The Basics of Aluminum Machining
Aluminum machining is a crucial process in various industries, including aerospace, automotive, and electronics. Understanding the basics of aluminum machining is essential for manufacturers and engineers to produce high-quality products efficiently. In this section, we will delve into the fundamental aspects of aluminum machining, including its properties, common machining processes, and the challenges associated with machining this versatile metal.
Aluminum is a lightweight, durable metal with excellent corrosion resistance, properties that make it ideal for many applications. However, aluminum’s low melting point and high thermal conductivity create challenges in the machining process, as machining aluminum requires careful consideration of cutting parameters, tool selection and coolant use to ensure optimal results.
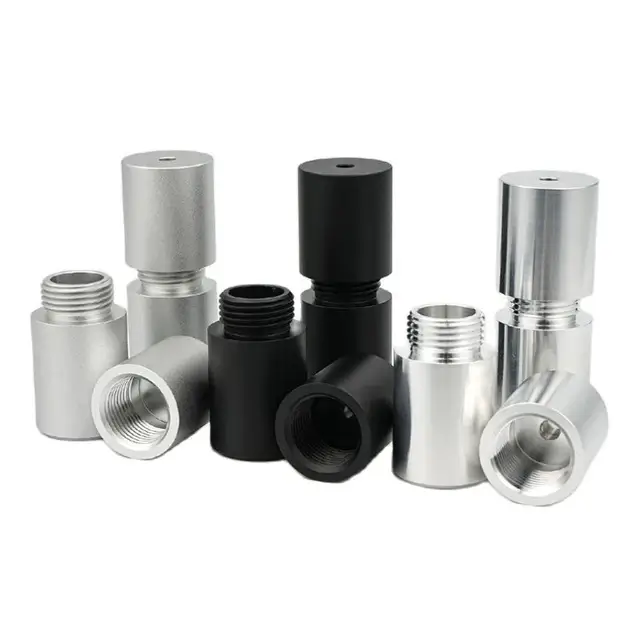
Aluminum processing technology
One of the most common machining processes for aluminum is milling. Milling involves using rotating tools to remove material from a workpiece and is a versatile process that can be used to create a variety of shapes and features. When milling aluminum, high spindle speeds and low feed rates are typically used to prevent excessive heat build-up, a detail that helps avoid melting the aluminum and extends tool life.
Another widely used aluminum machining process is turning. Turning involves rotating a workpiece while a cutting tool removes material to create cylindrical shapes. When turning aluminum, sharp cutting tools and high cutting speeds are recommended to minimize heat generation. Additionally, using a coolant is crucial to dissipate heat and prevent workpiece deformation.
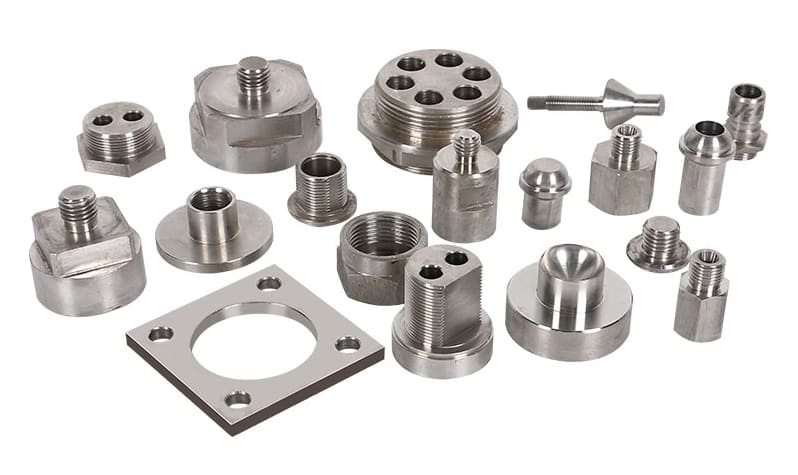
Drilling is another essential aluminum machining process. It involves creating holes in a workpiece using a rotating cutting tool. When drilling aluminum, high cutting speeds and low feed rates are preferred to prevent chip clogging and reduce heat buildup. Proper chip evacuation is crucial to avoid workpiece damage and ensure hole accuracy.
Aluminum machining also involves facing, where the cutting tool removes material from the end face of a workpiece to create a flat surface. Facing is commonly used to achieve precise dimensions and improve surface finish. Similar to other machining processes, high cutting speeds and proper coolant usage are essential for successful facing of aluminum.
Aluminum Processing Challenges
Despite its many advantages, aluminum machining presents some challenges. One of the main challenges is the tendency of aluminum to generate built-up edge (BUE) during cutting. BUE occurs when the material adheres to the cutting tool, leading to poor surface finish and increased tool wear. To mitigate this issue, using sharp cutting tools and appropriate cutting parameters is crucial.
Another challenge in aluminum machining is the formation of built-up heat. Aluminum’s high thermal conductivity causes heat to transfer rapidly to the cutting tool, leading to tool wear and workpiece deformation. Proper coolant usage and controlling cutting parameters can help dissipate heat and prevent these issues.
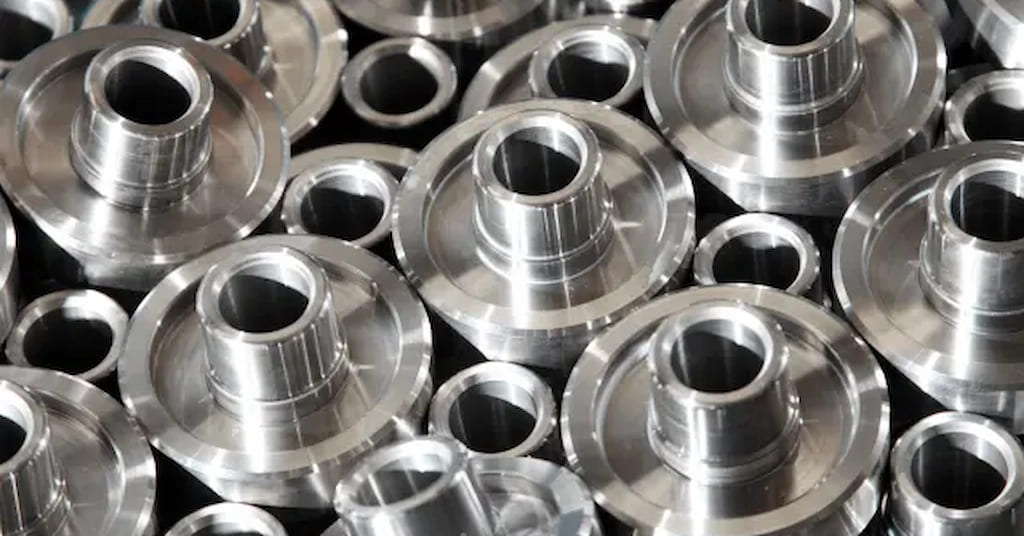
In conclusion
understanding the basics of aluminum machining is essential for manufacturers and engineers in various industries. Aluminum’s unique properties and challenges require careful consideration of cutting parameters, tool selection, and coolant usage. By employing the right techniques and tools, manufacturers can achieve high-quality results and maximize the benefits of aluminum as a versatile material.