Boring Machining Process: Detailed Overview
Boring machining is a typical technique for making holes in a material. Because during the manufacturing process, the material must go through a series of cutting processes until the final product is produced. And some parts may require holes to be made in the material.
Although other operations such as drilling can also create holes in a workpiece, CNC drilling is best suited for machining holes with larger diameters and higher dimensional accuracy.
In this article, we will discuss boring machining extensively and compare it to similar industrial cutting processes.
1.What is boring machining in the manufacturing industry?
Boring machining is a subtractive manufacturing technique used to enlarge pre-drilled or cast holes while improving their dimensional accuracy. The process uses a single-point cutting tool to remove sections of material from the inside of the workpiece.
Depending on the size and specifications of the required hole, boring machining is an ideal method for machining holes of different accuracy levels, diameters, and positional limitations. In fact, it is more suitable for machining larger holes than drilling due to its higher accuracy.
CNC hole machining uses machines such as lathes, jig boring machines, boring mills, etc. These devices come in different forms; for example, there are vertical boring machines and horizontal boring machines.
There are a variety of different boring tools and machines that can be used for other purposes. However, all boring tools perform three basic operations, namely:
- Enlarging a hole to a precise size and finish.
- Straightening a pre-drilled or threaded hole and repairing casting defects.
- Making a concentric hole with an outside diameter.
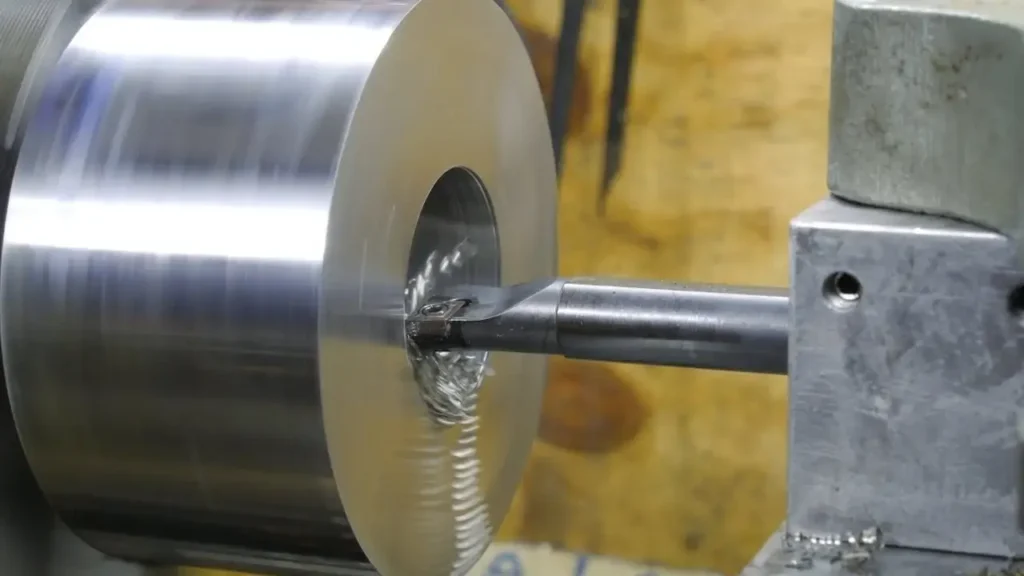
2.How is boring machining performed?
The boring process requires carefully placing the head of the machine into the already drilled or cast hole. The device then begins to slowly scrape away portions of the inner wall to enlarge the hole diameter. Drilling tools are similar to lathe tools used in lathes and milling machines.
Every drilling machine contains the following components.
- Chuck: A fixture that holds the material firmly while drilling.
- Workpiece: The material to be drilled using the drilling machine.
- Drilling tool: A cutting tool that removes (scrapes) portions of the hole, creating a larger and more precise hole.
3.Why and when do you need to drill holes?
We have already mentioned that drilling, milling, and some other manufacturing processes may be suitable for machining holes in a workpiece. However, when machining large holes requires high precision and tight tolerances, boring is the best machining technique.
Some industrial applications of CNC drilling include drilling holes in screws, manufacturing engine cylinders, and more.
In addition, manufacturing companies also use boring processes to drill holes in bearings, pins, and other substances that require hollow parts.
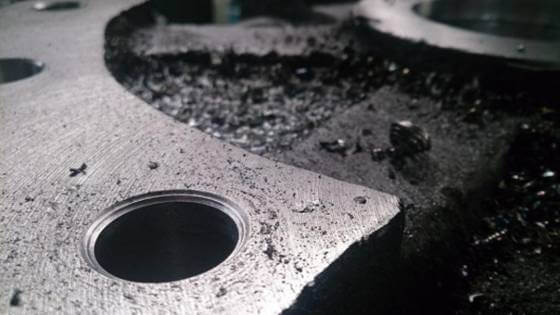
4.Types of Drilling Machines
Let’s first understand the common types of drilling machines.
1) Horizontal Boring Machines
These machines are the most common and widely used boring machines. They are common in many shops that specialize in repairs and small-scale manufacturing.
Holes are enlarged by inserting a single-pointed tool horizontally into an existing workpiece hole. In addition to drilling, these devices are also suitable for milling, drilling, and reaming operations.
2) Benchtop Boring Mills
These machines are typical horizontal boring machines. As the name implies, they are placed on a table and are used to perform various boring operations.
These machines use a spindle that is parallel to the table to drill holes. In addition to drilling, these machines are used as general-purpose manufacturing equipment, especially in smaller companies.
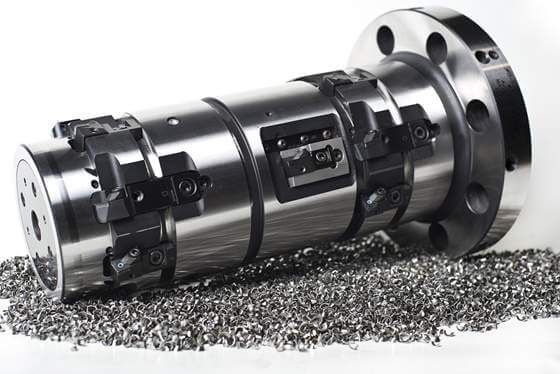
3) Vertical Boring Machine
This machine uses a rotating cutting piece connected to a horizontal table, but, since the drill moves up and down, it gets its name – vertical boring machine.
This device is suitable for enlarging existing cylindrical or conical holes as required by the workpiece. The hole is usually concentric with the axis of the rotating tool.
4) Precision Boring Machine
Like all drilling machines, these machines use a single-point cutting tool to drill holes in the workpiece. Therefore, the hole widens as the material moves parallel to the rotating tool.
Therefore, precision boring machines are ideal for machining large internal holes in workpieces with tight tolerances and extremely high precision requirements. In addition to enlarging the hole diameter, precision boring machines are also suitable for correcting the initial hole diameter and correcting all previous defects, maintaining high dimensional accuracy.
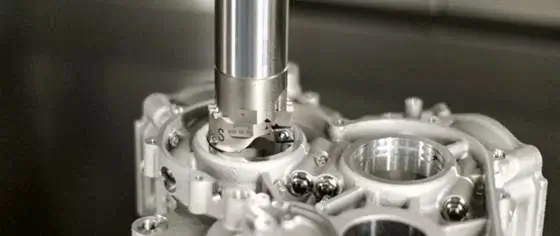
5.What are the challenges of drilling operations?
Indeed, drilling is an ideal operation for creating precise holes in materials. However, as with most manufacturing techniques, machinists may encounter some challenges associated with this process.
Let’s take a quick look at some of these challenges.
1) Tool wear or damage
During the cutting process, the parts of the drilling device will generate friction, causing tool wear and damage. As a result, this will reduce the function of the machine – the accuracy specifications will begin to decrease.
In addition, the product may require more surface treatment and post-processing operations.
2) Processing errors
For drilling, processing errors involve dimensional changes, including the shape, location of the hole, and the surface finish of the product.
These errors may be caused by one of the following reasons:
- Inappropriate boring process parameters.
- The workpiece is too rigid or too plastic.
- The tool bar aspect ratio is too large.
- The machining allowance adjustment is not allocated properly.
- Using a blade or tool that is not suitable for the workpiece material.
3) Surface treatment
Drilled parts may have poor surface finish, such as the appearance of cut lines or scales. Feed rate plays a critical role in the surface finish of a drilled part. Typically, manufacturers start drilling at a feed rate of 0.1 to 0.2 mm per revolution.
4) Measurement Error
This can be a significant challenge for most manufacturing processes. Using the wrong measuring tool or entering incorrect measurements can ruin the final product of the drilling process.
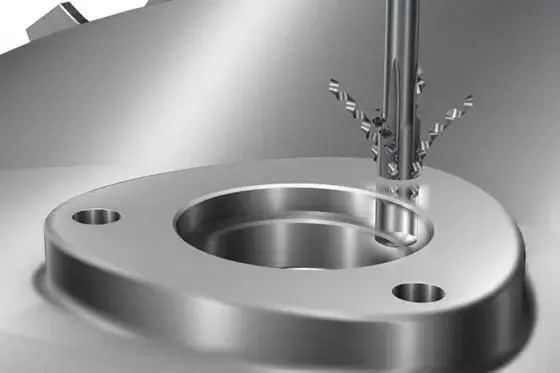
6.Important Tips for Boring Machining
Every machining process requires extremely high dimensional accuracy, including drilling. Therefore, every aspect of the machining process needs to be optimized.
The following is a guide to getting the best results using this machining technique when drilling holes in workpieces.
1) Machine Setup Tips
- Make sure to regularly check the tool wear of the boring machine and replace the faulty tool in time to ensure machining accuracy and boring quality.
- Before machining, check whether the workpiece fixture and the fixture that fixes the workpiece material are reliable and firmly fixed to avoid offset during the boring process.
- Make sure the machining process is carried out at a suitable low temperature and with sufficient lubrication to reduce friction and simplify cutting operations.
- Confirm and correct the repeatability and dynamic balance accuracy of the spindle to meet the CNC machining specifications.
- During the trial machining stage, when boring, check the dynamic gravity overhang value of the boring bar and make necessary adjustments to limit vibration and centrifugal cutting.
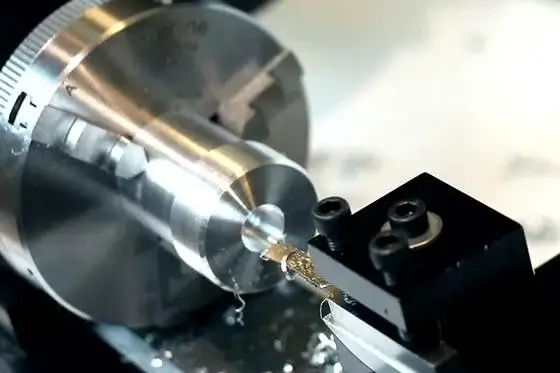
2) Accurate measurement tolerances
- Measure the diameter of the drilled or cast hole with a caliper and calculate the reserved machining allowance.
- Allocate drilling allowance according to the machining requirements (roughing, intermediate machining, finishing). Most industries follow: 0.5mm for roughing, 0.15mm for intermediate machining, etc.
- For difficult-to-machine materials and workpieces with high precision requirements, ensure that the drilling allowance is not less than 0.05mm
3) Boring tool tips
After setting up the boring bar, ensure that the cutting edge of the boring machine is in place. This includes ensuring that the upper plane of the tool edge is on the same horizontal plane as the feed direction of the boring cutter cutting head.
4) Trial drilling tips
When drilling, leave an allowance between 0.3 and 0.5 mm on the drilling tool. In addition, you may want to modify the allowance of the rough drilled hole to no less than 0.5 mm so that the final product after drilling meets the tolerance specifications.
7.Comparison of boring machining with other machining methods
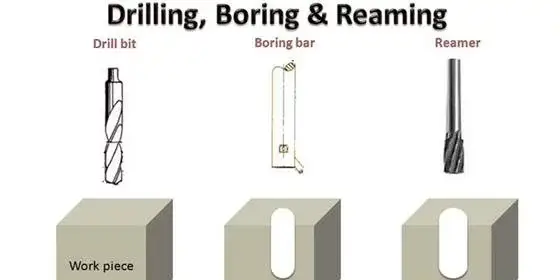
A range of other machining processes have similarities with boring. Here, we take a look at the similarities and differences between boring and similar machining processes.
1) Boring vs. drilling
Drilling and drilling are standard subtractive manufacturing processes – they both involve removing a portion of the material to form a hole. However, there are significant differences between the two methods.
Here are some of the differences between them.
- Drilling is the process of forming a hole in the workpiece, while boring is the process of enlarging the initial hole. Therefore, drilling precedes boring in the manufacturing process.
- Unlike drilling, the final product of the precision boring process has a good surface finish and first-class dimensional accuracy and precision.
- Boring is mainly done to enlarge the diameter of a hole, while drilling is done to increase the length of a hole in a material.
- In general, drilled holes are usually narrow, and sometimes chip evacuation is difficult, requiring continuous drilling. Boring holes have a wide enough diameter to facilitate chip evacuation.
2) Boring machining vs. turning machining
Like boring and drilling, turning is also a subtractive machining process. Boring uses a single cutting tool with a pointed tip to enlarge a pre-existing hole in a workpiece, while turning uses a static, non-rotating cutting tool to remove material fragments from the outside of the workpiece.
The main difference between the two processes is that turning removes material from the outer surface, while boring removes the inner part of the workpiece. Manufacturers usually use a machine called a lathe for turning operations, which is also a standard tool used in boring. However, boring uses other traditional equipment, similar to a milling machine.
3) Boring vs. reaming
Both are cutting processes that involve removing internal components of a workpiece. However, drilling uses a single-pointed tool while reaming uses a rotating cutter to scrape away material fragments. Another similarity is that both processes are performed on already drilled or cast holes.
Therefore, the main difference between them lies in the application process. While boring essentially aims to widen a pre-existing hole, reaming aims to create a finer and smoother inner wall for the workpiece. Therefore, reaming only removes a small amount of material from the material as its purpose is only to create smooth walls.
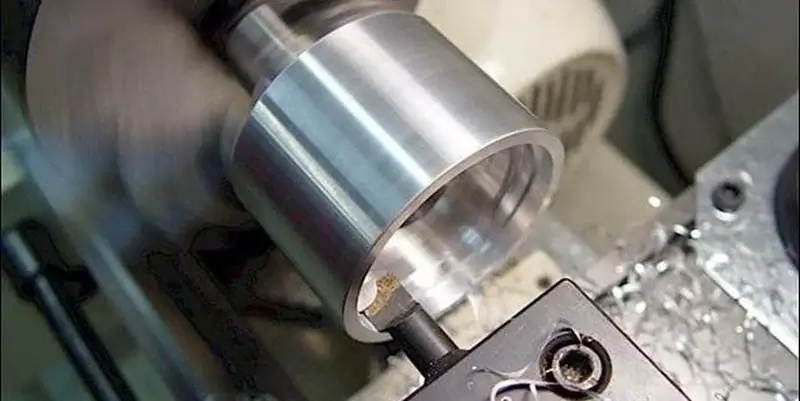
8.Conclusion
This article has covered the boring process in detail. It is a reliable and fast machining process used to widen cast or pre-drilled holes in a workpiece. Since it is a CNC machining process (i.e. computer controlled), you can be sure of its high precision and accuracy.
It is important to know that like other CNC machining processes, boring machining also presents some challenges.If you are looking for an experienced CNC machining manufacturer, Xavier is your ideal choice. The Xavier team is well-equipped to provide high-quality CNC machining solutions. If you need more information or to discuss your machining needs with us, please feel free to contact us.