Introduction to various aluminum tube surface treatment technologies
Aluminum is a versatile material that is used across a wide range of industries due to its light weight, corrosion resistance and good thermal conductivity, including the production of bmw owings mills parts, enco mill drill parts, gray mills parts washer and grinding mill parts.
However, aluminum tubes often need to undergo surface treatment processes in order to improve their appearance, protect them from environmental factors or improve their functionality. These processes can be divided into several categories, each with its own advantages and limitations, which can ensure the effectiveness of many parts such as bmw owings mills parts, enco mill drill parts, gray mills parts washer and grinding mill parts.
1.Mechanical Finishing
This process involves the use of mechanical forces to alter the surface of the tube. One popular technique is polishing, and another mechanical finishing technique is brushing.
1) Polishing
Polishing involves the use of abrasive materials to create a smooth and reflective surface. Polishing not only enhances the appearance of the aluminum tube, but also improves its corrosion resistance by removing any surface defects that could be the starting point for corrosion. However, polishing is a time-consuming process and may not be suitable for large-scale production.
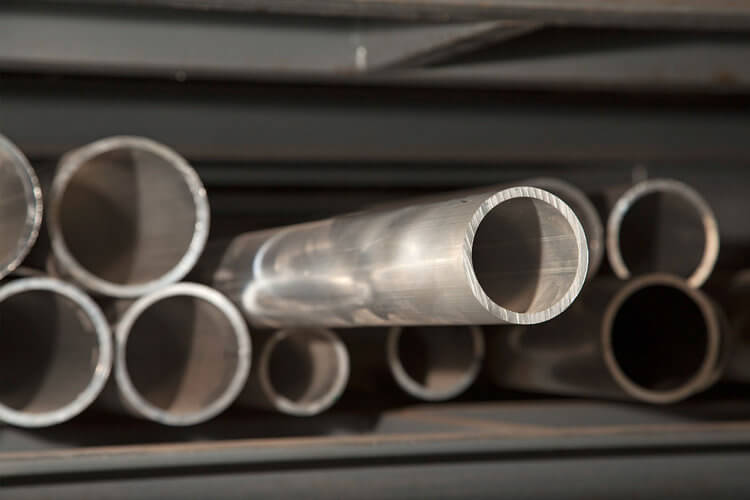
2) Brushing
Brushing requires the use of a wire brush or an abrasive pad to create a textured surface on the aluminum tube. As a result, this technique is often used to create a matte or satin finish that is both aesthetically pleasing and provides a better grip. However, brushing may not be suitable for applications that require a smooth and reflective surface.
2.Chemical Treatments
These processes involve the use of chemicals to alter the surface of the tube. One common technique is anodizing, which involves forming a protective oxide layer on the surface of the aluminum tube. Anodizing not only enhances the appearance of the tube by applying various colors, but also improves its corrosion and wear resistance.
However, anodizing is a complex process that requires careful control of chemical composition and temperature and may not be suitable for all aluminum alloys.
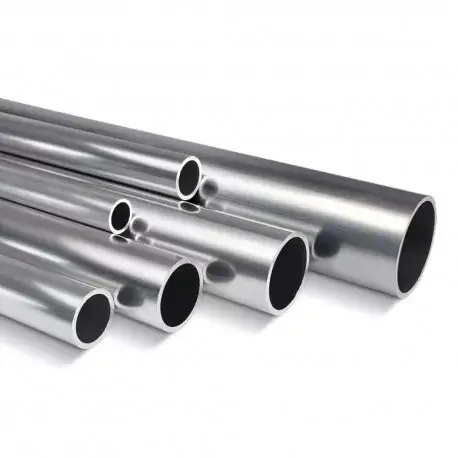
3.Electroplating
Electroplating is another chemical treatment technique used for the surface treatment of aluminum tubes. The process involves depositing a thin layer of metal on the surface of the tube through an electrochemical reaction. Electroplating enhances the appearance of aluminum tubes by providing a decorative and reflective coating.
It can also improve the corrosion and wear resistance of the pipes. However, electroplating requires the use of toxic chemicals and can be an expensive process.
4.Powder coating
The process involves applying dry powder to the surface of the tube and then heating it to form a protective and decorative coating. Powder coating offers excellent corrosion resistance, durability and a wide range of color options. It is also an environmentally friendly process as it does not involve the use of solvents. However, powder coating may not be suitable for applications that require a thin and uniform coating.
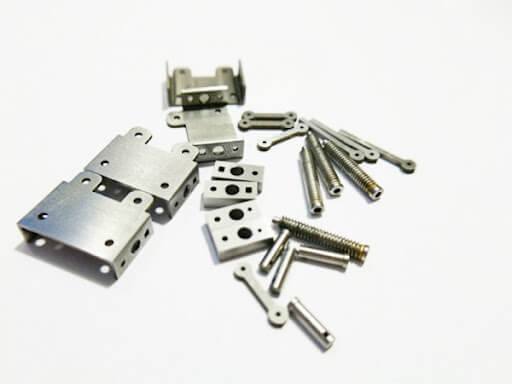
5.In summary
Aluminum tube surface treatment processes can be divided into several categories, each with their own advantages and limitations.
Mechanical finishing techniques such as polishing and brushing can enhance the appearance of the tube and improve its corrosion resistance. Chemical treatments such as anodizing and electroplating can provide a decorative coating and improve corrosion resistance. Powder coating offers excellent corrosion resistance, durability and a wide range of color options.
Understanding the advantages and limitations of these techniques is essential to selecting the most appropriate aluminum tube surface treatment process for various applications.