What are the Benefits of Aluminum CNC Machining?
Aluminum is widely used in the manufacturing industry due to its unique properties, such as light weight, corrosion resistance, and high ductility. In recent years, CNC machining has become a popular method for manufacturing aluminum parts due to its ability to produce complex shapes with high precision and accuracy.
In this blog post, we will discuss the benefits of aluminum CNC machining, including its advantages over other manufacturing processes and the different materials used for aluminum machining. We will also explore how aluminum CNC machining can benefit various industries and provide tips for choosing a CNC machining supplier that fits your needs.
1.What is aluminum CNC machining?
Aluminum CNC machining is the process of producing aluminum parts using CNC machines. CNC machines are computer-controlled machines that use rotating tools to remove material from a workpiece following a predetermined path or set of instructions. Aluminum CNC machining can produce parts with high precision and accuracy, making it a top choice for a variety of industries.
The aluminum CNC machining process begins with a CAD (computer-aided design) drawing of the part to be produced. The CNC machine then interprets the CAD drawing into a program it can understand, instructing the machine to cut and shape the aluminum. CNC machines cut aluminum according to programmed instructions, producing finished parts that meet the required specifications.
Aluminum CNC machining processes include CNC milling, CNC turning, and CNC drilling. CNC milling involves removing material from the surface of the aluminum using a rotating cutting tool, while CNC turning involves removing material from the center of the aluminum by rotating the aluminum relative to the cutting tool. CNC drilling involves drilling holes in the aluminum using a rotating drill.
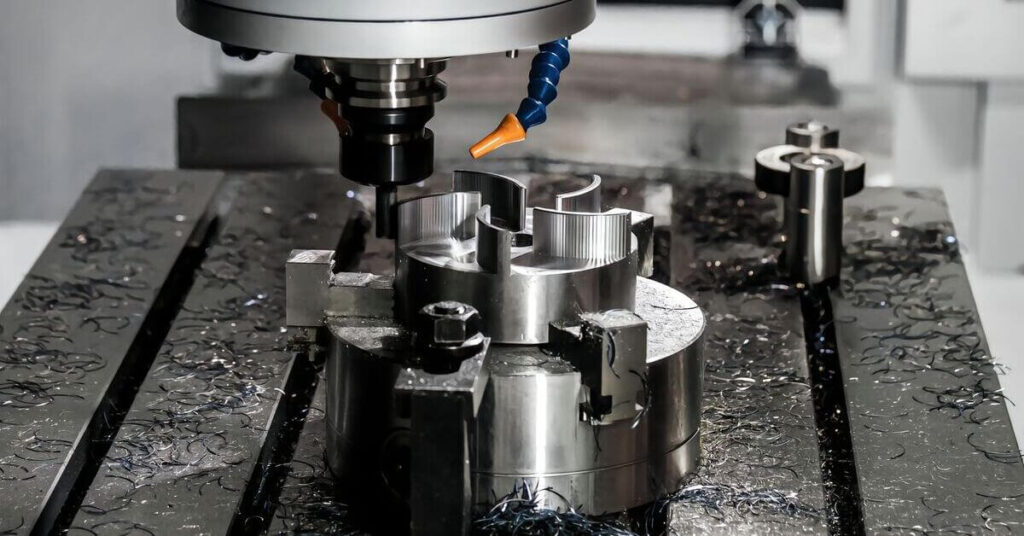
2.Materials used in aluminum CNC machining
Aluminum CNC machining can be performed using different types of aluminum alloys. These alloys have specific properties that make them suitable for different applications. Some commonly machined aluminum alloys include:
1) 6061 Aluminum
It is one of the most commonly used aluminum alloys in machining. It is known for its high strength, weldability, and corrosion resistance. Applications:
- Engine blocks
- Boat hulls
- Bicycle frames
- Window frames
- Electrical connectors
- Helicopter rotor skins
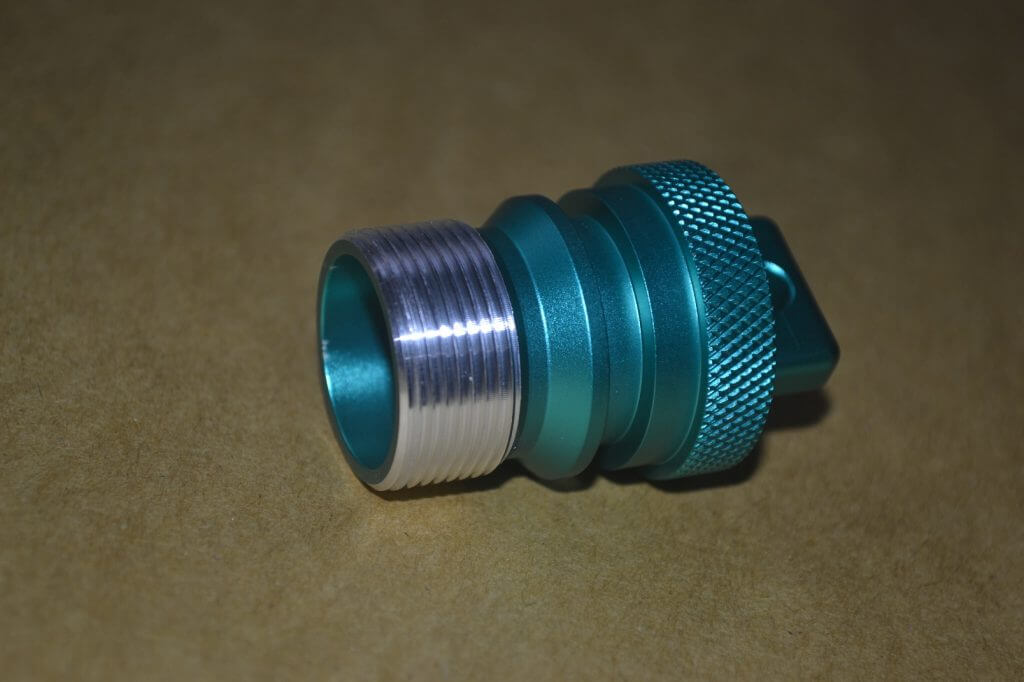
2) Aluminum 6063
6063 aluminum has a good strength-to-weight ratio, excellent corrosion resistance, and the ability to be easily formed and welded. Applications:
- Lighting Fixtures
- Bumpers
- Power Distribution Systems
- Boat Frames
- Aircraft
3) 7075 Aluminum
This alloy is known for its high strength-to-weight ratio and excellent fatigue resistance. It is commonly used in the aerospace, defense, and transportation industries.
- Fuselage Frames
- Military Aircraft Components
- Motorcycle Frames
- Camera Components
- Surgical Instruments
- Ship Hulls
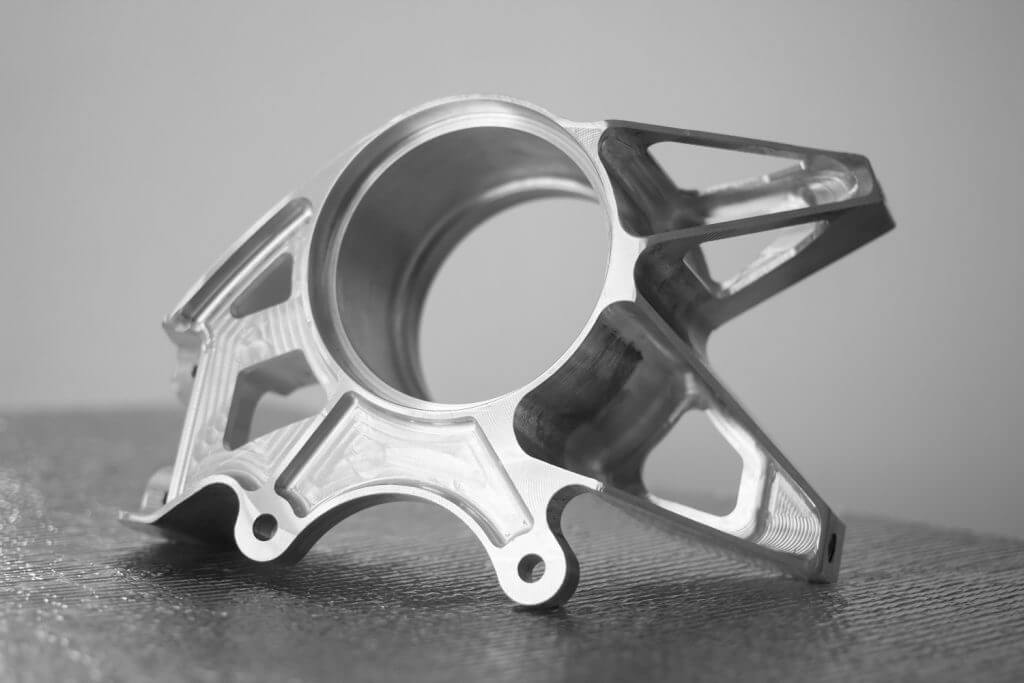
4) Aluminum 2024
2024 aluminum is a high-strength aluminum alloy with excellent fatigue resistance and machinability, commonly used in the aerospace and defense industries.
- Wing Skins
- Armored Vehicles
- Wheels
- Electronic Housings
5) Aluminum 5052
5052 aluminum is a non-heat-treatable aluminum alloy with good corrosion resistance and formability. Applications:
- Gasoline drums
- Deck
- Roof
- Shell
- Cookware
- Food and beverage cans
- Mechanical sheet metal
6) Aluminum 5083
5083 aluminum is a high-strength, non-heat-treatable alloy with excellent corrosion resistance and good weldability. Applications:
- Superstructures
- Oil rig components
- Bed liners and chassis
- Aircraft wings and fuselages
- Missile and bomb components
3.Advantages of aluminum CNC machining
Aluminum is one of the most popular materials for CNC machining projects because of its good physical properties. Its oxidized outer layer prevents it from corroding due to weather, and its strength makes it ideal for mechanical parts. Due to these advantages, aluminum parts are now widely used in all industries, but they are particularly prevalent in the automotive, aerospace, medical, and consumer electronics sectors.
1) Easy to bend
One of the benefits of using CNC machining to make aluminum CNC parts is that they can be easily bent. Unlike steel, aluminum can be easily turned during machining because the thickness of this material allows for the use of various forming methods appropriately. Various shapes of aluminum CNC parts can be easily achieved through pressing and machining.
2) Easy to Machinable
Another advantage of aluminum CNC machining processes is that the material can be easily manufactured through stamping, folding, and drilling. You can use it to form various shapes of parts as needed. The energy required for aluminum CNC machining is much lower compared to steel machining.
3) Low Temperature Resistance
Aluminum is resistant to low temperatures. We all know that steel is fragile, especially in welded parts or low temperature environments. Aluminum is easier to machine at low temperatures compared to steel.
4) Custom Finishing
Aluminum can be customized after machining to meet customer requirements. There are things you can do to give it a perfect custom look. Aluminum CNC parts can be plated in various colors according to your requirements. Some of the colors you can try include black, blue, and green.
5) Machinability
Aluminum is also known for its excellent machinability, which means it can be easily formed using various CNC machining processes such as milling, turning, and drilling. This makes it a popular choice for complex parts that require high precision and accuracy.
6) Cost-effective
Aluminum is an abundant and inexpensive material, making it an affordable choice for many applications. The light weight of aluminum also makes transportation and handling simpler and more cost-effective, thereby reducing overall manufacturing costs.
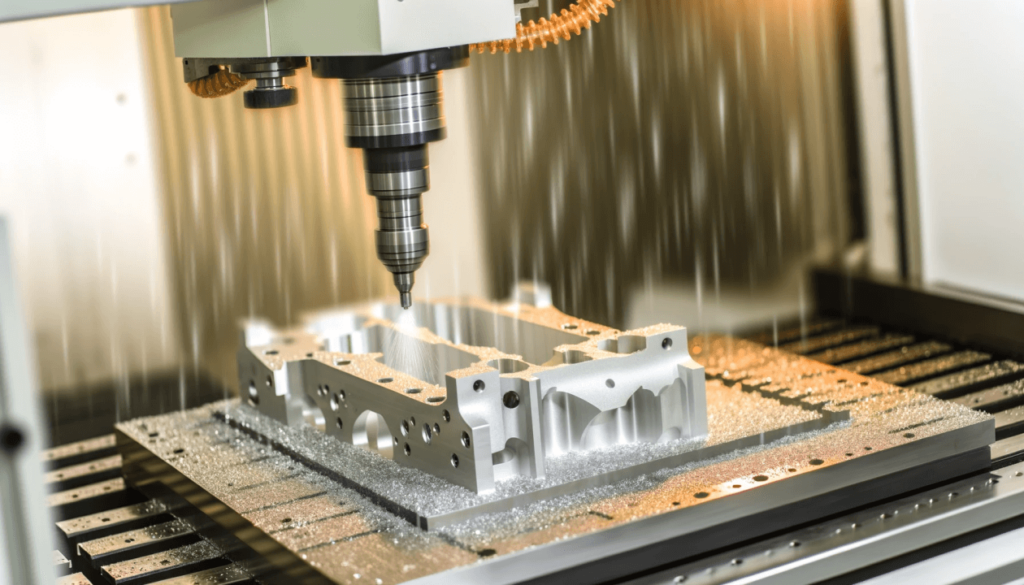
4.Other manufacturing processes combined with CNC machining
In the actual processing process, considering issues such as quantity, technology, and price, many times we will consider using other processes to obtain semi-finished products first, and then consider using CNC for precision machining. This can greatly save material costs and reduce costs.
Here are several commonly used methods for obtaining semi-finished products:
1) Extrusion + CNC machining
Extrusion is a manufacturing process that involves shaping aluminum into the desired cross-sectional profile. Typically, 6061 aluminum and 6063 aluminum are commonly used materials for extrusion.
2) Die casting + CNC machining
Die casting is a manufacturing process that involves injecting molten metal into a mold to produce complex shapes with high precision and consistency. This method is often used to produce large quantities of complex parts with strict tolerances. But the surface roughness of die castings is very rough, so the surface roughness can be improved by CNC machining.
3) Metal Manufacturing + CNC Machining
When using sheet metal processing, we usually use a CNC bending machine to bend the sheet metal into the desired shape, and then use a CNC machine for precision machining. CNC machines are usually used for cutting, drilling, punching, tapping and contouring sheet metal parts.
By combining these processes, we can significantly improve production efficiency and product accuracy while saving costs and reducing material waste.
4) Forging + CNC Machining
Forging is a manufacturing process in which a forging press or hammer is used to heat and shape the metal through compression force.
Common forging methods include cold forging, hot forging, and warm forging. After forging, CNC machines are generally used for precision machining. Common CNC machining includes milling, turning, drilling, tapping, etc.
5.Industries that benefit from aluminum alloy CNC machining
1) Aerospace
Because aluminum is light in weight and high in strength, it is very popular in the aerospace industry. Precision machining of aluminum parts is essential for producing aircraft components such as landing gear, engine components, and internal structures
2) Automotive
Aluminum CNC machining has a variety of applications in the automotive industry. One of the most important applications is the production of engine components such as cylinder heads, cylinder blocks, and pistons.
3) Electronics
Aluminum’s corrosion resistance and anodizing properties make it a popular choice for electronic components such as heat sinks, housing components, brackets, and housings.
4) Medical
CNC machining can produce precise and complex medical parts with tight tolerances, which is essential to ensure the safety and effectiveness of medical devices.
5) Agriculture
Aluminum parts are commonly used in agricultural machinery such as tractors, tillers, and harvesters.
6) Lighting
Aluminum CNC machining is often used to manufacture parts for LED lights, bulbs, lamps, and other lighting products.
6.Xavier’s capabilities in aluminum alloy CNC machining
Xavier is a professional CNC machining service provider with many years of experience in aluminum CNC machining. With advanced CNC machines and experienced operators, we can produce high-precision aluminum parts that meet customer requirements.
Whether you are ordering a prototype, a small batch, or a large-volume production of aluminum CNC machined parts, we have a flexible production system that can adapt to different production needs.
7.Conclusion
CNC machining has revolutionized the manufacturing industry by providing high precision and efficiency to produce complex parts. The benefits of CNC machining include increased productivity, improved accuracy, and the ability to process a wide range of materials.
However, choosing the right CNC machining shop is essential to ensure quality work and timely delivery. By considering factors such as experience, capabilities, certifications, and customer service, you can make an informed decision and have a successful CNC machining experience.
If you are undertaking a CNC machining project that requires high-quality, reliable, and efficient services, consider contacting Xavier. With our state-of-the-art equipment, experienced technicians, and commitment to quality control, we can provide the results you need for your project. Contact us today to learn more about our services and how we can help you achieve your goals.