CNC automatic tool changer: efficient tool selection and precise tool change
CNC automatic tool changer plays a vital role in modern manufacturing. With the rapid development of the manufacturing industry, the requirements for production efficiency and machining accuracy continue to increase, and CNC automatic tool changers have emerged as the times require. This technology can significantly improve processing efficiency, reduce manual operations, and ensure the continuity and stability of the processing process. It is an indispensable part of modern CNC machine tools.
1.Composition and working principle of CNC automatic tool changing device
(1) Tool magazine types and characteristics
One of the core components of the CNC automatic tool changer is the tool magazine. Depending on its structure and application scenarios, the tool magazine can be divided into various types such as disc tool magazine, chain tool magazine, and grid box tool magazine. The disc-type tool magazine has a simple structure and is suitable for small machine tools; the chain-type tool magazine has a large capacity and is suitable for large machining centers; the grid box-type tool magazine has a large capacity and is highly efficient.
(2) Type and working principle of tool changing manipulator
Tool changing manipulator is the key equipment for automatic tool change. Common types of manipulators include single-arm manipulators and double-arm manipulators. They are controlled by preset programs to select appropriate tools from the tool magazine and install them on the spindle quickly and accurately.
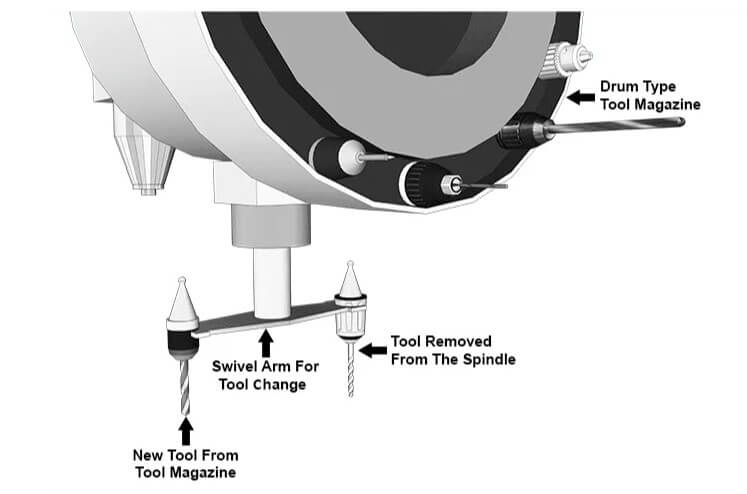
(3) Control system of CNC automatic tool changer
The control system of the CNC automatic tool changer is mainly composed of PLC (programmable logic controller). The PLC is responsible for receiving instructions from the CNC (computer numerical control) system, controlling the rotation of the tool magazine, the movement of the manipulator and the status of the spindle, ensuring that the tool changing process is completed quickly and accurately.
2.Detailed overview of tool magazine types of CNC automatic tool changer
(1) Disc tool magazine:
The tool can be placed axially, radially, or diagonally along the spindle, with the axially installed structure being the most compact. When the tool magazine capacity is large, a magazine structure can be used. At present, a large number of tool magazines are installed on the top or side of the machine tool column, or they can also be installed on a separate base. The disc type tool magazine has a simple structure and is suitable for situations where the tool magazine capacity is small.
(2) Chain tool magazine:
The tool capacity is larger than that of the disc type, and the structure is more flexible and compact. It often changes tools axially. The tool holder at the tool changing position can be protruded to facilitate tool changing. In addition, the lengthened chain method can be used to increase the capacity of the tool magazine, and the folding and rewinding method can be used to improve space utilization. When a large tool capacity is required, a multiple chain belt structure can be used.
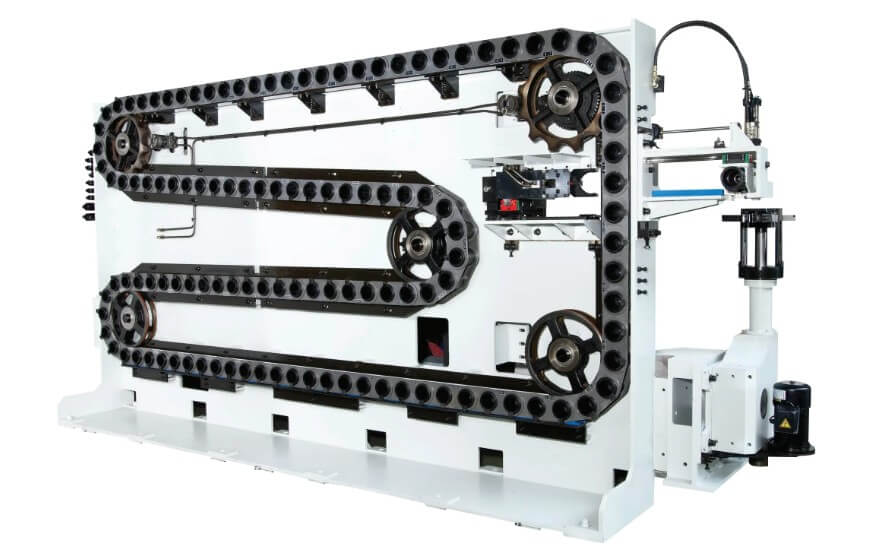
(3) Grid box tool magazine:
The tools are arranged in several straight rows. The tool-picking manipulator that moves vertically and horizontally completes the tool selection movement. The selected tools are sent to the fixed tool holder at a fixed tool-changing position, and the tool-changing manipulator exchanges the tools. This kind of tool magazine has high space utilization and large tool magazine capacity.
3.Tool selection method of CNC automatic tool changer
(1) Sequential knife selection:
Insert the tools used into the tool holder of the tool magazine according to the predetermined process sequence, and move them to the tool removal position in sequence when using them. This method does not require tool identification, but each tool cannot be reused in the process. In order to meet the processing needs, only the number of tools and tool magazine capacity can be increased, which reduces the utilization rate of tools and tool magazines. You must be very careful when installing tools and install them in order.
(2) Optional cutting tools:
The required tools are selected arbitrarily according to the requirements of the program instructions. The tools do not need to be arranged in the processing order of the workpiece in the tool magazine and can be placed arbitrarily. Each tool is coded, the tool magazine rotates during automatic tool change, and each prop is recognized by the “tool identification system”. Tools can be reused, the number of tools can be smaller, and the size of the tool magazine can also be slightly smaller.
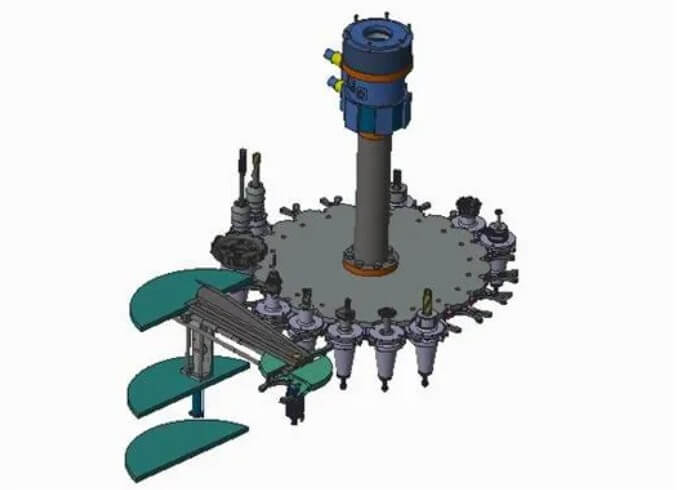
4.Detailed overview of manipulator types of CNC automatic tool changer
The method of tool exchange using a manipulator is the most widely used. The manipulator has great flexibility in tool change and can reduce tool change time. The form and method of tool change are less restricted.
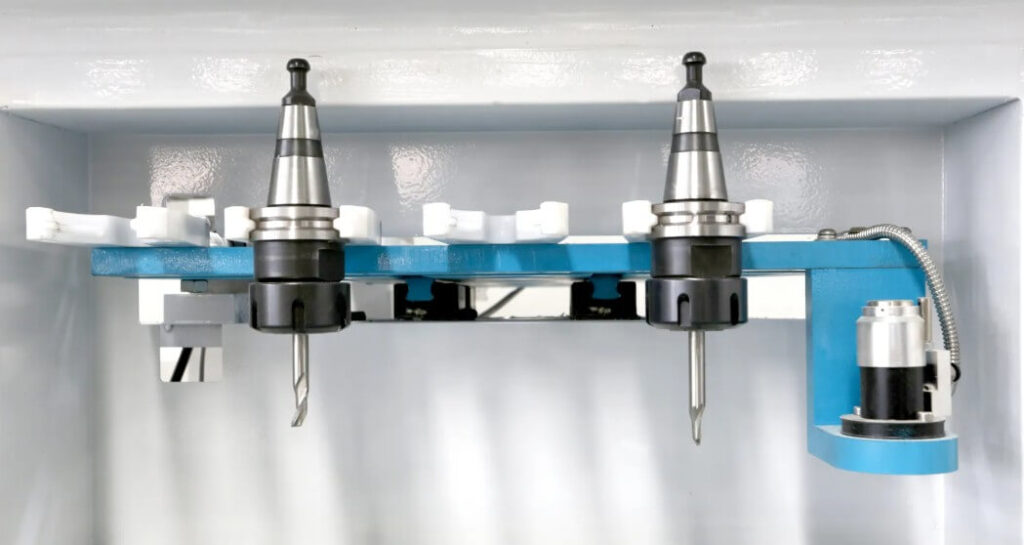
(1) Single-arm single-claw rotary manipulator:
The arm of this type of manipulator can rotate at different angles for automatic tool change. There is only one clamping claw on the arm. Whether it is on the tool magazine or on the spindle, this clamping claw can be used to load and unload tools, so the tool changing time is reduced. longer.
(2) Single-arm double-claw swing manipulator:
There are two clamping jaws on the arm of this type of manipulator. The two clamping jaws have different tasks. One clamping jaw only performs the task of removing the “old tool” from the spindle and returning it to the tool magazine. The other gripper performs the task of taking out the “new tool” from the tool magazine and sending it to the spindle, and its tool change time is less than that of a single-claw rotary manipulator.
(3) Single-arm double-claw rotary manipulator:
This type of manipulator has a clamping claw at each end of the arm. The two clamping claws can simultaneously pick up the tool from the tool magazine and the spindle. After rotating 180 degrees, the tool can be returned to the tool magazine and loaded into the spindle at the same time. The tool changing time is shorter than the above two single-arm manipulators, and it is a commonly used form.
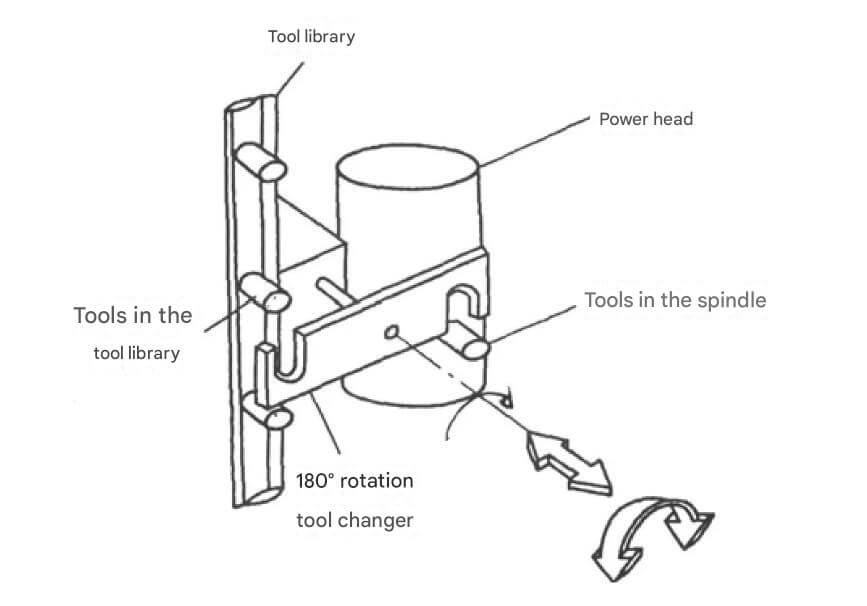
(4) Double manipulator:
This type of manipulator is equivalent to two single-claw manipulators that cooperate with each other to perform automatic tool changes. One manipulator retrieves the tool from the spindle and returns it to the tool magazine; the other manipulator takes out the “new tool” from the tool magazine and loads it into the machine tool spindle.
5.Tool exchange process of CNC automatic tool changer
Taking a single-arm double-claw rotary manipulator as an example, the tool exchange process is as follows:
(1) When the CNC device issues a tool change command, the manipulator takes out the tool to be changed from the tool magazine.
(2) The manipulator moves to the spindle position, removes the old tool from the spindle, and loads the new tool into the spindle at the same time.
(3) The manipulator returns the old tool to the tool magazine and completes a tool change.
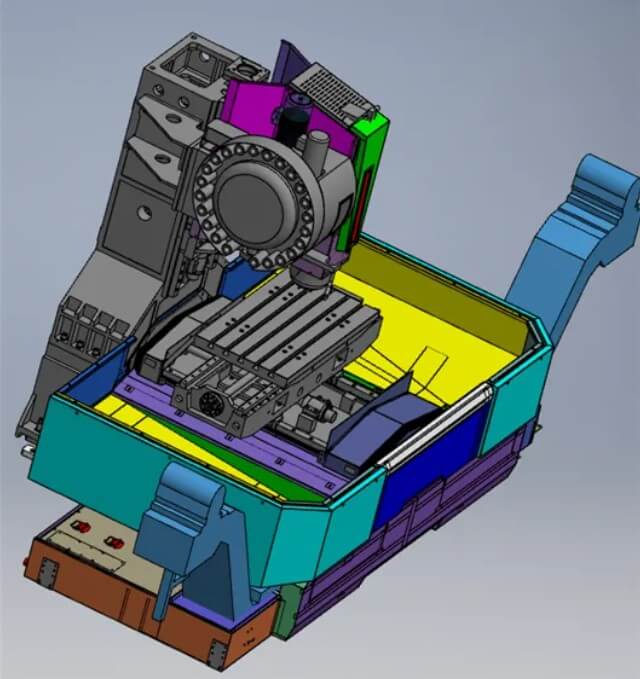
6.Overview of the control system details of the CNC automatic tool changer
(1) Control system
The control system of CNC automatic tool changer usually includes hydraulic system and electrical control system. The hydraulic system provides power to the manipulator, and the electrical control system is responsible for tool selection and positioning. Tool identification technology is one of the key technologies of CNC automatic tool changer. Commonly used tool identification methods include coding ring identification and tool holder coding identification.
(2) Tool identification method
Coding ring identification is to install equally spaced coding rings on the pull rod at the rear end of the tool holder, which are fixed by locking nuts. Tool holder coding identification is to code each tool holder, the tool is also coded, and the tool is placed in the tool holder that matches its number. When changing the tool, the tool magazine rotates so that each tool holder passes through the tool reader in turn until it is found. Specified tool holder.
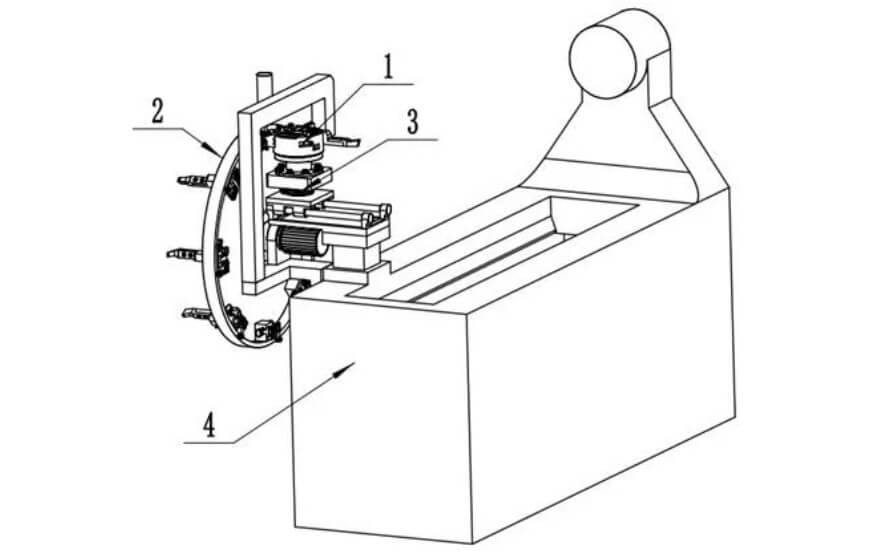
7.Analysis of key technologies of rapid CNC automatic tool changing device
(1) Design and manufacturing of cam tool change mechanism
Cam tool changer mechanism is widely used in CNC machine tools due to its high efficiency and reliability. The design of this mechanism is complex and requires precise calculation and processing of the working surface of the cam to ensure accuracy and smoothness during tool change.
(2) Optimized layout of tool magazine and tool changing mechanism
The layout of the tool magazine and tool change mechanism has a significant impact on tool change efficiency. Optimizing the layout can reduce the moving distance and time of the robot, thereby increasing the speed of tool change. For example, using a turret with tool magazines arranged around the spindle can significantly shorten tool changing time.
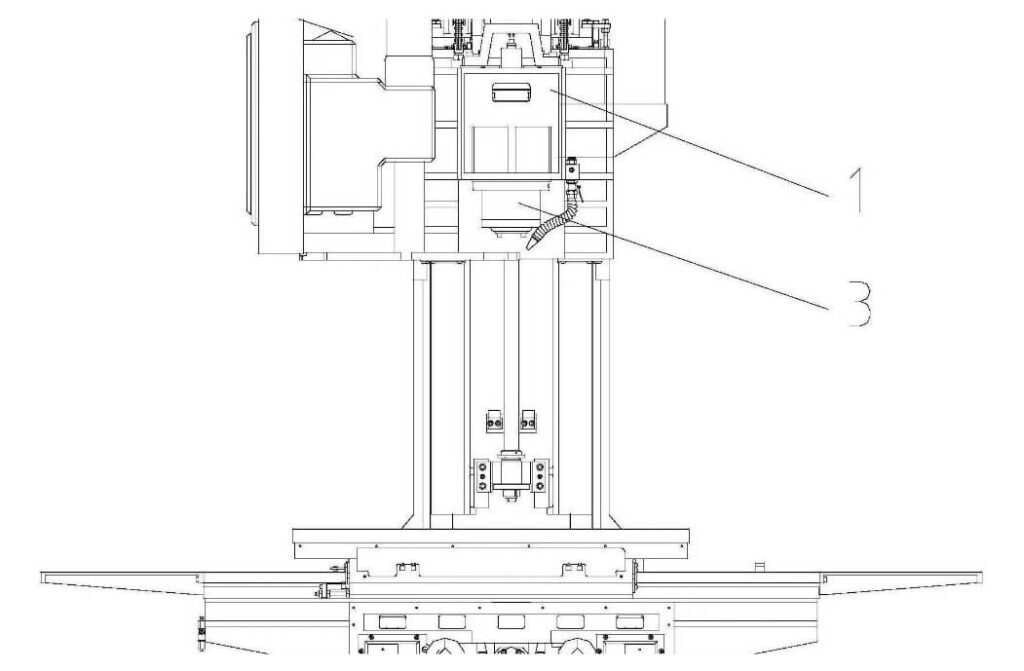
(3) Application of high-speed spindle and HSK tool holder
The application of high-speed spindle and HSK tool holder is one of the key technologies to improve the tool changing speed.
HSK tool holder is a common lightweight tool holder. Its short tapered shank structure is not only light in weight, but also has a short tool extraction and insertion stroke. With its high precision and quick locking characteristics, HSK tool holders are suitable for the rapid tool change needs of high-speed machining centers.
(4) Development of multi-spindle tool changing technology
Multi-spindle tool changing technology is a new technology developed in recent years. It allows simultaneous or sequential tool changes on multiple spindles, greatly improving production efficiency, especially in large or complex machining tasks.
8.Control strategy and optimization of CNC automatic tool changer
(1) PLC-based control system design
In the CNC automatic tool changer, PLC plays a core control role. Through the optimized design of the PLC program, precise control of the tool changing process can be achieved, reducing tool changing time and improving system reliability.
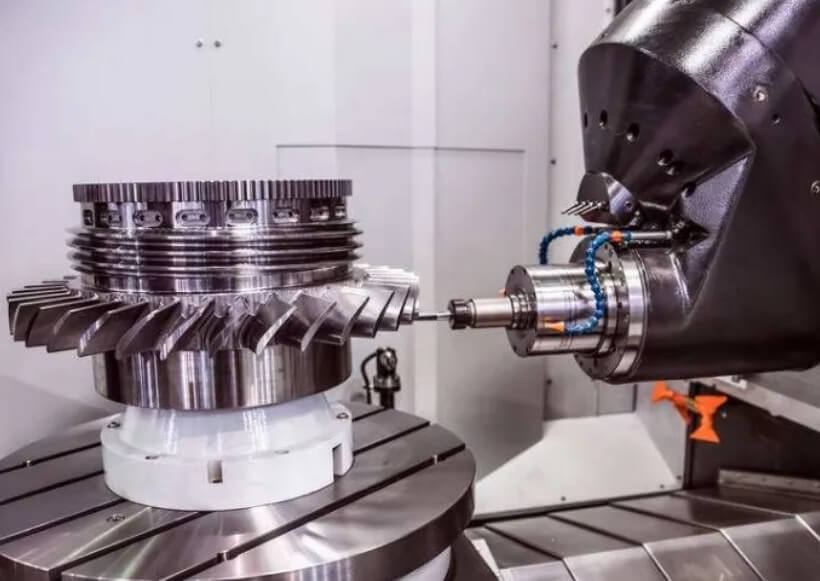
(2) Automated control of tool selection and exchange
The selection and exchange of tools are key links in the automatic tool change system. Through automated control, the system can automatically select the appropriate tool according to the needs of the machining task and quickly exchange it, thereby reducing downtime.
(3) Timing optimization and control logic of tool changing process
Optimizing the timing of the tool changing process can significantly improve tool changing efficiency. By precisely controlling the time sequence of each action and reducing unnecessary waiting and idling time, the tool changing process can be ensured to be fast and smooth.
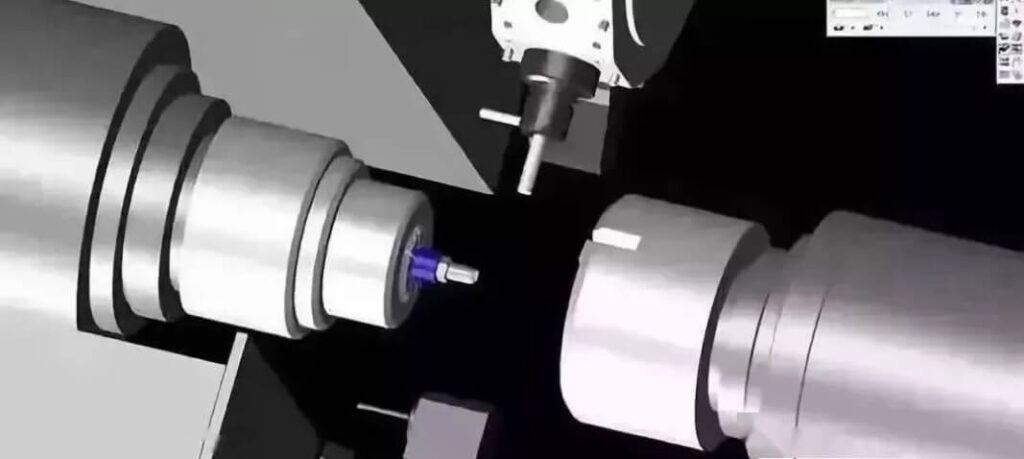
(4) Fault diagnosis and maintenance strategies
Effective fault diagnosis and maintenance strategies are key to ensuring the stable operation of CNC automatic tool changers. By monitoring the system status in real time and discovering and handling potential problems in a timely manner, the failure rate of the system can be reduced and the service life of the equipment can be extended.
9.Application case analysis of CNC automatic tool changer
(1) Application in automobile manufacturing industry
In the automobile manufacturing industry, CNC automatic tool changers are widely used in the processing of automobile parts. Through an efficient tool changing system, the production cycle can be significantly shortened, the processing accuracy of parts can be improved, and the needs of mass production can be met.
(2) Application in aerospace manufacturing industry
In the aerospace manufacturing industry, CNC automatic tool changers are used to process high-precision, complex-structured parts. Due to the extremely demanding material and design requirements of these components, automatic tool changing systems ensure continuity and accuracy of the machining process.
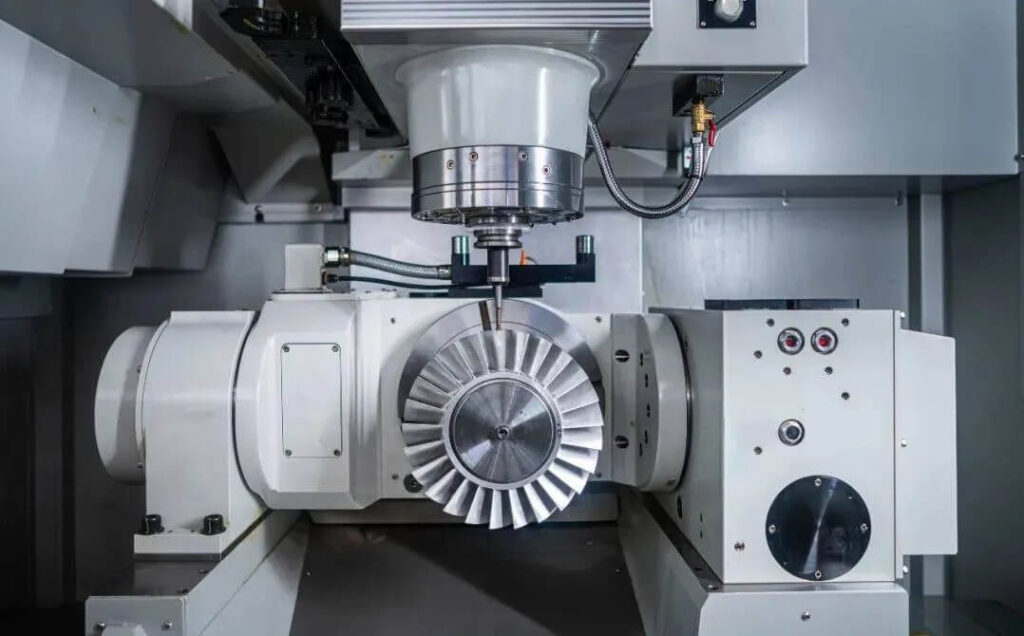
(3) Application in mold processing
In the field of mold processing, CNC automatic tool changers also play an important role. Complex mold processing requires frequent replacement of different types of tools, and the automatic tool changing system can significantly improve processing efficiency and mold quality.
10.Summary
The CNC automatic tool changer greatly improves the processing efficiency and accuracy of the machine tool, reduces auxiliary time, and reduces errors caused by multiple installations of workpieces. The tool magazine, manipulator and tool identification system are the core components of the CNC automatic tool changer, and their performance directly affects the overall performance of the CNC machine tool. With the continuous advancement of technology, CNC automatic tool changing devices will be more accurate, faster and intelligent, providing stronger support for the development of modern manufacturing.