Brass threaded inserts: manufacturing, application, advantages and disadvantages
As an important fastener, brass threaded inserts play an indispensable role in modern industrial manufacturing. With its unique material and structural design, it is widely used in various mechanical equipment, electronic products, automobile manufacturing, aerospace and other fields.
This article will elaborate on the definition, material characteristics, manufacturing process, application fields, advantages and challenges of brass threaded inserts.
1.Definition and classification of brass threaded inserts
(1) Definition
Brass threaded inserts, as the name suggests, are fasteners with threaded structures made of brass materials. They are usually embedded in softer materials such as plastics and aluminum alloys to enhance the thread strength of these materials so that they can withstand greater torque and tension.
(2) Classification
1) Classification by shape:
It can be divided into cylindrical threaded inserts and hexagonal threaded inserts. Cylindrical inserts are easy to install and suitable for most application scenarios; while hexagonal inserts are easy to install and remove using tools such as wrenches.
2) Classification by thread type:
Including standard thread, fine thread and coarse thread. Standard thread is widely used. Fine thread is suitable for occasions requiring higher precision and sealing, while coarse thread has better tensile strength.
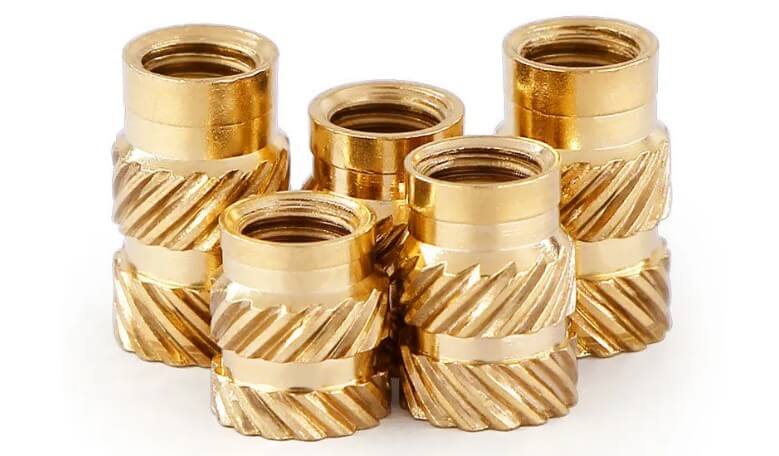
3) Classification by installation method:
There are press-in thread inserts and self-tapping thread inserts. Press-in inserts need to pre-process the corresponding holes in the base material and then press them in; self-tapping inserts can be directly screwed into the base material to form a threaded connection.
4) Classification by special function:
Such as waterproof thread inserts, high temperature resistant thread inserts, etc. These inserts can maintain good performance in special environments and meet specific usage requirements.
2.Structure and materials of brass thread inserts
(1) Structural composition
Brass thread inserts are mainly composed of threaded parts and installation parts. The design of the threaded part meets international standards to ensure compatibility with other threaded parts. This part is responsible for directly participating in the threaded connection and bearing the main mechanical force. The mounting part is used to fix the insert in the substrate, usually by pressing, bonding or welding.
The structural design of the insert needs to take into account its stress conditions and installation convenience in different application scenarios. For example, in a high-stress environment, the insert may require additional support structures to improve its stability.
(2) Material properties
Brass threaded inserts are usually made of brass alloy, which has excellent mechanical properties, wear resistance and corrosion resistance. Brass alloys are mainly composed of copper and zinc. By adjusting the ratio of the two, different mechanical and physical properties can be obtained.
For example, increasing the zinc content can increase the hardness of brass, while increasing the copper content can enhance its corrosion resistance. In addition, brass also has good processing properties and can be made into various complex shapes through turning, milling and other processes. In special application environments, other elements such as lead and tin may also be added to improve its cutting performance or wear resistance.
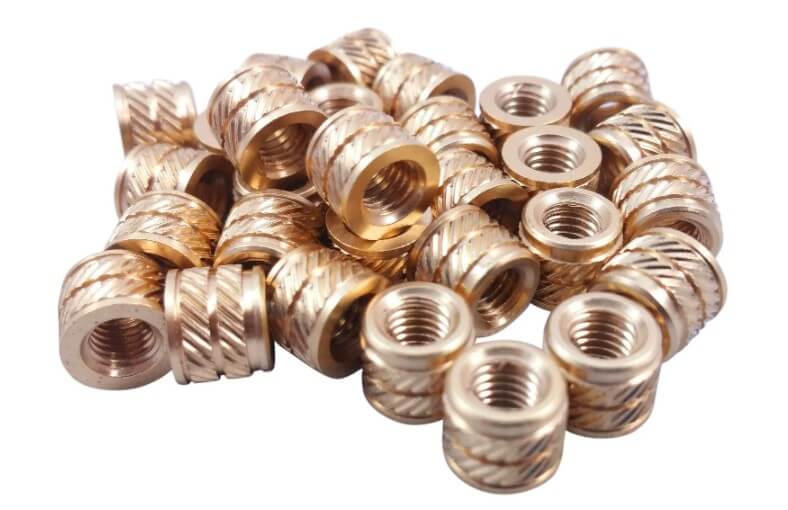
3.Manufacturing process of brass threaded inserts
The manufacturing process of brass threaded inserts mainly includes the following steps:
(1) Cutting
Select appropriate brass bars or plates according to the size requirements of the insert. Use a saw or shear to cut the material and obtain the required size of the blank.
(2) Turning
Clamp the blank on the lathe for rough turning and fine turning. Rough turning is mainly to remove most of the excess, while fine turning is to ensure that the outer diameter, length and end face accuracy of the insert meet the requirements.
Use a forming turning tool or a thread combing tool for thread turning. Forming turning tools are suitable for single-piece small batch production, while thread combing tools are suitable for large-scale production to improve efficiency.
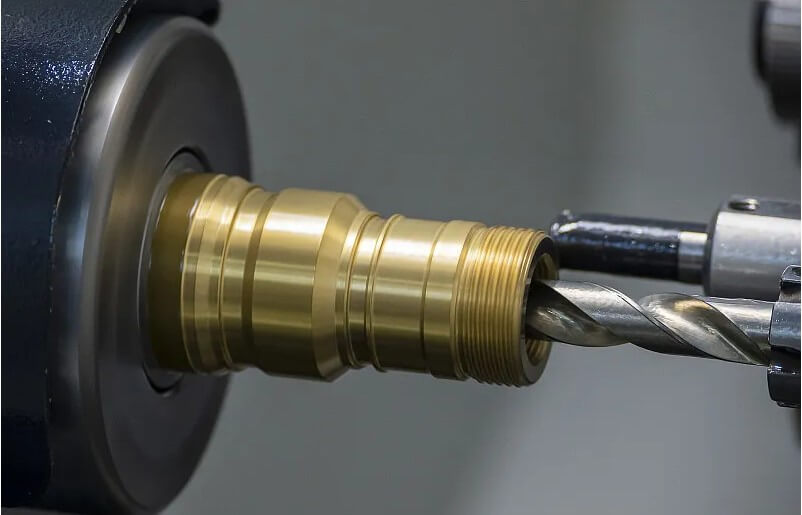
(3) Drilling
Drill the required bottom hole on the insert to prepare for subsequent tapping. Ensure the position and size accuracy of the hole when drilling.
(4) Tapping
Use a tap to process the internal thread in the bottom hole. During the tapping process, the torque and speed must be controlled to ensure the accuracy and quality of the thread.
For small diameter internal threads, tapping is the main processing method.
(5) Grinding (optional)
For threaded inserts with higher precision requirements, grinding can be performed on a thread grinder. Use a single-wire grinding wheel or a multi-wire grinding wheel for grinding to further improve the precision and surface roughness of the thread.
(6) Surface treatment (optional)
If needed, the insert can be surface treated, such as nickel plating, chrome plating, etc., to improve its wear resistance and corrosion resistance.
(7) Inspection
Use measuring tools such as thread gauges and micrometers to inspect the size and thread accuracy of the insert. Ensure that the product meets the design requirements and standards.
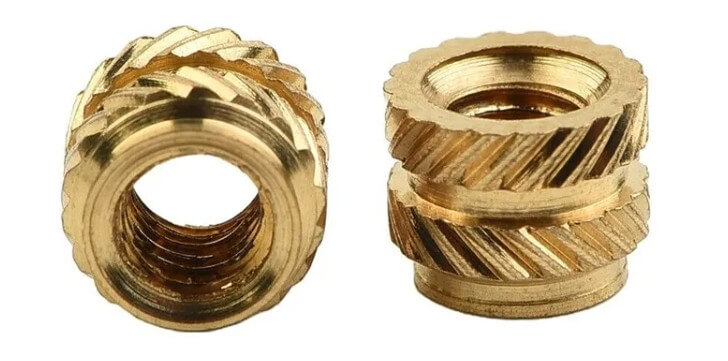
4.Advantages and disadvantages of 3D printed brass threaded inserts
Based on the good thermal conductivity and high tensile strength of brass, 3D printing technology has been used in brass parts processing. So how is the application of 3D printing technology for high-precision parts such as brass threaded inserts?
(1) Advantages
1) High manufacturing flexibility:
3D printing technology can produce on demand, reduce inventory pressure, and can achieve high customization to meet the needs of different application scenarios.
2) Large design freedom:
It can design and manufacture complex structures and geometric shapes that are difficult to achieve with traditional processing technology, thereby improving the functionality of the product.
3) High material utilization rate:
Compared with traditional cutting processing, 3D printing reduces material waste and the utilization rate of brass materials is more efficient.
4) Shortened production cycle:
No complicated mold making is required, which can significantly shorten the production time from design to finished product.
5) Excellent performance:
Brass threaded inserts have excellent mechanical properties, wear resistance and conductivity, and are suitable for a variety of industrial applications.
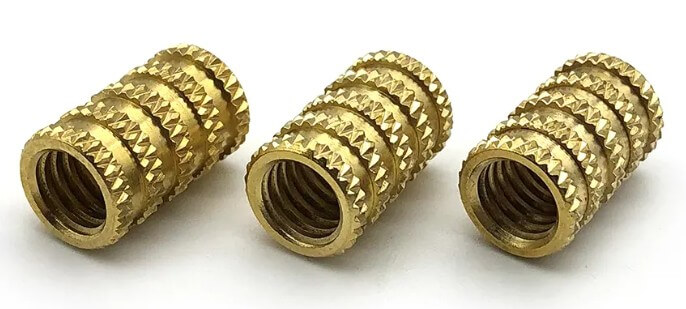
(2) Disadvantages
1) Surface roughness:
The surface of 3D printed brass threaded inserts may have a rough texture, requiring additional post-processing steps to achieve a smooth surface effect.
2) Dimensional accuracy limitation:
Although the accuracy of 3D printing technology continues to improve, there may still be a gap in dimensional accuracy and consistency compared to precision machining.
3) Cost issues:
Although material waste is reduced, the cost of 3D printing equipment and special brass materials may be high, affecting the overall economic benefits.
4) Interlayer bonding problem:
The bonding between layers during the printing process may be insufficient, affecting the overall strength and durability of the insert.
Summary:
Regarding 3D printing, it is currently less used in the production of brass threaded inserts, mainly because 3D printing still has certain limitations in the accuracy and surface quality of metal parts. For parts such as brass threaded inserts that require high precision and good surface quality, traditional turning and cutting methods are still the most common and effective manufacturing processes.
5.Application fields of brass threaded inserts
Due to their excellent performance, brass threaded inserts have been widely used in many fields:
(1) Electronic products:
In electronic products such as mobile phones, computers, and tablets, brass threaded inserts are often used to fix circuit boards, housings and other components to ensure the stability and reliability of the products.
(2) Automobile manufacturing:
In automobile engines, chassis, body and other parts, they are widely used to connect and fasten various parts to meet the high strength and high reliability requirements of automobiles.
(3) Mechanical equipment:
In various mechanical equipment, they are used to connect and fasten key components such as bearings, gears, and shafts to ensure the normal operation and safety of the equipment.
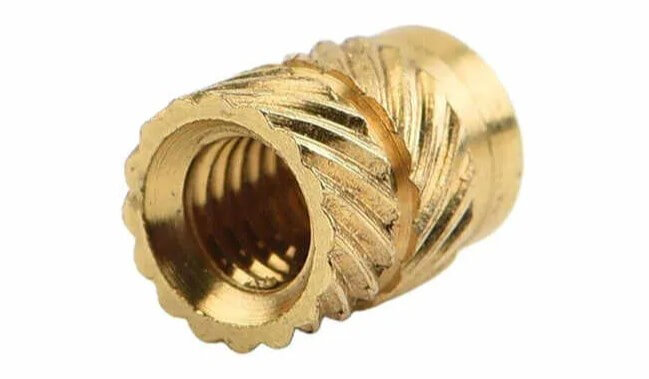
(4) Petroleum industry
Brass threaded inserts are mainly used in key components such as drilling equipment, pipe connectors and valves in the petroleum industry. These inserts ensure the reliability and long life of equipment in extreme environments due to their good corrosion resistance and high strength.
(5) Aerospace:
In the aerospace field, brass threaded inserts are widely used in the manufacture and maintenance of aircraft, satellites and other equipment due to their high strength, corrosion resistance and good conductivity.
(6) Household items:
In furniture manufacturing, they are used to connect plastic and wooden parts to ensure the structural stability and service life of furniture.
6.Advantages and challenges of brass threaded inserts
(1) Advantages
1) Enhanced thread strength:
Brass threaded inserts can significantly improve the thread strength of softer materials such as plastics and aluminum alloys, enabling them to withstand greater torque and tension.
2) Improved connection reliability:
By using brass threaded inserts, problems such as thread loosening and thread slipping can be effectively avoided, thereby improving the reliability and stability of the connection.
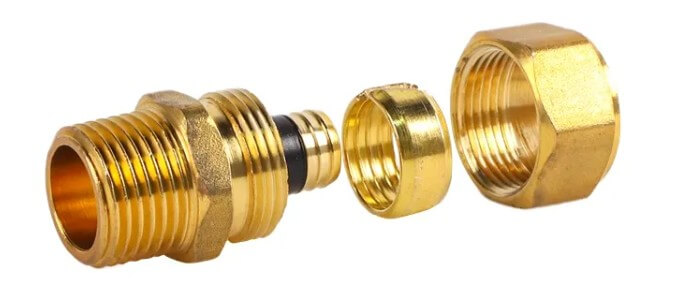
3) Extended service life:
Brass material has good corrosion resistance and wear resistance, which can extend the service life of threaded inserts and reduce the frequency of maintenance and replacement.
4) Wide range of applications:
Brass threaded inserts are suitable for a variety of materials and occasions, with a wide range of applications and flexibility.
(2) Challenges
1) Cost issues:
Compared with some plastic or aluminum alloy fasteners, brass threaded inserts are more expensive, which limits their application scope to a certain extent.
2) High installation requirements:
The installation of brass threaded inserts requires certain technical and equipment support. If improperly installed, it may affect its performance and service life.
7.Summary
In summary, brass threaded inserts have become indispensable fasteners in many industries due to their excellent mechanical properties and wide range of applications. Through continuous technological innovation and improvement, the performance of these inserts is continuously improving to meet more diversified application needs.