Brittle failure aluminum: a safety risk that cannot be ignored in the manufacturing industry
Among the many materials in the manufacturing industry, aluminum occupies an important position with its unique advantages.
However, the problem of brittle failure aluminum always threatens the safety of manufacturing. Brittle failure aluminum will not only lead to a decline in product performance, but may also cause serious safety accidents and cause huge losses to the manufacturing industry. This article will focus on the impact of brittle failure aluminum on the safety of the manufacturing industry, analyze the causes of its occurrence, and propose corresponding avoidance methods.
1.Basic characteristics of aluminum: physical and chemical properties
Aluminum is a silvery white and shiny metal with low density and good electrical and thermal conductivity. The density of aluminum is about 2.7 g/cm³, the melting point is about 660°C, and the boiling point is about 2467°C. Its atomic number in the periodic table is 13 and its atomic weight is 26.98. The chemical properties of aluminum are relatively stable. It usually appears in the +3 oxidation state in compounds. It has amphoteric characteristics and can react with acids and bases.
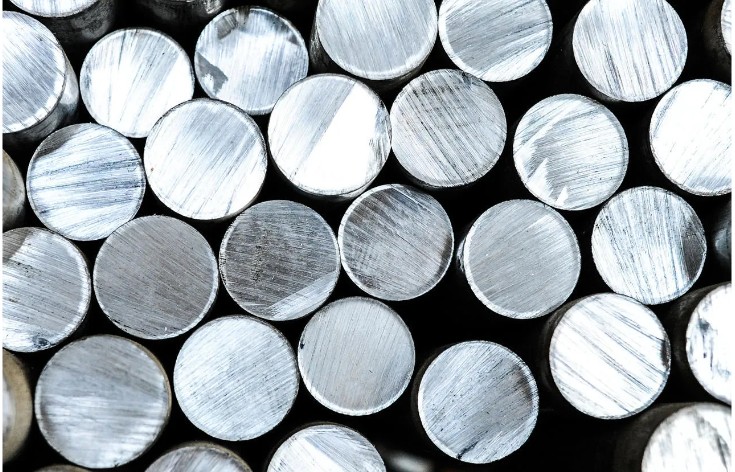
A dense oxide film is easily formed on the surface of aluminum, which makes aluminum have good corrosion resistance in the air. However, this oxide film loses its protective effect when encountering destructive media such as chloride ions, making aluminum susceptible to corrosion in environments such as seawater. In addition, aluminum can react with non-metals at high temperatures and dissolve in acids or alkalis, but has no significant reaction with water, sulfides, concentrated sulfuric acid, and organic acids.
2.Definition and impact of brittleness
(1) Concept of brittleness
In materials science, brittleness refers to the property of a material to suddenly break without obvious deformation when subjected to external forces. Brittle materials usually have no or very little plastic deformation capacity, and their fracture mode is characterized by rapid crack propagation and sudden fracture. This property is particularly important in engineering applications because brittle fracture is often difficult to predict and may lead to serious safety accidents.
Brittle fracture is different from ductile fracture. Ductile fracture is usually accompanied by large plastic deformation and energy absorption, while brittle fracture is a rapid and energy-releasing process. Therefore, understanding and controlling the brittleness of materials is key to ensuring manufacturing safety and reliability.
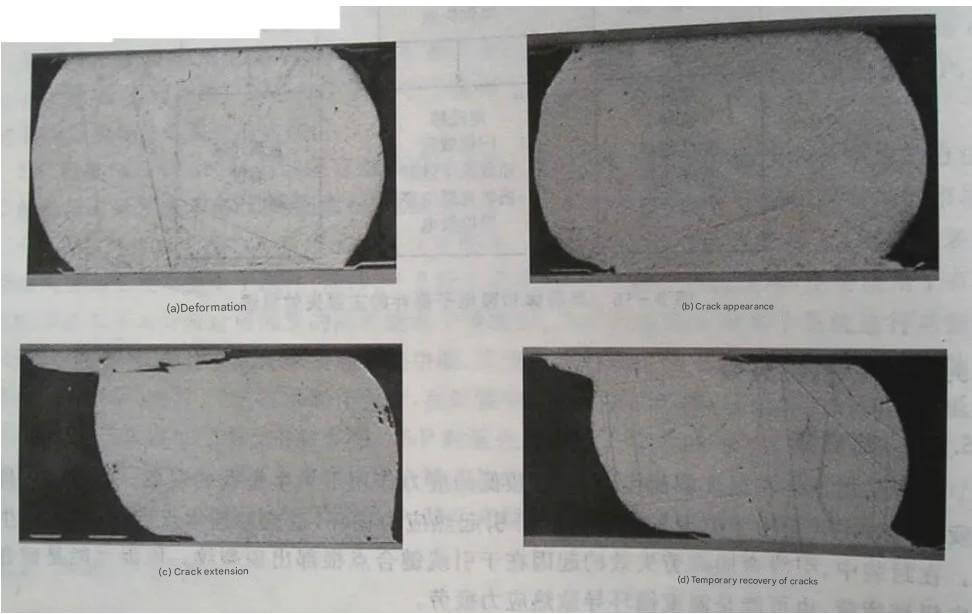
The phenomenon of aluminum slowly undergoing plastic deformation during welding
(2) Factors affecting brittle failure aluminum
The brittleness of aluminum is affected by many factors, including alloy composition, processing technology, use environment and internal defects. For example, certain alloying elements added to aluminum, such as copper, magnesium and zinc, can improve its strength, but may increase its brittleness. Processing technology, such as cold working and heat treatment, also has a significant effect on the brittleness of aluminum. Improper heat treatment may cause stress concentration and microstructural changes inside aluminum, thereby increasing its risk of brittle fracture.
In addition, the temperature and medium characteristics of the use environment will also affect the brittleness of aluminum. For example, aluminum may show higher brittleness in low temperature environments, while in corrosive media, the destruction of the surface oxide film may lead to increased brittleness of aluminum. Internal defects, such as impurities, pores and cracks, are important factors in the brittleness of aluminum. These defects may become the source of stress concentration, promoting the formation and expansion of cracks.
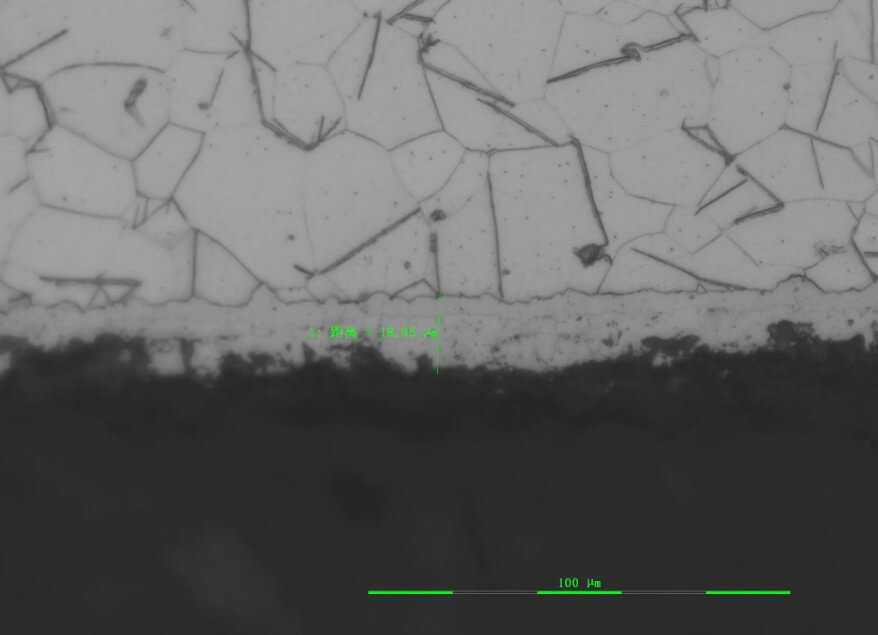
3.Brittleness of aluminum alloys
(1) Classification of aluminum alloys
Aluminum alloys are mainly divided into two categories: cast aluminum alloys and deformed aluminum alloys. Cast aluminum alloys are usually used in the cast state and are suitable for the manufacture of parts with complex shapes. Deformed aluminum alloys can be processed into various forms such as plates, bars and tubes through pressure, and have better mechanical properties and higher strength.
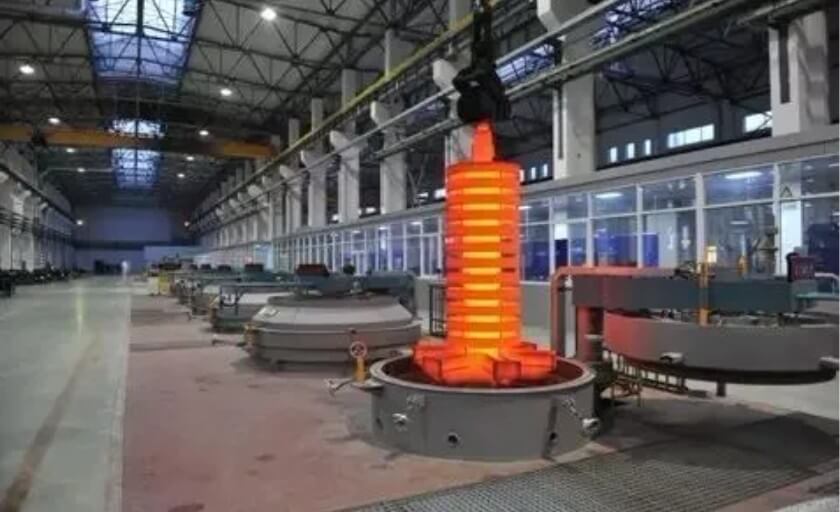
Deformed aluminum alloys can be further divided into non-heat-treatable and heat-treatable types. Non-heat-treatable aluminum alloys are mainly strengthened by cold working deformation, mainly including high-purity aluminum, industrial pure aluminum and rust-proof aluminum. Heat-treatable aluminum alloys can improve their mechanical properties through heat treatment methods such as quenching and aging, such as hard aluminum, forged aluminum, super-hard aluminum and special aluminum alloys.
(2) Brittleness of common aluminum alloys
Different types of aluminum alloys exhibit different brittle characteristics. For example, 7075 aluminum alloy is widely used in aviation and military industries due to its high strength and good mechanical properties, but its brittleness problem is also prominent, especially in high or low temperature environments. Although the strength of 2024 aluminum alloy is slightly lower, its crack propagation resistance is better and it is suitable for application scenarios requiring higher toughness.
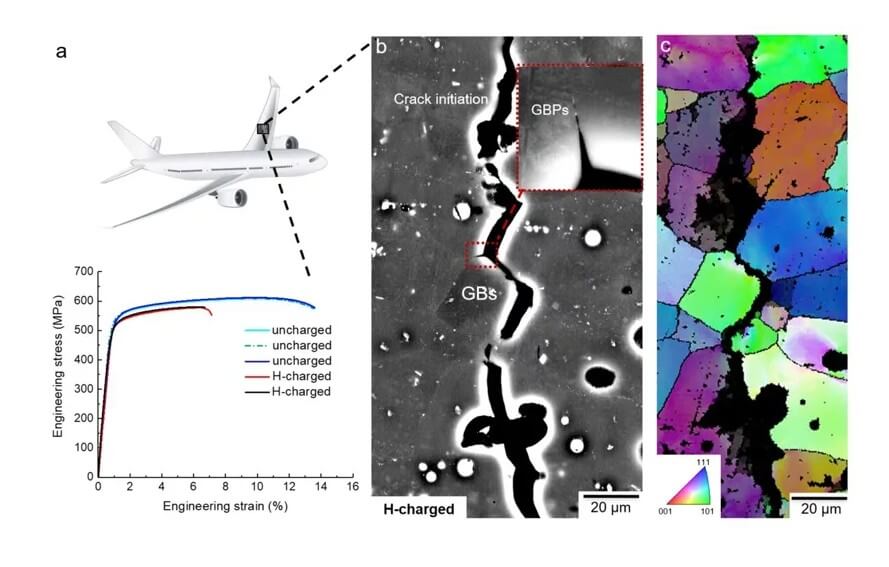
In addition, research has shown that the brittleness of aluminum alloys is not only related to the alloy composition, but also closely related to the heat treatment process and processing technology. For example, quenching and aging treatment can significantly improve the strength of aluminum alloys, but at the same time, it may also increase the risk of brittle failure aluminum. Therefore, in practical applications, it is necessary to comprehensively consider the strength and brittleness of aluminum alloys and select appropriate heat treatment and processing technology to ensure its safety and reliability in the use environment.
4.Mechanism of brittle failure aluminum
(1) Types of brittle fracture
Brittle fracture mainly includes two types: cleavage fracture and intergranular fracture. Cleavage fracture refers to the extension of cracks along a specific crystal plane, resulting in material fracture. This type of fracture usually occurs in materials with a highly ordered crystal structure, with a smooth fracture surface and obvious cleavage steps. Intergranular fracture refers to the extension of cracks along grain boundaries, resulting in material fracture. This type of fracture is usually related to the weakening of grain boundaries, such as impurity segregation, the formation of precipitation phases, etc.
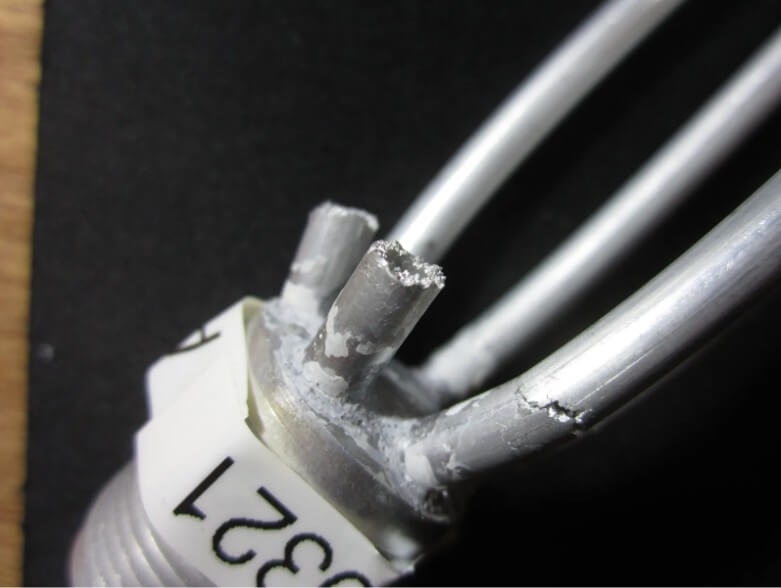
(2) The process of brittle failure aluminum
Brittle failure usually starts from defects or stress concentration points inside the material, such as impurities, precipitation phases, grain boundaries, etc. When external force acts on the material, these defects or stress concentration points will first produce cracks. As the external force increases, the cracks gradually expand and eventually lead to the sudden fracture of the material. This process is usually very rapid, and the material has almost no time for plastic deformation, so brittle fracture is a very dangerous failure mode.
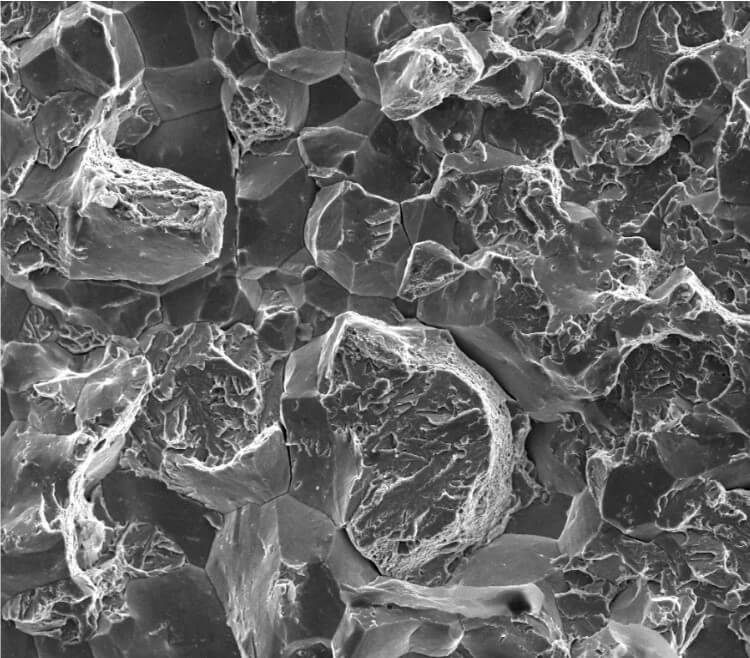
Microscopic view of aluminum fracture
Studying the mechanism of brittle failure aluminum is of great significance for preventing and controlling brittle fracture of aluminum. By improving the microstructure of the material, reducing internal defects, optimizing the processing technology and use conditions, the material’s ability to resist brittle fracture can be effectively improved. For example, in aluminum alloys, by controlling the alloy composition and heat treatment process, the precipitation of brittle phases can be reduced, the grain structure can be optimized, and the toughness and brittle fracture resistance of the material can be improved.
5.Methods to avoid brittle failure aluminum
(1) Material selection and optimization
Selecting the right aluminum alloy material is the first step to avoid brittle failure aluminum. For example, for applications that require high strength and high toughness, 2024 or 7075 aluminum alloys can be selected, but attention should be paid to their heat treatment status and processing technology to avoid increasing brittleness. In addition, by adding trace amounts of rare elements, such as scandium and zirconium, the grain size can be refined, and the toughness and brittle fracture resistance of aluminum alloys can be improved.
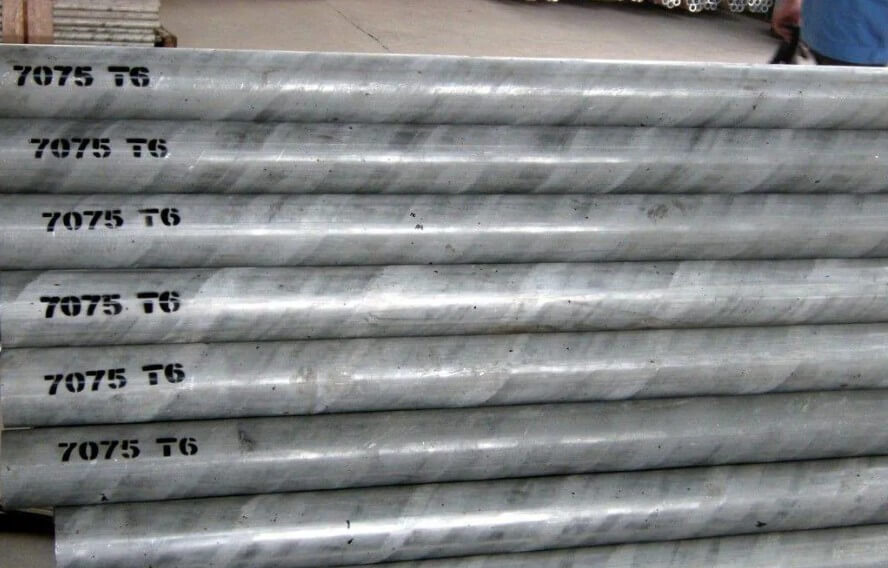
The selection of materials should not only consider their mechanical properties and brittle performance, but also their stability and corrosion resistance in the use environment. For example, in the marine environment, the surface oxide film of aluminum is easily damaged by chloride ions, resulting in corrosion and increasing the possibility of brittle damage to aluminum. Therefore, in this environment, aluminum alloy materials with good corrosion resistance should be selected, and appropriate protective measures should be taken, such as coating anti-corrosion layers and regular maintenance.
(2) Improve processing technology
Optimizing heat treatment and processing technology can effectively reduce the brittleness of aluminum alloys. For example, by controlling the cooling rate, the generation of internal stress and the precipitation of brittle phases can be avoided. In addition, the use of homogenization and aging treatment can improve the microstructure of aluminum alloys and improve their comprehensive performance.
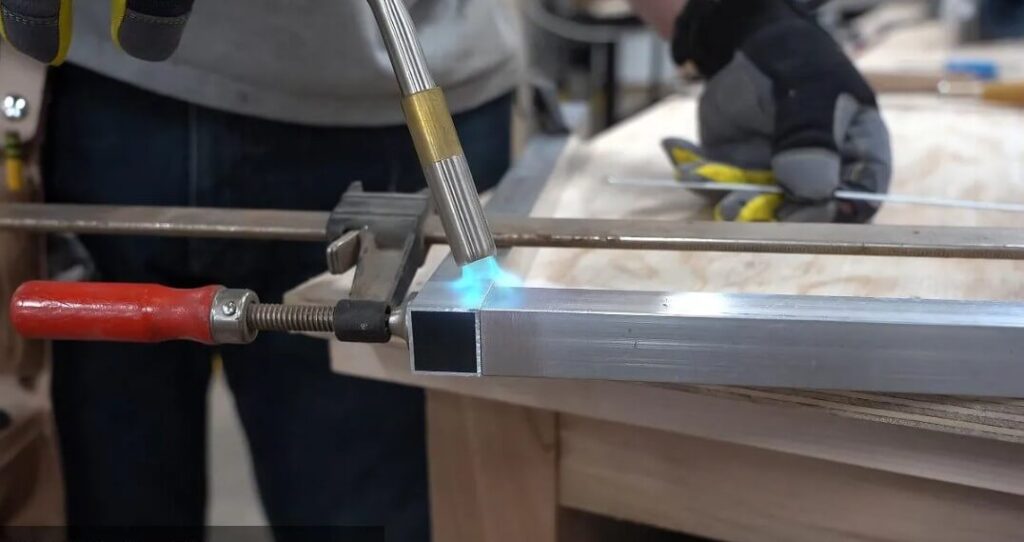
During the processing, attention should also be paid to controlling process parameters such as temperature, pressure, time, etc. to avoid unnecessary stress and defects. For example, during welding, appropriate welding parameters and welding materials should be selected to reduce the brittleness and defects of the welded joint. During cold working, the deformation amount and deformation speed should be controlled to avoid excessive stress and cracks inside the material.
6.Conclusion
The key factors for brittle failure aluminum include alloy composition, processing technology, use environment and internal defects. By rationally selecting materials, optimizing processing technology and controlling use conditions, the ability of aluminum to resist brittle fracture can be effectively improved to ensure the safety and reliability of engineering structures.