Basics of Aluminum Machining
Aluminum is one of the most widely used CNC materials in machine shops. It is widely used in manufacturing and prototyping to develop various industrial products because of its various advantages. In this regard, this guide will show some general characteristics of aluminum machining and how its different surface treatment methods work in reality. In addition, if you are a beginner, you will learn a lot about it and this guide will lay a good foundation for you to learn.
1.Why are aluminum alloys easy to machine?
Aluminum alloys are world leaders in the field of part manufacturing and prototyping. Not only do these alloys have high strength and excellent corrosion resistance, they are also easier to machine than any other material and are much lighter than steel. In addition, aluminum alloys are no worse than heavy metals in terms of load bearing. But it is important to remember that heavy metals are still the first choice where high rigidity is required.
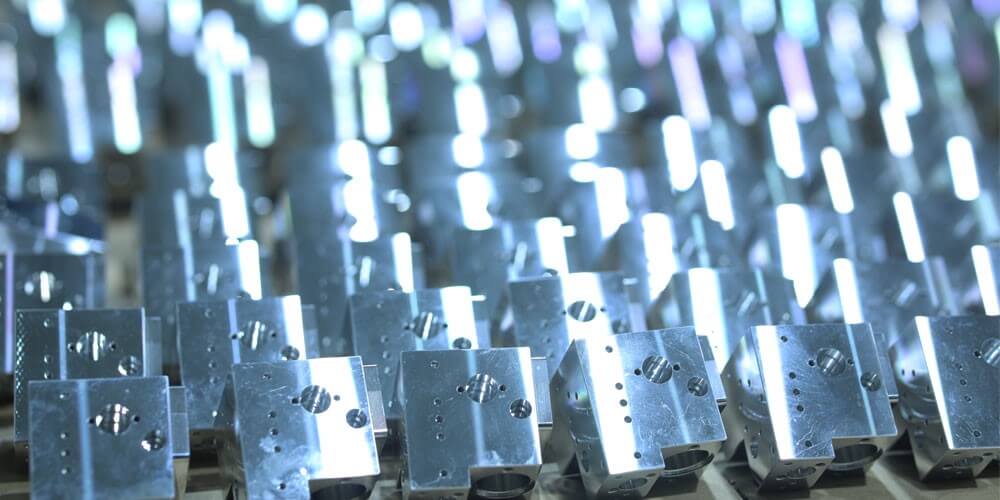
2.Suitable surface treatment methods for aluminum prototypes
Aluminum alloys can be machined at high speeds due to their soft nature, and their good thermal conductivity helps to quickly dissipate heat from the cutting area, reducing wear on the cutting tool and extending its service life. After machining, the final aluminum part usually does not need coating or painting to prevent corrosion because the oxide film is enough to protect it. However, some surface treatments are possible, as we will see in the following sections.
Prototyping is suitable for manufacturing complex machine parts with extremely high precision and accuracy. In the design and development phase of prototyping, people are not concerned about technology and material selection. At this stage, aluminum processing plays a vital role in developing products through rapid prototyping, and it is mainly suitable for developing metal prototypes. At the same time, since aluminum is stronger and more durable than other metal alloys such as brass and copper, and these metals have higher machinability compared to steel and titanium alloys. Therefore, in most cases, manufacturers prefer aluminum processing to develop metal prototypes.
1) Painting
Aluminum workpieces already have corrosion protection due to the oxide film on the surface of the material. However, there are also some other surface treatment techniques for aluminum prototypes to enhance the corrosion resistance of aluminum parts. For example, standard paint can be used for surface coating, which also has different variations to provide an aesthetic appearance to the final part and prevent adverse environmental effects.
2) Anodizing
Another method used for surface treatment is anodizing. In this process, the aluminum workpiece is connected to a circuit to remove impurities from the surface. This process creates micropores on the surface of the material, which increases the depth of the oxide layer and the corrosion resistance of the aluminum alloy. Additionally, a coat of paint can be applied to fill the pores created on the surface of the material. The result of this process will be a matte surface in the color you want.
3) Grinding and Polishing
Grinding and polishing can also be used to create a mirror-like surface. Grinding removes burrs from the surface of the material, allowing for high accuracy and precision. Polishing, on the other hand, creates a shiny, smooth surface, giving manufacturers a polished metal look.
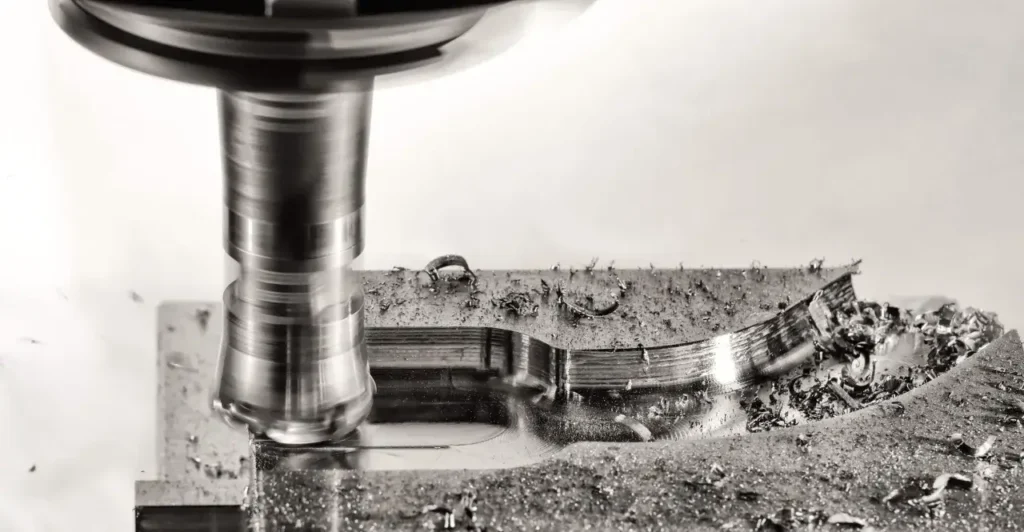
3.Different Applications of Aluminum Machined Parts
1) Construction Industry
Construction is synonymous with the building industry. Buildings do not corrode due to the use of aluminum. This helps in designing and developing projects that are suitable for modern needs. In construction, industrial aluminum comes in many forms, including profiles, rolled products, and solid forms. Aluminum has a beautiful surface and does not need to be cleaned, so aluminum is mostly used in exhibition halls, disaster relief rooms, temporary courtyards, etc.
2) Electrical Industry
Aluminum can be made into thin wires and is often used in products such as telephone wires and light bulbs. Due to its low density, aluminum is ideal for long-distance power transmission lines. At the same time, aluminum is more ductile and can be easily formed into more wires, so in addition to power transmission lines and cables, aluminum can also be used in electrical appliances, motors, and power systems.
3) Transportation Industry
Aluminum is ideal for the transportation industry because it is strong and lightweight. The main uses of aluminum are automobiles, railways, ships, and aircraft. Using aluminum parts is more advantageous than other metals because it is easier to shape and improves efficiency. At the same time, the light weight of aluminum also means low fuel consumption and emissions.
4) Aerospace Industry
Aluminum is an excellent material for making aircraft parts, so it is very suitable for the aviation industry. Aluminum has high corrosion resistance, excellent ductility, and a high strength-to-weight ratio. It also relieves any stress from high-altitude flight.
5) Consumer Goods Industry
The consumer goods industry is one that is very dependent on the consumption of aluminum CNC machined parts. You may be reading this article on a device, smartphone, or laptop, and every new electronic product comes with an aluminum body and components. Also because aluminum is stronger than plastic, which allows the material to absorb and dissipate heat.
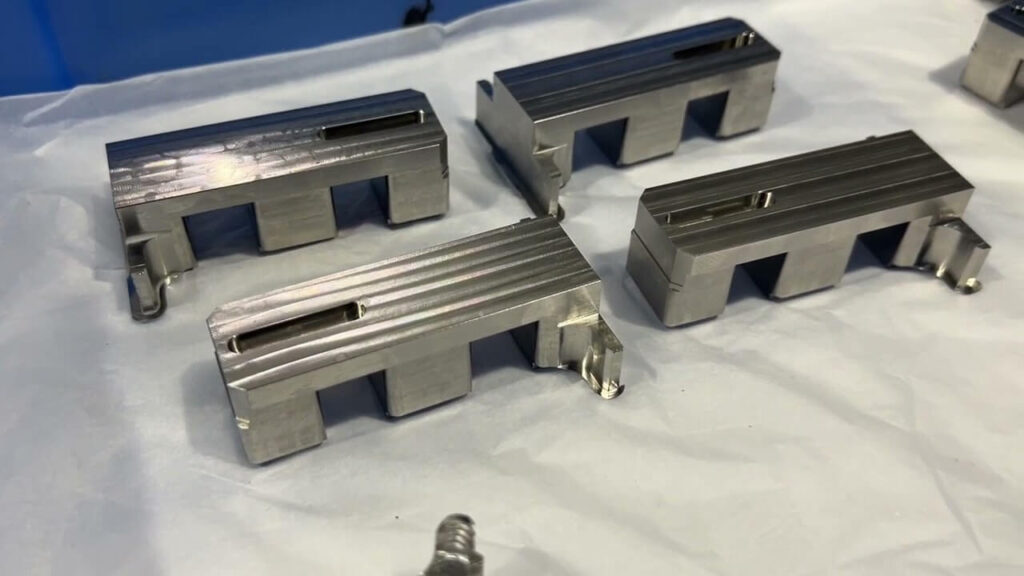
4.Specific parameters of aluminum processing process
Some important specifications must be considered during aluminum processing. Before processing aluminum alloy, you need to adjust the following parameters:
- Spindle speed exceeds 12,000 rpm (provides a smooth surface finish).
- Use tools with 2 or 3 grooves in this process.
- Maintain a high feed rate.
- Properly arrange the use of coolant.
- Use soft fixtures.
- Always check the chip discharge repeatedly.
- Use carbide tools for aluminum processing.
- Make sure your chip conveyor is working properly.
After adjusting the above parameters, aluminum alloy can be processed.
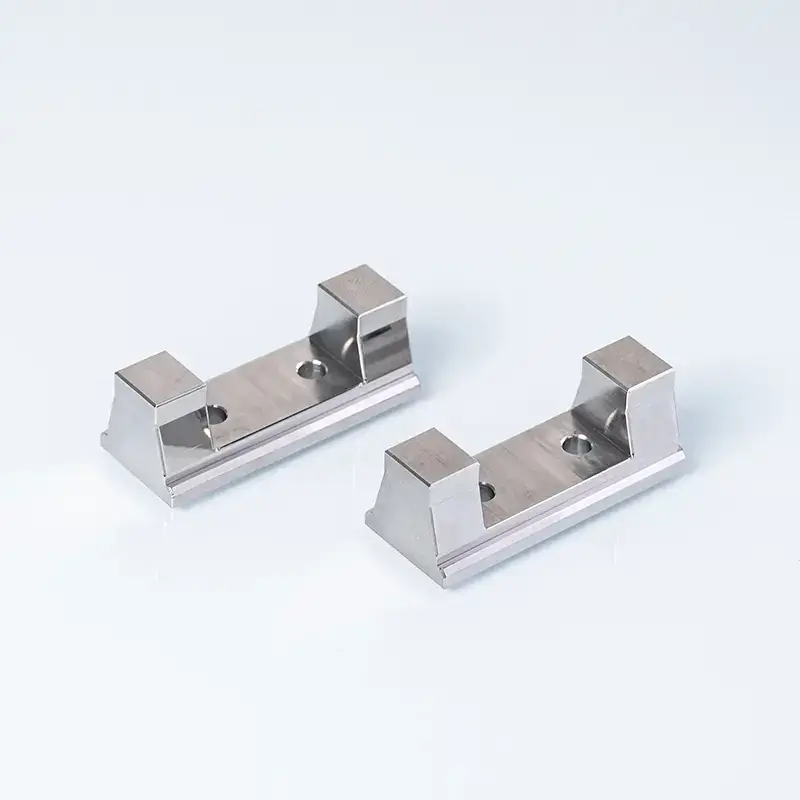
5.Summary
After discussing aluminum processing in detail, we come to the conclusion that it is best suited for the prototyping process. Since aluminum has some extraordinary abilities such as corrosion resistance, light weight, easy processing, and high strength, most companies prefer aluminum processing for rapid production of prototypes. This will also increase its market demand.
To improve the performance of aluminum parts, different surface treatment techniques can also be used to obtain high surface quality. For this purpose, painting, grinding and anodizing can be performed to improve. Therefore, aluminum parts lead the world with their high mechanical and chemical properties and are widely used in every industrial field, especially in the automotive and aerospace industries.
It is also important to note that aluminum processing should adopt specific parameters such as high feed rates, high spindle speeds, coolant availability and suitable tool selection. When machining at low feed rates and low spindle speeds, chips become difficult to remove, resulting in poor surface quality.
Finally, we concluded that more than 60% of manufacturers prefer to use aluminum for developing prototypes. But only highly trained personnel are allowed to carry out the machining process. The process can be performed on manual lathes or CNC machines, but the parts produced through CNC machining will have a better final product quality.