The revolution of CNC automatic: the automation advantages of CNC machining centers
With the advancement of Industry 4.0, CNC automatic technology plays an increasingly important role in modern manufacturing. As the core equipment of CNC automatic, CNC machining centers not only improve production efficiency, but also significantly improve processing accuracy and flexibility. This article will discuss in detail the concept, specific manifestations and significant advantages of CNC automatic.
1.Definition of CNC automatic
CNC automatic refers to the automatic control of machine tools through computer numerical control systems. It uses pre-programmed instruction sets to automatically complete complex processing tasks, reduce human intervention, and improve production efficiency and accuracy.
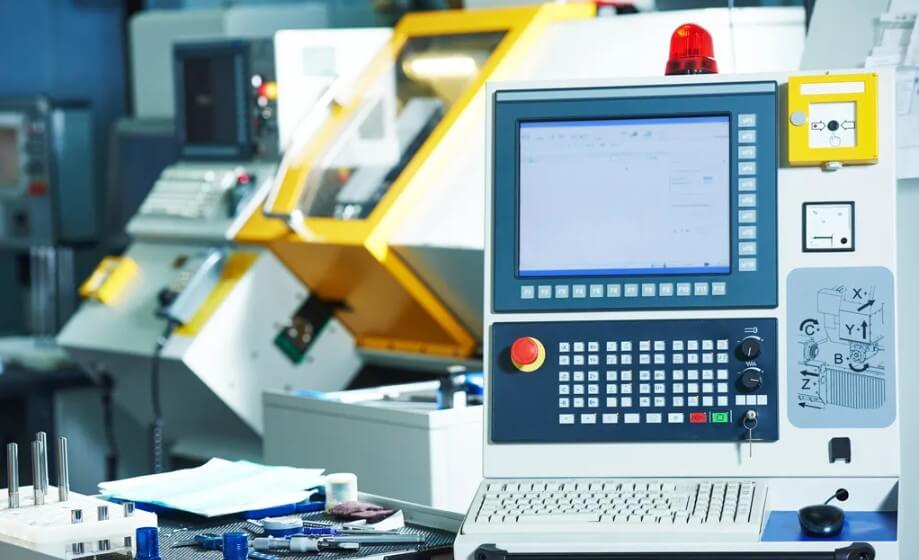
2.Specific manifestations of CNC automatic
(1) Automatic tool changing system (ATC)
The automatic tool changing system is one of the core automation functions of CNC machining centers. It can automatically change tools during the processing process, reduce tool changing time, and improve production efficiency. The ATC system usually includes a tool magazine, a tool changing robot and a control system.
1) Tool magazine: Stores a variety of tools and automatically selects according to processing requirements.
2) Tool changing robot: Quickly and accurately exchange tools between the tool magazine and the spindle.
3) Control system: coordinate the actions of the tool magazine and the manipulator to ensure a smooth tool change process.
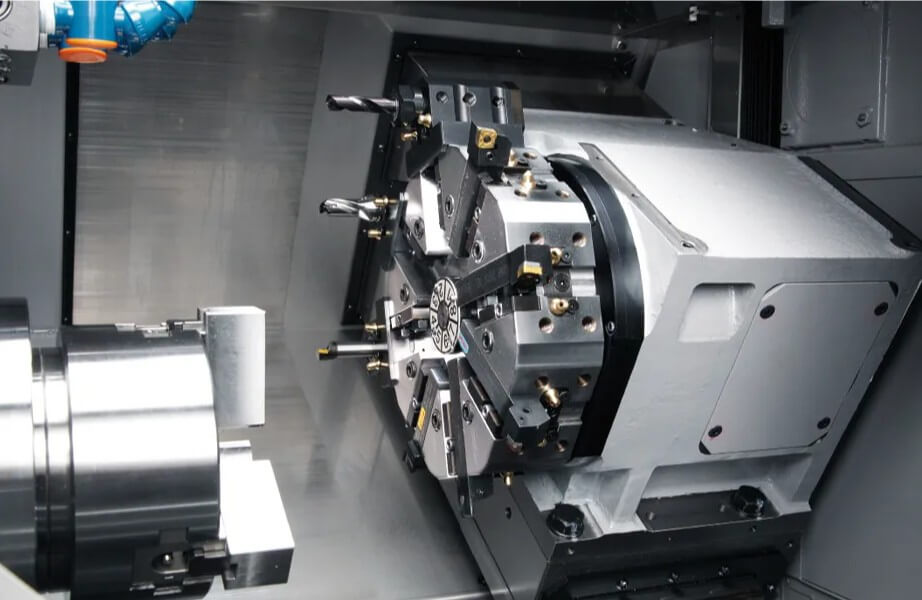
(2) Automatic workpiece clamping system
The automatic workpiece clamping system realizes automatic clamping and unloading of workpieces through the cooperation of the fixture and the manipulator. This not only reduces manual operation, but also improves clamping accuracy and consistency.
1) Fixture: designed according to the shape of the workpiece and processing requirements to ensure the stability of the workpiece.
2) Manipulator: automatically grab and place the workpiece to reduce manual intervention.
3) Sensor: detect the position and clamping status of the workpiece to ensure processing accuracy.
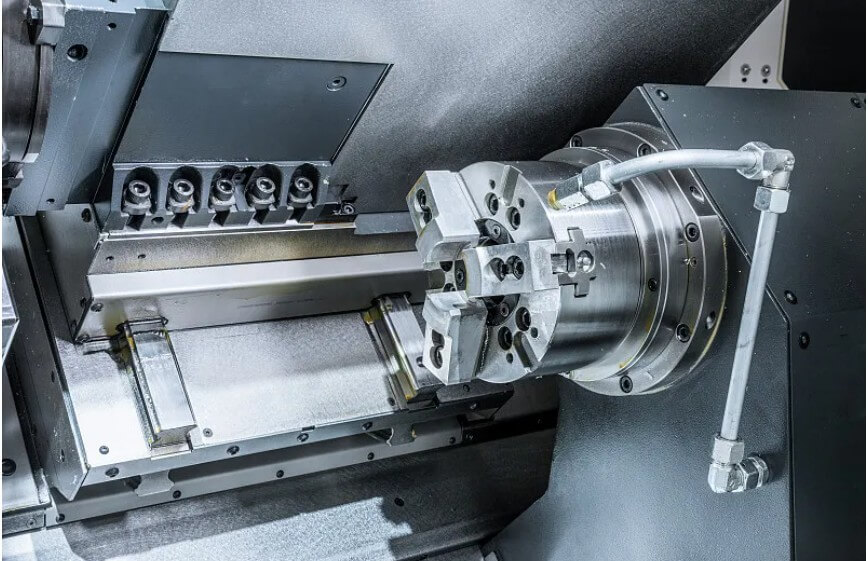
(3) Automatic detection and compensation system
The automatic detection and compensation system uses sensors and software algorithms to monitor errors in the processing process in real time and automatically compensates. This significantly improves processing accuracy and product consistency.
1) Sensor: real-time monitoring of temperature, vibration, tool wear and other parameters during the processing process.
2) Software algorithm: automatically adjust processing parameters and compensate errors based on sensor data.
Feedback system: feedback the compensation results to the control system to ensure processing accuracy.
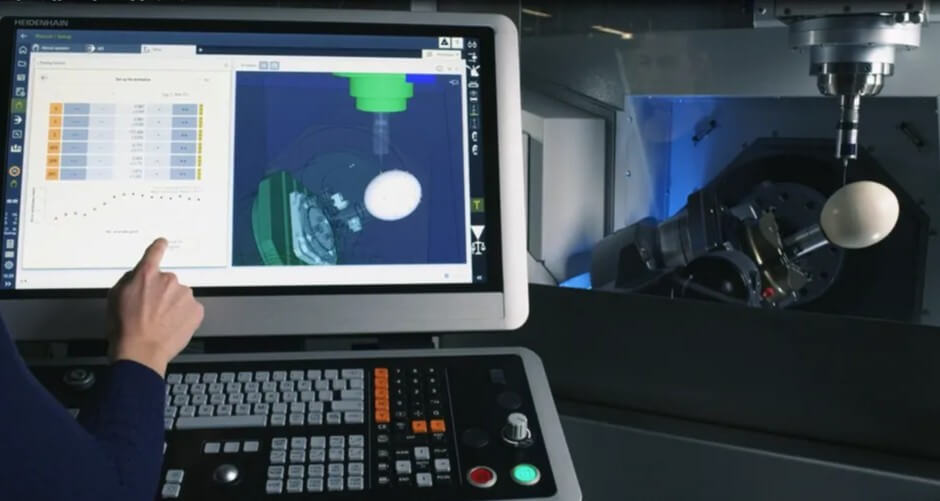
(4) Automatic programming and optimization
CNC machining centers are usually equipped with automatic programming software that can automatically generate machining paths and codes based on 3D models. This not only reduces programming time, but also optimizes machining paths and improves machining efficiency.
1) CAD/CAM software: Convert 3D models into machining codes and automatically generate machining paths.
2) Optimization algorithm: Optimize machining parameters and paths based on material properties and machining requirements.
3) Simulation system: Simulate the machining process in a virtual environment to ensure that the code is accurate.
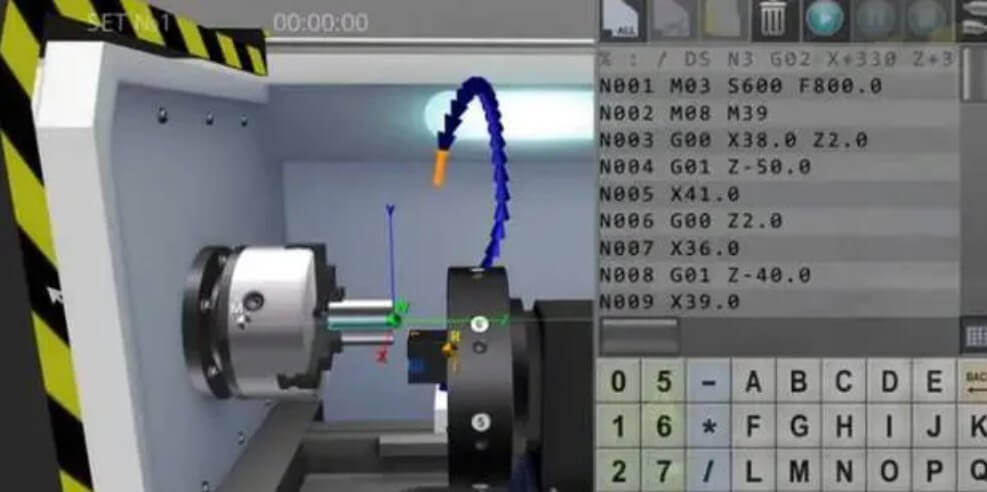
3.Significant advantages of CNC automatic in mechanical machining
(1) High precision:
CNC automatic uses computer control systems to accurately instruct and ensure that the relative position of the tool and the workpiece is accurate, thereby achieving high-precision machining and meeting high-standard customer needs.
(2) High efficiency:
CNC machine tools with a high degree of automation can reduce human intervention, achieve fast and continuous machining, greatly improve production efficiency, and shorten production cycles.
(3) Strong flexibility:
CNC machine tools can quickly adjust programs according to different processing requirements and are suitable for processing a variety of materials and shapes, which enhances the flexibility and adaptability of production.
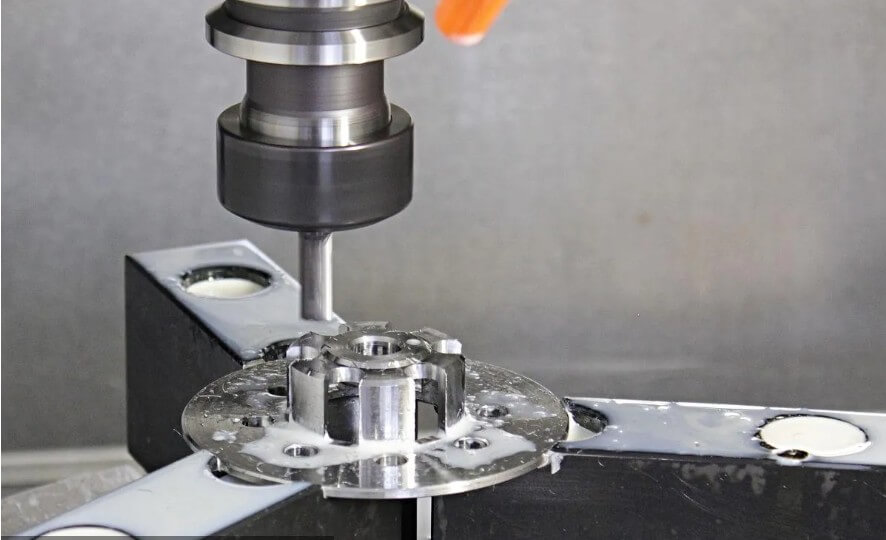
(4) Reduce labor costs:
Through automated processing, the dependence on skilled workers is reduced, labor costs are reduced, and errors caused by human operation are reduced.
(5) Improve product quality:
The high-precision processing capability of CNC machine tools helps to improve the dimensional accuracy and surface quality of finished products and enhance product competitiveness.
(6) Wide application:
In the fields of aerospace, automobile manufacturing, etc., CNC machine tools can process complex parts, ensure their performance and durability, and expand the application scope of mechanical processing.
4.Application and performance of CNC automatic in manufacturing industry
(1) Aerospace field
CNC technology is widely used in the processing of aircraft structural parts and engine parts, and can achieve high-precision and complex shape processing, such as thin-walled parts, integral structural parts, etc. The accuracy can usually reach 0.001mm, meeting the strict performance requirements of aviation parts.
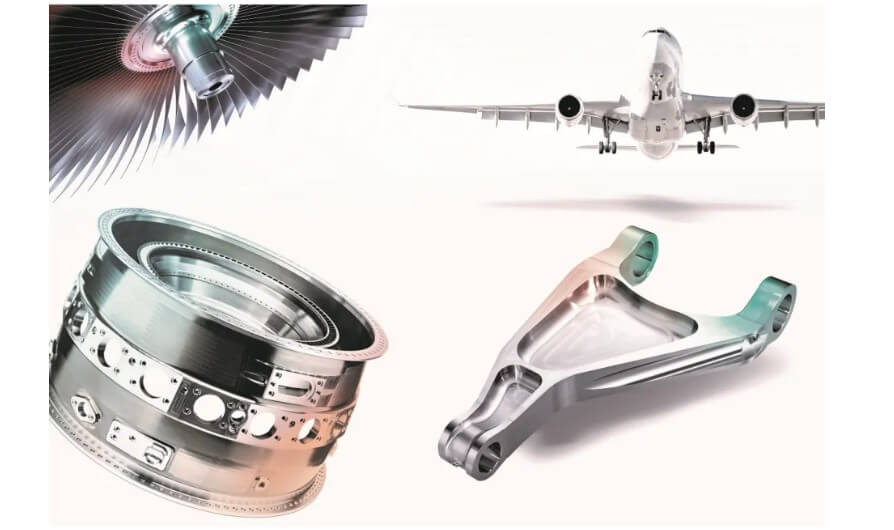
(2) Automobile manufacturing field
In the mass production of automobile parts, CNC machine tools are used to process key parts such as engine cylinders, crankshafts, and gearboxes. The processing accuracy can reach 0.01mm, ensuring the interchangeability and overall performance of parts.
(3) Mold manufacturing field
CNC machining occupies an important position in mold manufacturing and can process high-precision injection molds, stamping molds, etc. The accuracy can reach 0.005mm, and it can handle complex curved surfaces and cavity structures.
(4) Electronic manufacturing field
It is used to produce precision parts for electronic products, such as mobile phone parts and computer accessories. The accuracy can reach 0.002mm, and it can process miniature and high-precision parts to meet the development trend of lightweight and high-performance electronic products.
(5) Medical equipment manufacturing field
In medical equipment manufacturing, CNC technology is used to process high-precision parts such as artificial joints and surgical instruments. The accuracy can reach below 0.001mm, ensuring the reliability and safety of medical equipment.
5.Current status and future trends of CNC automatic technology
(1) Current status
CNC automatic programming technology has been widely used. Through computer numerical control and CAD/CAM software, efficient and accurate machine tool control can be achieved.
At present, CNC systems are developing towards high integration, high resolution and miniaturization, which improves processing efficiency and precision.
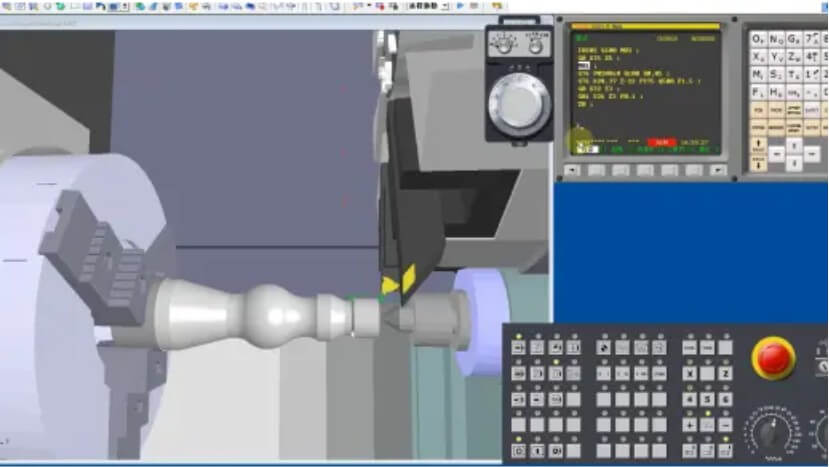
(2) Future trends
High precision: CNC systems will achieve nano-level processing and improve processing precision.
High speed: Rapid travel and cutting feed speed will be further improved, shortening processing time.
Intelligence: Integrate vision, touch and logic control technologies to enable machine tools to have autonomous decision-making capabilities.
Networking: Through the Internet of Things technology, remote monitoring and management of machine tools can be achieved.
Modular design: Product diversification and functional specialization meet the specific needs of different users.
6.Conclusion
From automatic tool change to intelligent programming, the progress of each CNC automatic technology is driving the manufacturing industry towards a more efficient and intelligent direction.