Carburizing, Nitriding and Carbonitriding: A Comprehensive Comparison Guide
In modern industry, metal surface treatment technology is crucial to improving the performance of parts. Carburizing, nitriding and carbonitriding are common surface hardening processes and are widely used in many fields such as machinery manufacturing, automobiles, aerospace, etc. Understanding the differences between them is important for obtaining high-performance parts. This article will explore these three processes in depth, including their principles, characteristics, differences and application scenarios, to help you make a wise choice.
1.Carburizing Process
1.Principle and Process
Carburizing is a heat treatment and surface hardening technique that usually heats metal (mainly steel) in the presence of carbon-containing materials (such as charcoal or carbon monoxide) to cause the metal to absorb carbon. For low-carbon workpieces, carbon diffuses to the surface, forming a hard outer layer, while the core remains tough and ductile. After treatment, the steel is usually quenched and tempered, the outer layer transforms from austenite to martensite, the hardness increases, and the core retains a softer ferrite and/or pearlite structure.
2.Key Control Points
The surface carbon content needs to be carefully controlled, about 0.8% is appropriate, to avoid excessive retained austenite affecting hardening. Carburizing is often used to solve the problem of undesirable decarburization in the early manufacturing stage. For parts that require high rigidity, such as gears, shafts and various automotive and mechanical parts, the carburizing process can improve their wear resistance and impact resistance.
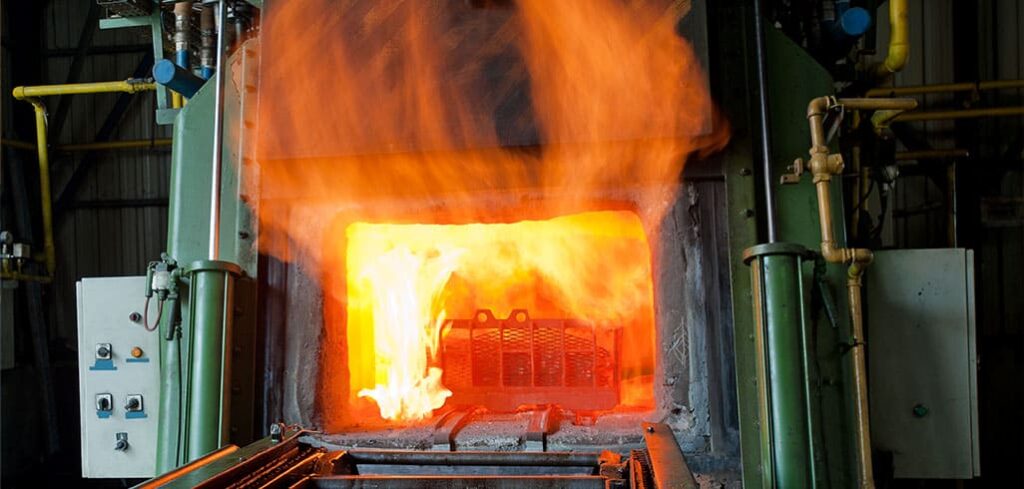
2.Nitriding process
1.Principle and process
Nitriding is a chemical heat treatment process in which nitrogen diffuses into the metal surface to form a hard outer layer while maintaining core properties. Effective on low carbon alloy steels containing nitride forming elements such as aluminum, molybdenum and chromium. Common methods include liquid nitriding, gas nitriding and ion nitriding. Taking gas nitriding as an example, the workpiece is placed in a sealed container, ammonia gas is introduced and heated. The nitrogen atoms generated by the thermal decomposition of ammonia are adsorbed on the surface of the workpiece and diffuse to the near-surface layer to form metal nitrides, making the surface hardness as high as 76 HRC ( 90HRA).
2.Process characteristics
Nitriding temperatures are below the austenitizing point of the steel, typically around 550°C (1022°F), resulting in low component deformation and good dimensional control. However, the hardness of the core is low and the permeability layer is shallow, so it is suitable for components that bear light to medium loads, as well as mechanical components and various tools and molds with heat resistance and corrosion resistance requirements.
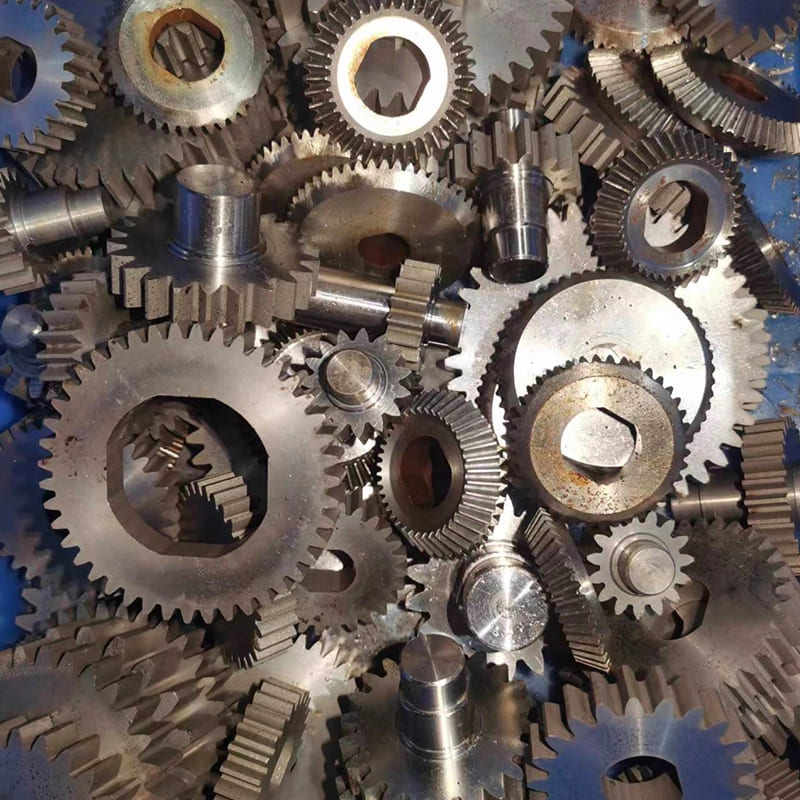
3.Carbonitriding Process
1.Principle and Process
Carbonitriding is a thermochemical surface modification technology that simultaneously injects carbon and nitrogen into the surface of parts to increase surface hardness and modulus. It is mainly used in low-carbon steel and is suitable for mass production of small parts such as gears, shafts, pistons, rollers and bearings, which require good wear resistance and a carburizing depth requirement of 0.1 to 0.75 mm.
2.Process Advantages
This process can produce a harder carburizing layer than carburizing, with a fast injection speed, good tempering and fatigue resistance, improved wear resistance and fatigue resistance, and a lower processing temperature.
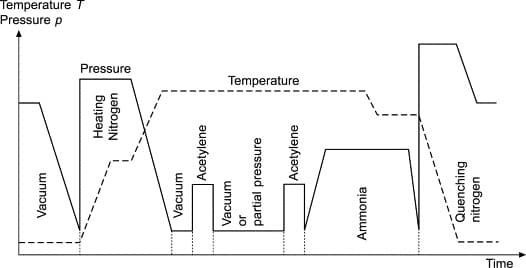
4.The difference between carburizing, nitriding and carbonitriding
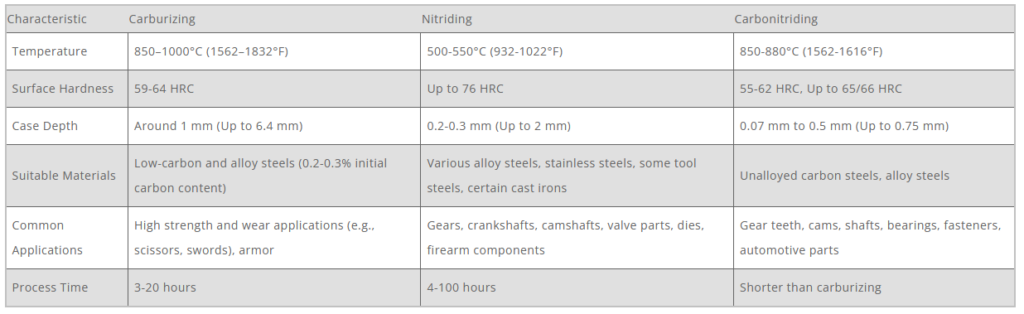
5.Application selection of carburizing, nitriding and carbonitriding
1.Carburizing Applications
Carburizing is suitable for high-strength and wear-resistant applications, when deep surface hardening is required, parts are subjected to high impact loads, slight distortion is allowed, and components are large. For example, gear teeth in heavy machinery, camshafts in high-performance engines, large industrial shafts, heavy equipment bearings, etc.
2.Nitriding Applications
Nitriding is suitable for parts that require excellent corrosion and wear resistance, high precision, and no additional processing, such as hydraulic cylinder rods, injection molds, aerospace precision gears, cutting tools, medical devices, etc.
3.Carbonitriding Applications
Carbonitriding strikes a balance between surface hardness and fatigue resistance. It is suitable for applications that need to balance multiple properties, consider cost-effectiveness, small and medium part sizes, allow certain deformation, and require good fatigue resistance, such as automotive clutch plates, engine valve seats, fasteners in corrosive environments, medium-sized gears, metalworking tools and molds, etc.
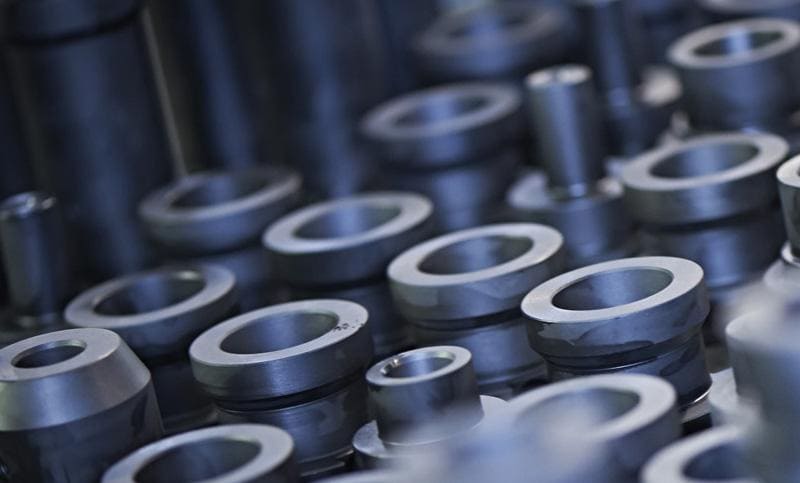
Summarize
Carburizing, nitriding and carbonitriding each have their own characteristics and advantages and are suitable for different application scenarios. In practical applications, the most suitable surface treatment process should be selected based on the specific requirements of the parts, taking into account factors such as performance, precision, and cost. With the continuous development of industrial technology, these processes will continue to improve and perfect, providing more reliable technical support for the manufacture of high-performance metal parts. By rationally selecting and applying these processes, the service life and reliability of parts can be effectively improved to meet the needs of various industrial fields.