Brass fittings: manufacturing process and application analysis
Brass fittings are widely used in industry, construction, home decoration and other fields because of their excellent mechanical properties, corrosion resistance and beautiful color. This article will introduce the manufacturing process of brass fittings and the main application areas.
1.Raw material preparation of brass fittings
Brass is an alloy composed of copper and zinc, the first step of manufacturing brass fittings is to prepare raw materials. According to the different performance requirements of the fittings, the ratio of copper and zinc in brass will be adjusted. Typically, brass contains between 60% and 90% copper and between 10% and 40% zinc. High-quality raw materials are the basis for ensuring the quality of brass fittings, so the composition and purity of raw materials need to be strictly controlled.
2.Manufacturing process of brass fittings
(1) Mechanical processing
1) Turning:
Turning is one of the most commonly used machining methods in the manufacture of brass fittings. Through the lathe to rotate the brass billet, and the use of cutting tools for cutting, can be processed cylinder, cone, thread and other shapes of fittings. Turning machining has high precision and good surface quality, and is suitable for the production of small and medium-sized fittings.
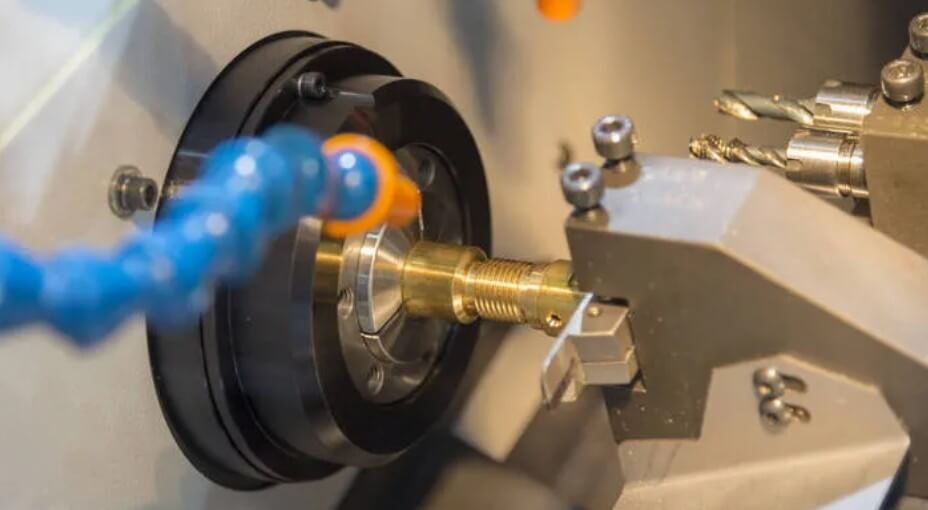
2) Milling:
Milling is a method of cutting and processing brass blanks through the milling cutter on the milling machine. Milling can process plane, surface, groove, hole and other complex shapes of fittings. Milling is highly flexible and suitable for the production of various types and sizes of fittings.
3) Drilling:
Drilling is the method of processing holes in brass fittings. Drilling can be carried out on drilling machines or CNC machining centers using drill bits. The accuracy and surface quality of the drilled holes directly affect the performance of the fittings.
4) Grinding:
Grinding is a method of processing brass fittings with high precision by means of grinding wheels on a grinder. Grinding can further improve the dimensional accuracy and surface quality of the fittings and is suitable for the final processing of high-precision fittings.
(2) 3D printing brass
1) Brass 3D printing materials
Brass 3D printing materials mainly include brass powder and brass wire material. Brass powder is suitable for selective laser melting (SLM) and electron beam melting (EBM) and other powder bed melting process. Brass filaments are suitable for filament deposition processes such as Direct Energy Deposition (DED). Brass powder and filament composition, particle size, purity and other parameters have an important impact on the performance and quality of printed parts.
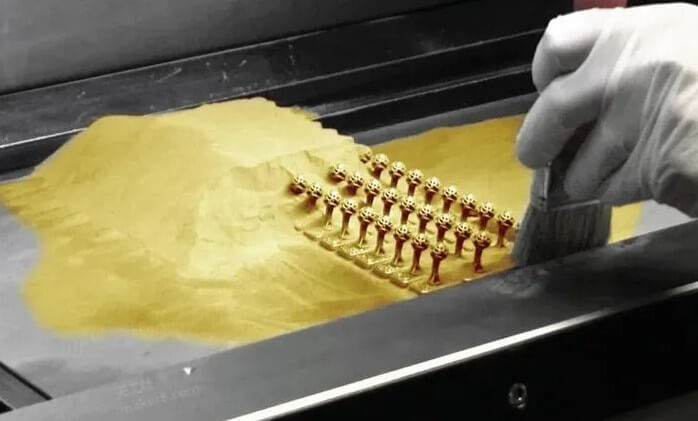
2) Brass 3D printing process
● Design 3D model:
Use computer-aided design (CAD) software to design a three-dimensional model of the required parts. In the design process, it is necessary to consider the characteristics and limitations of the printing process, such as the support structure and printing direction.
● Slicing process:
The 3D model is imported into the slicing software for slicing processing. The slicing software slices the 3D model into a series of thin slices to generate the print path and process parameters.
● Printing process:
According to the print path and process parameters generated by the slicing software, the 3D printer builds up the brass material layer by layer to form solid brass parts. During the printing process, parameters such as printing temperature, laser power, scanning speed, etc. need to be controlled to ensure the performance and quality of the printed parts.
● Post-processing:
After printing, post-processing is required. Post-processing includes removing the support structure, surface treatment, heat treatment, etc.
(3) Melting and Casting
1) Melting:
Prepared copper and zinc are put into the melting furnace for melting in a predetermined ratio. The melting temperature is generally between 950℃ and 1100℃. In order to ensure the homogeneity of the metal composition during the melting process, induction furnaces or fuel oil furnaces are usually used. At the same time, in order to prevent the metal from oxidizing, the melting process needs to add an appropriate amount of covering agent, such as charcoal or borax.
2) Casting:
After the melting is completed, the brass in molten state is poured into the pre-prepared casting mold. The casting mold can be sand, metal or ceramic, and different casting molds are suitable for the production of different types of fittings.
Sand casting is suitable for large, complex shape of the fittings; metal casting is suitable for small and medium-sized, mass-produced fittings; ceramic casting is suitable for high-precision, high surface quality of the fittings.
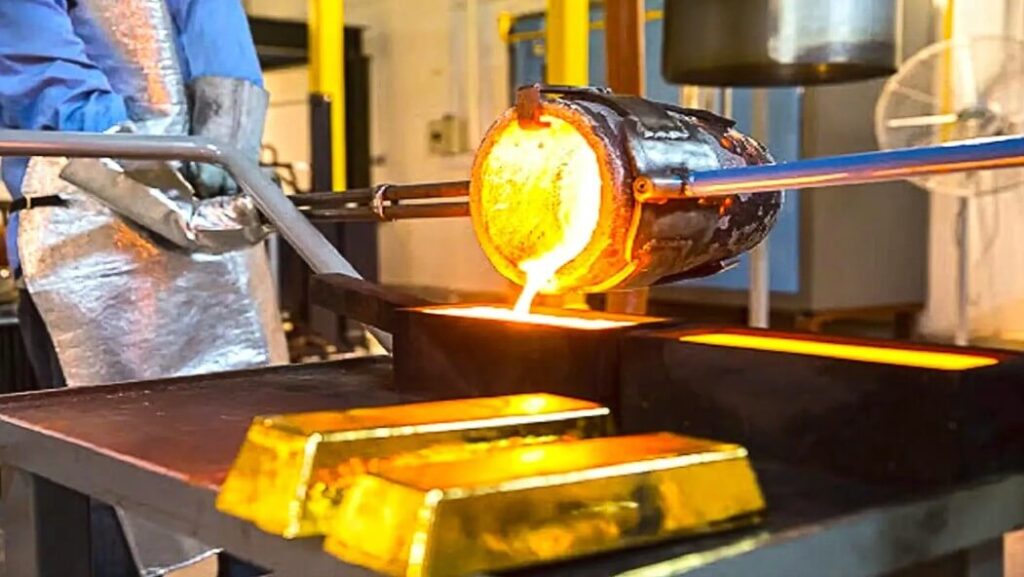
(4) forging and extrusion
1) forging:
For brass fittings that require high strength and high plasticity, forging is an important process step. Forging can be done by hammering or pressing the brass billet into the desired shape. During the forging process, the internal organization of brass is improved and the grain is refined, thus improving the mechanical properties of the fittings.
2) Extrusion:
Extrusion is the process of putting the brass billet into the extruder and extruding it into the required shape through the die. Extrusion process is suitable for the production of long, tubular or shaped brass fittings. During the extrusion process, the fluidity of brass material can be given full play to, and the molding of complex cross-section can be realized.
3.Surface treatment of brass fittings
(1) Polishing:
Polishing is the process of making the surface of brass fittings smooth and flat by mechanical friction on the surface. Polishing can improve the aesthetics and corrosion resistance of the fittings. Commonly used polishing methods are mechanical polishing, chemical polishing and electrolytic polishing.

(2) Electroplating:
Electroplating is a process of plating a layer of metal or alloy on the surface of brass fittings. Plating can improve the wear resistance, corrosion resistance and decorative fittings. Commonly used plating metals are chromium, nickel, zinc and so on.
(3) Oxidation treatment:
Oxidation treatment is the process of forming a layer of oxide film on the surface of brass fittings through chemical methods. Oxidized film can improve the corrosion resistance and aesthetics of the fittings. Commonly used oxidation treatment methods are chemical oxidation and electrochemical oxidation.
4.Main application areas
(1) Construction industry
In the construction field, brass fittings are widely used because of their beautiful appearance and excellent weather resistance. Brass doors, windows, locks, handles, faucets and other fittings are not only decorative, but also improve the safety and service life of the building. In addition, brass can also be used to make sculpture, murals and other works of art, adding artistic flavor to the building.
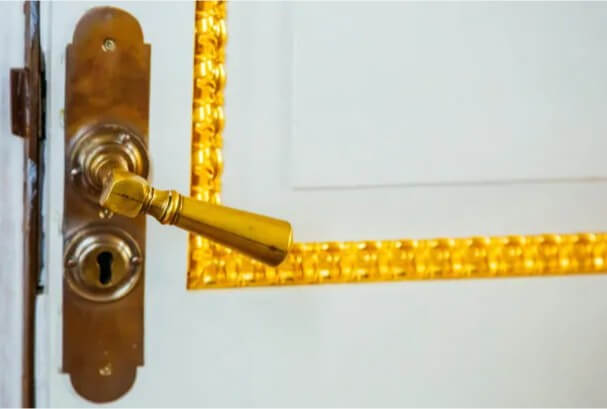
(2) Mechanical Manufacturing
The application of brass in the field of mechanical manufacturing is mainly focused on the following aspects:
1) Bearings and bushings:
Brass has good self-lubrication and anti-wear ability, suitable for making bearings and bushings and other friction parts.
2) Valves and pipe fittings:
Brass has strong corrosion resistance and is suitable for making valves, pipe fittings and other fluid control parts.
3) Fasteners:
Brass-made bolts, nuts and other fasteners have excellent mechanical properties and weather resistance, and are widely used in machinery manufacturing and construction.
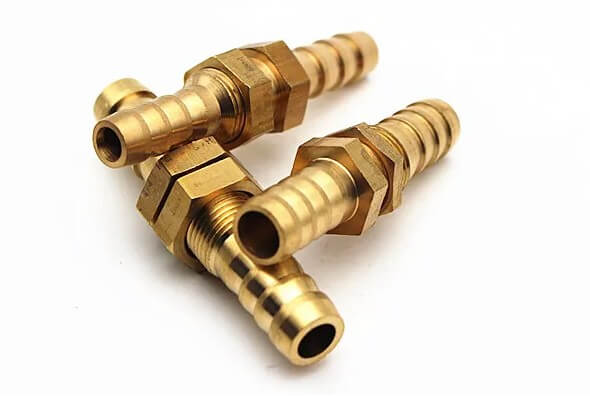
(3) Electrical equipment
The application of brass in electrical equipment is mainly focused on the following aspects:
1) Terminals and connectors:
Brass has good electrical conductivity and mechanical properties, suitable for making terminals and connectors and other electrical components.
2) Switches and relays:
Brass made of switches and relays with excellent contact properties and reliability, widely used in electrical control systems.
3) Cable sheath:
Brass cable sheaths have good shielding properties and mechanical properties, to protect the cable from external interference and damage.
(4) Shipbuilding
The application of brass in shipbuilding is mainly focused on the following aspects:
1) propeller and rudder blade:
Brass has good seawater corrosion resistance, suitable for making propellers and rudder blades and other ship parts.
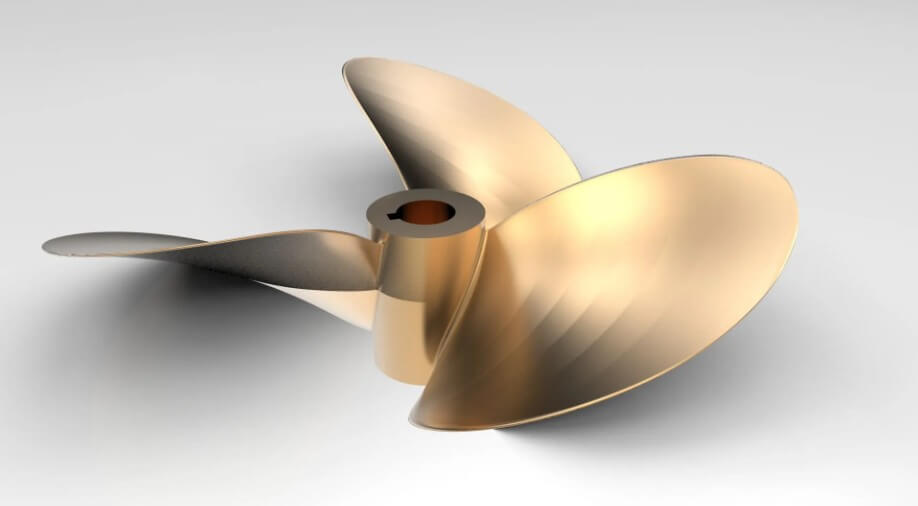
2) Valves and pipe fittings:
Brass has good corrosion resistance, suitable for making valves and pipe fittings and other fluid control parts on ships.
3) Decorative parts:
Decorative parts made of brass can add a sense of luxury and aesthetics to ships.
5.Unique advantages of brass fittings
(1) Good mechanical properties
Brass has excellent mechanical properties, including high strength, hardness and good ductility. These characteristics make brass fittings excel in bearing mechanical stress, not easy to deformation or fracture. In addition, brass also has good cutting performance, easy to process into a variety of shapes and sizes of fittings.
(2) Excellent corrosion resistance
Brass has good corrosion resistance, especially in the atmosphere, water and some chemical substances in the corrosion resistance is more prominent. This enables brass fittings to maintain stable performance for a long time in harsh environments, reducing the frequency of maintenance and replacement.
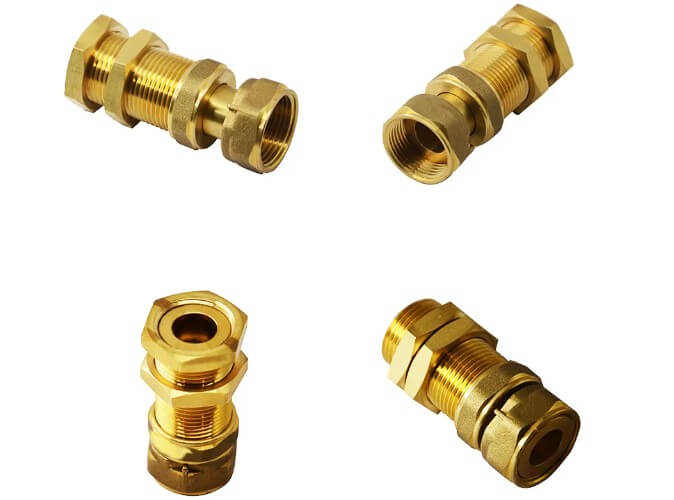
(3) Aesthetic appearance
Brass has a unique golden yellow appearance, after polishing treatment can show a mirror-like luster, has a high degree of decorative. In addition, brass can also be through the surface treatment technology (such as gold-plated, nickel-plated, etc.) to change the color of its appearance to meet the needs of different occasions.
(4) Good electrical and thermal conductivity
Brass has good electrical and thermal conductivity, although not as good as pure copper, but its comprehensive performance is more excellent. This makes brass fittings widely used in electrical equipment.
6.Summary
Brass fittings, as an important part of the manufacturing industry, the degree of sophistication of its manufacturing process directly affects the quality and performance of the product. At the same time, the application of brass fittings in many fields also reflects its wide applicability and importance.