Overview of chrome plating process
Chrome plating, also known as chrome plating, is a widely used chrome plating material. The chrome plating process is used in a wide range of industries. It involves depositing a thin layer of chrome on the surface of a metal, thereby enhancing its properties such as corrosion resistance, hardness, and shiny appearance. It also plays a role in bar turning of industrial parts, bunton zero turn mower parts, and craftsman 42 inch zero turn mower parts. This article aims to provide a comprehensive overview of the chrome plating process.
1.Chrome Plating Steps
1) The chrome plating process begins with the preparation of the metal surface
The surface must be thoroughly clean and free of any contaminants such as dirt, grease or rust. This is usually accomplished through a series of cleaning and polishing steps, including degreasing, pickling and mechanical polishing.
The goal is to create a smooth, clean surface on the part, such as turning of industrial parts, bunton zero turn mower parts and craftsman 42 inch zero turn mower parts, to enable the chrome layer to adhere properly.
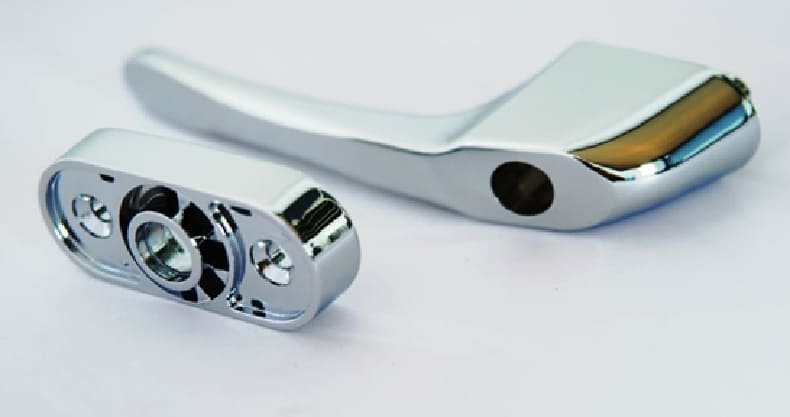
2) Once the surface is prepared, the electroplating process can begin
Chrome plating can be achieved through a variety of methods, including electroplating and chemical plating. Electroplating is the most common method and involves the use of an electrolytic cell containing chromium ions. The metal surface acts as a cathode, while a chromium anode is used to provide the chromium ions. When an electric current is applied, the chromium ions are reduced and deposited on the metal surface to form a thin layer of chromium.
3) During the electroplating process
The thickness of the chromium layer can be controlled by adjusting the electroplating time and current density. Therefore, for applications that require enhanced corrosion resistance or improved wear resistance, a thicker chromium layer is usually required. But be aware that too much thickness can cause the chrome layer to crack or peel off.
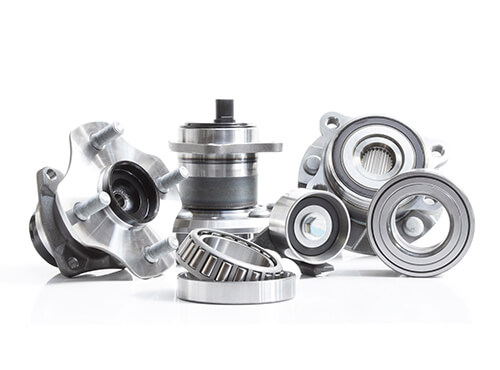
2.Key Benefits of Chrome Plating
1) Excellent Corrosion Resistance
The chrome layer acts as a barrier, preventing the metal underneath from coming into contact with corrosive substances. This makes chrome-plated surfaces ideal for industries such as automotive, aerospace, and marine that are often exposed to harsh environments.
2) Improved Hardness
The hardness of the chrome layer can be further increased by adding other elements such as nickel or cobalt to the plating solution. This makes chrome-plated surfaces suitable for applications that require wear and scratch resistance, such as cutting tools, molds, and machine parts.
3) Provides a Decorative and Lustrous Appearance
The reflective properties of chrome give the coating a mirror-like finish, making it ideal for applications in the automotive and consumer goods industries. Chrome-plated parts such as bumpers, trims, and accessories add a touch of elegance and sophistication to vehicle and home decor.
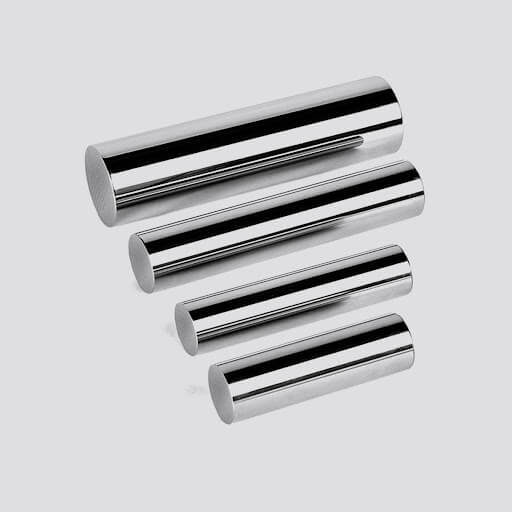
3.In summary
Chrome plating is a versatile process that offers a range of benefits, including corrosion resistance, hardness and aesthetics. The process involves depositing a thin layer of chromium on the surface of the metal through electroplating or electroless plating. The resulting chrome surfaces can be used in a variety of industries, including automotive, aerospace and consumer products. Whether for functional or decorative purposes, chrome plating remains a popular choice for enhancing the performance and appearance of metal surfaces.