Centreless grinding process: an indispensable technology in modern industry
Since its introduction, the centreless grinding process has been widely used in modern industry for its excellent processing performance. Its processing characteristics without the need for center support have greatly improved the processing accuracy and surface quality of the workpiece. This article will comprehensively introduce the definition, principle, characteristics, classification, key processes and key technologies of the centreless grinding process, as well as its application in different industrial fields, and explore its important position in modern industry and future development direction.
1.Basic concept of centreless grinding process
(1) Definition and principle
Centerless grinding is an efficient CNC precision grinding process. Its basic principle is to use the friction between the grinding wheel and the guide wheel to drive the workpiece to rotate and grind. The workpiece does not require traditional center positioning during the grinding process, but is stabilized and ground by the combined action of the grinding wheel, guide wheel and support plate. This grinding method can achieve automatic feeding and grinding of the workpiece by adjusting the angle and position of the grinding wheel and guide wheel, thereby improving the efficiency and accuracy of grinding.
(2) Synergy of key components
The centreless grinding process mainly relies on the coordinated work of three key components: grinding wheel, guide wheel and support plate. The grinding wheel is responsible for performing the actual grinding operation, removing material from the workpiece surface by rotating at high speed. The guide wheel drives the workpiece to rotate through the friction with the workpiece, and its speed and angle can be adjusted to control the feed speed and direction of the workpiece. The function of the support plate is to support the workpiece and ensure its stability during the grinding process.
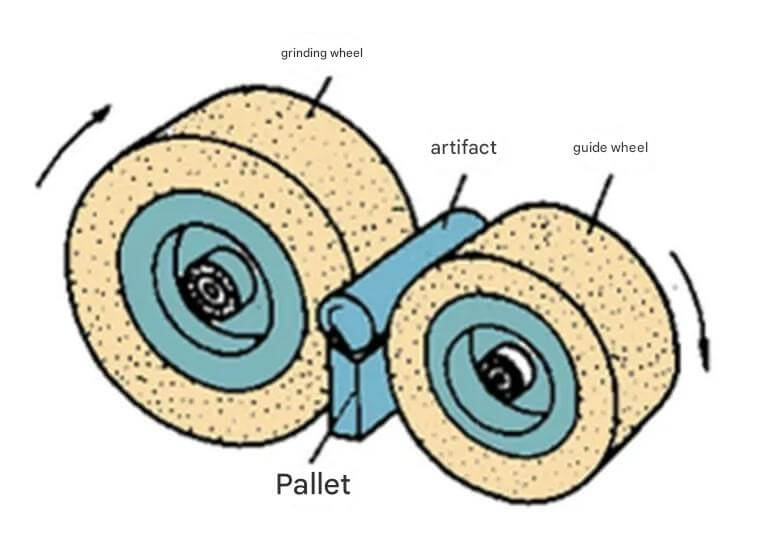
(3) Characteristics
The main characteristics of the centreless grinding process are its high efficiency and high precision. Since the workpiece is self-centered during the grinding process, it can reduce the error caused by improper clamping and improve the roundness and dimensional consistency of the workpiece. In addition, centerless grinding can achieve continuous automated production and is suitable for the needs of large-scale industrial production.
(4) Classification
Centerless grinding is mainly divided into through-grinding and cut-in grinding. In through-grinding, the workpiece passes continuously between the grinding wheel and the guide wheel, which is suitable for the grinding of long strips of workpieces. In-feed grinding is to feed the workpiece laterally between the grinding wheel and the guide wheel, which is suitable for shorter or complex-shaped workpieces. The flexible application of these two methods enables the centreless grinding process to meet the processing requirements of workpieces of different shapes and sizes.
2.Key process of centreless grinding process
Centreless grinding process is an efficient metal processing method, named because it does not require a center support. It is widely used in the mass production of parts such as shafts, pins and bearings. The key process flow of centerless grinding will be analyzed in detail below:
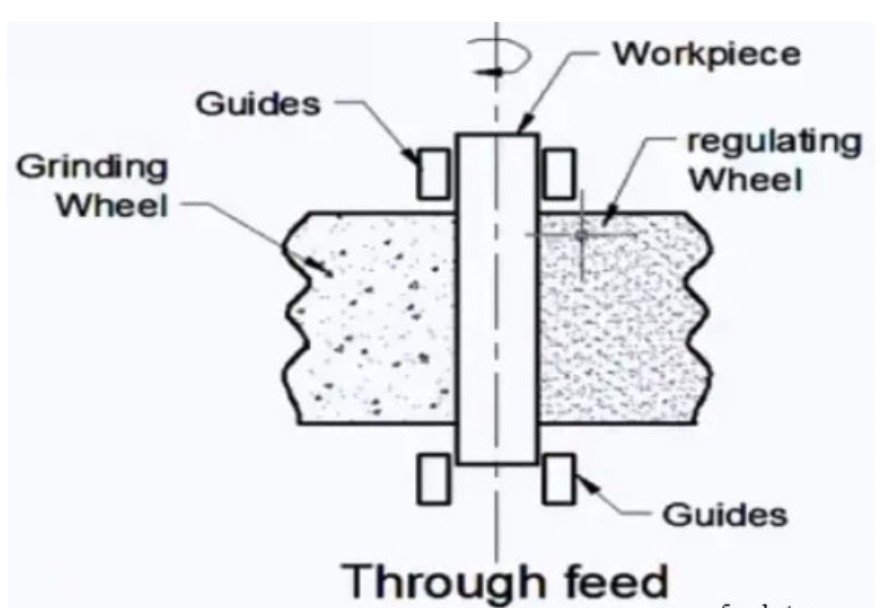
(1) Preparation:
Before starting centerless grinding, a series of preparations need to be carried out first. This includes determining the processing parameters, such as grinding speed, grinding depth, etc., to ensure processing quality and efficiency. In addition, the workpiece needs to be preliminarily processed, such as cutting the end face to keep it in the same plane and clamping it in the chuck.
(2) Adjusting equipment:
Adjusting the various parameters of the centerless grinder is a key step to ensure processing accuracy. The operator needs to adjust the center height of the grinding wheel to make it the same as the center height of the workpiece, and adjust the angle of the grinding wheel to ensure that it is in a straight line with the workpiece. In addition, the angle and position of the guide wheel need to be adjusted so that it can effectively drive the workpiece to rotate and move.
(3) Grinding method selection:
There are three main grinding methods for centerless grinders: through-type, cut-in type and cut-in-through type. Through-type grinding is suitable for slender cylindrical workpieces. The axial feed of the workpiece is achieved by adjusting the slight inclination angle of the guide wheel axis. Cut-in type grinding is used to grind workpieces with shoulders or bosses. The grinding wheel or guide wheel is cut in for grinding. Cut-in-through type is a combination of the two and is suitable for workpieces with complex shapes.
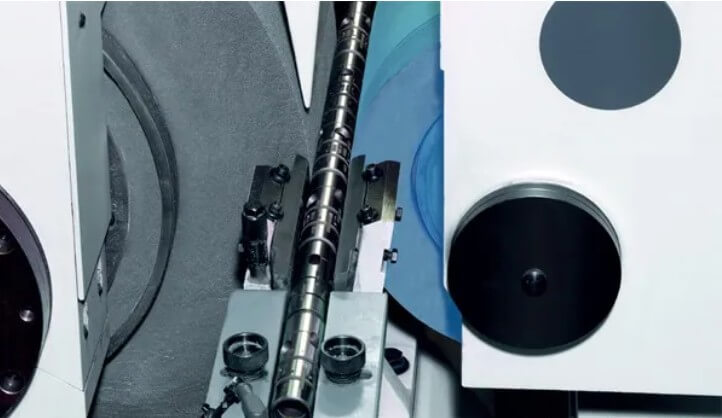
(4) Grinding process:
After starting the grinding wheel, the diameter change of the workpiece is detected by a non-contact photoelectric element, and the flow rate and speed of the grinding wheel are controlled to keep it stable during the processing. Under the fixed grinding wheel radius and center height, the operator needs to control the distance between the grinding wheel and the workpiece to produce appropriate grinding action.
(5) Quality inspection:
After grinding, the diameter, roughness and other indicators of the workpiece need to be tested to ensure that the processing quality meets the process requirements. If problems such as grinding burns and insufficient grinding accuracy are found, the processing parameters or equipment status need to be adjusted in time.
(6) Cleaning and maintenance:
After processing, clean the work area and keep the equipment and working environment clean. This step is of great significance to ensure the normal operation of the equipment and extend the life of the equipment.
3.Key technologies of centreless grinding process
(1) Selection and adjustment of grinding wheel and guide wheel
Selecting suitable grinding wheel and guide wheel is the key in centreless grinding process. The hardness and particle size of the grinding wheel directly affect the grinding efficiency and workpiece surface quality, while the hardness and surface state of the guide wheel affect the rotation stability and feed speed of the workpiece. Correctly adjusting the angle and position between the two wheels can ensure automatic feeding of the workpiece and a stable grinding process.
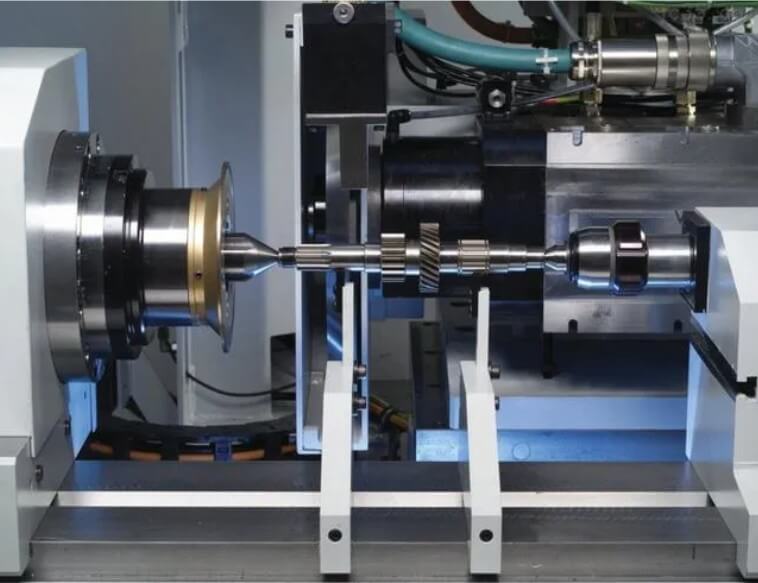
(2) Adjustment and optimization of the support plate
The support plate plays an important role in supporting the workpiece in centerless grinding. The position and angle adjustment of the support plate directly affect the grinding effect of the workpiece. Optimizing the design and adjustment of the support plate can improve the stability and grinding accuracy of the workpiece and reduce vibration and errors during the grinding process.
(3) Determination of workpiece center height
Determination of workpiece center height is an important technical parameter in the centreless grinding process. The center of the workpiece must be higher than the center line of the grinding wheel and the guide wheel to ensure the stability and roundness of the workpiece during the grinding process. The correct center height setting can be determined through experiments and adjustments to ensure the best grinding effect.
(4) Grinding parameter setting
Grinding speed, depth and feed speed are key parameters in the centreless grinding process. Reasonable parameter setting can effectively improve grinding efficiency while ensuring the machining accuracy and surface quality of the workpiece. For example, a higher grinding speed can improve grinding efficiency but may affect the surface quality; while a larger grinding depth may cause burns and deformation on the workpiece surface. Therefore, it is necessary to determine the optimal grinding parameters through experiments and adjustments based on specific processing requirements and material properties.
(5) Use of coolant
Coolant plays a role in cooling and lubrication in the centreless grinding process, which can effectively reduce grinding heat, prevent overheating of the workpiece and grinding wheel, and improve grinding efficiency and workpiece surface quality. When choosing a suitable coolant, we should not only consider its cooling performance, but also its corrosiveness to workpieces and equipment and its environmental friendliness. For example, water-based coolants have good cooling performance, but may be corrosive to certain metal materials; while oil-based coolants have good lubrication performance, but the cooling effect is relatively poor.
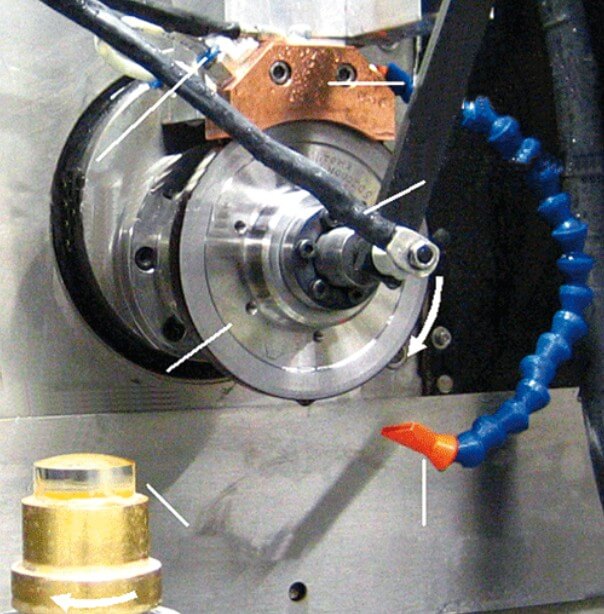
4.Application fields and examples of centerless grinding technology
(1) Application in the automotive industry
The centerless grinding technology is mainly used in the automotive industry to produce key components such as shafts and bearings. For example, high-precision grinding of automobile drive shafts, crankshafts and other components usually adopts centerless grinding technology to ensure their dimensional accuracy and surface quality, thereby meeting the requirements of high performance and long life of automobiles.
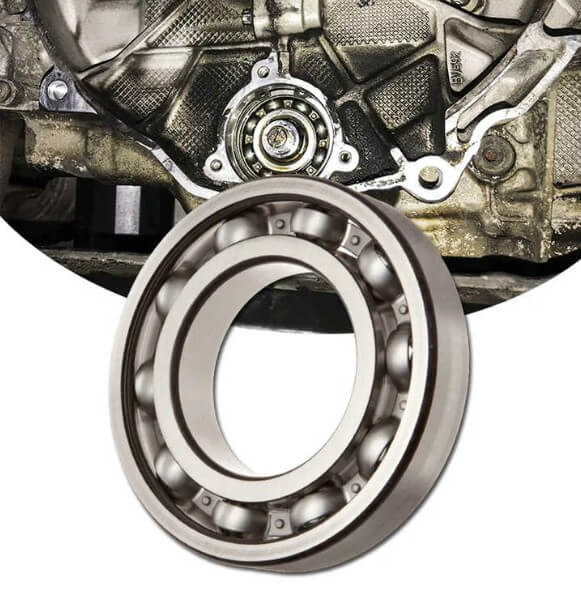
(2) Application in bearing manufacturing
In bearing manufacturing, the centreless grinding process is used to process the inner and outer rings of bearings. This technology can accurately control the size and shape of the bearing rings, improve the rotation accuracy and service life of the bearings. The high efficiency and consistency of centerless grinding make it an ideal choice for mass production of bearings.
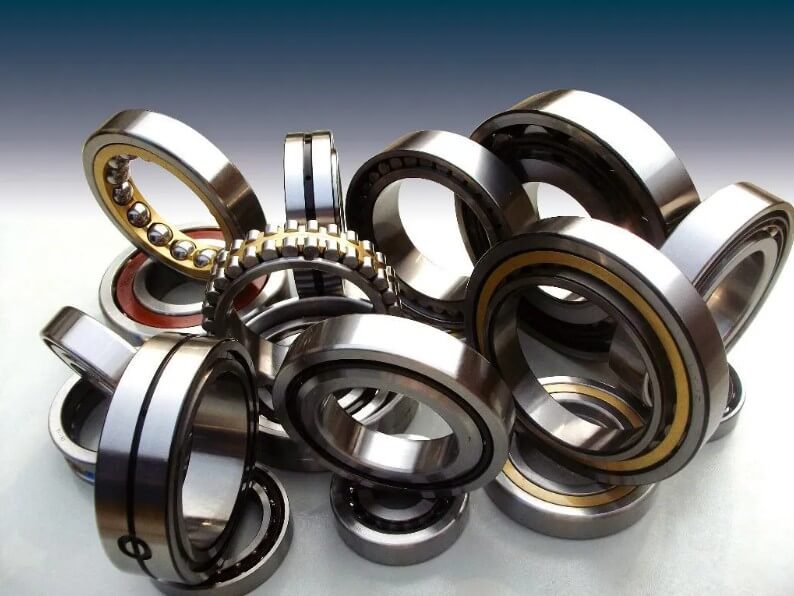
(3) Application in other fields
In addition to automobile and bearing manufacturing, centerless grinding is also widely used in aerospace, electronic products and other fields. For example, in the aerospace field, centerless grinding is used to process key components of high-strength alloy materials to ensure their high precision and reliability. In electronic product manufacturing, centerless grinding is used to process precision metal parts such as connectors and housings.
5.Common problems and solutions of centreless grinding process
(1) Problem of large roundness error of workpiece
Large roundness error of workpiece is one of the common problems in centerless grinding. This is usually caused by uneven wear of grinding wheel or guide wheel, improper adjustment of pallet or incorrect setting of workpiece center height. Solutions to this problem include regular inspection and replacement of grinding wheel and guide wheel, precise adjustment of pallet position, and optimization of workpiece center height setting.
(2) Workpiece surface quality problem
In centerless grinding, workpiece surface quality problems may manifest as surface roughness not meeting requirements or grinding burn. This is usually related to improper setting of grinding parameters, insufficient use of coolant or inappropriate selection of grinding wheel. By optimizing the grinding speed, feed rate and grinding depth, as well as ensuring sufficient and effective cooling, the surface quality of the workpiece can be significantly improved.
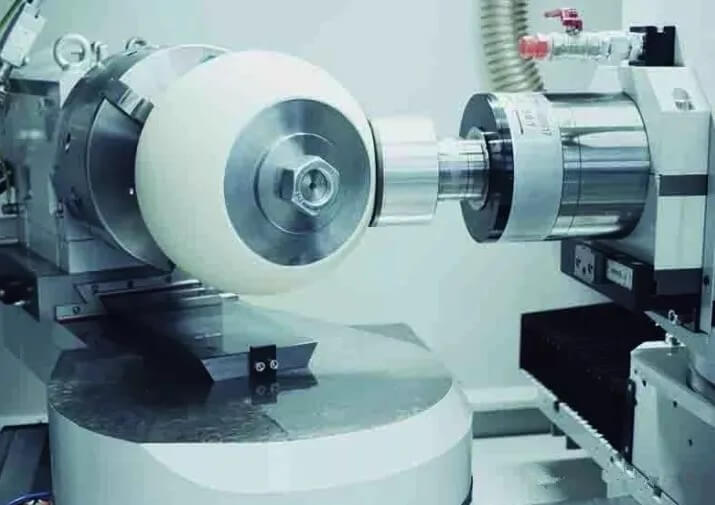
(3) Equipment adjustment and maintenance issues
Precise adjustment and regular maintenance of centerless grinders are the key to ensuring grinding quality and efficiency. Common equipment problems include wear of the grinding wheel and guide wheel, deviation of the support plate position, etc. Regular inspection and adjustment of the equipment, timely replacement of worn parts, and necessary maintenance and care can ensure the stable operation of the equipment and the grinding effect.
6.Development trend and future direction of centreless grinding process
(1) Development trend
With the growing demand for high efficiency and high precision in the manufacturing industry, the centreless grinding process is moving towards higher precision and higher automation. Modern centerless grinders are increasingly adopting CNC technology, which can not only improve grinding accuracy, but also realize more complex grinding operations and automated production processes.
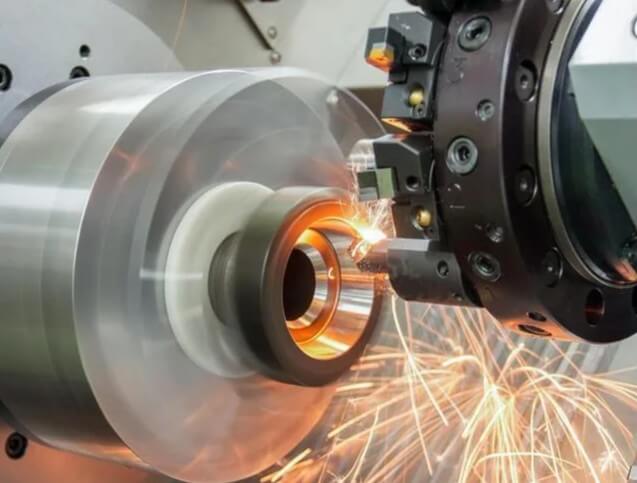
(2) Application of new technologies in centerless grinding
New technologies such as artificial intelligence and machine learning are being introduced into the field of centerless grinding to optimize the grinding process and improve processing quality. These technologies can help analyze grinding data in real time and automatically adjust grinding parameters, thereby reducing manual intervention and improving production efficiency and product quality.
7.Summary
As an efficient precision machining method, the centreless grinding process has broad application prospects in the future manufacturing industry. Through continuous technological innovation and optimization, centerless grinding will continue to play an important role in improving machining accuracy, efficiency and automation level.
4 Comments