Black Oxide Coating Process Basics and Step-by-Step Guide
Black Oxide Coating is one of the surface treatments used on machined parts. It can give good surface characteristics on the machined parts while having little effect on the dimensions of the parts. In this article, we will explain the process of black oxide coating, their types and applications.
1.What is black oxide coating (blackening)?
Black oxide coating is a type of coating that belongs to the category of conversion coating, which is a surface treatment that uses a chemical process to produce the coating. The name “black oxide or blackening” comes from the fact that the coating can turn the color of the metal surface black.
The black oxide surface treatment process involves immersing the machined metal parts in an alkaline solution, which converts the iron on the metal surface into a compound called magnetite, which forms a black coating on the metal surface. Metals that can be black oxide include stainless steel, copper, silver solder, zinc, etc.
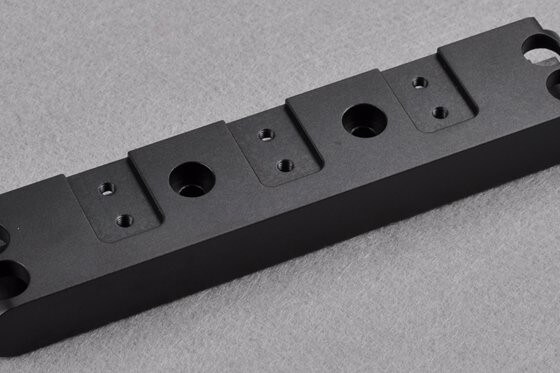
2.Steps of the black oxide process
The blackening process generally involves three steps, which include:
①Cleaning
The process involves preparing the workpiece for the black oxide finishing coating. The machinist uses an alkaline solution to degrease and clean the part. The alkaline solution is then rinsed off with distilled water.
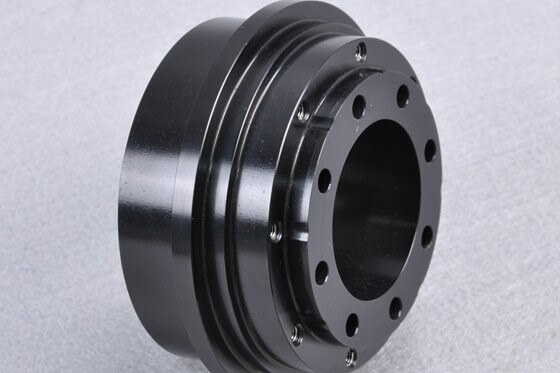
②Rust Removal/Pickling
This process is only necessary if the part is rusted or scaled. It involves soaking the finished part in an acid solution to remove all rust and oxide stains from the part.
③Neutralization
This process is only necessary if the finished part has blind holes or the part needs to be assembled. This involves re-cleaning the part with an alkaline solution. This helps prevent bleed-through that can damage the surface of the part.
④Deplating
This process is only used if the finished part is plated with another material such as chromium, zinc, cadmium, etc. The machinist must de-plate the part because the black oxide finish cannot adhere to the plated part.
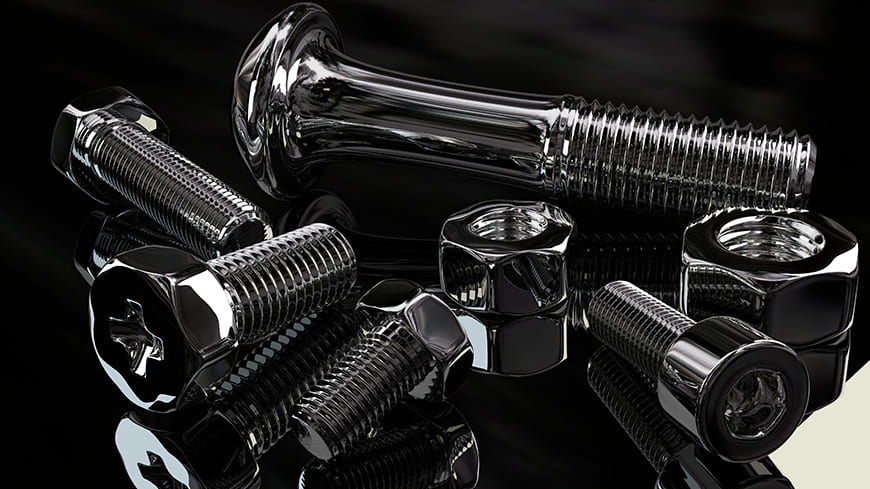
⑤Black Oxidation
This is the process of applying the black oxide finish where the machinist immerses the machined metal part in a tank filled with various alkaline solutions such as sodium hydroxide, nitrates, and/or nitrates. This stage has different temperatures that determine the type of coating on the part surface.
At high temperatures (141°C), the process leaves a magnetite coating (Fe2O3) on the part. However, at low operating temperatures (90 – 120°C), the process deposits a copper selenium coating (Cu2Se) on the surface of the part.
⑥Post-treatment
Without post-treatment, the finished part is still very susceptible to corrosion. This rule does not apply to black oxide stainless steel or brass surfaces. This is because these metals have inherent corrosion protection. However, for other metal parts, post-surface treatment is quite important. Common post-treatment methods are oil, wax and lacquer.
Oil is a common post-treatment material used by machinists. It makes the surface shiny and also enhances lubrication and corrosion protection. Wax makes the surface duller, but has higher lubrication and corrosion protection properties. Lacquer is also a good choice, but it needs to be done quickly because the black oxide coating dries very quickly.