The Benefits of CNC Engraving Aluminum Parts with 3D Printed Fixtures
Using 3D printed fixtures for CNC engraving of aluminum parts offers a range of advantages that make it an attractive option for many industries. This innovative approach combines the precision and durability of CNC engraving with the flexibility and cost-effectiveness of 3D printing. Tombstone machining is also one of the many fixtures available.
By using 3D printed fixtures, manufacturers can achieve greater precision and efficiency in the engraving process, producing a high-quality finished product.
Key benefits of 3D printing aluminum parts
One of the key advantages of using 3D printed fixtures for CNC engraving aluminum parts is the ability to create custom fixtures quickly and easily. Traditional fixtures often require time-consuming and expensive machining processes, which can be a significant barrier to entry for small businesses or those with limited resources. With 3D printing, however, manufacturers can design and produce fixtures in-house, reducing lead times and costs.
Additionally, 3D printed fixtures offer a high level of customization. Because during the 3D printing process, manufacturers can easily modify and iterate their designs, allowing for rapid prototyping and testing. This flexibility is especially valuable in industries where product designs change frequently or where customization is a key requirement, because by using 3D printed fixtures, manufacturers can adapt to changing customer needs and stay ahead of the competition.
In addition to customization, 3D printed fixtures offer greater accuracy and repeatability. Because CNC engraving requires precise positioning of the part to achieve the desired depth and detail of the engraving. Traditional fixtures cannot always provide the necessary level of accuracy, resulting in inconsistent finished products. On the other hand, 3D printed jigs can also be designed with tight tolerances and specific features to ensure precise alignment and positioning of parts, allowing for consistent and high-quality engraving across multiple parts.
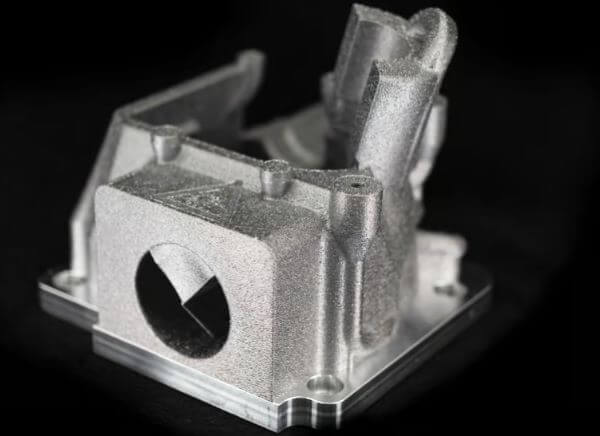
Another benefit of using 3D printed fixtures for CNC engraving aluminum parts is the reduced risk of damage to the part. Traditional fixtures often require clamping or other methods of securing the part in place, which can lead to scratches, dents, or other forms of damage. 3D printed fixtures, on the other hand, can be designed with features that securely hold the part without causing any harm. This is particularly important when working with delicate or expensive materials, where even minor damage can be costly.
Furthermore, 3D printed fixtures offer a lightweight and cost-effective alternative to traditional fixtures. Traditional fixtures are often made from metal or other heavy materials, which can be expensive and cumbersome to handle. 3D printed fixtures, on the other hand, can be produced using lightweight and affordable materials, such as plastic or resin. This not only reduces costs but also makes the fixtures easier to handle and transport.
In conclusion, CNC engraving aluminum parts with 3D printed fixtures offers a range of benefits that make it an attractive option for many industries. The ability to quickly and easily create custom fixtures, along with improved accuracy and repeatability, allows manufacturers to achieve high-quality engraving results. Additionally, the reduced risk of damage to the part, as well as the lightweight and cost-effective nature of 3D printed fixtures, further enhance the appeal of this innovative approach. As technology continues to advance, it is likely that more industries will adopt this method to improve their engraving processes and stay competitive in the market.