Basic introduction to nano machining technology
Nano machining technology involves the understanding, manipulation and control of matter at the nanoscale, i.e., approximately 1 to 100 nanometers in size. Nano machining technology is being applied across the entire spectrum of manufacturing processes and products. It has the potential to revolutionize manufacturing by developing faster, cleaner, and more energy-efficient systems and materials.
Nanomaterials and nanoelectronic devices are leading to enhanced manufactured products with new properties. The combination of nano machining technology and manufacturing processes is expected to transform entire industries in the 21st century.
1.Nano machining technology
Nano machining refers to the specialized manufacturing methods required to create nanoscale structures and devices, typically between 1-100 nanometers. There are two main approaches:
1) Top-down approaches
These techniques can manipulate larger-scale materials and structures down to the nanoscale.
- Photolithography is the transfer of mask patterns onto a photosensitive layer, which is common in semiconductor printing on integrated circuit silicon wafers.
- Micromachining uses tools to carve nanostructures, while etching uses acids to selectively erode materials to obtain nanometer-sized patterns.
- Direct writing methods, such as microcontact printing and dip-pen nanolithography, deposit nanoscale inks onto substrates.
2) Bottom-up methods
These techniques build nanostructures atom by atom or molecule by molecule.
- Chemical synthesis combines atoms/molecules into nanostructures through designed reactions.
- Molecular self-assembly spontaneously organizes molecules into stable nanoscale structures.
- Positional assembly uses external forces to guide nanoelements to assemble into organized patterns.
- Molecular beam epitaxy deposits single atomic layers onto crystalline substrates to grow nanostructures.
3) Other technologies for nano machining
- Computer modeling enables computational design, simulation, and analysis of nanomaterials
- Scanning detection techniques such as scanning tunneling microscopy allow direct imaging and manipulation of single atoms.
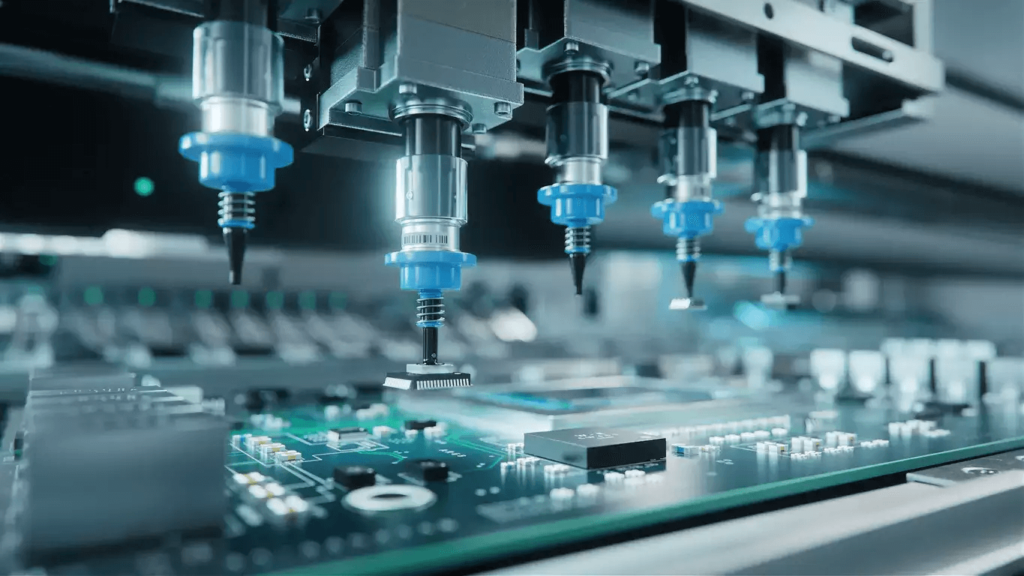
2.Innovation of nano machining technology in manufacturing
Nano machining technology is driving innovation across the manufacturing industry, including materials, industrial processes, quality control, and product design. These include:
1) Materials
Nano machining techniques can synthesize and design materials where the components are designed and organized at the nanoscale to achieve superior performance. This includes:
- Metal alloys: Alloy systems such as steel, magnesium and aluminum alloys can be enhanced by integrating nanoscale features such as nanoparticles, nanolayers and nanocomposites. This significantly improves strength, hardness and corrosion/oxidation resistance compared to traditional alloys.
- Metal nanoparticles: Metal nanoparticles exhibit unique optical, electronic and magnetic properties due to quantum effects. They have a wide range of applications in the sintering of nanostructured metals, alloying elements, catalysts, sensors and actuators. Common metal nanoparticles include gold, silver, iron oxide and titanium dioxide.
- Ceramics: Nanophase/nanostructured ceramics composed of nanoscale particles have significantly enhanced mechanical properties such as hardness and toughness, as well as improved electrical, optical, magnetic and thermal properties compared to traditional ceramics. Examples include nanocrystalline aluminum oxide, zirconium oxide, titanium dioxide and silicon carbide.
- Polymers: Addition of nanoscale fillers such as nanoparticles, nanotubes/fibers can reinforce polymers and produce nanocomposites with excellent strength, flame retardancy, wear/scratch resistance, and barrier properties. Nanoscale surface engineering of polymers imparts functional coatings such as antimicrobial, self-cleaning, and antifouling.
- Composites: Reinforcement of composite systems with nanoparticles, nanotubes, and nanofibers can significantly improve strength, stiffness, fracture toughness, fatigue resistance, and creep resistance compared to conventional composites.
- Smart Materials: Nanoscale smart materials can be designed to exhibit controllable properties when exposed to external stimuli such as pressure, temperature, humidity, light, etc. Shape memory alloys, self-healing polymers, and color systems are examples. This allows the creation of structures/devices that are responsive to the environment.
- Biomaterials: Nanoscale engineering of biomaterial surfaces can modulate biological interactions, allowing for better integration with cellular systems and improving the performance of medical implants, prosthetics, diagnostic devices, etc.
2) Industrial processes of nano machining
- Nanometrology: Involves precision measurement, characterization, and quality control at the nanoscale. Advanced microscopy techniques such as scanning electron microscopy, atomic force microscopy, and scanning tunneling microscopy make it possible to visualize and manipulate nanostructures. Spectroscopic techniques such as Raman spectroscopy can characterize materials based on molecular features. These techniques are fundamental to research, manufacturing, and quality control.
- Surface Engineering: Nanoscale surface engineering techniques impart functional coatings and treatments to improve material performance and properties, such as wear/corrosion resistance, biocompatibility, electrical properties, sensing capabilities, etc. This includes physical/chemical vapor deposition, micro-arc oxidation, sol-gel processing, electrophoretic deposition, etc.
- Nanolithography: It refers to the manufacturing technology that creates nanoscale structures and devices. Lithography uses light to form nanostructure patterns on a substrate. Nanoimprinting uses molds to imprint nanofeatures on materials. This has promoted the development of nanoelectronics, sensors, microfluidics, etc.
- Nanomanipulation: The technology of using probes to directly manipulate, locate, analyze, assemble, and modify nanoscale materials, molecules, and structures. Scanning probe microscopes are commonly used microscopes.
- Chemical synthesis: These methods facilitate large-scale, high-volume manufacturing of nanoparticles, nanotubes, and nanowires with controlled size and composition through engineered reactions at the molecular scale. Some of the methods used include sol-gel processing, electrochemical deposition, hydrothermal/solvothermal synthesis, chemical vapor deposition, etc.
- Self-assembly: It involves the spontaneous organization of nanoscale components such as molecules, nanoparticles, and nanotubes into structured, functionalized systems without external forces. This bottom-up approach mimics nature and expands the capabilities beyond top-down nanomanufacturing.
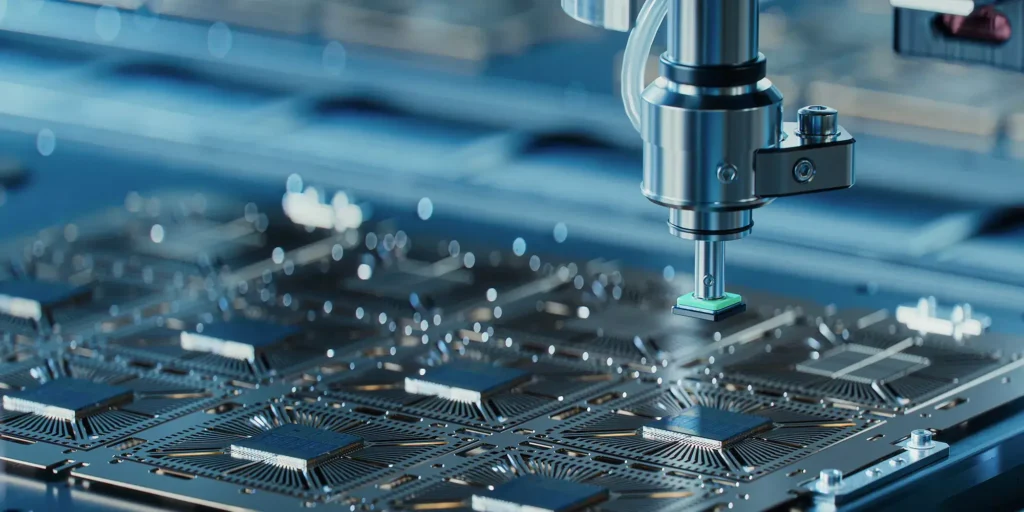
3.Key applications of nano machining technology in manufacturing
Nano machining technology is changing products in the following manufacturing sectors:
1) Automotive manufacturing
- Lightweighting: Metal alloys and composites reinforced with nanoparticles/nanotubes help reduce vehicle weight and improve fuel efficiency.
- Coatings: Nano coatings greatly improve the surface hardness, wear resistance, and corrosion resistance of engine components and body panels.
- Catalysts: Nanoparticle-based catalysts improve combustion efficiency and reduce exhaust emissions.
- Sensors: Nano sensors help in precise monitoring of vehicle control and safety systems.
- Batteries: Nanomaterials make electric vehicle batteries more durable and higher capacity.
2) Aerospace Manufacturing
- Composites: Nanoparticle-reinforced composites provide aircraft structures with superior strength, stiffness, and damage tolerance.
- Coatings: Nanocoatings make fuselages and wings resistant to erosion, corrosion, and lightning strikes.
- Sensors: Extensive networks of nanosensors for real-time performance monitoring and control.
- Fuels: Nanocatalysts enable fuller, more efficient combustion, resulting in reduced emissions.
3) Electronics Manufacturing
- Nanoelectronics: Nanomaterials enable further miniaturization and integration of electronic components. Carbon nanotube interconnects, graphene, and quantum dot-based structures are under development.
- Displays: Carbon nanotubes enable flexible displays. Quantum dots improve color clarity in LED displays.
- Sensors: Nanosensors offer significantly improved sensitivity, response time, and portability over micrometer-scale sensors.
- Batteries: Nanomaterials such as silicon nanowires are used to produce durable, high-capacity batteries for portable devices and electric vehicles.
4) Textiles
- Fabrics: Nanofiber reinforcements produce extremely lightweight, tough, breathable, and wrinkle-free fabrics.
- Coatings: Nanocoatings give textiles anti-fouling, dust-proof, wrinkle-resistant, flame-retardant, and other functional properties while remaining breathable.
- Waterproofing: Nanoscale fibers/coatings tightly repel water droplets.
- Sensing: Nanoparticles and nanofibers coated with sensing molecules are used in smart textiles.
5) Medical Manufacturing
- Implants: Nanoscale surface engineering of implants such as knee or hip implants allows for better integration with surrounding tissues.
- Prostheses: Lightweight nanoengineered prostheses mimic natural body tissues with superior mechanical properties and biointegration capabilities.
- Devices: Nanosensors enable rapid diagnostics. Nanoparticles help enable targeted drug delivery.
- Wound Dressings: Nanosilver coatings have antimicrobial properties. Nanopatterned surfaces stimulate cell growth and speed healing.
- Tissue Engineering: Nanoscale scaffolds guide cell proliferation and differentiation to regenerate damaged tissues or organs.
6) Sustainable Manufacturing
- Energy efficiency: Nanomaterials such as aerogels for thermal insulation, nano solar cells and thermoelectric devices reduce energy consumption.
- Renewable energy: Nanomaterials improve the efficiency of solar cells, fuel cells, hydrogen storage and batteries used for renewable energy generation.
- Waste reduction: Nanoparticles act as catalysts and nanofiltration allows for efficient recycling. Nanocomposites reduce the amount of materials used.
- Pollution reduction: Nanocatalysts selectively convert pollutants into less toxic forms. Nanofibers are used to filter ultrafine particles.
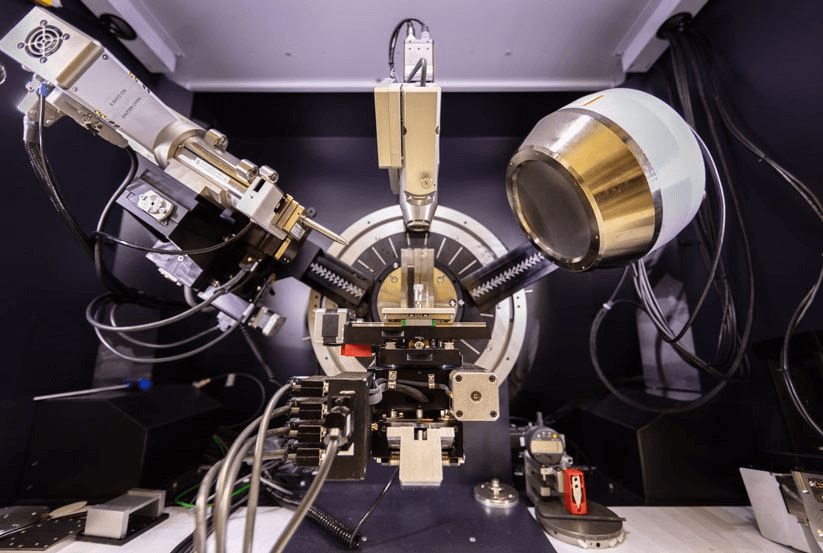
4.Advantages of nano machining technology in manufacturing
Major nanomaterials are widely used in the following manufacturing applications:
- Improved material properties: Nanomaterials make it possible to develop stronger, lighter and more versatile materials. For example, carbon nanotubes have a tensile strength 100 times that of steel but weigh only 1/6 of that. Nanocomposites mixed with nanoclay, nanocellulose or graphene have excellent strength and flame retardancy.
- Product miniaturization: Nanoelectronics encompass smaller and smaller electronic devices and components, allowing for extremely compact products.
- Higher precision: Nanomanufacturing processes can produce items with nanometer precision. This allows for precise reproducibility and fewer defects.
- Enhanced product functionality: Coatings, sensors, and devices added at the nanoscale can enhance performance and add new functionality.
- Better catalysis: The larger surface area of ​​nanoparticles can increase their catalytic activity. Nanoengineered catalysts can be used to make fuel production and chemical processes more efficient.
- Energy savings: Nanomaterials help reduce energy consumption in various processes by enhancing heat transfer, light absorption, and more. Better insulation materials, fuel additives, batteries, and electronics developed using nanomachining techniques can also save energy.
- Reduced waste: Nanofabrication techniques minimize material waste. Lighter nanoengineered products can further reduce raw material use and energy requirements during transportation.
- Enhanced safety: Nanosensors can detect defects, cracks, or faults before they are visible to the naked eye. This can help prevent catastrophic system failures.
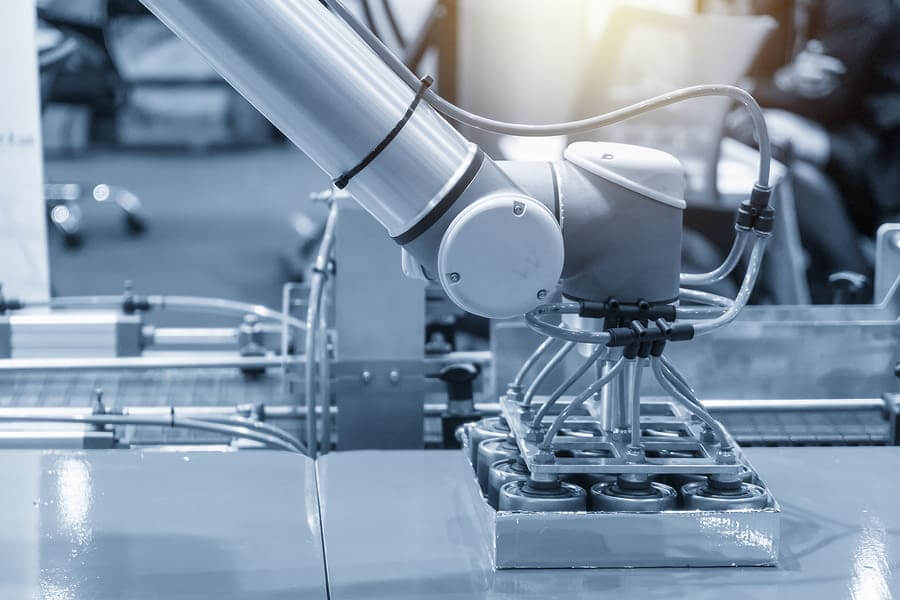
5.Challenges of nano machining in manufacturing
While nano machining has great transformative potential, there are some challenges to its large-scale adoption in manufacturing:
- The cost of nanoengineered materials and commercial-scale nanofabrication techniques is high compared to traditional methods.
- Difficulty in achieving uniform dispersion of nanomaterials like carbon nanotubes in composite matrix. This affects strength and quality.
- Scalability issues arise in translating lab-developed nanoscale processes to industrial-scale manufacturing.
- Environmental issues: Wastewater generated by manufacturing poses a threat to the environment due to the inherent toxicity of synthetic (organic and inorganic) chemicals.
- Integration challenges in incorporating nanomaterials into existing manufacturing workflows and quality control protocols.
- Ambiguity in intellectual property and licensing issues for startups and research groups to commercialize lab-scale nano innovations.
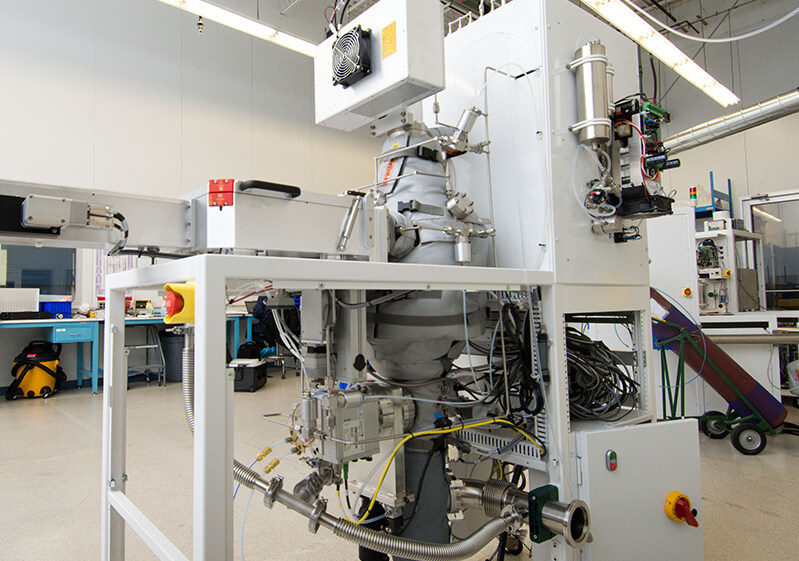
6.The future of nano machining
Some promising research directions that can leverage the capabilities of nano machining technology to improve manufacturing outcomes include:
- R&D and commercialization of nanomaterials like graphene, nanocomposites, and carbon nanotubes that can transform the properties of finished products across industries. Initiatives like Nano Mission are an example.
- Adoption of nanofabrication techniques like dip pen lithography and nanoimprinting can enable low-cost, scalable nanocomposite manufacturing. Establishment of dedicated nanofabrication centers.
- Provision of nanosensors and automation solutions for smart, real-time process control on factory floors. Encourage adoption under smart advanced manufacturing and Industry 4.0 initiatives.
- Develop a skilled workforce through nanoscience and nanoengineering training programs to implement nanomachining-driven innovations in the manufacturing industry.
- Responsible development of engineered nanomaterials through toxicology studies, safety guidelines, and environmental regulations. Life cycle analysis of nanomaterials under the Nano Mission.
- Public-private partnerships, including with MSMEs, to enable the benefits of nanomachining technologies to be adopted by a wider range of industries. Programs to support MSMEs.
- International collaborations, technology transfer, and sharing of best practices to accelerate the development of nanomanufacturing.
- Support technology startups and entrepreneurs working on developing nanomachining technology products and solutions for manufacturing through incubator programs.
Continuous research into the synthesis, properties, and safety of nanomaterials is key to the widespread adoption of nano machining technologies. Responsible and sustainable development can significantly advance manufacturing technologies and usher in a new era of materials innovation.