The Ultimate Guide to CNC End Mill Selection
This article aims to explain the basics of CNC end mill science while answering simple questions you may have: Which CNC end mill should I use on my CNC machine?
1.What is a CNC end mill?
Selecting the right CNC end mill before starting up your CNC machine can be a fairly complex task. There are many variables that come into play, such as CNC end mill length, geometry, profile type, material, and several trade-offs must be considered: performance, cost, surface finish, tool life.
What exactly is a CNC end mill? Is it like a drill? This is a common question because the terminology is often confused, but the answer is no. Drills are designed to penetrate directly into the material and create only holes, while CNC end mills can cut sideways into the material and create slots or profiles.
Additionally, most CNC end mills are designed to center cut, which means they can also penetrate into the material, which makes them more versatile than drills.
There are three main factors that will influence your choice:
- What kind of shapes do you want to mill (2D contours, 3D shapes, holes…)?
- What kind of material do you want to mill?
- What are your goals in terms of performance and surface finish while maintaining an acceptable cost and staying within the capabilities of your CNC machine?
Answering these questions will help you determine the required tool geometry based on the type of project, the material to be cut and the desired surface finish. So let’s dive into the theory and then answer these questions with some concrete examples.
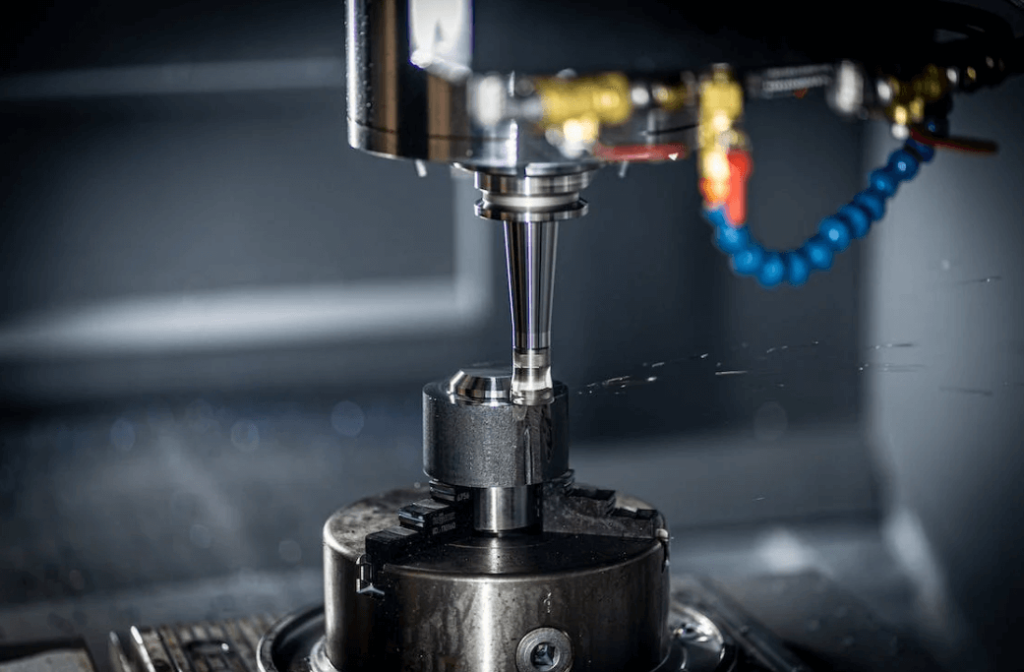
2.Main characteristics of CNC end mills
Below are explained the main characteristics used to describe CNC end mills. In addition to these geometrical characteristics, CNC end mills are characterized by their type, number of flutes, material (and coating).
Thus, in a classic catalog, the above CNC end mill would be described as:
- Type: Flat End
- Number of Flutes: 4
- Material: Solid Carbide
- Shank Diameter: 6mm
- Cutter Diameter: 6mm
- Overall Length: 50mm
- Flute Length: 22mm
- Helix Angle: 45°
Each of these features directly affects how the CNC end mill behaves during machining operations and the cutting possibilities in terms of performance and shape.
1) What size CNC end mill should I use?
Let’s say you want to mill a very deep groove in a tall component. You need a long tool to be able to machine the bottom without the spindle arbor colliding with the material stock.
Therefore, the length of the CNC end mill will depend on how deep it must penetrate the material. A concept related to this observation is called “stickout”. It is defined by the distance from the end of the tool holder to the tip of the CNC end mill.
Also, keep in mind that the depth of cut should never exceed the flute length of the CNC end mill. If the depth of cut exceeds the flute length, the chips will not be removed properly, heat will build up, and there is a risk of tool damage.
At this point, it seems wise to buy the longest CNC end mill possible so that it can be used flexibly in more situations, right? This is not the case, because the greater the overhang, the less rigid the tool. If the overhang is too large and you over-process it, the cutting forces will bend it, which is called “tool deflection.”
Tool deflection can actually be very problematic because it causes:
- Chatter, which is vibration caused by the relative movement between the workpiece and the cutting tool;
- Poor surface finish with ripples, mainly caused by chatter;
- Inaccurate tolerances on machined parts;
- Shortened tool life due to bending fatigue.
In short, shorter CNC end mills are more rigid and cost less. So save extra-long CNC end mills for operations that really need them.
2) Shank and tool diameter
The diameter of the tool will directly affect the profile you cut. Let’s say you want to make a box and assemble it using 90° interlocking joints.
Since your tool is a cylinder with a certain radius, it is not possible to do this. In fact, the tool will leave a circular profile at each internal corner with a radius equal to half its diameter. The larger the diameter of your CNC end mill, the larger the radius of this circular profile.
To overcome this problem, CNC operators use what is called “dogboning”. Dogbone angles describe the shape of the corners that extend outside the cutting area to form a perfect 90º angle.
On the other hand, increasing the diameter of your tool has two main advantages.
First, it makes your tool more rigid, which will allow you to make deeper cuts while minimizing tool deflection. In fact, the rigidity is much greater, because a 2x increase in diameter will make it 16x more rigid.
Secondly, it improves your MMR (Material Removal Rate) because the CNC end mill can remove more material per unit time as it moves inside the material, allowing you to optimize certain operations and complete the same work faster.
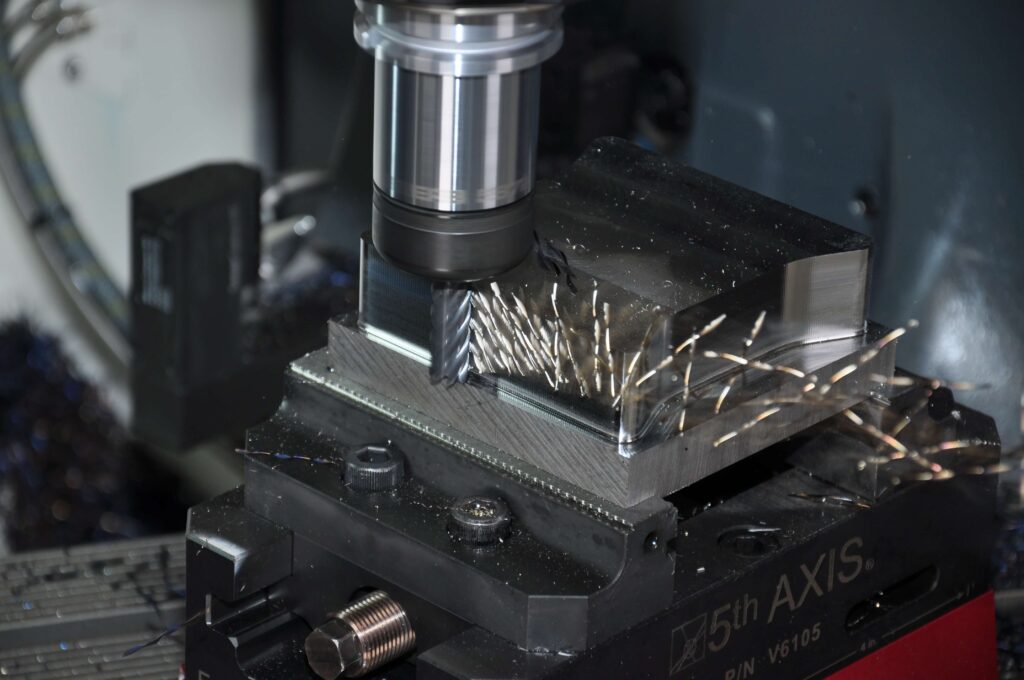
3) How many flutes should I choose?
Chip flutes are deep spiral grooves that form and evacuate chips. They are part of the structure of a CNC end mill and are used to create sharp cutting edges (sometimes called “teeth”).
The number of flutes on a CNC end mill is a critical parameter that depends primarily on the material you are cutting and the capabilities of your machine.
In fact, the number of flutes on a CNC end mill will affect:
- The feed rate of the machine
- The surface finish of the work
- The tool’s ability to clear chips
Feed rate is indeed directly related to the number of chip flutes on a CNC end mill: if you increase the flutes, you must increase the feed rate or reduce the spindle speed to maintain a constant chip load. Therefore, depending on the speed capabilities of your CNC machine and spindle, you may have to choose a CNC end mill with fewer or more chip flutes.
Second, having more flutes on a tool can make the cut smoother, but it also leaves less room for the chips to evacuate. This may be overlooked if you are cutting soft materials, but it can be completely ignored if you are cutting materials such as aluminum.
The reason is that aluminum produces very large chips compared to other materials. Therefore, when a CNC end mill is cutting in a hole or slot, its flutes provide a crucial path for the chips to evacuate.
This is why it is recommended to use 2- or 3-flute CNC end mills for aluminum, as they have more room for chips than 4-flute CNC end mills, where the chips will gradually clog, overlap the tool’s cutting edge, and eventually break.
In summary, fewer flutes are best for chip evacuation, while more flutes produce a smoother surface finish.
4) Should my helix angle be higher or lower?
General CNC end mills typically have a helix angle of about 30°. Increasing the helix angle will reduce cutting forces as well as the heat and vibration generated during milling. Therefore, CNC end mills with larger helix angles tend to produce a better surface finish on the workpiece.
Unfortunately, this comes with a trade-off. CNC end mills become weaker and cannot withstand large cutting depths at high feed rates. Therefore, milling cutters with a smaller helix angle are stronger, but they produce a poorer surface finish.
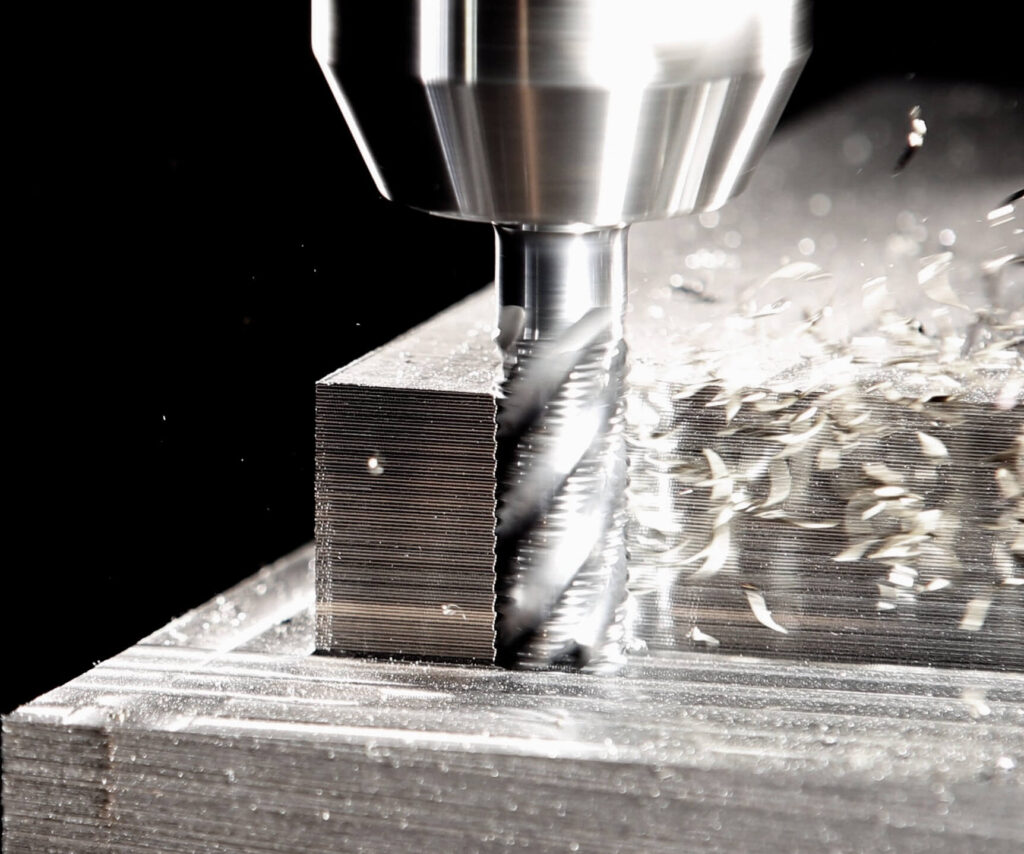
3.There are different types and shapes of CNC end mills
There are as many types of CNC end mills as there are possible cutting operations: profiling, contouring, slotting, countersinking, drilling… Here is a brief overview of the main CNC end mills.
- Square CNC end mills are the most common CNC end mills and can be used for many milling applications, including slotting, profiling and plunge cutting.
- Radius CNC end mills have slightly rounded corners, which helps to evenly distribute cutting forces, prevent damage to the CNC end mill and extend its service life. They can produce flat-bottomed grooves with slightly rounded inner corners.
- Roughing CNC end mills are used to quickly remove large amounts of material during heavy-duty operations. Their design produces almost no vibration, but has a higher surface roughness.
- Tapered CNC end mills are center-cutting tools that can be used for plunge cutting and are designed to machine beveled grooves. They are commonly used for die castings and molds.
- Ball nose mills have rounded tips and are used to mill 3D shapes or circular grooves.
- T-slot CNC end mills can easily cut precise keyways and T-slots to create workbenches or other similar applications.
- Straight groove CNC end mills have a zero-degree helix angle. They are ideal for machining materials where the lifting effect of the spiral grooves may cause undesirable results, such as wood, plastics, and composites. For these materials, straight grooves minimize edge wear and provide a better surface finish than spiral universal CNC end mills.
As the CNC mill rotates the mill clockwise, the spiral direction of the groove determines whether the chips are ejected toward the top or bottom of the workpiece. Upcut CNC end mills are the most traditional CNC end mills, and they pull the chips away from the material, which is a very important function for most milling operations in many different materials.
It has a disadvantage if you want to cut laminated materials because it leaves a poor surface finish on the top of the workpiece. The advantage of a down-cut CNC end mill is that it pushes the chips down, leaving a cleaner cut on the top, but it also wears down the bottom edge.
Combine up-cut and down-cut and you have a compression cutter where the bottom half of the flute length is carved one way and the top is carved the other way.
This feature makes them a great choice for cutting plywood, composites, and laminates. Try using it to cut a sheet of plywood in one go and you should get cleaner edges on both sides.
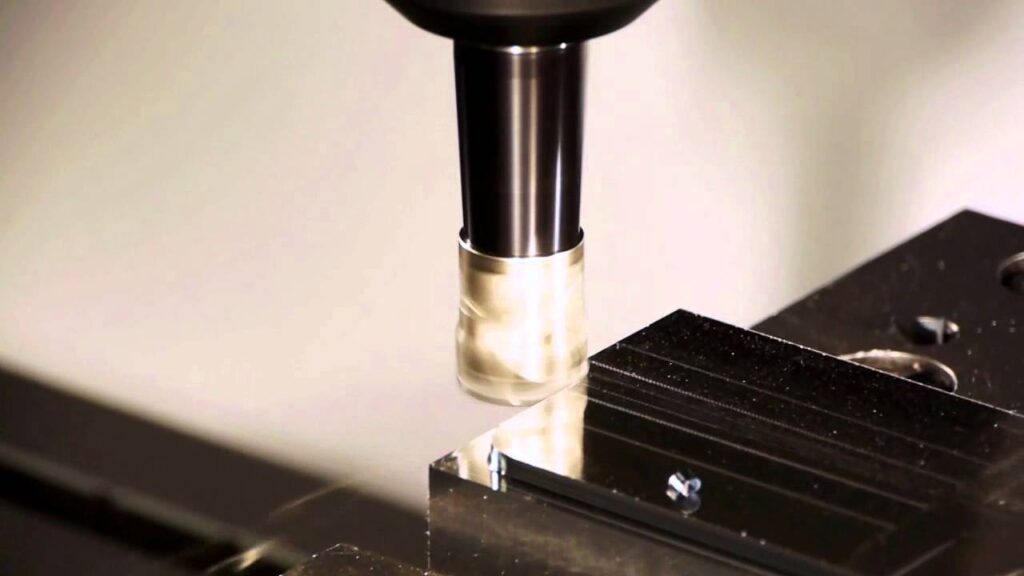
4.How to Choose the Right CNC End Mill Material
This section could take a whole article, so let’s briefly discuss the two main materials that cutting tools are made of: high-speed steel and carbide.
- High-speed steel (HSS) is the least expensive of the two, has good wear resistance, and can be used to mill a variety of materials such as wood, metal, etc.
- Coated carbide CNC end mills are more expensive than HSS CNC end mills, but they are more rigid and can run 2 to 3 times faster than HSS. They are also extremely heat resistant, so they are also suitable for milling harder materials.
So, are carbide CNC end mills worth the extra money? Of course they are. Since they run much faster than HSS, they will greatly increase your machine productivity. They are also more durable and have a longer tool life, making them worth the investment.
Another easy way to improve the performance of your CNC end mill is to add a quality coating. The most common coating is TiAlN (titanium aluminum nitride), which allows you to cut 25% faster on average without spending too much money.
If you don’t care too much about performance, then go for a carbide CNC end mill with a diameter of 8 mm or less. Consider getting a larger tool with HSS to save some money, as the larger diameter can compensate for the rigidity of the tool.
Also, if you are just starting out with CNC milling, don’t forget that you will probably make mistakes and damage some CNC end mills until you get it right, so it’s best to use an HSS CNC end mill.
If you are looking for an experienced CNC machining manufacturer, Xavier is your ideal choice. The Xavier team is well-equipped to provide high-quality CNC machining solutions. If you need more information or to discuss your machining needs with us, please feel free to contact us.