case parts |
Case parts: the invisible heroes behind technology
In the tide of modern technology, electronic equipment is constantly developing towards miniaturization and intelligence.
Behind the operation of these high-tech products are the silent contributions of countless case parts. These seemingly insignificant parts are the key to the stable operation of electronic equipment. This article will take you to understand the world of case parts and explore their important role in the development of science and technology.case parts
1.Definition and role of case parts
(1) Definition
Case parts refer to those parts that have extremely high requirements on size, shape and surface quality. They are mainly used to construct the shell or internal structure of electronic equipment, precision instruments and high-tech equipment, playing a key role in support, protection, heat dissipation and connection. The precision of case parts directly affects the stability and reliability of the entire equipment, especially in the fields of aerospace, medical equipment and information technology, the quality of case parts is even more important.
(2) Role
1) Support and protection:
Case parts provide stable support for electronic components to prevent them from being damaged by external forces. At the same time, they can also effectively prevent external factors such as dust and moisture from eroding internal components.
2) Heat dissipation management:
Through reasonable structural design, case parts can optimize the heat dissipation path inside the equipment, improve heat dissipation efficiency, and ensure that electronic equipment operates stably at an appropriate temperature.
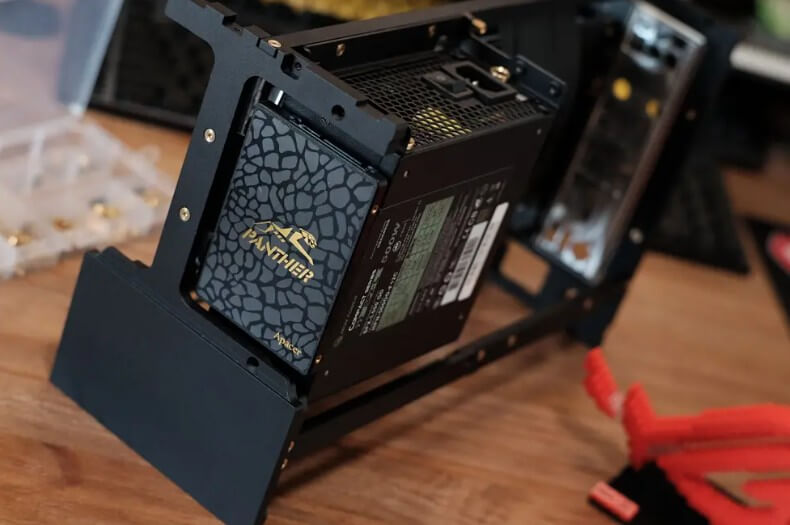
3) Electromagnetic shielding:
Some case parts have good electromagnetic shielding performance, which can effectively block the interference of electromagnetic waves generated by internal components to the outside world, and also prevent the influence of external electromagnetic waves on the equipment.
4) Easy installation and maintenance:
The design of case parts takes into account the convenience of installation and maintenance. Through modularization and standardization, the assembly and disassembly of equipment are simpler and faster.
5) Dustproof and soundproof:
Some high-end chassis are also equipped with dustproof nets and soundproof cotton to reduce dust entry and noise generation, and improve the user experience.
2.Industry application and importance of case parts
(1) In the aerospace field, case parts need to withstand extreme temperature and pressure changes to ensure the normal operation of aircraft.
(2) In medical equipment, precision chassis not only provide protection, but may also directly participate in the treatment process, such as precision parts in MRI machines and CT scanners.
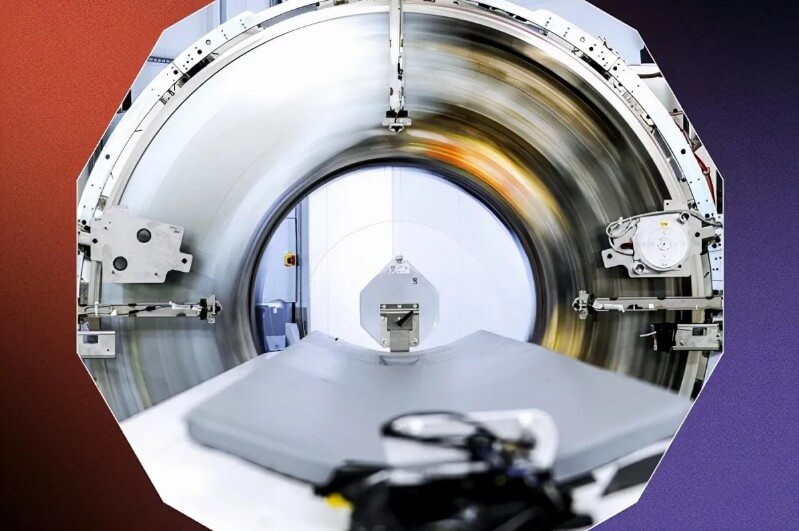
(3) Information technology industries, such as computers, servers, and high-speed communication equipment, have extremely high requirements for the precision and heat dissipation performance of chassis parts to ensure efficient and stable data processing.
The application of these industries not only requires parts to have high precision, but also requires materials to have specific physical and chemical properties to adapt to different working environments.
3.Material selection for case parts
(1) Common material types and their characteristics
The material selection of case parts has a decisive influence on their performance. Commonly used materials include aluminum alloys, stainless steel, and titanium alloys. Aluminum alloys are widely used in electronic equipment chassis due to their good thermal conductivity, light weight, and corrosion resistance. Stainless steel is often used in environments that require high strength and high corrosion resistance due to its excellent strength and corrosion resistance. Titanium alloys are used in high-end equipment and medical equipment due to their extremely high strength-to-density ratio and good biocompatibility.
(2) The impact of material selection on part precision and performance
The choice of materials not only affects the mechanical properties of the parts, such as strength and durability, but also affects their processing performance. For example, aluminum alloy is easier to process and is suitable for large-scale production; while titanium alloy is stronger, it is more difficult to process and more expensive. Different materials also react differently to heat treatment and surface treatment, which will affect the final accuracy and service life of the parts. Therefore, choosing the right material is a key step to ensure that the parts meet the design requirements and performance indicators.
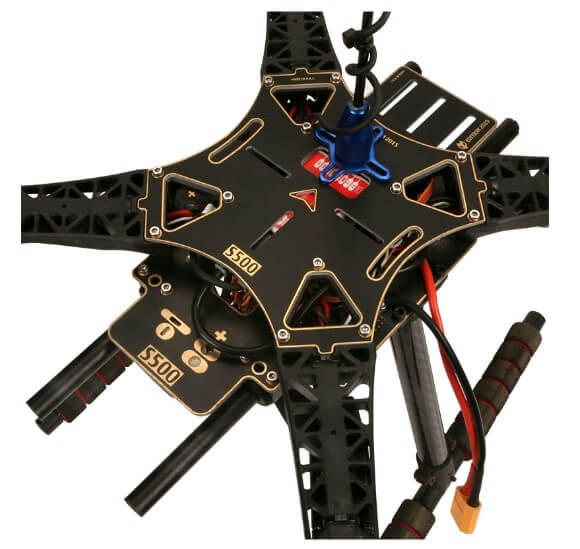
4.CNC machining methods for case parts
There are various machining methods for case parts, and each method has its specific advantages and scope of application. The following is a classification and introduction of several major CNC machining methods:
(1) CNC turning:
CNC turning is suitable for machining rotating parts such as shafts and discs. By controlling the lathe with a CNC system for automated machining, high-precision and high-efficiency machining can be achieved. This method is often used to process various shafts, holes and other parts in the machining of case parts.
(2) CNC milling:
CNC milling is one of the most commonly used methods in the machining of case parts. It can process various complex shapes and features, such as planes, curved surfaces, slots, holes, etc. CNC milling machines are equipped with a variety of tools and can perform rough machining, semi-finishing and finishing to meet different precision and surface quality requirements.
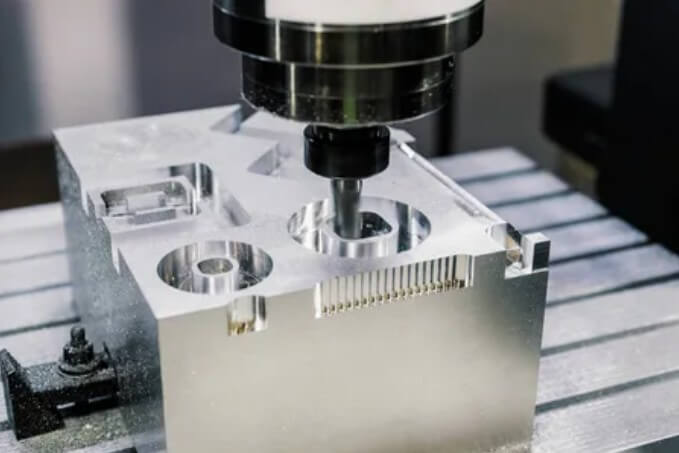
(3) CNC wire cutting:
CNC wire cutting is a cutting method that uses the principle of electric spark discharge, which is particularly suitable for processing parts with high hardness and complex shapes. In the processing of case parts, wire cutting is often used to cut various special-shaped holes, narrow slits and parts with complex shapes.
(4) CNC punching:
CNC punching is suitable for mass production of thin plate parts. Through the CNC system to control the punch press for automatic punching, it can quickly and efficiently process parts of various shapes. This method is often used to process various holes, slots and other features in the processing of case parts.
(5) CNC bending:
CNC bending is an important method for sheet metal forming. Through the CNC system to control the bending machine for automatic bending, high-precision sheet metal bending can be achieved. In the processing of case parts, bending processing is often used to process the bending parts of various boxes.
(6) CNC grinding:
CNC grinding is mainly used to improve the surface quality and precision of parts. By controlling the grinding machine through the CNC system for automated grinding, it is possible to achieve precision grinding of various materials. This method is often used to process high-precision planes, curved surfaces and other parts in the processing of case parts.
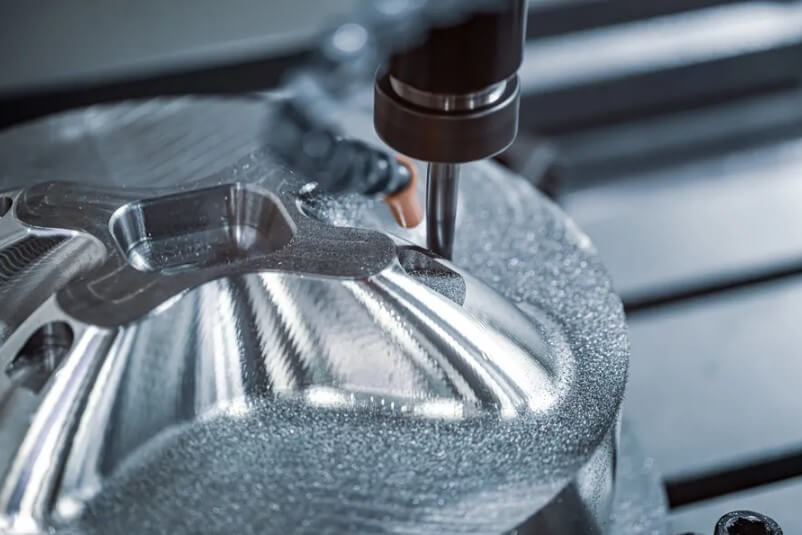
(7) CNC drilling:
CNC drilling is suitable for processing various holes on parts. By controlling the drilling machine through the CNC system for automated drilling, it is possible to achieve high-precision and high-efficiency hole processing effects. This method is often used to process various mounting holes, positioning holes and the like in the processing of case parts.
5.Factors affecting the precision of case parts during processing
(1) Factors of the machine tool itself
The precision of the machine tool directly affects the processing precision of the parts. Guide rail error, spindle rotation error and transmission chain error are the three common error sources of machine tools.
Guideway error will affect the motion accuracy of the machine tool, resulting in position deviation of the parts during processing. Spindle rotation error will affect the roundness and surface roughness of the parts. Especially in high-precision processing, the control of rotation error is crucial. Drive chain error will affect the transmission accuracy of the machine tool, resulting in dimensional deviation of the parts during processing.
(2) Influence of process parameters
Cutting speed, feed rate and cutting depth are the three major process parameters in cutting processing. The selection of these parameters has a direct impact on the processing accuracy and surface quality of the parts.
For example, too high a cutting speed may lead to increased cutting heat, thereby causing thermal deformation of the parts; too low a cutting speed may lead to increased cutting force, thereby causing elastic deformation of the parts. Feed rate and cutting depth also need to be reasonably selected to avoid excessive cutting force and cutting heat.
(3) Control of environmental factors
Environmental factors such as temperature, humidity and vibration will also affect processing accuracy. For example, temperature changes will cause thermal expansion and contraction of machine tools and parts, thereby affecting processing accuracy; humidity changes may cause rust on machine tools and parts, thereby affecting processing quality; vibration may cause unstable movement of machine tools, thereby affecting processing accuracy. Therefore, in precision machining, the working environment needs to be strictly controlled to reduce the impact of environmental factors on machining accuracy.
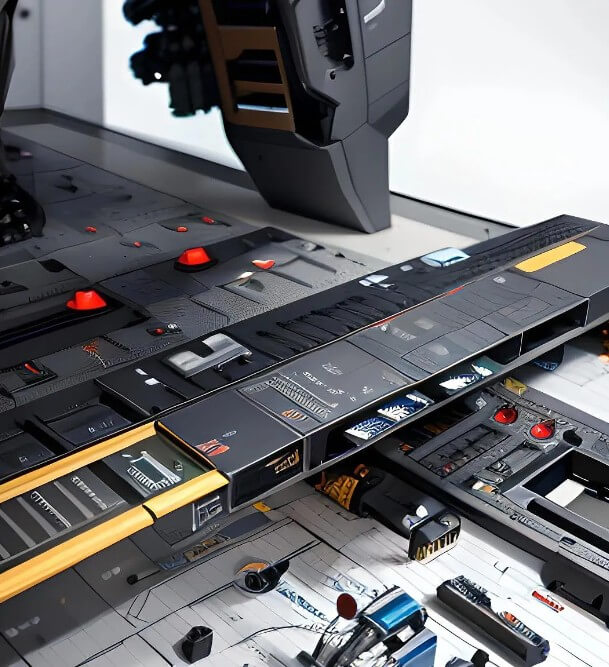
6.Inspection technology of case parts
(1) Classification and application of inspection methods
The inspection methods of case parts mainly include two categories: precision inspection and surface quality inspection. Precision inspection usually uses equipment such as three-dimensional coordinate measuring machines and optical measuring instruments. These equipment can measure the size and shape errors of parts with high precision. Surface quality inspection often uses tools such as surface roughness meters and microscopes to evaluate the surface finish and defects of parts.
(2) Commonly used inspection equipment and tools
Three-dimensional coordinate measuring machines are one of the most commonly used high-precision measuring equipment. They can measure the complex geometric shapes and dimensional errors of parts. Surface roughness meters are used to measure the microscopic geometric shapes of part surfaces and evaluate their smoothness. Microscopes are used to observe the microstructure and defects of part surfaces. Especially in high-precision machining, even small differences in surface quality may affect the performance of parts.
7.Summary
The impact of case parts on the performance of the entire system is significant, and the strategy and significance of improving the precision of parts are also very important. By adopting advanced materials, optimized design and precise processing technology, the precision and performance of case parts can be significantly improved.