Automobile chassis parts: the key to ensuring driving safety and stability
As an important part of the car, automobile chassis parts bear the weight of the vehicle and ensure its smooth driving. Chassis parts are complex and diverse, and each part plays an irreplaceable role. This article will explore in depth the importance, types, functions of each part, manufacturing methods and technologies, and design requirements and challenges of chassis parts.
1.The importance of chassis parts to cars
Chassis parts play a vital role in cars. They directly affect the performance, safety and comfort of the vehicle. The following are several aspects of the importance of chassis parts:
(1) Handling performance:
Chassis parts such as suspension systems and steering systems are directly related to the handling performance of the vehicle. Precision chassis parts can provide more accurate steering and more stable driving, allowing drivers to better control the vehicle, especially at high speeds or in complex road conditions.
(2) Ride comfort:
Chassis tuning and parts precision have an important impact on ride comfort. For example, the design of the suspension system can absorb road vibrations, reduce bumps, and improve ride comfort.
(3) Safety:
The safety design of chassis parts is crucial to protecting the occupants. For example, the precision parts of the braking system ensure that the vehicle can stop quickly and stably in an emergency, while the stability of the steering system helps to prevent the vehicle from losing control.
(4) Stability:
The design and manufacturing accuracy of chassis parts have a direct impact on the stability of the vehicle. For example, the precision adjustment of the suspension system and stabilizer bar can reduce the roll of the vehicle when turning and improve driving stability.
(5) Durability:
Chassis parts generally have higher durability and can maintain long-term stable performance under various road conditions and environments, reduce the failure rate, and extend the service life of the vehicle.
(6) Driving experience:
The precision of chassis parts directly affects the driving experience. A good chassis design can provide smooth acceleration, sensitive braking response and precise steering, making driving more pleasant and safe.
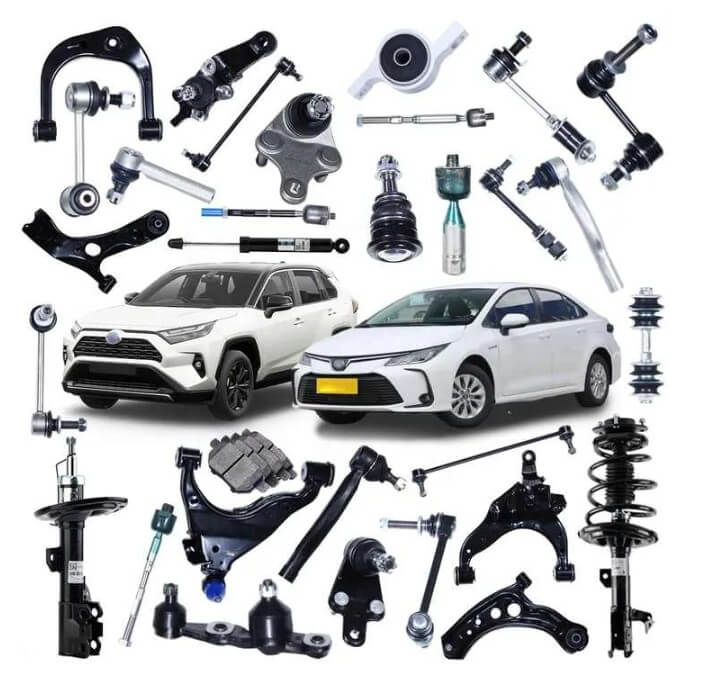
2.Types and functions of chassis parts
Chassis parts are key components of the vehicle chassis system. They each have different functions and work together to ensure the smooth operation and good handling of the vehicle. The following are some of the main chassis parts and their functions:
(1) Transmission system parts:
1) Clutch: responsible for the switching and combination of power in the transmission system, ensuring smooth start and gear shifting of the car, and preventing overload of the transmission system.
2) Transmission: interrupts the power transmission of the transmission system, changes the transmission ratio, and realizes neutral and reverse driving.
3) Universal transmission device: transmits power between rotating shafts whose relative positions often change.
4) Main reducer: changes the direction of power transmission and provides a common transmission ratio for each gear.
5) Differential: adjusts the speed difference between the left and right tires.
6) Axle: connects the differential and the drive wheel and transmits torque.
(2) Driving system parts:
1) Frame: supports and connects the various assemblies of the car, ensures that each assembly is in the correct relative position, and bears various loads inside and outside the car.
2) Axle: carries various loads of the car and maintains the normal driving of the car.
3) Wheel: supports the entire weight of the car, reduces and absorbs vibration and impact when the car is driving.
4) Suspension: transmits the torque between the wheels and the frame, including elastic elements, shock absorbers, etc., to buffer the impact of the road and ensure smooth driving.
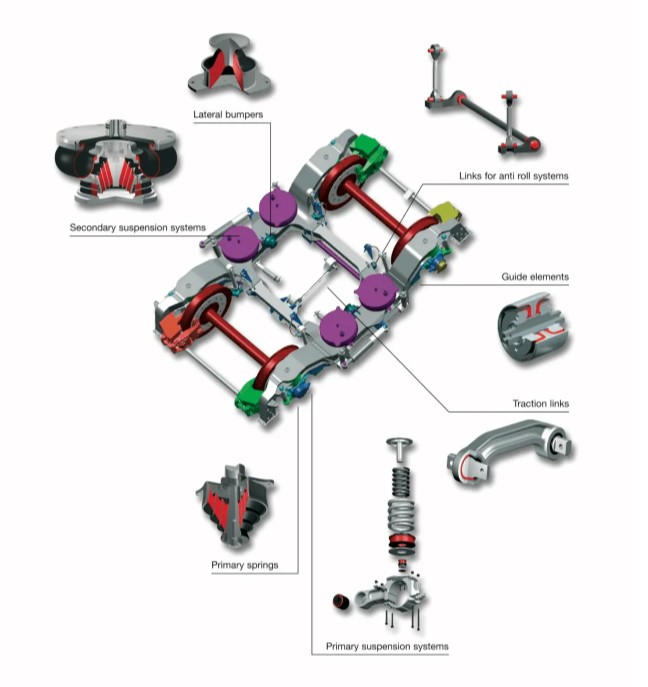
(3) Steering system parts:
1) Steering wheel: converts the driver’s steering intention into torque to control the direction of the car.
2) Steering shaft and steering column: transmit the torque transmitted by the steering wheel to improve the safety performance of the car.
(4) Braking system parts:
1) Brake disc and brake pad: generate braking force through friction to reduce the speed or stop the car.
2) Master brake cylinder and brake cylinder: control the braking system and assist braking.
3) Brake pedal: operate the service brake to control the deceleration and parking of the car.
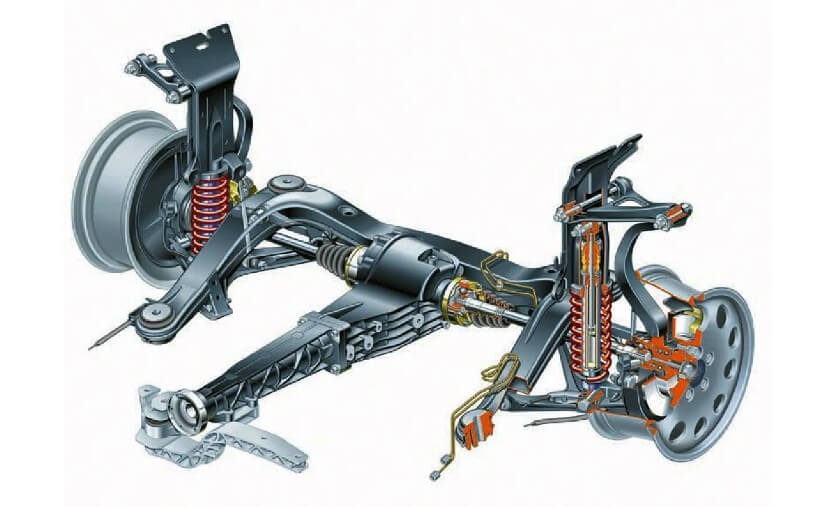
3.Manufacturing technology of precision chassis parts
The manufacturing of precision chassis parts involves multiple steps and technologies, including material selection, manufacturing process and precision machining.
(1) Material selection
Chassis parts usually need to have high strength, wear resistance and corrosion resistance. Commonly used materials include high-strength steel and aluminum alloy. Aluminum alloys are widely used in modern automobile manufacturing due to their lightweight properties to reduce vehicle weight and improve fuel efficiency. For example, aluminum alloy suspension systems are not only lightweight, but also provide better handling and comfort. High-strength steel is widely used in transmission systems and brake systems due to its high strength and durability to withstand high stress and high wear.
(2) Manufacturing process
The manufacturing process of chassis parts has a significant impact on their performance. Common manufacturing methods include forging, casting and hydroforming. Forging can improve the mechanical properties of materials and make parts more durable; casting is suitable for making parts with complex shapes; hydroforming can produce light and complex parts without reducing material strength.
For example, forged suspension system parts have higher strength and durability and can withstand high stress and high wear; cast transmission system parts can achieve complex shapes and structures, improve transmission efficiency and reliability; hydroformed steering system parts can produce light and complex parts without reducing material strength, improving steering accuracy and reliability.
(3) Precision machining
CNC machine tools and CNC machining technology play an important role in the manufacturing of chassis parts. These technologies can ensure high precision and high consistency of parts and meet strict design requirements. For example, CNC machine tools can accurately process complex suspension system parts to ensure their dimensional accuracy and surface quality; CNC machining technology can efficiently process high-precision steering system parts to ensure their steering accuracy and reliability. The following are the detailed steps and important parameters of CNC machining technology for chassis parts:
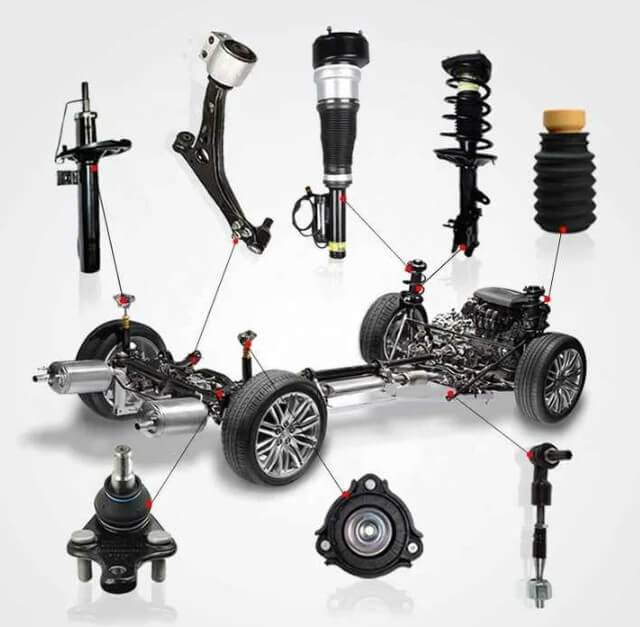
1) Part and blank analysis:
Chassis parts have complex shapes, including planes, contours, grooves, bosses and drillings. Aluminum materials are selected, and the blank size is 115mm×95mm×30mm, with a 3~4mm margin reserved.
2) Processing process division:
It is divided into two stages: rough machining and fine machining. First mill the clamping surface, and then use the clamping surface as the reference to process the part. Follow the principle of reference surface first, primary first and secondary second, rough first and fine second, and surface first and hole second.
3) Machine tool and tool selection
KVC650B machining center is selected, with a spindle speed of 60~6000r/min and a rapid moving speed of 10000mm/min. The tools are selected as end mills and keyway milling cutters with good rigidity and high durability.
4) Fixture selection and positioning:
Use flat vise clamping, with the bottom surface and two side surfaces as positioning reference. Ensure that the clamping mechanism does not affect the processing part, easy loading and unloading, and minimal clamping deformation.
5) Determination of processing parameters:
According to the accuracy requirements of the parts, determine the process parameters such as back cutting amount, spindle speed, and feed speed. Ensure processing quality and efficiency.
6) Tool path planning:
The tool path of the outer contour, plane, groove and other parts needs to be carefully designed to ensure processing accuracy and surface quality.
7) Processing result analysis:
Analyze the processing results, adjust the process parameters in time, and ensure that the parts meet the requirements of the drawings.
4.Design requirements and challenges of chassis parts
The design of chassis parts needs to meet a variety of standards and requirements, and faces a series of challenges.
(1) Design standards and safety requirements
The design of chassis parts must meet strict safety standards and performance requirements. For example, parts of the braking system need to be able to work reliably under high speed and heavy load conditions to ensure driving safety. Design standards include not only dimensional accuracy and surface quality, but also aspects such as material properties, structural strength and durability. High-performance design can not only provide an excellent driving experience, but also ensure the safety and reliability of the vehicle.
(2) Wear resistance
Chassis parts such as suspension system and transmission system components need to have good wear resistance to cope with complex road conditions and long-term operation. For example, the control arm and ball head of the suspension system need to withstand high stress and high wear, so it is necessary to select high-wear-resistant materials and improve their wear resistance through surface treatment technology. The gears and bearings of the transmission system also need to have high wear resistance to extend their service life and improve transmission efficiency.
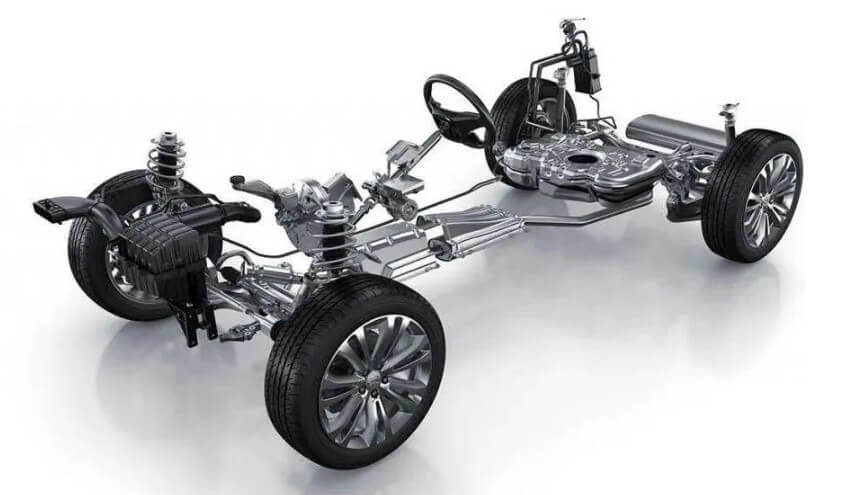
(3) Corrosion resistance
Since chassis parts are exposed to various harsh environments such as rain, mud and salt for a long time, corrosion resistance is an important factor in design. The use of corrosion-resistant materials and surface treatment technologies can effectively extend the service life of parts. For example, stainless steel or aluminum alloy materials can be used, and surface treatment technologies such as nickel plating and zinc plating can be used to improve the corrosion resistance of chassis parts. Anti-corrosion design can not only extend the service life of parts, but also improve the overall reliability and safety of the vehicle.
(4) Strength and durability
Chassis parts need to bear the weight of the vehicle and various dynamic loads during operation. Therefore, sufficient strength and durability must be ensured during design. For example, the brake discs and brake pads of the braking system need to withstand the impact of high temperature and high pressure, so high-strength materials need to be selected and their strength and durability need to be improved through heat treatment technology. The drive shaft and differential of the transmission system also need to have high strength and durability to withstand the impact of high torque and high stress. Strength and durability design can not only extend the service life of parts, but also improve the overall performance and safety of the vehicle.
5.Summary
In summary, the chassis parts of automobiles have their own functions and work together to ensure the stability and safety of the vehicle. Whether it is the transmission system, drive system, steering system or braking system, each part is crucial. Understanding the manufacturing, functions and characteristics of these chassis parts will help us better manufacture and use cars and extend the service life of vehicles.