Benefits of Aluminum Prototyping in Product Development
Aluminum prototyping is a critical step in the product development process. It allows designers and engineers to create physical models of their designs before committing to mass production. Spare parts for hotpoint washing machines, swan coffee machine parts, taylor ice cream machine parts, tcl washing machine spare parts, and vintage singer machine parts can also use this process.
This article will explore the advantages of aluminum prototypes and help projects such as spare parts for hotpoint washing machines, swan coffee machine parts, taylor ice cream machine parts, tcl washing machine spare parts, and vintage singer machine parts decide which method is the most suitable.
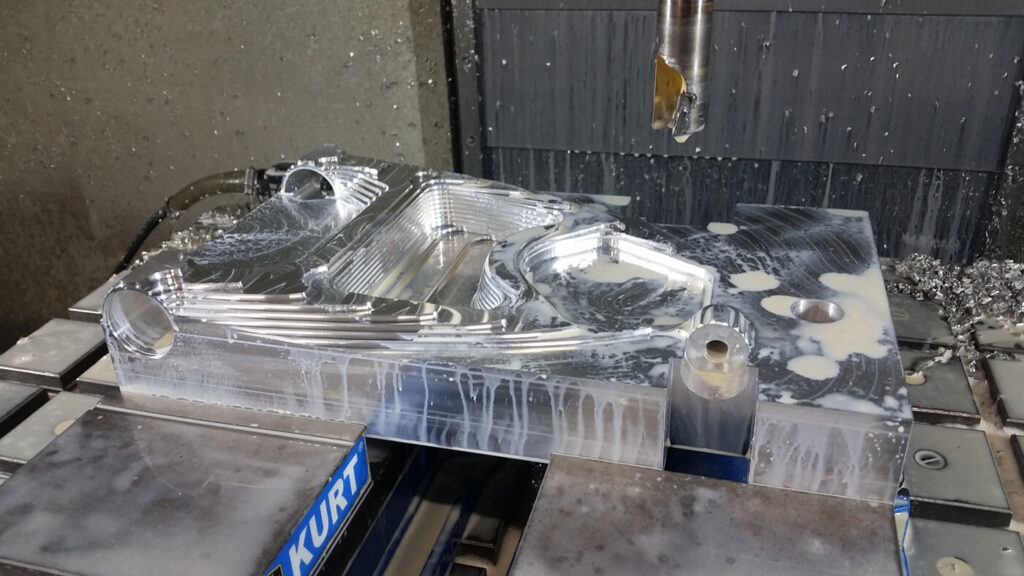
One of the key advantages of aluminum prototyping is its cost-effectiveness. Compared to other materials like steel or plastic, aluminum is relatively inexpensive. This makes it an ideal choice for prototyping, especially when multiple iterations are required. By using aluminum, you can save money on materials and production costs while still achieving high-quality prototypes.
Another benefit of aluminum prototyping is its versatility. Aluminum is a lightweight and malleable material, making it easy to shape and manipulate. This allows designers to create complex and intricate designs with ease. Whether you’re working on a small electronic device or a large industrial machine, aluminum prototyping can accommodate a wide range of product sizes and shapes.
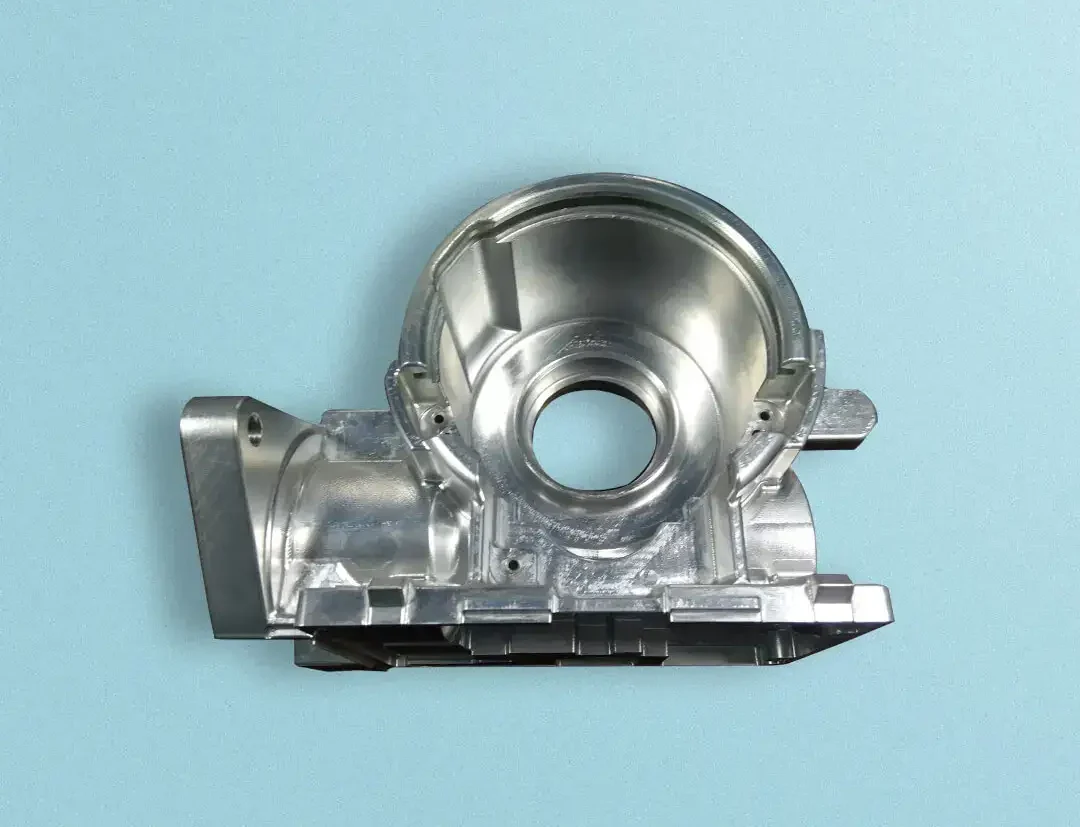
In addition to its versatility, aluminum offers excellent strength and durability. Despite its light weight, aluminum is known for its high strength-to-weight ratio. This means the aluminum prototype can withstand rigorous testing and evaluation without compromising its structural integrity. And whether your prototype is subject to mechanical stress or environmental conditions, aluminum can rise to the challenge and ensure functionality.
Furthermore, aluminum prototyping offers excellent thermal conductivity. This is particularly important for products that generate heat, such as electronic devices or automotive components. Aluminum’s ability to dissipate heat efficiently ensures that your prototype remains cool and functional even under demanding conditions. By using aluminum, you can test the thermal performance of your design and make any necessary adjustments before moving on to mass production.
When it comes to surface finish, aluminum prototyping also shines. Aluminum can be easily polished, anodized, or coated to achieve the desired aesthetic and functional properties. This allows designers to create prototypes that closely resemble the final product in terms of appearance and performance. Whether you’re looking for a sleek and glossy finish or a textured and rugged surface, aluminum can deliver.
Now that we’ve explored the benefits of aluminum prototyping, let’s discuss how to decide on the best approach for your project. The first step is to assess your specific requirements and constraints. Consider factors such as budget, timeline, and desired level of detail. This will help you determine whether you should opt for traditional machining, 3D printing, or a combination of both.
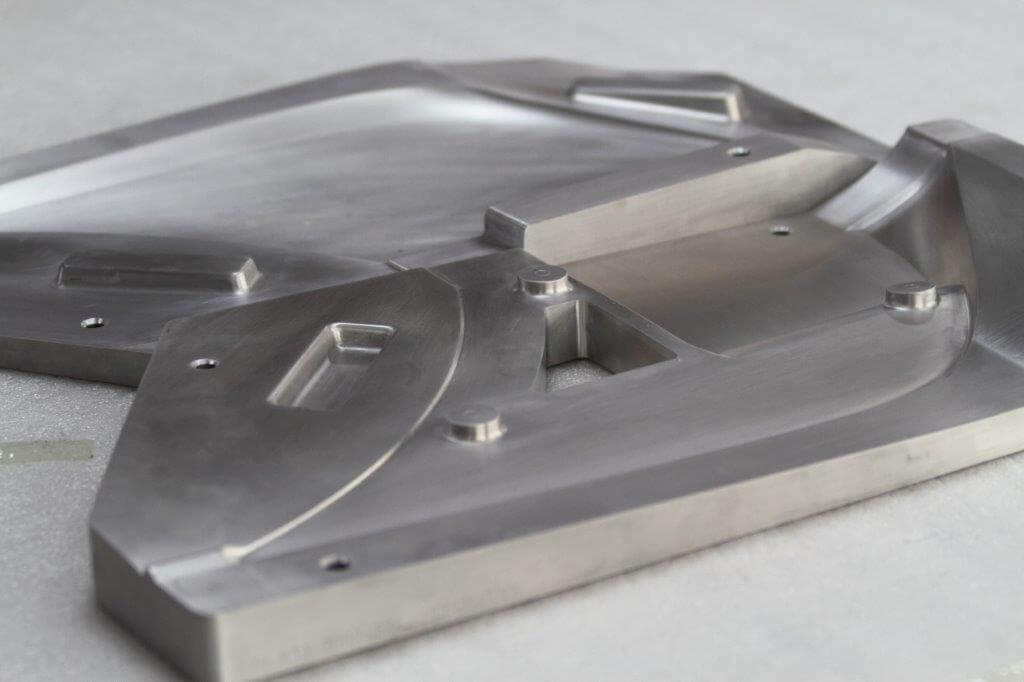
Traditional machining involves cutting, drilling, and shaping aluminum using CNC machines. This approach is suitable for projects that require high precision and intricate details. On the other hand, 3D printing offers greater design freedom and faster turnaround times. It is ideal for projects that involve complex geometries or rapid prototyping.
In some cases, a combination of traditional machining and 3D printing may be the best approach. This hybrid method allows you to leverage the strengths of both techniques while minimizing their limitations. For example, you can use traditional machining for critical components that require high precision and 3D printing for larger, less detailed parts.
In conclusion, aluminum prototyping offers numerous benefits in product development. Its cost-effectiveness, versatility, strength, thermal conductivity, and surface finish make it an excellent choice for creating high-quality prototypes. By assessing your specific requirements and constraints, you can determine the best approach for your project, whether it involves traditional machining, 3D printing, or a combination of both.