Understanding the Causes of Burrs in CNC Machining
CNC machining is a widely used manufacturing process that involves the use of computer-controlled machines to shape and cut a variety of materials. While CNC machining offers many advantages, a common problem faced by manufacturers is the formation of burrs.
Burrs are unwanted raised edges or rough surfaces produced during the machining process. They can negatively impact the quality and functionality of the final product. Therefore, it is critical to understand the causes of burrs in CNC machining and how to minimize them.
1.Main causes of burrs in CNC machining
1) Cutting tools
One of the main causes of burrs in CNC machining is the cutting tool itself. The geometry of the tool, such as the rake and relief angles, can significantly affect the formation of burrs. Blunt or improperly ground tools can also cause burr formation.
In addition, the cutting speed and feed rate used in the machining process can also affect the severity of the burr. Higher cutting speeds and feed rates tend to produce more severe burrs.

2) Machining materials
Another factor that contributes to burr formation is the machining material. Since different materials have different machinability, this affects the formation of burrs. For example, highly ductile materials like aluminum are more susceptible to burr formation than hard materials like steel. At the same time, the presence of impurities or contaminants in the material can also increase the likelihood of burr formation.
3) Part Design
The design of the part being machined can also have an impact on burr formation. For example, sharp corners, thin walls, and complex geometries can present challenges to the machining process and lead to burr formation.
In addition, the orientation of the part relative to the cutting tool can also affect burr formation, as improper fixation or clamping can cause vibration or deflection, which can create burrs.
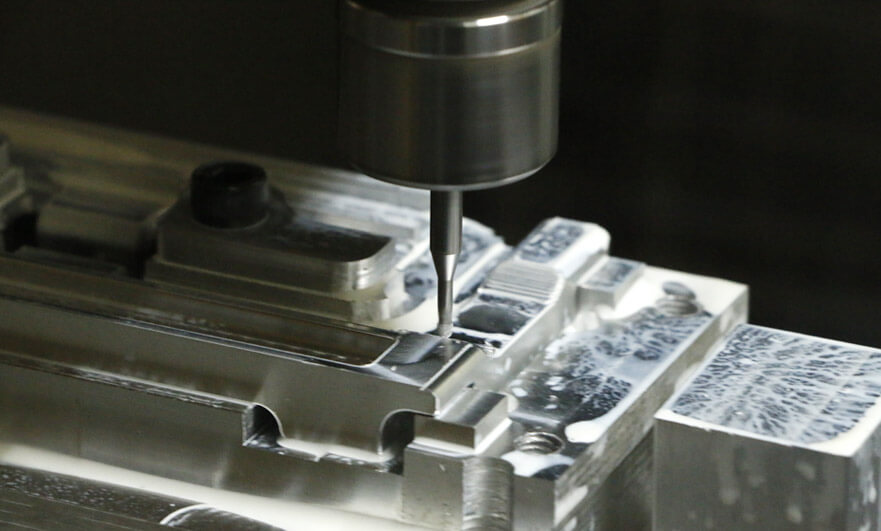
2.Countermeasures for Burr Generation in CNC Machining
To minimize burrs in CNC machining applications, a variety of strategies can be used.
1) Selecting the Right Cutting Tool
Tools with the correct geometry and sharpness can help reduce burr formation. Regular tool maintenance, such as sharpening or replacing dull tools, is also essential.
2) Controlling Cutting Parameters
Controlling cutting parameters is another effective way to reduce burrs. Adjusting cutting speeds and feed rates can help find the best balance between material removal and burr formation. It is important to conduct thorough testing and experimentation to determine the ideal cutting parameters for each specific material and part design.
3) Material Selection
Proper material selection is also critical to reducing burrs. Selecting materials with higher hardness or lower ductility can help reduce the likelihood of burr formation. Ensuring that the material is free of impurities or contaminants can also help reduce burrs.
4) Optimizing Part Design
In addition, optimizing part design can help reduce burrs. Avoiding sharp corners or thin walls can reduce the chances of burr formation. If sharp corners are required, adding radius or chamfers can help relieve stress concentrations that cause burrs.
In addition, carefully considering part orientation and implementing proper fixture techniques can help minimize vibration and deflection, thereby reducing burrs.
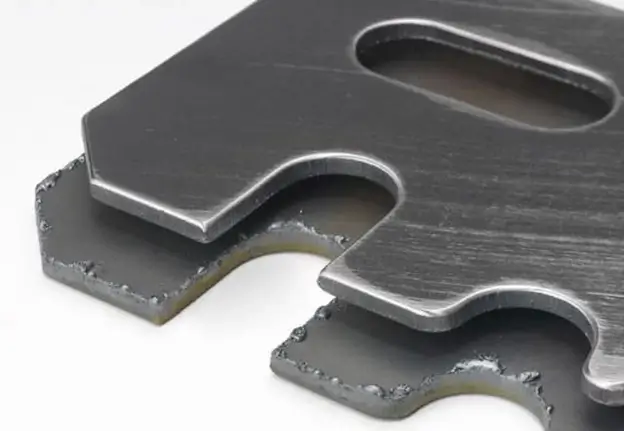
In summary, burrs are a common problem in CNC machining applications that can negatively impact the quality and functionality of the final product. Understanding the causes of burrs, such as tool geometry, material properties, and part design, is critical to minimizing burr formation.
By selecting the right cutting tool, controlling cutting parameters, selecting the right material, and optimizing part design, manufacturers can effectively minimize burrs and improve the overall quality of CNC machined parts.