The Importance of Quality Assurance in Ultra Precision Machining
In the world of manufacturing, precision is critical. This is especially true for industries like aerospace, medical and electronics that rely on ultra-precision machining to create precise and complex components, with tolerances measured in microns. Achieving such precision requires not only state-of-the-art machinery and skilled operators, but also a robust quality assurance process.
Quality assurance plays a key role in ultra precision machining
Quality assurance plays a crucial role in ultra precision machining, ensuring that every component produced meets the highest standards of accuracy and reliability. By implementing a comprehensive quality assurance program, manufacturers can minimize errors, reduce waste, and deliver products that exceed customer expectations.
One of the primary reasons quality assurance is so important in ultra precision machining is the high level of precision required. With tolerances often measured in microns, even the slightest deviation can result in a faulty component. By implementing rigorous quality control measures, manufacturers can catch and correct any deviations before they become a problem.
Another reason quality assurance is crucial in ultra precision machining is the complexity of the components being produced. These components often have intricate geometries and require multiple machining operations to achieve the desired shape and dimensions. Each operation introduces the potential for errors, making it essential to have a robust quality assurance process in place to ensure that each step is executed correctly.
Furthermore, quality assurance helps manufacturers identify and address any issues with the machining process itself. By closely monitoring the machining parameters, such as cutting speed, feed rate, and tool wear, manufacturers can identify any deviations that may affect the quality of the finished component. This proactive approach allows for adjustments to be made before any faulty components are produced, saving time and resources.
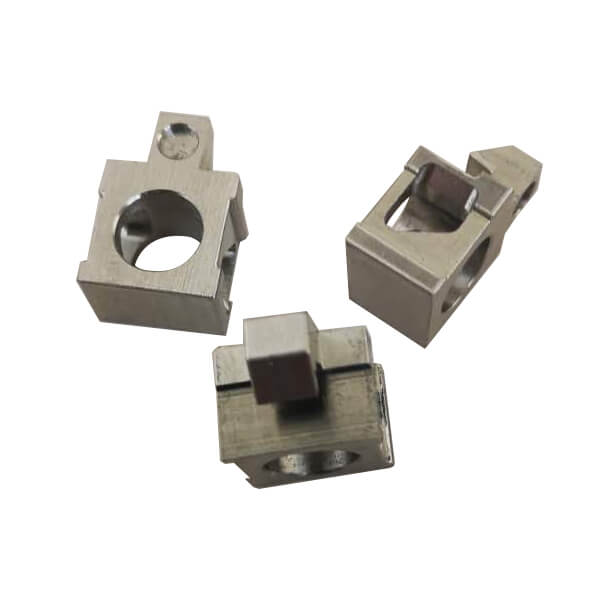
In addition to preventing errors, quality assurance also plays a vital role in continuous improvement. By analyzing data collected during the quality assurance process, manufacturers can identify trends and patterns that may indicate areas for improvement. This data-driven approach allows for the optimization of machining processes, resulting in increased efficiency and higher quality components.
Implementing a comprehensive quality assurance program in ultra precision machining requires a combination of advanced technology and skilled personnel. State-of-the-art metrology equipment, such as coordinate measuring machines and optical profilometers, is used to measure and verify the dimensions and surface finish of the components. Skilled operators, trained in the use of these tools, are responsible for interpreting the data and making any necessary adjustments to the machining process.
To ensure the effectiveness of the quality assurance program, manufacturers must also establish clear quality standards and procedures. These standards should be communicated to all personnel involved in the machining process, ensuring that everyone understands the expectations and requirements. Regular training and performance evaluations can help maintain a high level of quality and consistency.
In conclusion, quality assurance plays a crucial role in ultra precision machining. By implementing a comprehensive quality assurance program, manufacturers can ensure that every component produced meets the highest standards of accuracy and reliability. From preventing errors to driving continuous improvement, quality assurance is essential for achieving excellence in ultra precision machining.