Brass CNC Machining :Golden visual temptation
Brass is an alloy composed of 60%-70% copper and 30%-40% zinc. It has a beautiful golden color, good durability and excellent machinability. Brass CNC machining services are suitable for low friction and complex parts.
In order to give you a comprehensive understanding of brass, let’s discuss the types of grades suitable for brass CNC machining, processing advantages, the differences between copper, bronze and brass, the surface treatment of brass, and factors to be considered in brass CNC machining.
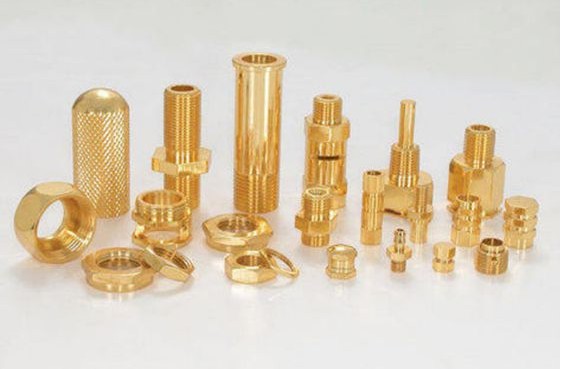
1.Types of grades suitable for brass CNC machining
Brass has different grades, depending on the copper and zinc content it contains. Brass CNC Machining | Custom | CNC.These changes in composition also affect the application characteristics of different grades of brass CNC machining. This section will introduce the advantages, disadvantages and applications of several brass CNC machining grades.
(1) C230 red brass
Features: Stronger than golden brass.
Advantages: Good corrosion resistance, excellent machinability, both cold working and hot working are possible.
Disadvantages: prone to corrosion in harsh environments, timely cleaning during brass CNC machining
Applications: decorative parts, lamps, steam iron parts, construction, jewelry, sprinklers.
(2) C330 low-lead brass
Features: relatively low lead content
Advantages: high strength, high water corrosion resistance, excellent machinability
Disadvantages: sensitive to highly corrosive conditions (acids), easy to weld difficult during brass CNC machining
Applications: power cylinders, pumps, linings, oil pipes, ammunition primers
(3) C353 engraver’s brass
Features: both wear-resistant and strong, good machinability
Advantages: good strength, excellent machinability, excellent resistance
Disadvantages: not suitable for welding, not suitable for normal hot and cold work of brass CNC machining
Applications: adapters, watch parts, wheels, couplings, gears, valve stems
(4) C360 Free-machining brass
Features: High lead content, highest machinability, incredible strength
Advantages: Excellent machinability (stronger than C353), good corrosion resistance
Disadvantages: Lead content can cause surface finish to break in some cases of brass CNC machining, acid sensitivity, possible environmental impact of lead
Applications: Screw machine parts, musical instruments, electrical equipment, plumbing fittings
(5) C365 Brass Plate
Origin: Named after George Frederick Muntz
Advantages: Excellent corrosion resistance and strength, high machinability
Disadvantages: Not suitable for welding, limited cold forming
Applications: Baffles, support plates, tube sheets for condensers, heat exchangers
(6) C464 Brass Plate
Features: Incredible corrosion resistance in brass CNC machining due to the addition of tin
Advantages: Good corrosion resistance and strength, can be hot worked, similar to C360 Compared with brass, the machinability is acceptable
Disadvantages: easy to cause structural cracks on the alloy surface, easy to dezincify over time
Applications: condenser tubes, missile parts, naval applications, wear plates, fasteners, bushings

2.Advantages of brass CNC machining
(1) Brass is an alloy of copper and zinc. It is cost-effective and highly durable, and has excellent heat and corrosion resistance, making it an ideal alternative to many other more expensive metals and alloys.
(2) Brass has extremely high ductility due to the copper content. Surprisingly, the ductility of brass is even better than that of copper. The high ductility of brass makes it the first choice for machining projects. Brass CNC machining allows machinists to easily process brass metal into different shapes.
(3) Due to its low coefficient of friction, brass is the preferred material for brass CNC machining in applications such as gears, locks and bearings.
(4) With good strength and hardness properties, brass is not only easy to process, but also has high strength. Although it is not as strong as steel, it is also quite durable.
(5) Aesthetics. For machining, the aesthetics of the finished product is one of the main considerations. Brass naturally has a bright golden color, which means that brass CNC machined parts can be used with little or no additional surface treatment.

(6) Brass is a natural antibacterial agent, making it ideal for medical applications.
(7) Because brass does not produce sparks, it is often used to make parts that may be used in explosive or flammable environments.
(8) As a high-density material, brass CNC machined parts are ideal for heavy industrial parts.
(9) Brass is an ideal machining metal. During brass CNC machining, it can be easily cut at faster speeds and feed rates without negatively affecting tool wear, surface finish and chip formation.
(10) Brass has a high recycling rate and high utilization rate. Brass can be 100% recycled, and the waste generated after brass CNC machining can be recycled to save costs. In addition, brass shavings are used to produce more brass over and over again without losing the properties of the material.
3.Copper vs. bronze vs. brass, can you tell the difference between these three?
When learning about brass CNC machining, we also need to talk about the differences between brass, bronze and copper. What is the relationship between the three? To understand these, let’s take a look at the differences in their material properties, which is crucial to helping you choose the most suitable application.
(1)Differences in material properties
Copper is a non-ferrous metal that exists in a pure state. This metal exists naturally and you can use it directly for processing.
Bronze is an alloy of copper and usually contains a considerable amount of tin as the main element. However, it also contains nickel, aluminum, phosphorus, zinc, etc.
Brass is an alloy of copper and zinc. It usually contains lead and may also contain elements such as manganese, iron, aluminum, and silicon. The scope of brass CNC machining is relatively wide.
(2)Differences in corrosion resistance
Copper can resist salt solutions, soil, non-oxidizing minerals, organic acids and alkaline solutions, and is corrosion-resistant.
Bronze is a copper alloy that usually oxidizes when exposed to air. Thus, it forms a protective layer (mottled patina). Bronze can withstand saltwater environments. Therefore, it is very useful in marine applications and marine fittings.
Brass is less corrosion resistant than bronze and copper. However, certain brasses that contain a lot of manganese are generally more corrosion resistant.
In conclusion, bronze is the most corrosion resistant of the three metals.
(3)Difference in durability
Copper is a strong material, but more flexible than bronze. You can stretch and bend it easily with little cracking or scratching.
Bronze is a strong and durable material that does not bend easily. Therefore, it is a durable material.
However, brass is prone to cracking, but its durability is still very good.
(4)Difference in weight
Based on density, the weight of bronze and brass is very close. The density of brass is about 8720 kg/m3, the density of bronze is about 7400 to 8900 kg/m3, and the density of copper is about 8930 kg/m3, copper is the heaviest of the three metals.
If you have to choose between bronze and brass when your project requires lightweight metal, brass CNC machining is the better choice.
(5)Difference in weldability
Brass, bronze, and copper are all weldable in their respective fields. These metals can be joined by silicon bronze welding, MIG equipment, or other techniques.
In addition, brass alloys also support MIG, TIG, and silver soldering. However, lead-containing alloys are more difficult to weld. Basically, alloys with lower zinc content are easier to weld.
(6)Difference in color
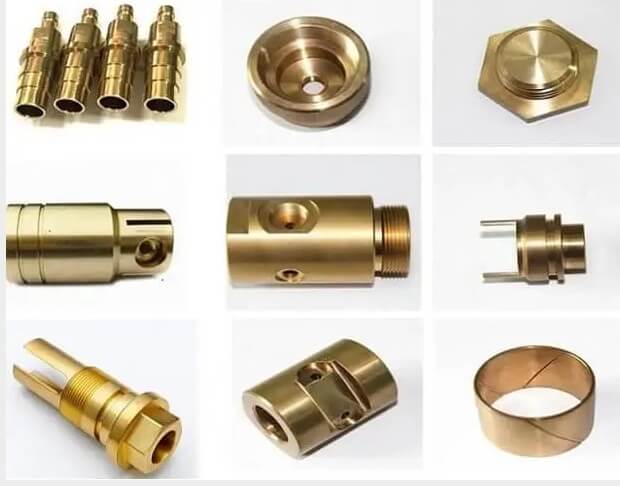
Brass has a soft golden color, similar to ordinary stone. Brass CNC machining makes brass golden.
Bronze has a slightly reddish brown color. The reddish brown of bronze has a dull golden hue.
The color of copper is very similar to bronze, and the reddish brown of newly exposed copper is very distinctive.
4.Surface treatment selection for brass CNC machining
Brass itself has no natural coating, but the natural golden surface of brass means that brass machined parts are used as end products. If the part has other cosmetic purposes, you may want to polish it externally. Here are a few optional surface treatments for brass CNC machined parts:
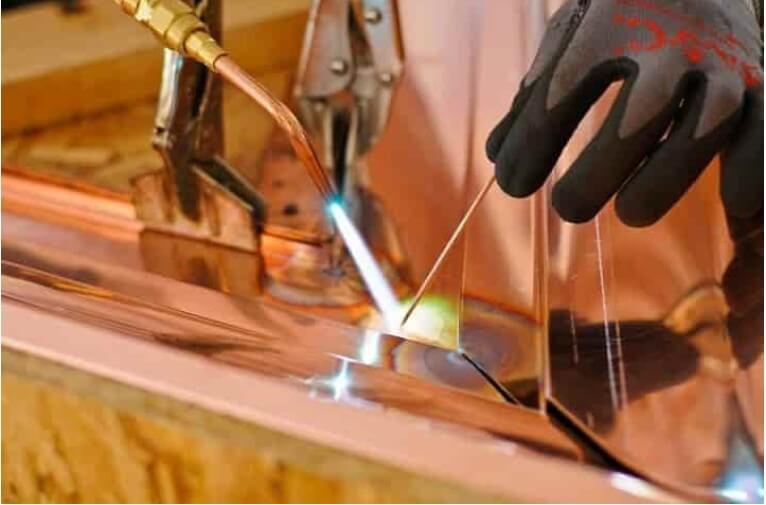
(1) Machined surface
Because brass has a bright natural golden surface, machined finished brass parts are also more beautiful. Not many, in most cases, parts with machined surfaces are usually focused on their functionality rather than aesthetics.
(2) Polishing
This involves using grinding wheels and grinding discs to polish the surface of custom brass parts. The abrasive on the grinding disc helps remove impurities and make the surface smoother. After polishing, the brass CNC machined parts will be more shiny and beautiful.
(3) Electroplating
This surface treatment method uses electroplating to bond the molecules of another metal to the surface of the brass part. The metals used for electroplating include aluminum, stainless steel, etc. The surface after electroplating is usually bright or smooth.
(4) Honing
This surface treatment method uses a grinding stone to polish the finished surface. It can form a cross pattern on the surface of the brass part.
5.What are the key factors to consider in brass CNC machining?
(1) Material Selection
Different grades of brass have unique properties, including varying machinability, strength, corrosion resistance, and aesthetics. It is critical to select the appropriate grade of brass that meets the specific requirements of the project.
(2) Tool Selection
Using sharp tools is essential in brass CNC machining. However, the type of tool is also important. High-speed steel (HSS) or carbide tools are widely used due to their superior hardness and heat resistance.
(3) Machining Parameters
Properly setting the machining parameters (cutting speed, feed rate, depth of cut) can significantly affect the efficiency of the brass CNC machining process and the quality of the finished part.
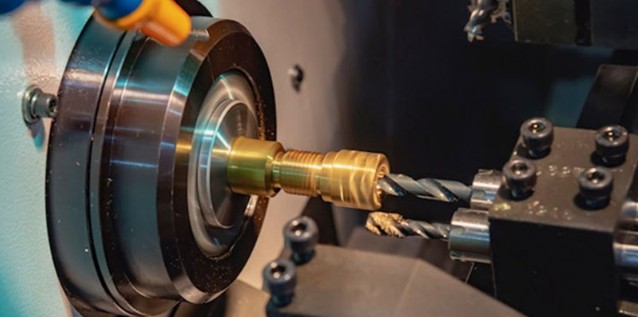
(4) Cooling and Lubrication
While brass is known for its good heat dissipation, using the right coolant or lubricant can reduce tool wear, improve surface finish, and extend tool life.
6.Summary
Brass CNC machining is a complex but rewarding process that requires a deep understanding and careful planning of all aspects. There are many aspects to consider, from the superior properties of brass that make it an excellent choice for a variety of applications to machining techniques and the types of surface finishes that can be achieved.
Brass and its numerous alloys offer tremendous potential for a wide variety of applications. Both the versatility and machinability of brass can significantly enhance the functionality and aesthetics of a final product. Additionally, manufacturing components through CNC machining of brass is incredibly cost-effective.
If you are looking for an experienced CNC machining manufacturer, Xavier is your ideal choice. The Xavier team is well-equipped to provide high-quality CNC machining solutions. If you need more information or to discuss your machining needs with us, please feel free to contact us.
1 Comment