Key Technology Essentials of Brass Turned Parts Processing: Creating the Perfect Component
Brass turned parts, as an important part of the precision manufacturing field, have received widespread attention for their unique metallic luster, exquisite processing technology and excellent performance. In this article, we will bring you an in-depth understanding of the process principles, key technologies and wide range of applications of brass turned parts, to feel the charm of the ingenuity of precision manufacturing.
1.The basic characteristics of brass material and its processing influence
Brass is an alloy of two metals, copper and zinc, with a copper content of 60% to 90% and a zinc content of 10% to 40%. Depending on the copper and zinc content, brass can be divided into several types, each with different physical and chemical properties. Brass materials have a variety of excellent properties and are used in a wide range of industries. Its basic properties include:
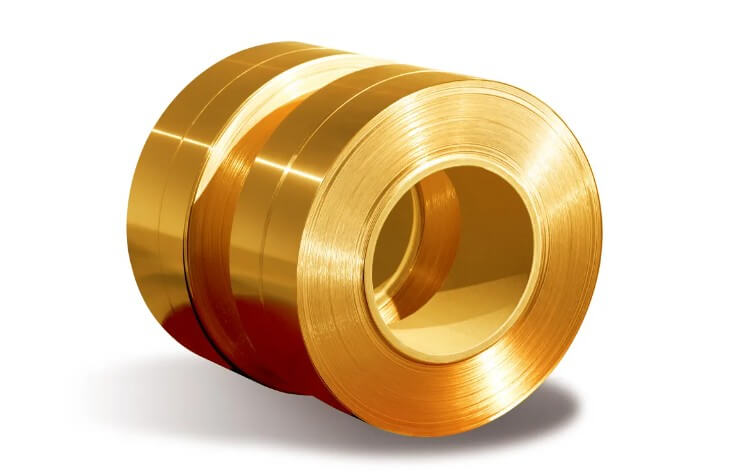
(1) Mechanical properties:
Brass has excellent strength and plasticity, suitable for the manufacture of high-strength parts. Its wear resistance and fatigue resistance ensure long-term stable operation, but may be affected in high temperature and high pressure environment.
(2) Corrosion resistance:
Brass has good corrosion resistance to a variety of acids, alkalis and salt solutions, and is suitable for piping systems in the fields of chemical industry and shipping. However, corrosion may still occur in specific strong oxidizing environments.
(3) Thermal conductivity:
The good thermal conductivity of brass makes it widely used in refrigeration and heating systems, which can effectively transfer heat and improve system efficiency.
(4) Solderability:
Brass is easy to weld and braze, good gas tightness, convenient for piping system connection. However, the soldering process needs to pay attention to temperature control to avoid changes in the performance of the heat-affected zone.
(5) Processing performance:
Brass is easy to form, cut and polish, suitable for manufacturing precision parts. However, work-hardening phenomenon may occur in the machining process, need to soften the material through appropriate annealing treatment.
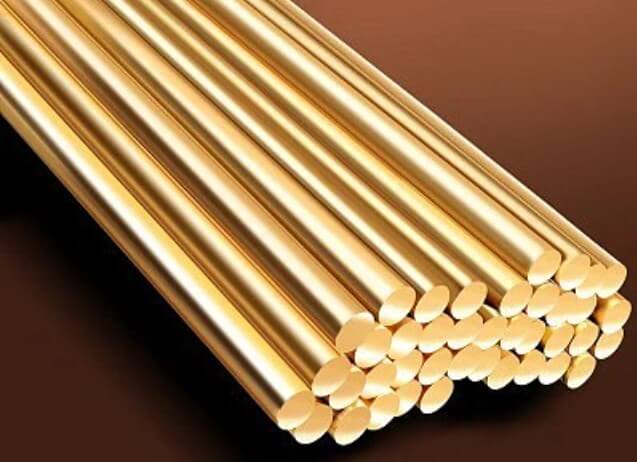
(6) hardness and composition:
The hardness of brass is affected by the ratio of copper to zinc, the higher the zinc content, the lower the hardness. By adjusting the composition and heat treatment process, the hardness of brass can be optimized to meet the needs of different application scenarios.
(7) Electrical conductivity:
High copper content brass (such as H90) has good electrical conductivity, suitable for the electrical and electronic industry, manufacturing cable shields and connectors, etc..
2.The processing principle and common process methods of brass turned parts
Turning is a basic and widely used method in mechanical manufacturing, especially suitable for processing rotary parts. The following are the basic principles and common process methods of brass turned parts processing:
(1) The basic principle of turning processing
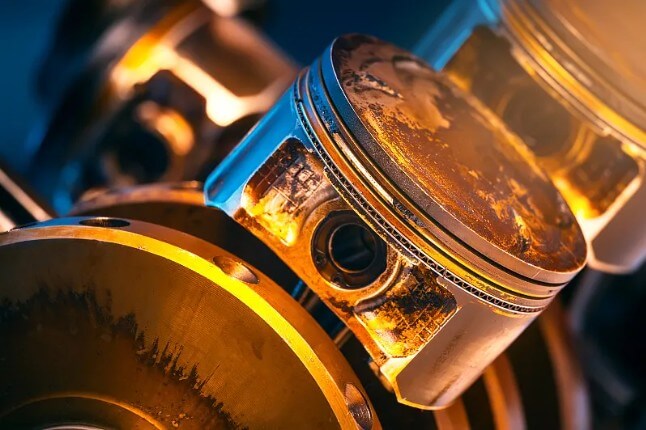
1) Turning process mainly depends on the rotary movement of the workpiece and the linear or curvilinear movement of the tool. Through the cutting tool on the rotating workpiece cutting, so as to change the shape and size of the workpiece, so that it meets the requirements of the design drawings.
2) In turning brass parts, the tool cuts the workpiece with a certain cutting speed, feed and depth of cut. Since brass has good cutting performance, a higher cutting speed can be selected to improve processing efficiency.
(2) Turning processing of the common process methods
1) External turning:
This is the most common process in turning processing, mainly on the outer cylindrical surface of the workpiece for cutting. For brass parts, external turning can efficiently remove excess material and obtain a smooth external surface.
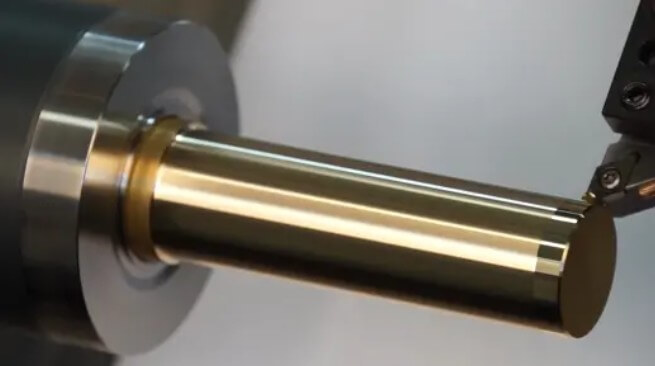
2) Internal turning:
In contrast to external turning, internal turning is the machining of the inner hole of the workpiece. This process requires special attention to tool rigidity and chip removal to ensure the surface quality and machining accuracy of the inner hole.
3) face turning:
End face turning is to process the end face of the workpiece. Through the cutting motion perpendicular to the axis of the workpiece, a flat end face can be obtained, which is suitable for machining the step surface or sealing surface of brass parts.
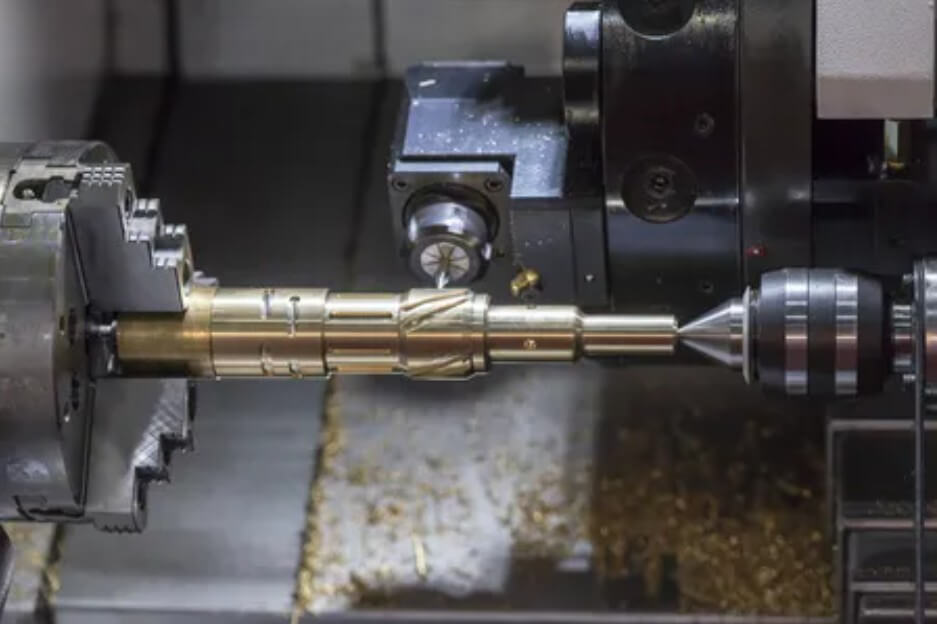
4) groove turning:
Groove turning is a process of cutting grooves on the surface of the workpiece. Grooving on brass parts is often used to make a retreat groove, sealing grooves and other functional structures.
5) Thread turning:
Through special thread turning tools, various specifications of threads can be processed on brass parts. This process requires high machining accuracy and tool stability.
3.The key processing technology of brass turned parts
Brass turned parts are widely used in modern manufacturing industry, and its excellent mechanical properties and beautiful appearance make it become the material of choice for many precision parts and decorative parts. However, there are many challenges associated with brass turning that require key technologies to ensure quality and efficiency. The following are four critical process technologies in the machining of brass turned parts.
(1) Selection and Use of Cutting Fluid
Cutting fluid plays a vital role in the machining of brass turned parts, and its main functions include cooling, lubrication, chip removal and rust prevention. Choosing the right cutting fluid not only improves tool life, but also significantly improves the processing surface quality.
1) Classification of cutting fluids:
•Oil-based cutting fluid: outstanding lubrication effect, good rust prevention, but poor cooling effect, suitable for brass finishing with high lubrication requirements.
•Water-based cutting fluid: good cooling effect, but lubrication and rust resistance is relatively poor, suitable for roughing and high-speed cutting, can quickly take away the cutting heat.
•Synthetic cutting fluid: both good lubrication, cooling and anti-rust performance, suitable for a variety of processing conditions, especially suitable for complex brass turning parts processing.
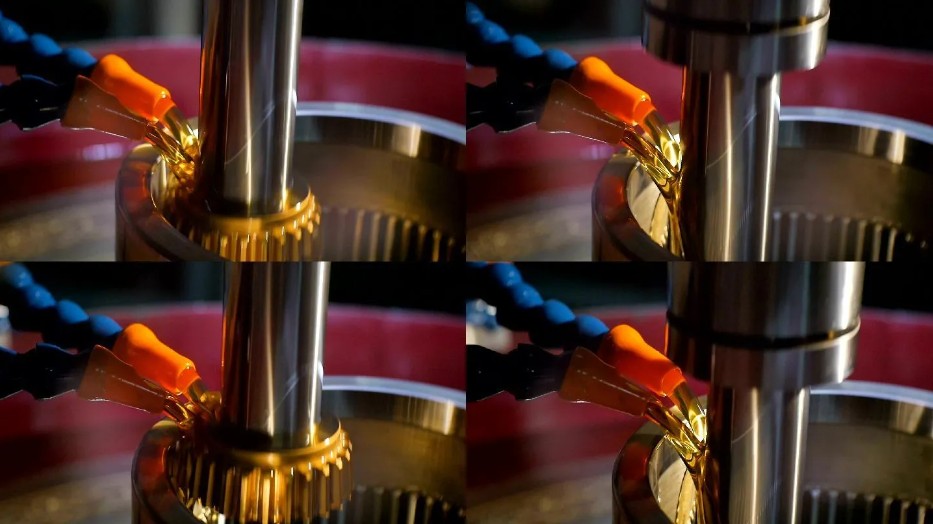
2) The use of cutting fluid function
•Lubrication: reduce the friction between tool and workpiece, reduce cutting force and tool wear, improve the surface finish of workpiece.
•Cooling: take away the heat generated in the cutting process, prevent the tool and workpiece from overheating, prolong the life of the tool and ensure machining accuracy.
•Cleaning: flushing away chips and oil, keeping the tool and workpiece clean, preventing machine tool pollution.
•Anti-rust: form a protective film on the surface of the workpiece to prevent rusting during the cutting process and contact with moisture in the environment.
3) Suggestions for use:
•Select the appropriate type of cutting fluid according to specific machining requirements and machine conditions.
•Check and replace the cutting fluid regularly to keep it clean and stable in performance.
•Reasonable control of cutting fluid flow and pressure to ensure that the cutting area is adequately cooled and lubricated.
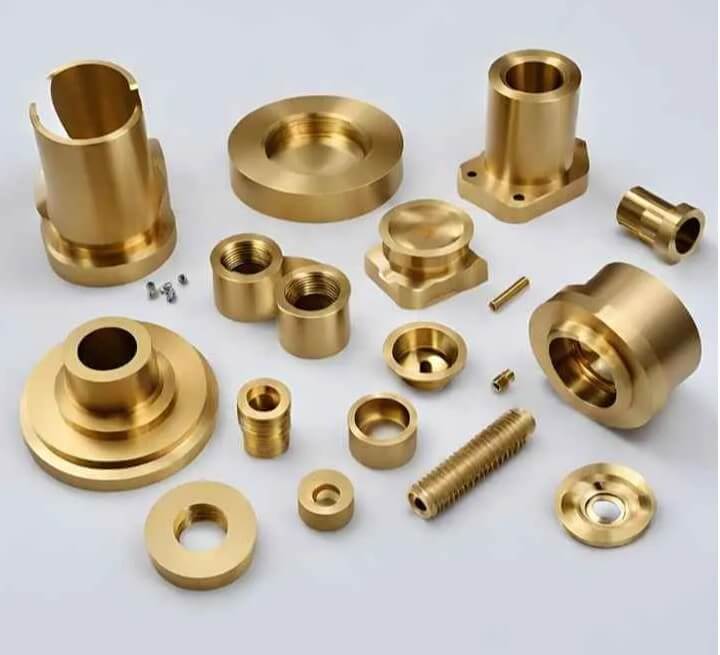
(2) Clamping method and fixture design
Reasonable clamping method and fixture design are the key factors to ensure the machining accuracy and efficiency of brass turned parts. Brass material is soft, easy to produce deformation in the clamping process, so we need to pay special attention to the control of the clamping force and the optimization of the fixture structure.
1) Clamping method:
•Three-point clamping: three-point clamping can provide stable and reliable clamping force, suitable for most of the brass turned parts processing.
•Vacuum clamping: Vacuum clamping fixes the workpiece by adsorption, which can effectively avoid the indentation on the surface of the workpiece, and is suitable for the machining of thin-walled and easily deformed brass turned parts.
•Hydraulic clamping: Hydraulic clamping force is large and uniform, suitable for processing large and complex brass turned parts.
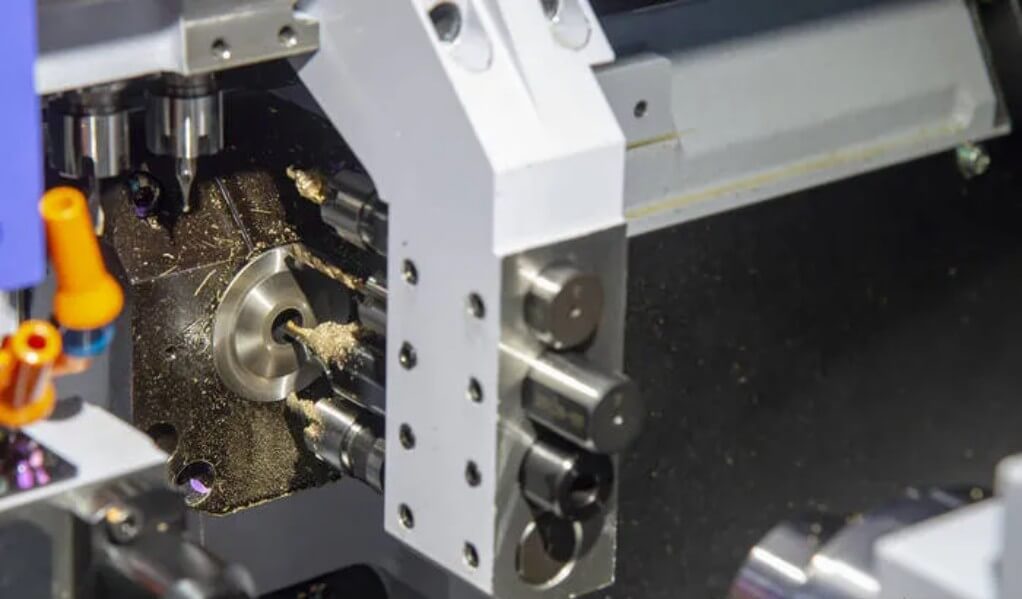
2) Fixture design:
•Positioning accuracy: the positioning elements of the fixture should have high accuracy and stability to ensure the accurate position of the workpiece in the machining process.
•Clamping force distribution: Reasonable design of the location and number of clamping points, so that the clamping force is evenly distributed on the workpiece to reduce deformation.
•Operation convenience: the fixture design should consider the operation convenience, improve the clamping efficiency and reduce the auxiliary time.
3) Design suggestions:
•Customize the design of the fixture according to the shape, size and processing requirements of the workpiece.
•Use finite element analysis and other methods to optimize the design of the fixture to improve its rigidity and stability.
•Check the accuracy and wear of the fixture regularly, and carry out maintenance and replacement in time.
(3) Selection and optimization of cutting parameters
The selection of cutting parameters directly affects the machining efficiency, surface quality and tool life of brass turned parts. Reasonable cutting parameters can improve productivity and reduce processing costs under the premise of ensuring processing quality.
1) Cutting parameters
•Cutting speed: the choice of cutting speed should be based on tool materials, workpiece materials and processing requirements. Higher cutting speed can improve machining efficiency, but it will also increase tool wear.
•Feed: the size of the feed directly affects the surface roughness and cutting force. Smaller feed can obtain better surface quality, but will reduce machining efficiency.
•Backfeed amount: the selection of backfeed amount should be based on the workpiece allowance and machine power comprehensive consideration. A larger amount of back draft can improve machining efficiency, but it will also increase cutting force and tool wear.
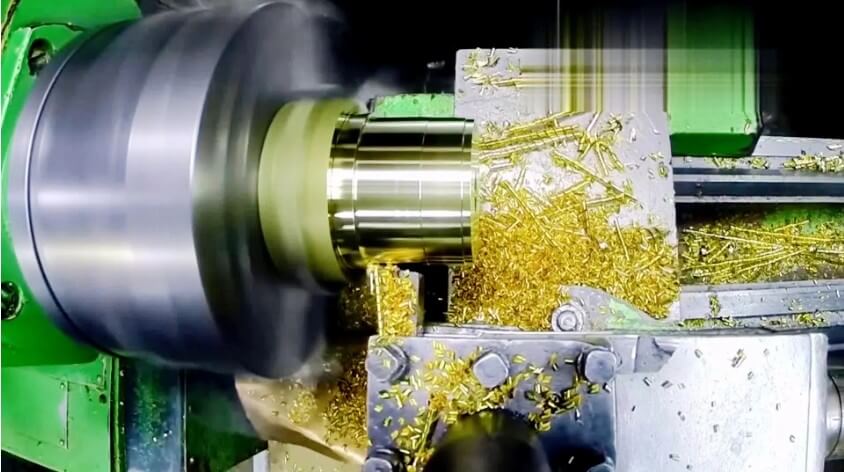
2) Optimization suggestions:
•Test and optimize the cutting parameters according to the specific machining conditions and workpiece requirements.
•Use cutting database and simulation software to predict and optimize cutting parameters.
•Check the tool wear regularly and replace the tool in time to ensure the machining quality.
(4) Tool material and geometric parameters
Tool materials and geometric parameters are important factors that cannot be ignored in brass turning machining. Reasonable tool selection and geometric parameter design can effectively improve machining efficiency and quality and reduce machining costs.
1) Tool material:
•High-speed steel: high-speed steel tools are less expensive and suitable for low-speed and small batch brass turning processing.
•Cemented Carbide: Cemented Carbide tools have high hardness and good wear resistance, suitable for high-speed and high-volume brass turning processing.
•Coated tools: coated tools have high surface hardness, good wear resistance and oxidation resistance, suitable for high precision and high efficiency brass turning.
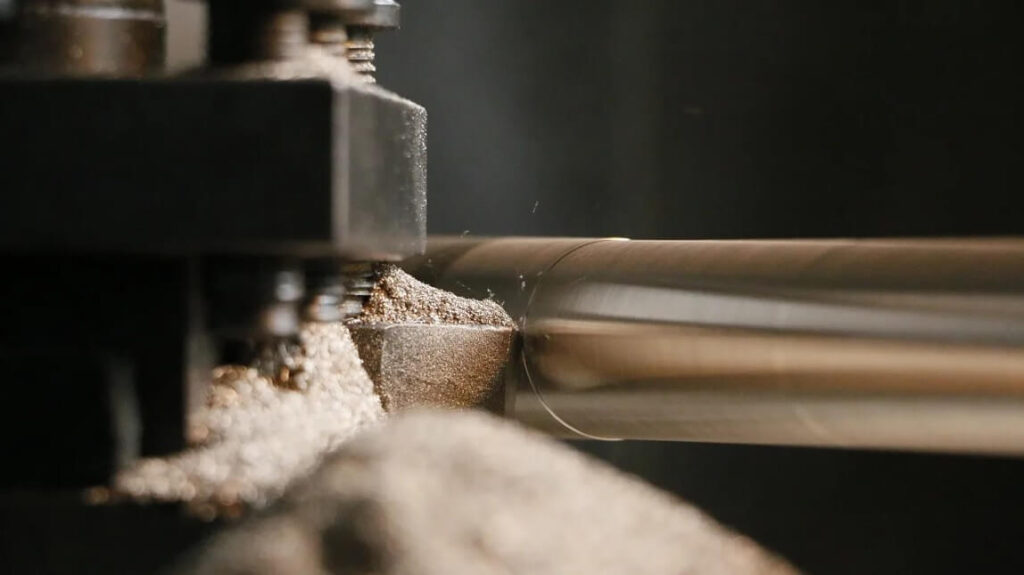
2) Tool geometry parameters:
•Front angle: larger front angle can reduce cutting force and cutting heat, improve tool life, but will reduce tool strength.
•Back angle: a larger back angle can reduce the friction between the tool and the workpiece, improve the machining surface quality, but will reduce the tool strength.
•Camber angle: Reasonable camber angle can control the chip flow direction and avoid the chip scratching the machined surface.
3) Suggestions for selection:
•Select appropriate tool materials and geometric parameters according to specific machining requirements and workpiece materials.
•Regularly check the tool wear and replace the tool in time to ensure the machining quality.
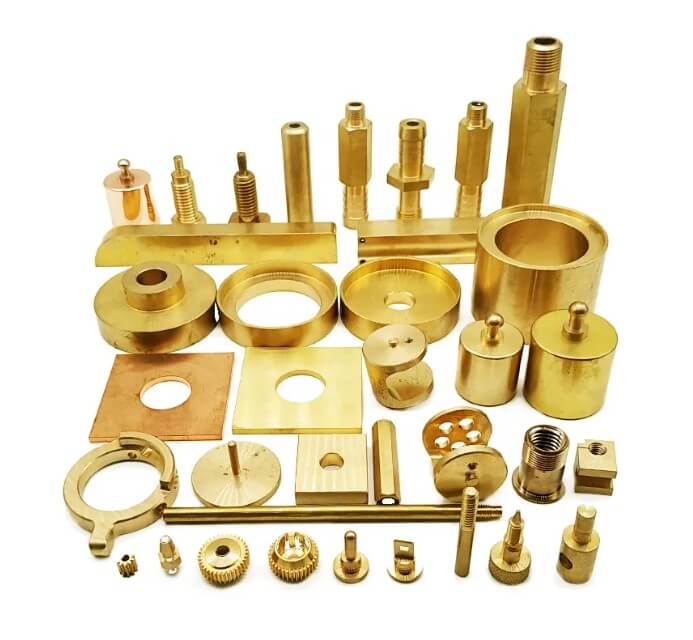
Summary:
The processing of brass turned parts requires comprehensive consideration of a number of factors such as cutting fluid, clamping method, cutting parameters and tool materials, etc. Through the selection and optimization of reasonable process technology, it can effectively improve the processing efficiency and quality, reduce the processing cost, and promote the sustainable development of the manufacturing industry.
4.The specific application of brass turned parts
Because of its excellent mechanical properties, good corrosion resistance and beautiful appearance, brass turned parts have been widely used in many industries. The following are a few specific application areas:
(1) Aerospace industry
Brass turned parts are commonly used in the manufacture of aircraft and spacecraft parts, such as connectors, valves, bearings and so on. Its high strength and good fatigue resistance make it perform well in extreme environments. For example, fuel regulator valves in aircraft engines require brass materials to ensure corrosion resistance and sealing.
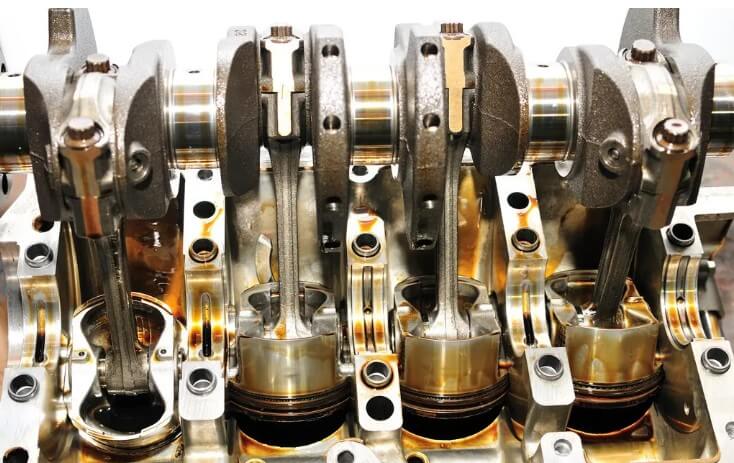
(2) Automobile Manufacturing
In the automotive industry, brass turned parts are widely used in the manufacture of a variety of key components, such as brake system parts, steering system components, fuel system components and so on. The wear resistance and corrosion resistance of brass ensures the stability and safety of these parts in long-term, high-intensity use.
(3) Precision instruments and electronic devices
As brass has excellent conductivity and processing performance, it plays an important role in precision instruments and electronic devices. For example, brass turned parts can be used to manufacture electronic connectors, switch parts, sensor housings and so on. These parts are widely used in communication equipment, medical equipment, laboratory instruments.
(4) Shipbuilding
Ships operate in harsh marine environments and require high corrosion resistance of materials. Brass turned parts are used in the manufacture of marine valves, pipe joints, pump shafts and other components, and its seawater corrosion resistance greatly extends the service life of ship parts.
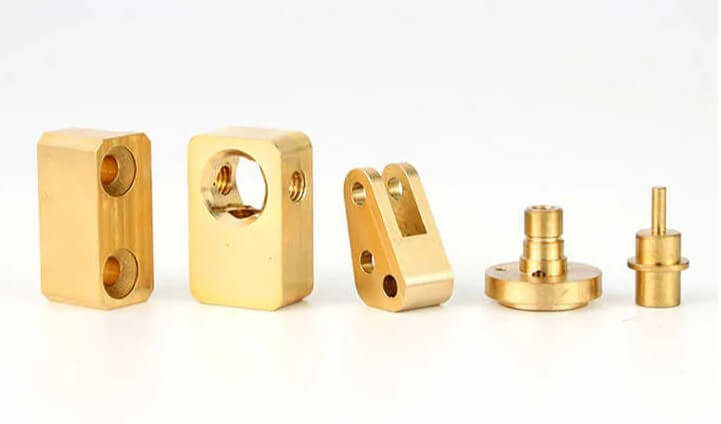
(5) Architectural decoration
Turned brass parts are also commonly used in the field of architectural decoration, such as the production of door handles, locks, lamps, faucets and so on. Its beautiful appearance and good corrosion resistance make it the first choice of high-grade architectural decoration materials. In addition, brass unique metallic luster and sense of history, also gives the building a unique cultural atmosphere.
(6) Machinery Manufacturing
In all kinds of mechanical equipment manufacturing, brass turned parts are used to make gears, bushings, bolts and other key parts. Its good mechanical properties and wear resistance ensure the efficient operation and long life of mechanical equipment.
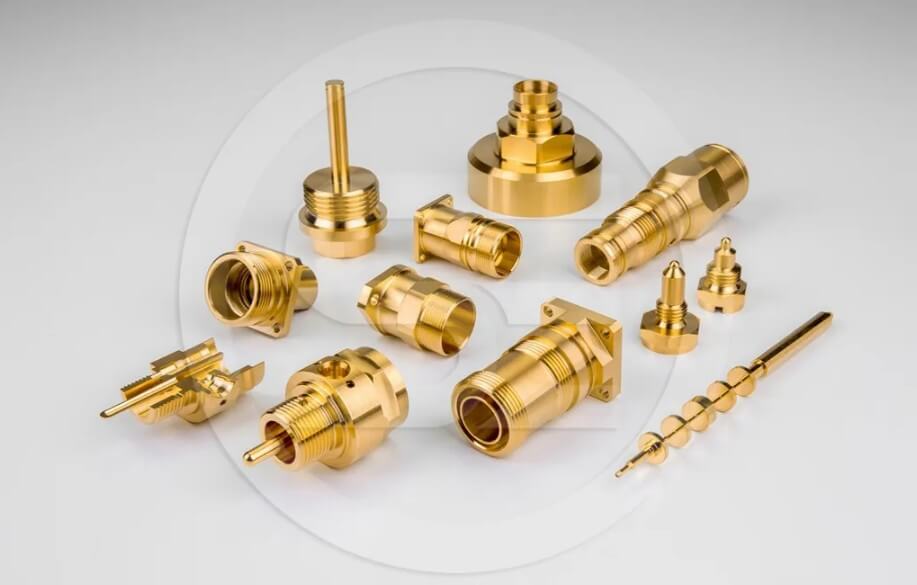
5.Summary
To summarize, through the precision turning process, brass turned parts not only have excellent mechanical properties, but also show a beautiful appearance. In the modern manufacturing industry, the application of brass turned parts is more and more extensive, and its unique advantages are also increasingly prominent. Understanding and mastering the key technology of brass turned parts processing plays an important role in enhancing the competitiveness of enterprises.