Advantages of Aluminum Prototype Parts in Product Development
Aluminum prototype parts have become increasingly popular in product development due to their numerous advantages. These parts offer a range of benefits that make them an ideal choice for creating prototypes before moving on to full-scale production. In this article, we will explore the advantages of using aluminum prototype parts and discuss the best way to build them.
One of the key advantages of aluminum prototype parts is their lightweight nature. Aluminum is a lightweight metal, making it an excellent choice for applications where weight reduction is crucial. This is particularly important in industries such as aerospace and automotive, where every ounce saved can have a significant impact on performance and fuel efficiency. By using aluminum prototype parts, designers can accurately assess the weight and balance of their products, ensuring optimal performance in the final production stage.
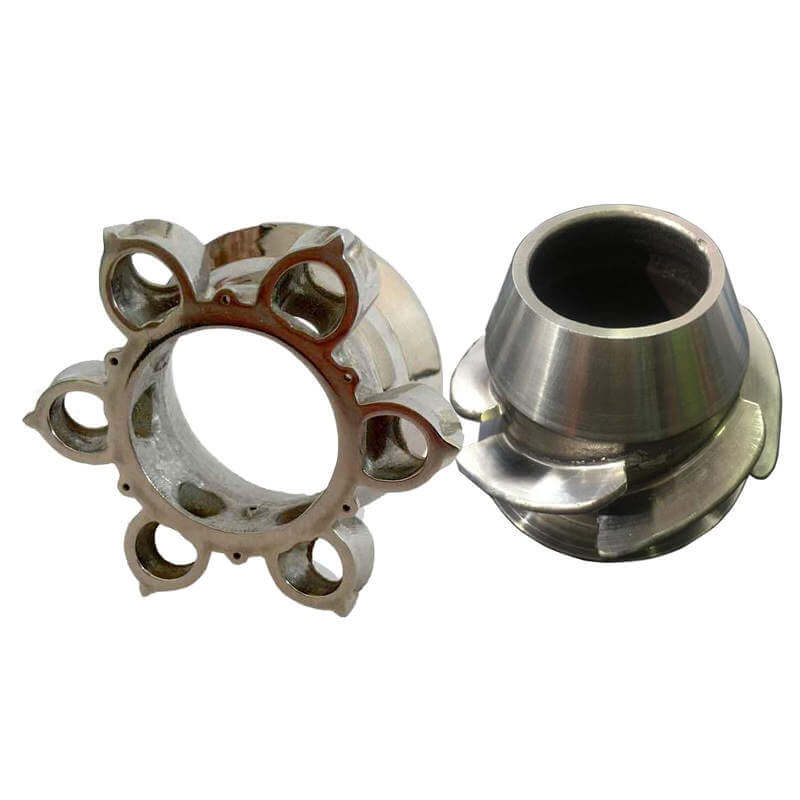
Another advantage of aluminum prototype parts is their high strength-to-weight ratio. Although aluminum is lightweight, it is a strong and durable material. This makes it suitable for a wide range of applications from consumer electronics to industrial machinery. And, by using aluminum prototype parts, engineers can test the structural integrity of their designs and identify any potential weaknesses before proceeding to full production. Not only does this help minimize the risk of costly errors, it also ensures that the final product meets the required strength and durability standards.
In addition to its lightweight and high strength-to-weight ratio, aluminum also offers excellent corrosion resistance. This is particularly important in industries where products are exposed to harsh environments or corrosive substances. By using aluminum prototype parts, designers can assess the material’s resistance to corrosion and make any necessary adjustments to ensure the longevity of the final product. This is especially beneficial in industries such as marine and offshore, where products are constantly exposed to saltwater and other corrosive elements.
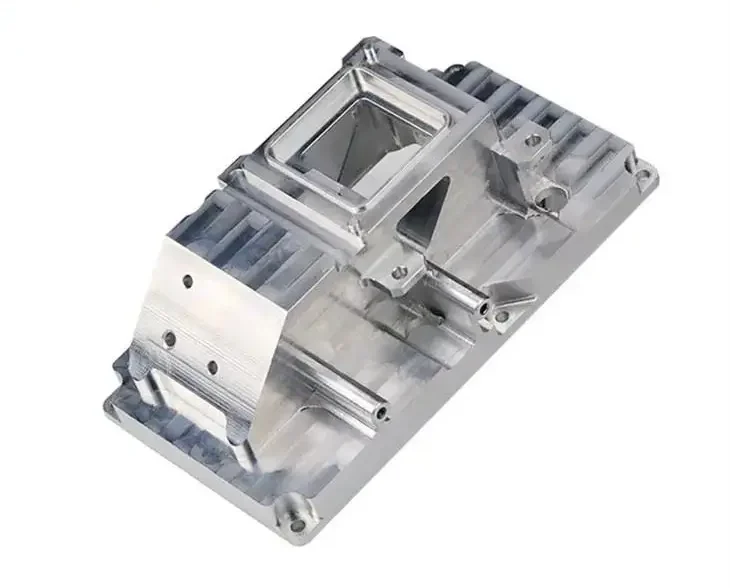
Furthermore, aluminum prototype parts are highly machinable. Aluminum is a relatively soft metal, making it easy to machine and shape into complex forms. This allows designers to create intricate prototypes that accurately represent the final product. By using aluminum prototype parts, engineers can test the functionality and fit of their designs, ensuring that all components work together seamlessly. This helps to identify any potential issues early on and allows for necessary modifications to be made before moving on to full-scale production.
When it comes to building aluminum prototype parts, the best way is to utilize advanced manufacturing technologies such as CNC machining. CNC machining offers a high level of precision and repeatability, allowing for the creation of complex aluminum parts with tight tolerances. This ensures that the prototypes accurately represent the final product and allows for thorough testing and evaluation. Additionally, CNC machining offers a fast turnaround time, allowing designers to quickly iterate and refine their designs.
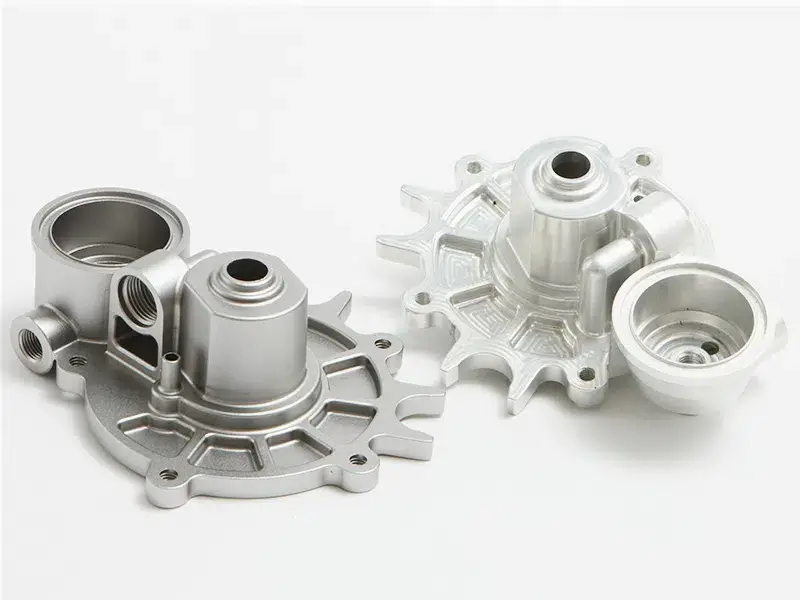
In conclusion, aluminum prototype parts offer numerous advantages in product development. Their lightweight nature, high strength-to-weight ratio, corrosion resistance, and machinability make them an ideal choice for creating prototypes. By utilizing advanced manufacturing technologies such as CNC machining, designers can build accurate and functional aluminum prototype parts that help to minimize risks and ensure the success of the final product.