Basic Introduction to Gear Manufacturing
Gears are an ancient and critical mechanical component that are widely used in modern industry. The quality of gear manufacturing directly affects the performance and service life of the gears. So, how are gears made? In this article, we will explore various aspects of gear manufacturing in depth.
1.Importance of gear manufacturing
Gear manufacturing is a diverse field, with a variety of processes used to manufacture gears for different types and applications. Gears play a key role in power transmission and often operate under harsh conditions, so it is vital to ensure that the gears are in perfect condition, reliable, with minimal residual stress and a very low risk of crack growth. This also makes gear manufacturing a specialised field with tight tolerances and little room for error.
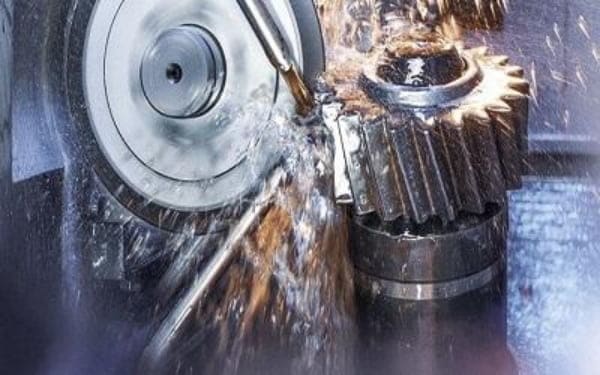
2.Types and applications of gears
Before we delve into the gear manufacturing process, it’s important to understand the types, applications, and benefits of gears. Factors such as application requirements and performance parameters can significantly influence gear selection, and from a manufacturing perspective, classifying gears based on tooth profile is a common approach.
1.Spur gears
Spur gears are widely used in power plants, aerospace components, industrial machines and other fields. It is simple to manufacture and can withstand high speeds and high loads, but it is noisy during operation and is not suitable for applications that require smooth operation. Spur gears can mesh with the same type or internal and external gears and are used in a variety of gear mechanisms. Their simplicity makes them easy to manufacture and maintain accuracy. Their low axial load makes them excellent in gear systems that focus on minimizing mechanical losses.
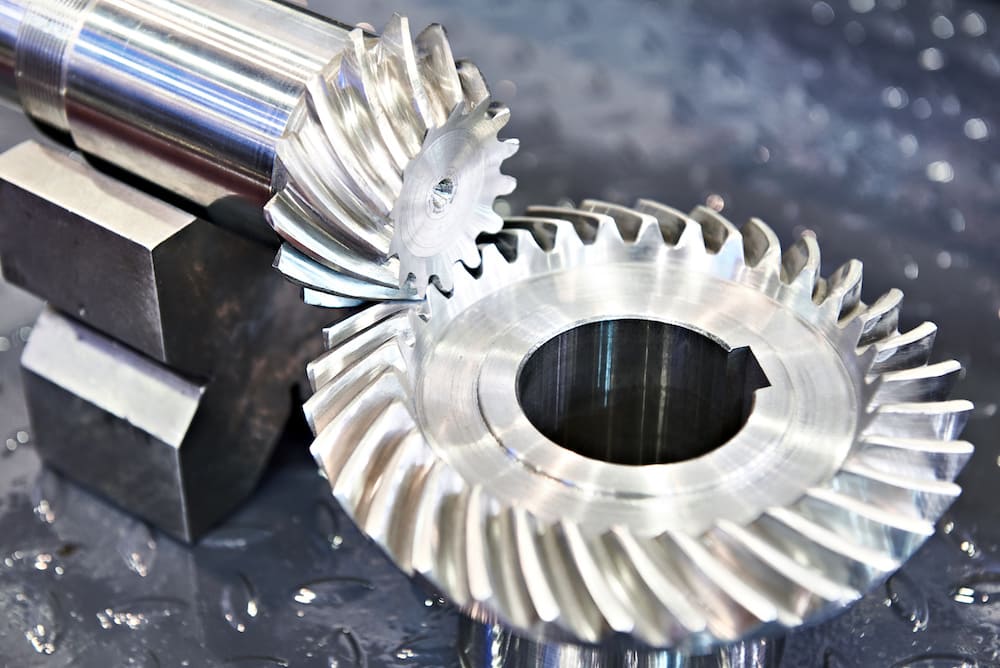
2.Helical gears
The teeth of helical gears rotate around a cylinder and can run smoothly with parallel and non-parallel axes, but are only compatible with other helical gears with the same helix angle. The helical teeth of helical gears can reduce the impact load, making the operation smoother and lower noise, but the efficiency is lower than that of spur gears, and the transmission mechanism has greater losses and requires thrust bearings. Helical gears are more challenging to manufacture than spur gears, with the helix angle more difficult to replicate accurately and the axial elements more expensive to fabricate and integrate, making them more suitable for specific applications.
3.Bevel gears
Bevel gears are located on a conical surface and can change the transmission direction between intersecting axes. Common types include spur bevel gears, spiral bevel gears, equal diameter bevel gears, crown gears and hypoid gears, which are widely used. in various fields.
4.Worm gear
Worm gear consists of worm gear and spiral gear, and is widely used in aerospace, industrial machinery, elevators and automobile steering systems. Although the worm gear device cannot provide high speed or efficiency, it has the unique property of a self-locking mechanism and has high friction during operation, and may require continuous friction to achieve optimal conditions.
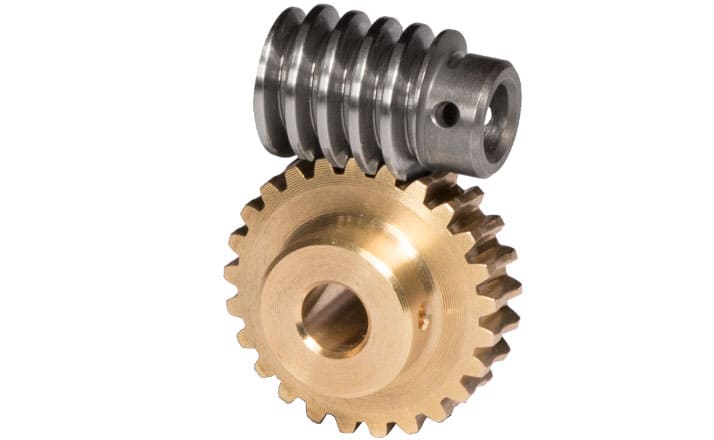
5.Rack and pinion
The rack and pinion system can convert rotational motion into linear motion or vice versa. The gear teeth can mesh with spur and helical teeth. It is widely used in automobile systems, weighing scales and other institutions.
3.Materials used in gear manufacturing
In gear manufacturing, the choice of material depends on factors such as gear type and usage scenario. Material selection is either affected by gear geometry or determined by gear performance. Common raw materials include copper alloys, iron alloys, aluminum alloys and thermoplastics, each of which has its optimal mechanical properties.
(I) Copper alloys
When gears need to withstand corrosive environments or non-magnetic requirements, copper alloys are often the best choice. Common copper alloys for gears are brass, phosphor bronze and aluminum bronze.
1.Brass: Brass is an alloy of copper and zinc. Different zinc contents change the ductility of the alloy. Low zinc content maintains high ductility and is often used in low-load environments, such as spur gears and racks in instrument drive systems. Its copper base makes processing easy and antibacterial.
2.Phosphor bronze: Phosphor bronze is an alloy of copper, tin and phosphorus. Tin improves strength and corrosion resistance, while phosphorus enhances wear resistance and stiffness. It is suitable for high-friction drive components, such as worm gears, and can resist friction and wear and lubricant performance degradation.
3.Aluminum bronze: Aluminum bronze contains copper, aluminum, iron, nickel, manganese and other elements. It is more wear-resistant and corrosion-resistant than phosphor bronze. It can resist oxidation, salt water and organic acid corrosion. It can be used for cross-axis helical gears, worm gears, etc., and can withstand greater loads.
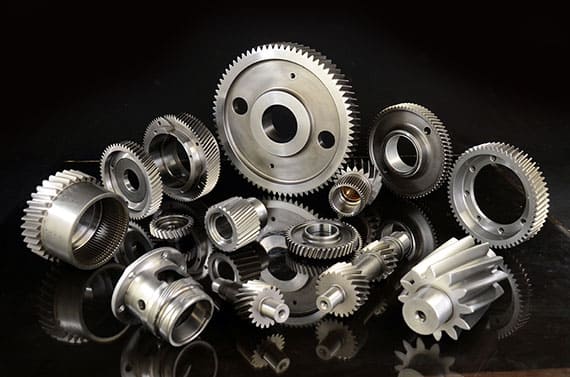
(II) Ferroalloys
When the gear design requires excellent material strength, ferroalloys are the best choice. Gray iron can be cast into gears. Steel is an alloy of iron, carbon and other trace elements. It mainly includes carbon steel, alloy steel, stainless steel and tool steel.
1.Carbon steel: Carbon steel alloys are used for a variety of gears. They are easy to process, wear-resistant, hardenable and relatively cheap. They can be divided into low carbon steel (carbon content less than 0.30%), medium carbon steel and high carbon steel (carbon content greater than 0.60%). They are ideal for spur gears, helical gears, etc. They can be induction hardened or laser hardened, and the hardness can reach HRc 55.
2.Alloy steel: such as AISI 4140 contains aluminum, chromium and other elements. It is stronger, easier to process and more corrosion-resistant than carbon steel. It can be used for spur gears, etc. It can also be carburized or surface hardened, and the hardness can reach HRc 63.
3.Stainless steel: Stainless steel alloys contain at least 11% chromium, and are divided into ferrite, austenite, martensite, precipitation hardening steel, etc. For example, 303 stainless steel contains sulfur and has good processability. 316 alloy has strong corrosion resistance and is used for spur gears, etc. 304 alloy is commonly used for racks.
(III) Aluminum alloy
Aluminum alloy can replace iron alloys in applications that require a high strength-to-weight ratio. Its weight is about one-third of that of steel alloys of the same size, and passivation treatment can prevent oxidation corrosion. Commonly used aluminum alloys are 2024, 6061 and 7075. 2024 aluminum alloy has high strength but low corrosion resistance. 7075 aluminum contains zinc and magnesium and is resistant to stress loads. 6061 aluminum is an alloy of aluminum, silicon and magnesium. It is medium-strength, corrosion-resistant and weldable. All three can be heat-treated to increase hardness and can be used for spur gears, etc.
(IV) Thermoplastics
For gears where weight is a key criterion, thermoplastics are the best choice. Plastic gears can be processed and some are suitable for injection molding, such as acetal (polyoxymethylene or POM), which comes in two forms: homopolymer (POM-H) and copolymer (POM-C). It can be used for a variety of gears. It has good dimensional stability, low friction coefficient, creep resistance, self-lubricating but brittle. Nylon is more suitable for bearing impact loads. For example, nylon 6/6 has good vibration absorption and is dimensionally unstable when exposed to water. It can be self-lubricating by impregnating molybdenum, or embedded with glass fiber or carbon fiber to increase strength, and is suitable for various gears.
4.Common gear manufacturing methods
Gear manufacturing is a complex job that requires high precision and multiple processes to achieve a balance between cost, quality and operational efficiency. Common gear manufacturing processes include:
(1)Casting
Casting is a common process for manufacturing gear blanks or cylinders, which is suitable for large gear production. Common casting methods include shell casting, die casting, sand casting and metal mold casting. Casting processes are the choice of many applications due to their large-scale production capabilities and relative simplicity.
(2)Forging
Forging can produce gear blanks and finished gears, which are suitable for relatively simple gears, especially with good fatigue performance in heavy-duty applications. However, the forging process requires a lot of force, which limits the size and thickness of the gear. It is usually suitable for gears with a diameter range of 6 to 10 feet. Whether machining is required depends on the type of forging.
(3)Extrusion and cold drawing
Extrusion and cold drawing are gear forming processes. During extrusion, the heated metal profile passes through a predetermined shape die to form a bar; the cold drawing process is similar, but the blank is not heated, which can improve mechanical properties, but the cost is higher. Although the extrusion tool cost is low, it is not necessarily the most economical method.
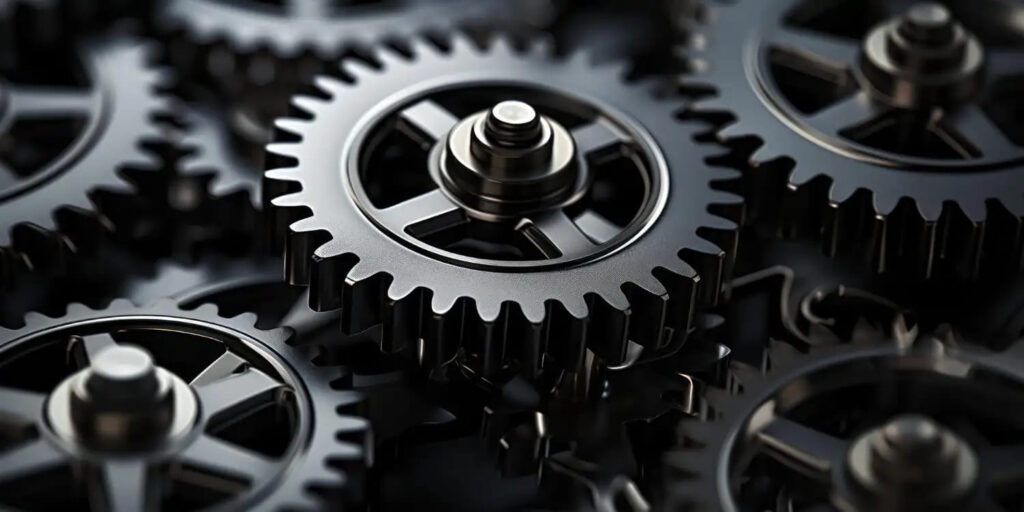
(4)Powder Metallurgy
Powder metallurgy is an advanced process that is widely used in gear manufacturing. The process starts with metal powder, which is shaped, compacted and then heated. Powder metallurgy is efficient and suitable for large-scale production, but the resulting gears have load and size limitations, high initial setup costs, and are not suitable for small-scale production.
(5)Blanking
Blanking is similar to extrusion, using metal sheets and dies to form the gear shape, and spur gears work best. This process has been used in lightweight applications in multiple industries, such as office equipment, hydraulic equipment, etc.
(6)Gear machining
Machining is a common gear manufacturing process, and the rise of CNC machining has further increased its popularity. Common gear machining methods include hobbing, forming, broaching and milling.
5.Gear Manufacturing Post-Processing
Depending on the gear manufacturing method, post-processing steps are critical to ensure that the gear reaches optimal condition. Post-processing includes activities such as heat treatment to enhance fatigue properties, dimensional correction and surface finishing. Common surface treatment processes include grinding, honing, shaving and polishing.
1.Grinding
It can make the surface smooth and can be performed intermittently or continuously.
2.Honing
It can polish the surface and correct minor errors in the tooth shape.
3.Shaving
It removes a very thin layer from the surface to obtain a smooth profile, but it is more expensive and is rarely used in gear production.
4.Polishing
Use compression to smooth the surface and enhance the finish.
Summarize
Gear manufacturing is a complex and delicate process involving a variety of processes, materials and post-processing methods. Different gear types, application scenarios and manufacturing requirements require the selection of appropriate processes and materials. With the continuous advancement of technology, gear manufacturing processes are also constantly developing and improving to meet the growing industrial needs.
If you need an experienced gear manufacturer, Xavier is your best choice. The Xavier team is well-equipped to provide high-quality customized processing solutions to meet your personalized processing needs. If you want to learn more or discuss your processing needs with us, please feel free to contact us.