CNC Aluminum Machining: 8 Things You Need to Know
CNC or Computer Numerical Control is a family of processes used for prototyping or mass production. These processes run on a computer program and involve various operations such as turning and milling.
Meanwhile, aluminum is a preferred material in the manufacturing industry due to its functional versatility. Its excellent machinability and interesting thermal and mechanical properties make it popular in the industry.
Moreover, the easy formability of aluminum makes it ideal for the drilling process involved in CNC aluminum machining. Essentially, other lightweight metals such as magnesium and titanium alloys cannot even compare to the versatility of aluminum.
It is commonly used in the production of CNC cars and other CNC parts that need to be lightweight for heavy use. So, in this article, we will cover five things you may not know about CNC machining aluminum.
1.Aluminum as a Material for CNC Aluminum Machining
Aluminum is one of the lightest metals and is known for being soft, easy to forge, easy to machine, and durable. Its appearance depends on the roughness of its surface, which makes it appear silver or dark gray in its unprocessed state.
Moreover, it lacks magnetism but is a good conductor of electricity, although it is not as conductive as copper for a specific cross-sectional area. It is non-flammable and has a melting point of about 640 degrees Celsius. In terms of its wide range of applications, aluminum is widely used in CNC automotive applications such as ATV, aerospace, and medical industries due to its light density of 2.68.
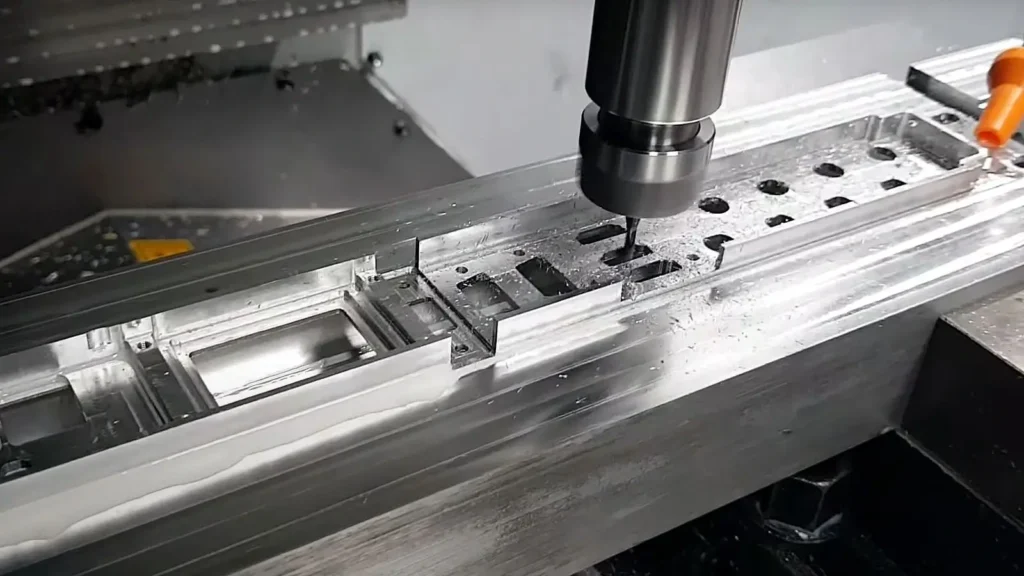
2.Aluminum Grades
Although aluminum is available in a variety of grades for various CNC aluminum machining processes, the choice of aluminum grade ultimately depends on the machining project you are planning. Aluminum is graded and ranked based on its most and least important characteristics.
In this case, aluminum grades allow you to choose aluminum with specific shapes and characteristics based on your requirements as all of them are highly machinable.
Below we have discussed several aluminum grades and their importance:
- 6061 Aluminum: It is commonly used in 5-axis CNC aluminum machining. It is undoubtedly very suitable for extrusion processes due to its excellent weldability and local properties. Apart from this, it also has excellent mechanical properties with excellent corrosion resistance, medium to high strength, cold anodizing, bend machinability, and excellent toughness under extreme conditions.
- 7075 Aluminum: While this grade of aluminum is also better in terms of corrosion resistance, the reason for its popularity is its excellent fatigue strength. However, due to its high price, it may not be suitable for welding. Therefore, it is still a good choice for making strong parts such as bicycle parts, fuselages, climbing kits, and aircraft wings.
- Aluminum 2024: Aluminum 2024 is known for its excellent mechanical properties such as wear resistance and high strength. At the same time, its corrosion resistance is poor and it is not weldable. It is mainly used in the military and aerospace industries.
3.CNC Aluminum Machining Prototypes
Aluminum machining prototypes are usually made of various alloys. Almost all of these alloys have high strength and low density structures. The most commonly used aluminum alloy is 6061-T6 because it is very suitable for use in electronics, transportation, aerospace, and military industries, etc.
Typically, CNC aluminum machining operations for prototypes have excellent control tolerances, such as 0.001MM, while making unique and high-quality aluminum prototypes. Again, CNC milling is the best choice because of the benefits brought by the machining process to achieve high precision and milling aluminum.
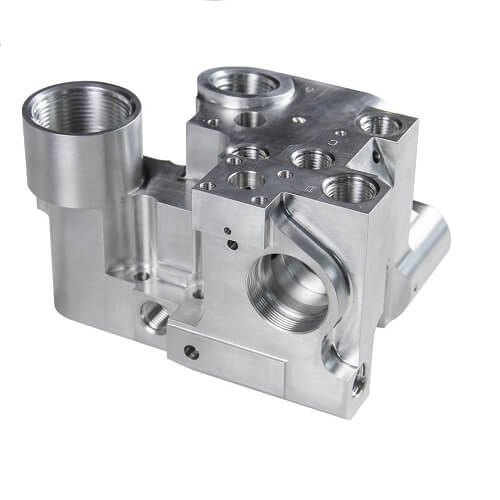
4.CNC Aluminum Machining: Parts and Components
CNC machined aluminum manufactures different CNC parts and components suitable for various services such as turning, milling and grinding. There is no doubt that the popularity of well-machined CNC aluminum parts in the engineering field is now steadily increasing.
Here are some CNC machined aluminum parts and components:
- Front panels
- Pins
- EMI housings
- Spline shafts
- Medical equipment
- Lighting fixtures
5.Avoid deformation in CNC aluminum machining
Although aluminum is the darling of the industry, it also has serious drawbacks. Due to its relatively low hardness and high thermal expansion, aluminum will deform when machined into thin walls. However, several precautions can be taken in advance to avoid material deformation.
1) Symmetrical CNC aluminum machining
It is crucial to prevent extreme heat concentration and instead create a heat dispersion or dissipation mechanism to minimize the rate of thermal deformation.
2) Layered multi-CNC aluminum machining
There are multiple cavities in the aluminum alloy plate, which will cause one cavity wall to distort due to the distribution of forces. To prevent this from happening, make sure that all cavities are processed at the same time.
6.Ensure proper CNC aluminum machining cutting parameters\
The size of the cutting depth has a significant impact on the cutting parameters. But on the other hand, CNC milling operations can solve this problem by increasing the machine speed, reducing cutting forces, while maintaining efficiency and reducing the number of cuts.
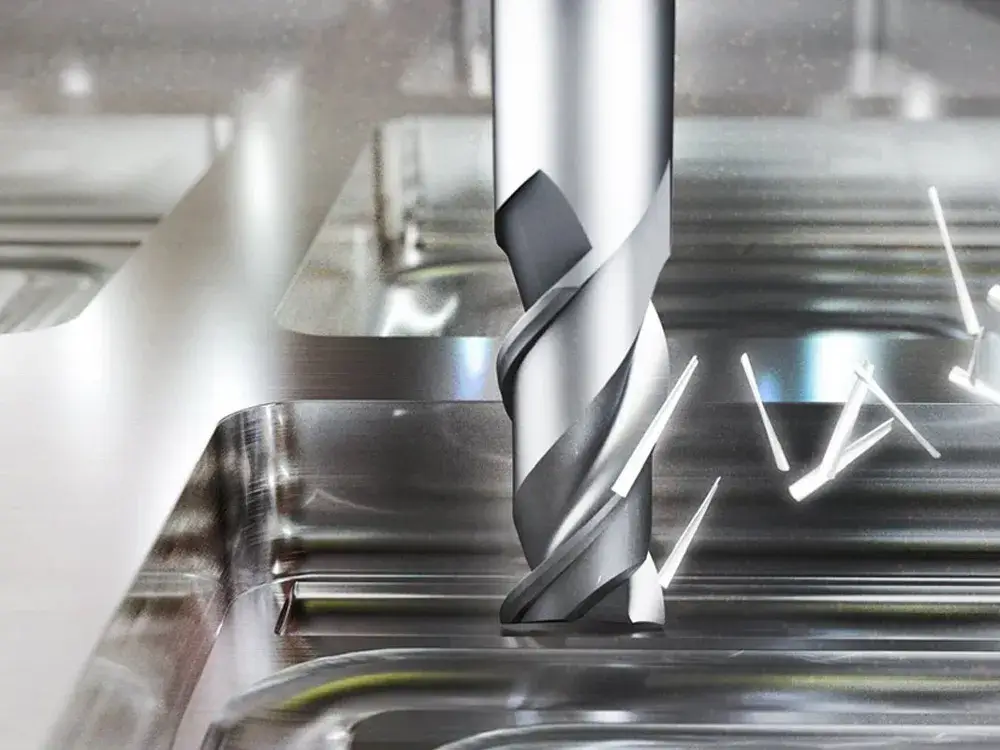
7.CNC aluminum machining – drilling and milling
When the milling cutter is used for the cavity, the cutting becomes full, causing cutting heat, deformation and expansion. However, the easiest way to avoid this problem is to pre-drill with a tool larger than the milling cutter before inserting the milling cutter and milling.
8.5-axis CNC aluminum machining
During 5-axis machining, the CNC cuts at five angles of the axis simultaneously. At the same time, the process is fast and reliable and can be used to design complex parts. According to records, the reasons for adopting 5-axis CNC aluminum machining are as follows:
- The setup remains single, which shortens the delivery time and improves efficiency.
- It can provide better geometry by avoiding collisions with the tool holder, tilting the table/tool.
- Cutting pieces do not have to go through multiple workstations, thus minimizing errors, maintaining precision or accuracy, and ensuring high quality.
- It allows the use of smaller tools with higher rigidity. Some of these tools allow for higher spindle speeds by reducing the load on the cutting tool.
9.Conclusion
In conclusion, we have discussed various CNC aluminum machining procedures that transform pre-machined aluminum parts into finished products. Remember, it refers to a painstaking process that requires experience, precision and accuracy, and sturdy machinery. This is no doubt due to the different aluminum alloys used.
On the other hand, aluminum has several significant benefits, including a fast cutting process and high-quality results. Moreover, the industry is filled with professionals to cater to your needs; however, do your homework and get samples to ensure the quality of CNC aluminum.
If you are looking for an experienced CNC machining manufacturer, Xavier is your ideal choice. The Xavier team is well-equipped to provide high-quality CNC machining solutions. If you need more information or to discuss your machining needs with us, please feel free to contact us.