Carbon Steel vs. Alloy Steel: A Comprehensive Comparison
In the field of machining, choosing the right steel is crucial to ensure the quality and performance of the product. Carbon steel and alloy steel, as two common types of steel, show different characteristics in terms of durability, resistance, etc. A deep understanding of the differences between carbon steel and alloy steel will help you make a wise material choice. This article will comprehensively compare the performance of carbon steel and alloy steel in terms of durability, corrosion and heat resistance, environmental resistance, and processing performance.
Differences Between Carbon Steel and Alloy Steel
When evaluating materials for a specific application, especially in demanding environments, two properties play a key role: durability and resistance. Steel in its various forms is often selected for these qualities. Let’s take a closer look at how these two types of steel perform in terms of durability and resistance.
1.Durability
①Carbon steel’s durability
A lot depends on its carbon content, which can be as low as 0.04% and as high as 2.5%.
1.Mild steel: This type is often called low carbon steel. It is relatively soft and can be easily formed. However, this softness means that it will wear or deform more quickly under high stress.
2.Medium carbon steel: The carbon content is well balanced compared to mild steel, providing higher strength and hardness. This balance gives it good durability, especially against wear.
3.High carbon steel: This is the hardest of the carbon steels, making it extremely wear-resistant. However, its hardness makes it more brittle, meaning it can easily break under extreme pressure or sudden impact.
②Alloy steel’s durability
Is the result of a combination of various metals mixed with a base iron and carbon. Elements such as manganese, chromium, and nickel can be added to enhance specific properties.
1.Wear resistance: Some alloy steels are formulated to provide superior wear resistance. For example, when chromium is added, a protective layer forms on the steel’s surface, which greatly reduces wear.
2.Impact resistance: Nickel and manganese can increase the toughness of steel. This means that the steel can absorb more energy during an impact without breaking, making it ideal for environments where sudden stress is a concern.
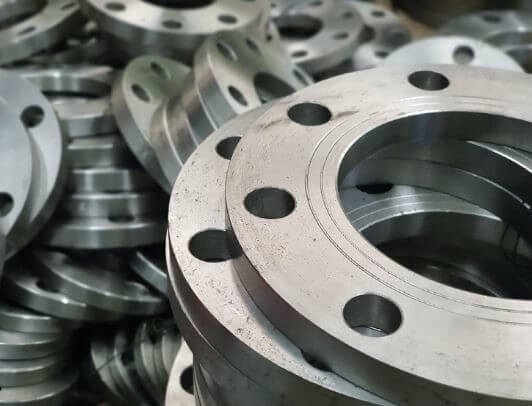
2.Corrosion and heat resistance
①Corrosion resistance of carbon steel
On its own, carbon steel is not particularly corrosion resistant. Exposure to moisture or chemicals can cause rust. However, protective coatings or treatments, such as galvanizing or painting, can prevent corrosion.
②Corrosion resistance of alloy steels
Alloy steels shine in this department. Adding metals such as chromium, nickel, or copper can significantly enhance their resistance to oxidation and corrosion. For example, stainless steel contains a lot of chromium and is particularly resistant to rust and staining.
③Heat resistance of carbon steel
It can withstand daily temperature fluctuations, but it is not designed for high temperature applications. Prolonged exposure to high temperatures will impair its performance and shorten its overall lifespan.
④Heat Resistance of Alloy Steels
Alloy steels once again take the lead. Specific alloying elements, such as molybdenum, tungsten, and vanadium, can significantly enhance the heat resistance of steels. This makes certain alloy steels well suited for industries such as energy production where components are often subjected to high temperatures.
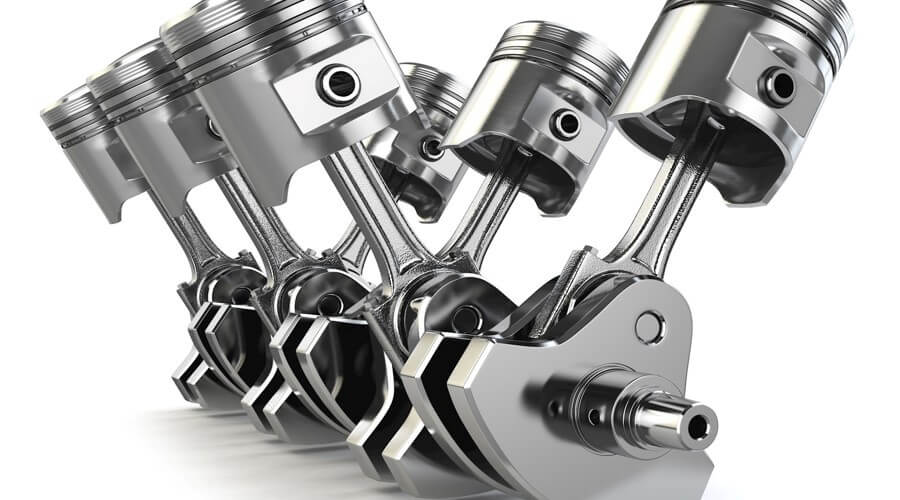
3.Environmental Resistance
In addition to corrosion and heat resistance, resistance to environmental factors is also critical. For example, steels used in marine environments need to be resistant to salt water, which can be corrosive. Here, stainless steels or specially formulated alloy steels are chosen for their ability to withstand the attack of salt water.
4.Comparison of processing performance of carbon steel and alloy steel
The machinability of carbon steels generally decreases as their carbon content increases. However, with the right tools and techniques, even high-carbon steels can be machined effectively.
In contrast, the machinability of alloy steels is largely affected by the specific alloying elements they contain. Some elements can enhance machinability, while others may reduce it. For example:
1.Sulfur: Often added to improve machinability.
2.Nickel, chromium, molybdenum: These reduce the machinability of steels.