Boring Machining Process: The Ultimate Guide
In the field of manufacturing, boring is an indispensable technical means. When it is required to generate holes of different specifications and sizes on the workpiece, the Boring Machining Process plays its unique role. It can modify existing holes, has good compatibility with a variety of materials, and performs well in achieving tolerance requirements. This article will explore the principles and advantages of boring technology in depth, and take you to a deeper understanding of this technology.
1、What is Boring Machining Process
Boring is a subtractive manufacturing process that uses specially designed cutting tools to enlarge holes that have already been drilled or cast. Different boring tools include lathes, boring mills and jig boring machines, all of which perform basic operations such as enlarging holes, creating concentric holes and straightening holes.
2、Boring Machining Process operation flow
Boring can be done on a lathe or a milling machine. Before the operation, you need to select the appropriate cutting tool, clamp the workpiece, install the tool and align the hole. Set the cutting parameters according to the workpiece material and hole specifications, and gradually expand the hole to the required size and surface finish through the engagement of the cutting tool and the workpiece.
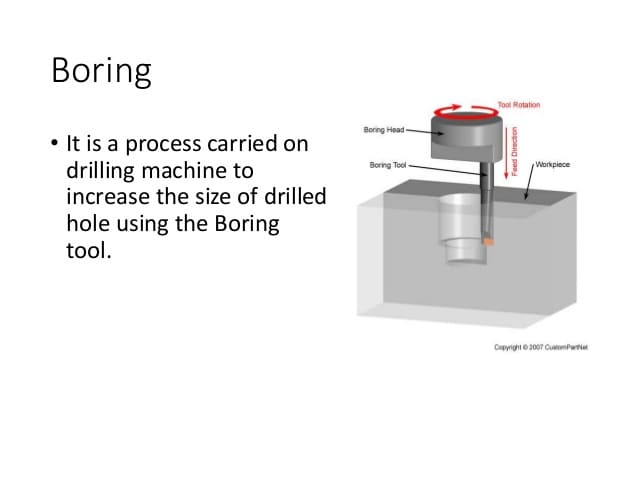
3、Types of Boring Machines
1.Horizontal boring machine:
used for drilling horizontal holes, with horizontal spindle, suitable for large and solid parts, and can also perform drilling, milling and reaming.
2.Vertical boring machine:
a special milling machine with vertical spindle, suitable for heavy workpieces and large holes, and can achieve tight tolerances.
3.Precision boring machine:
with high precision and good surface finish, it is suitable for industries such as aerospace, medical and automotive, and can correct hole defects.
4.Table boring machine:
a common type of horizontal boring machine, with an adjustable worktable and a wide range of uses.
5.Floor boring machine:
used for processing large parts, with a T-shaped space on the bottom plate to fix the workpiece.
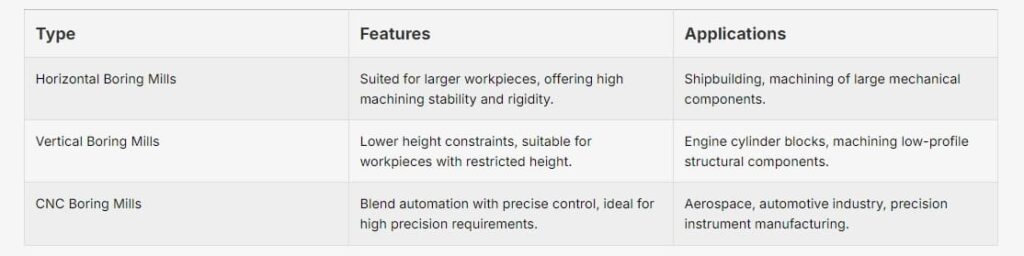
4、Application of Boring Machining Process
Boring is widely used in material processing in many industries. In the automotive industry, it is often used in the production of engine cylinders and engine blocks; in the aerospace field, this process is used to make precise holes for engine parts; in addition, in some special fields, such as jewelry and furniture manufacturing, boring can also be used to process decorative holes for aesthetic purposes.
5、Advantages of Boring Machining Process
1.High precision
During boring, the cutting tool is aligned with the centerline of the existing hole, which can achieve higher precision than drilling and other techniques that use the overall position of the hole for processing. The cutting tool is aligned with the centerline of the hole, and CNC boring reduces errors and has higher precision.
2.High efficiency:
Boring is a fast manufacturing technology that helps speed up production and thus shorten the time to market of products.
3.Excellent surface quality:
The Boring Machining Process can produce holes with excellent surface finish and meet high quality requirements.
4.Versatile
Boring can be performed horizontally or vertically on different machines, and a single boring tool can process holes of different diameters.
5.Compatible with CNC technology
The Boring Machining Process is perfectly compatible with CNC technology. This reduces manual intervention, reduces the risk of errors, and saves costs.
6.Suitable for complex tasks
CNC boring can perform complex machining operations and support mass production of high-quality products.
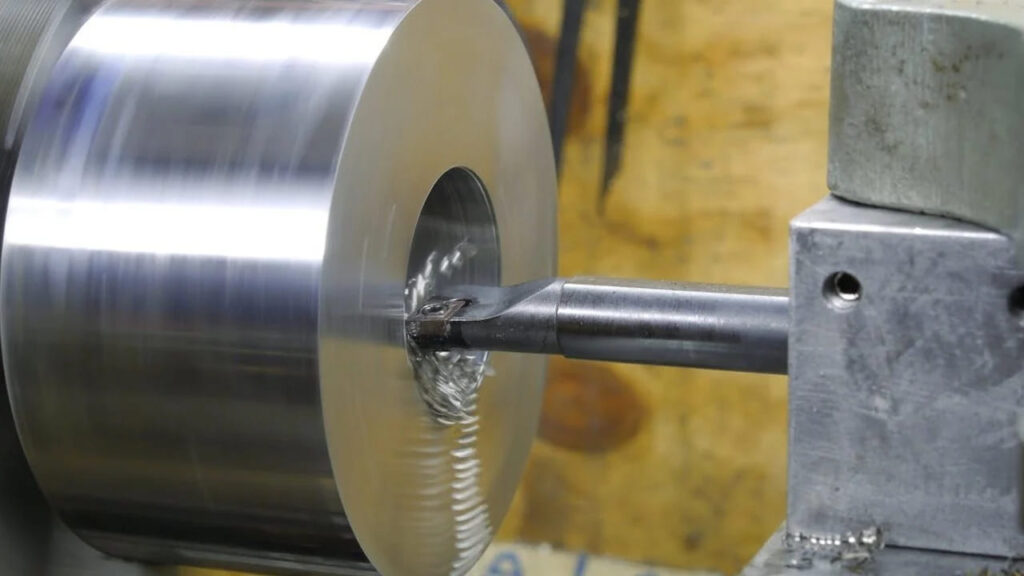
6、Challenges of Boring Machining Process
1.Machine wear:
During the cutting process, the cutting tool is subject to friction, which will cause wear of the tool over time. Therefore, it is necessary to use the correct cutting parameters, ensure good lubrication and regularly maintain the machine to extend the tool life.
2.Processing errors:
During the boring operation, processing errors may occur, which will affect the quality of the final part. It may be caused by incorrect cutting parameters, improper machine settings and tool mismatch. It is necessary to adjust the settings and select the correct tool.
3.Finishing and quality control:
Feed speed affects surface finish. Too high feed speed will cause chatter. It may also cause problems due to poor chip removal and incorrect blade radius.
7、Key points for optimal Boring Machining Process
1.Choose the right tool:
Different boring tools are required for different applications. Choosing the right equipment correctly ensures the precision and accuracy of the hole.
2.Choose high-quality coolant and lubrication:
The Boring Machining Process generates heat and causes friction, which can have an adverse effect on the process. By using high-quality coolants or lubricants, the temperature of the cutter can be regulated, the surface finish can be improved, and the tool life can be extended.
3.Optimize cutting parameters:
Before processing, it is important to determine the correct parameters based on the material and requirements to improve efficiency and reduce errors.
4.Maintain boring equipment:
Over time, the tools of the boring machine will gradually wear out. In order to maintain the processing accuracy and boring quality, the operator needs to regularly check and replace defective parts and clean the equipment.
5.Ensure correct processing settings:
In order to obtain the best processing results, the boring machine needs to be set up correctly. This includes ensuring that the workpiece is firmly clamped to prevent any deviation during the process. In addition, parameters such as spindle positioning and dynamic balancing accuracy need to be verified and corrected according to the specific application.
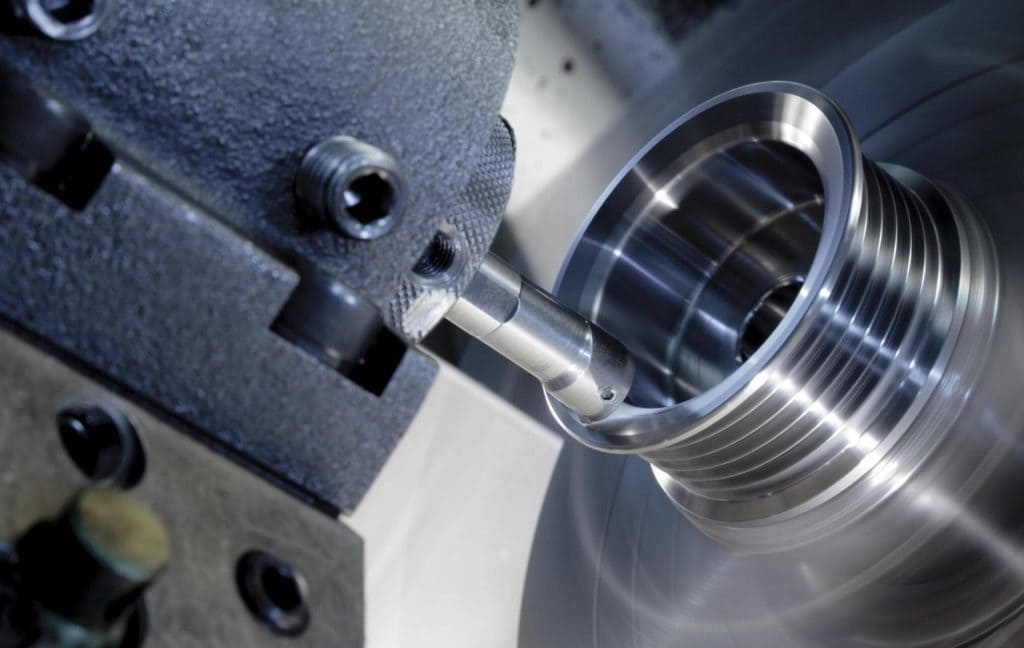
8、Comparison of Boring Machining Process with other processing technologies
1.Comparison with drilling:
Drilling only creates simple holes, while boring is a process that expands and improves the accuracy of existing holes. The accuracy level of drilling is about 0.02 inches, while the accuracy of boring can reach about 0.0005 inches.
2.Comparison with turning:
Boring is to remove material from the inside of the hole, while turning is to remove material from the outside of the workpiece. The two use different cutting tools and the amount of material removed.
3.Comparison with reaming:
Boring and reaming are similar in that they are both used to expand and refine existing holes. However, reaming removes a small amount of material from the inside of the hole, giving the hole a better finish; conversely, boring can remove more material from the workpiece, resulting in a larger diameter hole.
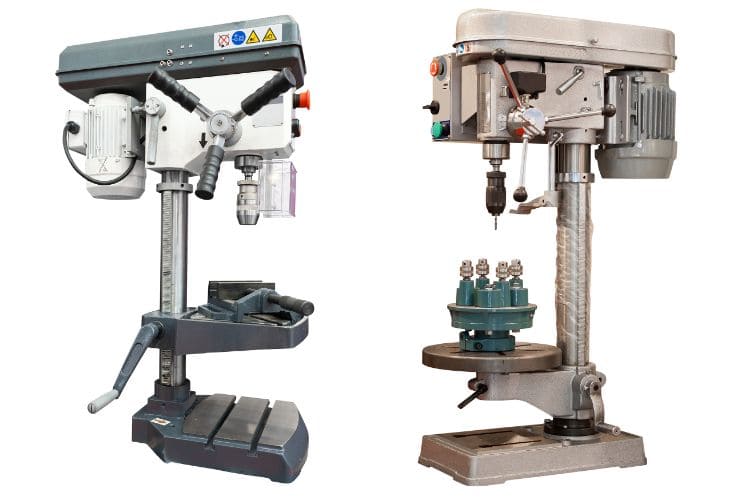
9、 Conclusion
Boring technology plays an important role in modern manufacturing. Whether it is its precise processing capabilities, various types of boring machines, wide range of material applications, or coping strategies when facing challenges and its comparative advantages with other processing technologies, boring technology has demonstrated its unique value.
If you are looking for an experienced CNC machining manufacturer, Xavier is your ideal choice. The Xavier team is well-equipped to provide high-quality CNC machining solutions. If you need more information or to discuss your machining needs with us, please feel free to contact us.