A Comprehensive Guide to Automotive Parts Manufacturing
In recent years, the automotive parts manufacturing industry has shown a rapid development trend, which is mainly due to the continuous increase in market demand for automotive parts, components and spare parts. With the rapid development of automotive technology, consumers have increasingly stringent requirements for automotive quality and performance, which in turn has driven the growth of demand for automotive parts manufacturing.
This guide aims to deeply analyze the field of automotive parts manufacturing and take you to a detailed understanding of the entire production process, including how parts are designed, manufactured, tested and finally applied to automobiles.
1.Common technologies for automobile parts manufacturing
(I) CNC machining
CNC machining is commonly used in the customized production of automobile parts. It uses pre-programmed instructions to control high-speed rotating cutting tools to gradually remove blank materials until a customized part that meets the requirements is formed. CNC machining technology is often used to manufacture high-precision, complex-shaped parts such as engine cylinder heads, crankshafts, and gears.
(II) 3D printing
3D printing is an innovative automobile parts manufacturing technology that quickly prints free-form and complex plastic or metal parts based on three-dimensional digital models. In the field of automobile parts manufacturing, 3D printing technology is widely used in rapid prototyping, direct manufacturing of complex structural parts, and production of personalized customized parts.
(III) Sheet metal processing
Sheet metal parts are widely used in automobile body covering. Sheet metal processing usually uses laser or plasma technology to cut the flat contour of the part first, and then bend it into the desired shape. Sheet metal processing is often used to manufacture parts such as doors, roofs, and floors.
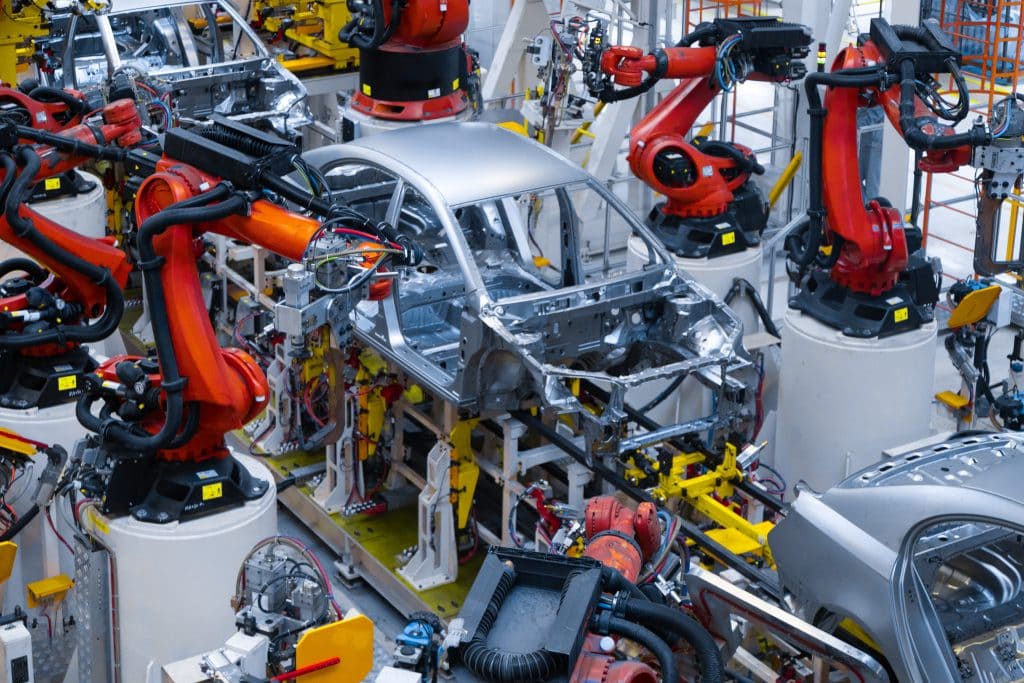
(IV) Injection molding process
Injection molding process is mainly used to manufacture plastic parts in automobile parts manufacturing. The desired parts are obtained by injecting molten plastic material into a pre-designed mold and cooling and solidifying it. The injection molding process has the advantages of high production efficiency, low cost, and the ability to manufacture parts with complex shapes.
(V) Casting
Casting technology is to pour molten metal liquid into the mold cavity, wait for it to solidify and cool, and obtain parts of the desired shape and size. Casting technology occupies an important position in the manufacture of automotive parts. About 10% of the weight of the entire vehicle is obtained by casting.
2.Materials used in the manufacture of automobile parts
(I) Steel
Steel is one of the most commonly used raw materials in the manufacture of modern automobile parts. In the manufacture of automobile parts, different types of steel are used for different parts because they can provide good strength and impact absorption for the parts. For example, steel is widely used in parts such as door panels and support beams. In addition, according to the stiffness requirements, steel is also used in the manufacture of parts such as car roofs and exhaust pipes.
(II) Plastic
Plastic, as an important raw material for the manufacture of automobile parts, is obtained through petrochemical processing. Studies have shown that plastic accounts for 8% – 10% of the weight of each car. Due to its good durability, it is widely used in air-conditioning vents, floors, switches, handles, and many parts inside the engine. With its strong load-bearing capacity and wide applicability, plastic can replace steel in some scenarios and occupies an important position in the manufacture of automobile parts.
(III) Rubber
Rubber is an indispensable key material for the manufacture of automobile parts. About 65% of rubber production is used in the manufacture of automobile parts, and its main uses include the manufacture of various types of transmission belts. Rubber is highly versatile and can be shaped into different shapes as needed. It plays a key role in improving the efficiency of automobile operation, heat resistance and road safety, and can maintain a stable shape during use.
(IV) Aluminum
Aluminum is a high-quality and durable material in the manufacture of automotive parts, and its use is on the rise. Auto parts manufacturers prefer aluminum because it combines rigidity, toughness and light weight. Currently, aluminum is widely used in the manufacture of engine parts, which helps to reduce fuel consumption and improve performance, while gradually replacing some hard metals in the manufacture of wheels and other parts.
(V) Glass
In the field of automotive parts manufacturing, glass plays a vital role, especially from the perspective of ensuring driving vision. Different types of glass are used in the form of lenses in cars to provide drivers with a clear view of the surroundings. Windshields can protect the driver’s safety in bad weather conditions. With the advancement of technology, rear lenses are also made of glass, which improves the clarity of the rear view. In addition, laminated glass is widely used in the manufacture of automotive parts to reduce injuries in traffic accidents.
(VI) Fiberglass
Because of its rust-resistant properties, fiberglass is often used to replace steel in the manufacture of automotive parts. It is woven from small strands of air and coated with a resin coating to obtain tensile strength and heat resistance. The main uses of glass fiber in the automotive industry include improving the fire resistance of automobiles manufacturing parts such as bumpers and wheels, and also having an insulating effect.
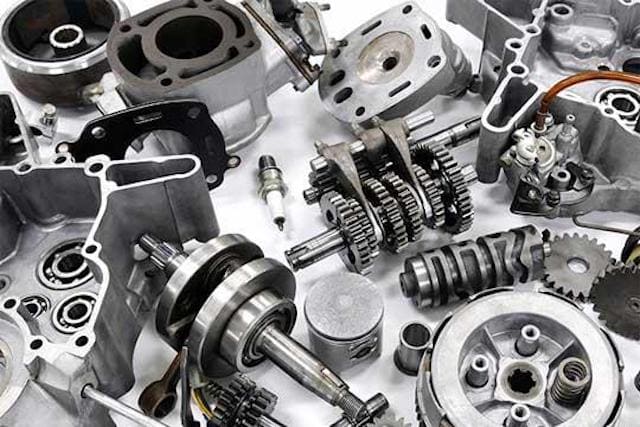
(VII) Lead
Lead is mainly used in the automotive industry to maintain stability and weight balance. Its most important use is in the manufacture of automotive batteries. Both traditional fuel vehicles and electric vehicles contain lead components because lead can effectively maintain the battery temperature within a safe range.
(VIII) Titanium
Titanium is used by some automotive parts manufacturers to manufacture specific parts, especially internal combustion engine parts, due to its corrosion resistance and low density. The use of titanium to manufacture parts can reduce fuel consumption, improve vehicle efficiency, and help reduce engine combustion noise. However, due to the high price of titanium, only a few manufacturers currently use it.
(IX) Magnesium
Magnesium is one of the raw materials widely used in the automotive parts manufacturing industry. Its outstanding advantage is its light weight. Therefore, magnesium is often used to manufacture weight-sensitive parts such as steering wheels and interior parts, which helps to improve vehicle handling performance. Using magnesium materials on the front end of the car can make the vehicle more flexible in turning.
(X) Copper
Although copper is not used in large quantities in the manufacture of automotive parts, it plays a key role in electrical connections. Copper has good thermal conductivity and is often used in radiators and electrical connections in cars, such as starters, radios, and other safety systems.
3.Types of Auto Parts
(I) Mechanical Parts
Engine Parts
As the core power component of a car, the engine is like the heart of the car, converting fuel into mechanical energy to provide power for the car to drive. Its key components include cylinder block, piston, turbocharger and fuel injector. The quality and performance of these components directly affect the efficiency and reliability of the engine, and are the focus of attention in the Automotive Parts Manufacturing.
Transmission Parts
The transmission system is responsible for transmitting the power generated by the engine to the wheels to ensure that the vehicle can travel at a suitable speed. The main transmission components are gearbox, clutch and transmission system. High-quality transmission components can ensure the smoothness and efficiency of power transmission.
Suspension and Steering Parts
The suspension and steering system are essential to ensure the smooth and comfortable driving of the vehicle and maintain the stability and handling of the vehicle. Struts, shock absorbers and tie rods are key components of the system. These components work together to enable the vehicle to cope with various road conditions during driving and provide the driver with a good driving experience.
(II) Electrical Parts
Battery and Charging System
The battery is the core of the automotive electrical system, providing power for engine starting and other electrical equipment operation. The alternator and starter motor are key components. The alternator is responsible for charging the battery, while the starter motor is used to start the engine. The performance and reliability of these components are directly related to the normal operation of the vehicle’s electrical system.
Ignition and starting system components
The ignition and starting system components are responsible for igniting the fuel-air mixture in the engine and maintaining combustion. The ignition coil converts the battery voltage to a higher voltage, and the spark plug ignites the fuel mixture.
Lighting and instrument components
The lighting and instrument components are critical for the driver to monitor vehicle performance and ensure visibility in various driving conditions. Headlights, taillights, and dashboard instruments are key components of this system. Good lighting and clear instrument displays can improve driving safety and comfort.
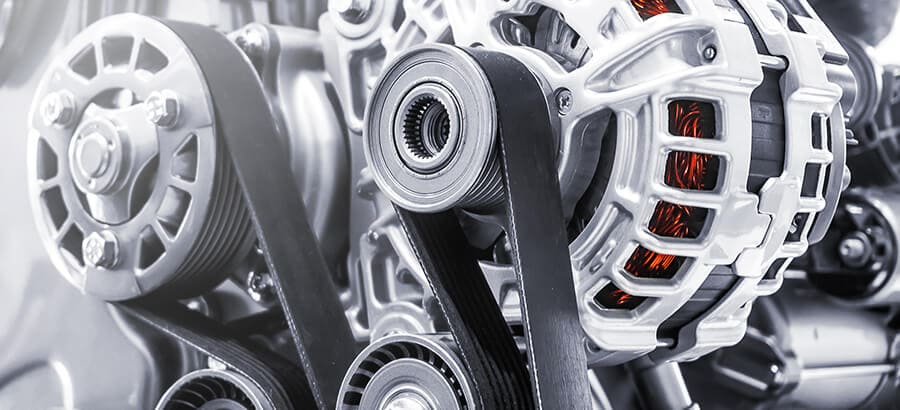
(III) Body and interior parts
External body parts
External body parts not only affect the appearance of the car, but also play an important role in its aerodynamic performance and structural integrity. The hood, fenders, doors, and bumpers are key external body parts.
Interior parts
Interior parts and accessories are important for improving the comfort, functionality, and safety of the vehicle cabin. High-quality interior components can provide passengers with a comfortable riding environment and convenient use experience.
(V) Other automotive parts
Turbocharger
Turbocharger is one of the most popular automotive parts in the current market. It improves engine performance and combustion by increasing the intake volume, thereby increasing output power.
Advanced Driver Assistance System (ADAS)
ADAS is a rapidly developing field in the automotive industry, covering technologies such as adaptive cruise control, lane departure warning system and automatic emergency braking.
Lithium-ion battery
With the rise of electric vehicles, lithium-ion batteries have become a key component of automobiles.
Automotive sensors
Sensors play a vital role in modern vehicles, and their applications range from engine management to safety systems.
4.Automotive Parts Manufacturing Process
(I) Design Phase
Automotive parts manufacturing begins with design, which involves determining requirements, CAD design, and design process planning. All parties work together to determine part requirements, design and test using CAD software. The design process includes concept development, verification, prototyping, test improvement, and final approval.
(II)Mold Casting
Covering pattern making (selecting materials according to parts and casting methods), mold formation (sand molds, permanent molds, ceramic shell molds for different parts), melting and pouring, cooling and solidification, casting and finishing.
(III)Prototype Design and Testing
Prototype Design: including 3D printing, CNC machining, manual model making; functional prototypes to evaluate performance and assembly; pre-production prototypes to test manufacturing processes.
Testing: performance testing (pressure, durability), environmental testing (temperature and humidity, corrosion), safety testing (collision, impact), regulatory compliance testing.
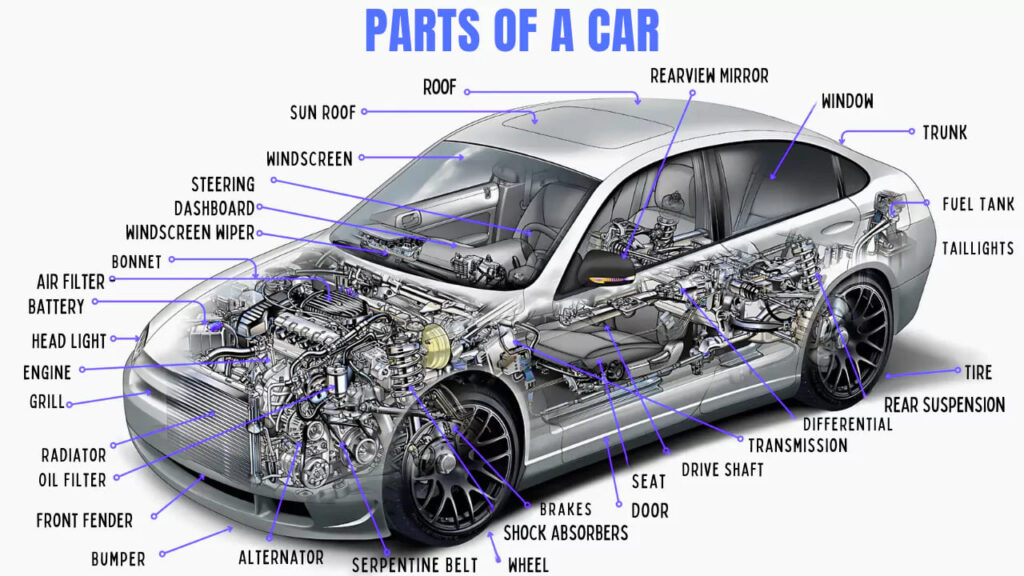
(V)Batch Manufacturing and Assembly
Stamping: blanking, forming, punching, and trimming.
Welding: spot welding, MIG and TIG welding, and robot welding are used in different situations.
Painting: preparation, electrostatic painting, curing, inspection.
Final assembly: component installation, electrical system integration, functional testing, final inspection.
(IV)Quality Control
Inspection and testing: in-process inspection, non-destructive testing, performance testing.
Statistical process control: data processing and problem correction.
Final quality assurance: vehicle testing and aesthetic inspection.
5.Surface treatment technology for automobile parts manufacturing
(I) Powder coating
When customizing the painting of automobile parts, powder coating is one of the most common customization methods. Most customers want their cars to have different colors, matte surfaces, cool patterns or specific pictures.
(II)Anodizing
Anodizing is often used to customize aluminum auto parts. Anodizing is a simple process to thicken the aluminum oxide layer by inserting the part into an electrolyte and placing it at the anode of the current, which causes ions to detach from the metal surface, forming deep microscopic pores on the surface, and thickening the oxide film around the pores. If the pores are filled with paint, a metallic luster effect can be achieved.
(III) Polishing
Polishing requires the use of abrasive paste and soft tools to obtain a perfect surface finish.
6.Conclusion
In summary, automotive parts manufacturing is a complex and diverse field, covering everything from advanced manufacturing technology to multiple material applications, from a rich variety of parts to rigorous manufacturing processes. Understanding these contents will help us gain a deeper understanding of the automotive parts manufacturing industry.
1 Comment