Introduction to Machining Metals
As with any precision machining, knowing what materials the final product will be made of before you begin work is important for both planning and cost. Precision machining is no exception. The goal of optimal machining is to provide customers with high-quality precision components from the prototype to the production stage. JR Machining has the equipment and experience to manufacture a wide range of precision parts using metals such as brass, steel, aluminum, nickel, and more.
Knowing what materials and metals to use allows us to provide more accurate estimates and quotes to potential customers. Today, we want to talk about what types of metals we use in our machining.
There are actually five types of metals that you might use when doing a project. Each metal has different properties and therefore different advantages and disadvantages. Let’s talk about them:
1.Ferrous Metals
Ferrous metals are metals that contain iron, such as steel or cast iron. Their main property is a high strength-to-weight ratio, which means it can be used for products that need to be strong and lightweight. Ferrous metals are also durable, high-quality, magnetic, and can be recycled, which is more environmentally friendly than other metals. While ferrous metals have many advantages, they are also prone to corrosion and can be costly to complete a project. These metals are very strong, but heavier than aluminum and titanium alloys, which can be a disadvantage depending on the project. Some common examples of ferrous metals are stainless steel, cast iron, carbon steel, and wrought iron.
2.Aluminum
Of the nonferrous metals, aluminum is the most commonly used. The advantages of aluminum are that it is easy to machine, has a high strength-to-weight ratio, and even has some corrosion resistance. Aluminum comes in different grades or alloys that are used for different purposes. 2011 aluminum is designed for machining, but 6061 is also one of the more common grades. Like all aluminum grades, this material is strong, durable, and easy to machine, and because it is widely available, it is very economical.
Since aluminum comes in a variety of different alloys, each alloy has different properties that make it perfect for some applications and not so good for others. When working with aluminum, it is important to have a thorough understanding of the machinability of each alloy. While aluminum is a strong and affordable material, it is inherently soft and has a low melting point, making it difficult to machine.
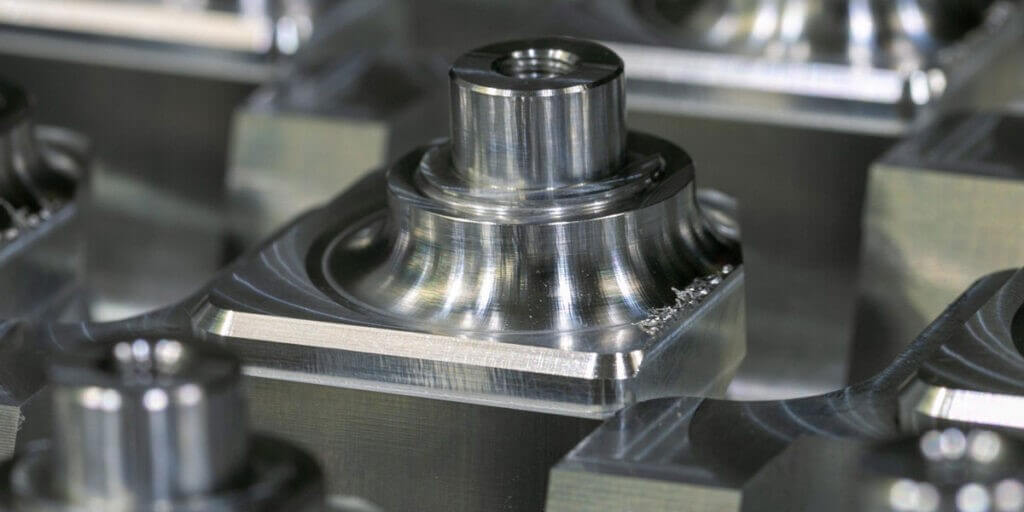
3.Brass and Other Copper Alloys
Many people choose brass or copper because of their decorative properties, electrical and thermal conductivity, and corrosion resistance. Brass and copper are easy to machine and are often used in construction applications such as joining, finishing, and plating. While using brass and copper can provide an upscale look, they do require a lot of maintenance as they tarnish easily.
4.High-Temperature Nickel
High-Temperature Nickel is a superalloy developed specifically for aircraft engines. Since they are primarily used in turbine engines for the aerospace and marine industries, this metal is incredibly strong. High temperature nickel can withstand extreme temperatures and highly corrosive environments. On the other hand, high temperature nickel is extremely difficult to machine due to its strength and ability to withstand high temperatures.
5.Titanium
Titanium is commonly used in aerospace and transportation-related industries for its strength and corrosion resistance. Titanium is twice as strong as aluminum, but it also weighs about 60% more. In addition to its high strength, titanium is also biocompatible, meaning it is non-toxic and will not be rejected by the human body. While titanium has these advantages, it is difficult to machine, extremely expensive, and will burn even at air temperatures below its melting point.
From strength and durability to cost and corrosion resistance, there are many factors to consider before selecting a metal. Understanding the properties and characteristics of these metals will help you determine the right alloy for each project.