Pros and Cons of Aluminum Injection Molds
There are several factors to consider when choosing the right type of plastic injection mold for your manufacturing needs. One of the most important decisions you need to make is whether to use an aluminum injection mold or a steel injection mold. Both options have their own advantages and disadvantages, and understanding these can help you make an informed decision. For example, become a better plastic parts engraving machine manufacturer.
The main advantages of aluminum injection molds
One of the main advantages of aluminum injection molds is their cost-effectiveness. Aluminum is a relatively inexpensive material compared to steel, making it a popular choice for manufacturers on a budget. In addition, aluminum molds can be produced faster than steel molds, which helps shorten delivery times and get plastic parts engraving machine manufacturer’s products to market faster.
Another advantage of aluminum injection molds is their light weight. Because aluminum is much lighter than steel, this makes handling and shipping of molds easier. And if the mold needs to be moved frequently or the space in the manufacturing plant is limited, aluminum injection molds will be more beneficial.
In addition to being lightweight, aluminum injection molds also offer excellent thermal conductivity. This means that they can cool down and heat up more quickly than steel molds, resulting in shorter cycle times. This is particularly beneficial if the plastic parts engraving machine manufacturer has high-volume production needs and wants to maximize efficiency.
However, it is important to note that aluminum injection molds are not without their drawbacks. One of the main disadvantages is their lower durability compared to steel molds. Aluminum is a softer material, which means that it is more prone to wear and tear over time. This can result in a shorter lifespan for the molds and the need for more frequent replacements.
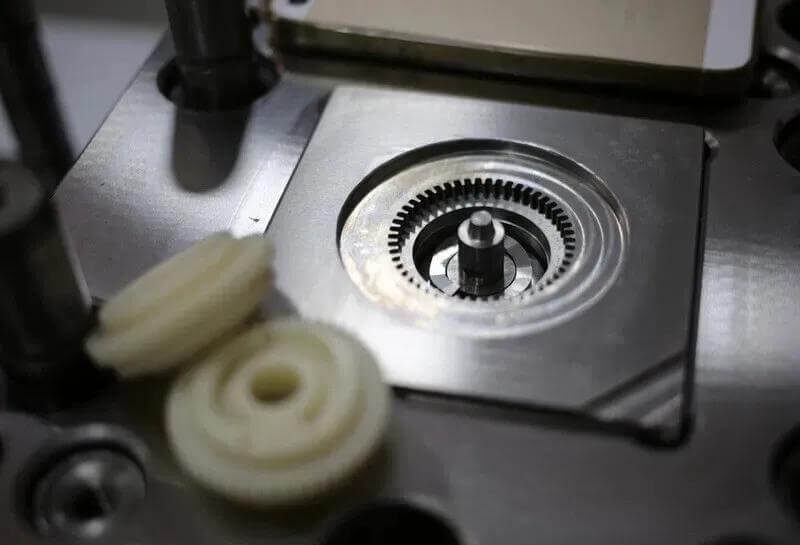
Furthermore, aluminum injection molds may not be suitable for all types of materials. Certain plastics, such as those with high melting points or corrosive properties, may not be compatible with aluminum molds. In these cases, a steel mold would be a more appropriate choice.
Another potential drawback of aluminum injection molds is their limited ability to withstand high pressures. Steel molds are generally more robust and can handle higher injection pressures without deformation. If your manufacturing process requires high-pressure injection, a steel mold may be the better option.
In conclusion, both aluminum and steel injection molds have their own set of advantages and disadvantages. Aluminum molds are cost-effective, lightweight, and offer excellent thermal conductivity. However, they may not be as durable as steel molds and may not be suitable for all types of materials or high-pressure applications. On the other hand, steel molds are more durable and can withstand higher pressures, but they are more expensive and have longer lead times. Ultimately, the choice between aluminum and steel injection molds will depend on your specific manufacturing needs and budget.