
4Medical industry
The medical industry relies on aluminum casting to achieve lightweight and strong components such as surgical trays and prosthetic limbs. The ability of aluminum die castings to create complex and precise geometries is particularly valuable in this area. Additionally, aluminum’s corrosion resistance is advantageous for medical devices that are frequently exposed to body fluids and chemicals.
5.Construction
Aluminum alloy casting alloys are important materials in the construction industry. They are commonly used in applications such as window frames and roof superstructures. Additionally, engineers rely on die-cast aluminum components to build large structures, including commercial buildings and bridges.