CNC Machining Aerospace Parts: Everything You Need to Know
The quality and durability of machined and aerospace components are put to the test every time they break through the clouds at 30,000 feet.
Precision CNC Machining aerospace parts are made up of thousands of machined parts and are very complex to manufacture. Take the Boeing 747, for example, which consists of more than 6 million parts and takes up to 5,500 hours to manufacture. With such complexity, maintaining strict industry standards can be challenging.
1.The Role of CNC Machining Aerospace Parts in the Aerospace Industry
Computer numerical control (CNC) machining uses computer-controlled cutting tools, such as end mills and drills, to remove material from a workpiece to shape an aircraft component.
CNC machining is one of the few manufacturing processes that can provide the unique structure and high precision, uniformity, and efficiency required to economically produce such parts compared to the machining capabilities of a standard machine shop. Given the complexity and variety of modern aircraft parts, the aerospace industry relies heavily on CNC machining services.
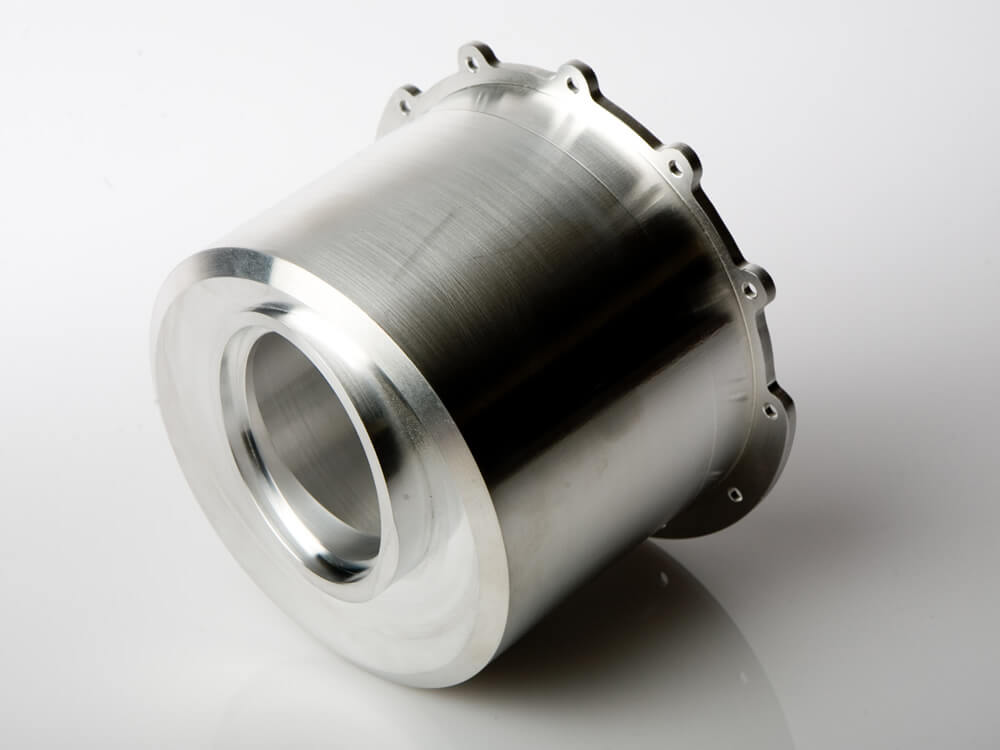
2.Types of CNC machining aerospace parts
CNC machining provides the impetus for many of today’s leading aerospace companies. From using high-performance polymers to create strong yet lightweight plastics, to designing and producing complex specialty parts with tight tolerances and low surface finish, meeting the fast-paced demands of aerospace innovation is challenging.
This is where CNC machining aerospace applications come into play. While the capabilities of CNC machining are very powerful, no two properties other than strength and weight dictate the quality of the materials used when CNC machining aerospace parts.
1) Lightweight Metal Parts
Since strong metals are required for the functional structure of aircraft, it is challenging to find metals that are light enough to not affect fuel efficiency, yet resilient enough to withstand the tremendous forces and temperature changes encountered in flight.
Therefore, aerospace companies often use titanium, copper, and brass alloys instead of heavier metals such as stainless steel. Because titanium is 50% lighter than steel and nearly 30% stronger, it is widely used in aerospace mechanical parts.
Another popular metal widely used in aircraft parts is aluminum or aluminum alloys. Although aluminum is only half as strong as titanium, it is an easily machined metal and more cost-effective, making it ideal for manufacturing a wide range of aircraft components.
2) High-Performance Plastics
Polymer materials such as PTFE, PCTFE, and PAI are often used in aerospace applications because they offer significant engineering design advantages, such as specific strength properties (which can save 20% to 40% weight), lower thermal expansion properties, and the ability to meet stringent dimensional stability requirements.
In addition, polymer plastics are impact-, wear-, and vibration-resistant, and are lighter than metals, which is why they are often used in aircraft interior components such as:
- Bearings
- Interior wall panels
- Aircraft doors
- Ventilation ducts
- Seats and service trays
- Wire ducts
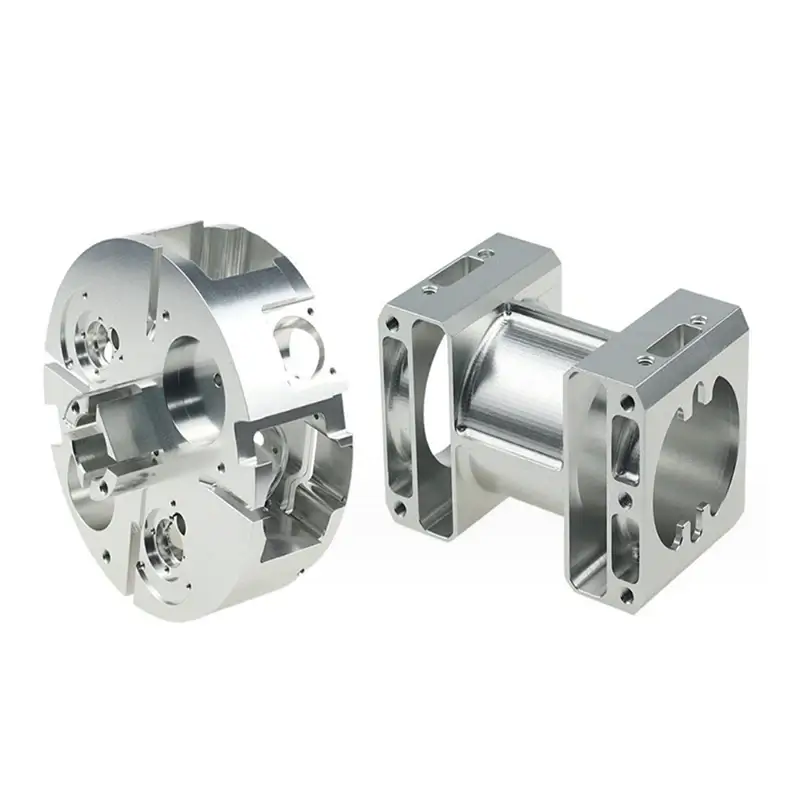
3.How CNC machining is used in the aerospace sector
The benefits of CNC machining are not limited to the production of aerospace end-user parts. For example, without CNC machining, aerospace research and development would not be able to move so quickly because without CNC machining, it would be impossible to derive and test new concept iterations and be able to modify them quickly.
4.Application of CNC machining aerospace parts in aviation
From manufacturing small connection modules that make up navigation systems to machining large fuel bodies, transmissions and landing gear, passenger planes, helicopters, fighter jets and cargo planes rely on CNC milling to accurately produce state-of-the-art aircraft parts.
5.CNC machining aerospace parts for space exploration
CNC machining helps companies such as SpaceX, NASA and Blue Origin design, process and manufacture aerospace parts from start to finish. Whether it is manufacturing the smallest parts of a rocket shell or a jet engine, CNC machining can provide the high precision required.
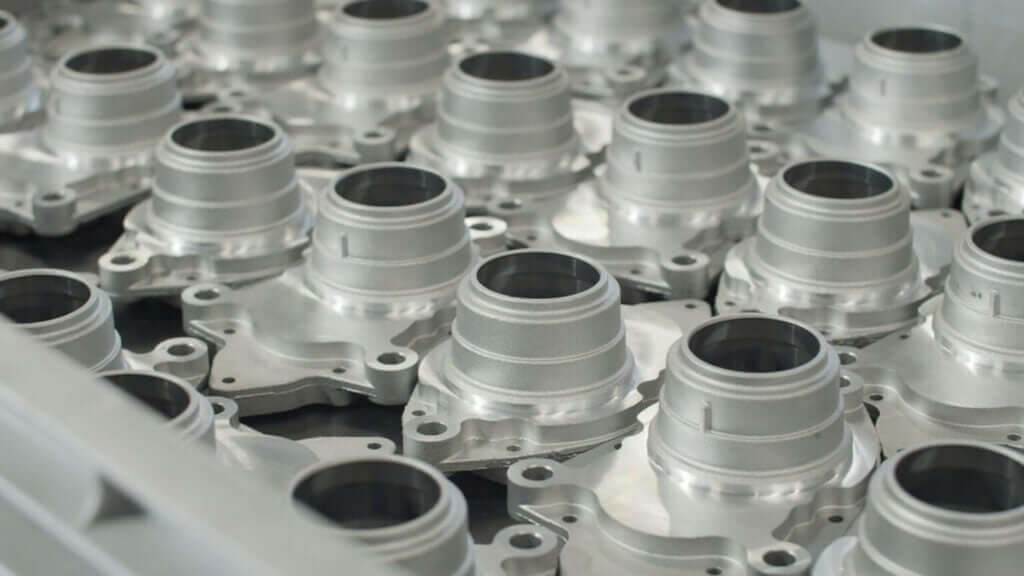
6.Solve common CNC machining aerospace parts problems
While CNC machining enables machinists to overcome many manual limitations often encountered in standard manufacturing processes, there are still problems that pre-programmed software cannot help solve.
To help reduce the challenges of CNC machining aerospace parts, here are six tips:
- Deploy simulation technology-mitigate machining errors by simulating the accuracy of G codes in CNC systems.
- Create a specialized production line – Consider modifying your manufacturing system based on product type and characteristics to enhance the process flow.
- Reduce clamping time – Improve the efficiency and reliability of your CNC machining by properly designing fixtures and minimizing preparation steps.
- Invest in scalability – Increase your machining output by investing in high-speed milling machines and other Swiss machining tools.
- Learn about all configuration tools – Maximize your aerospace machining potential by gaining a deep understanding of the full range of machining capabilities supported by your CNC system.
- Maintain industry standards – Quality control certifications such as AS9100 Revision D, ISO 9001 2015, and ITAR help ensure that machined parts meet or exceed industry standards.
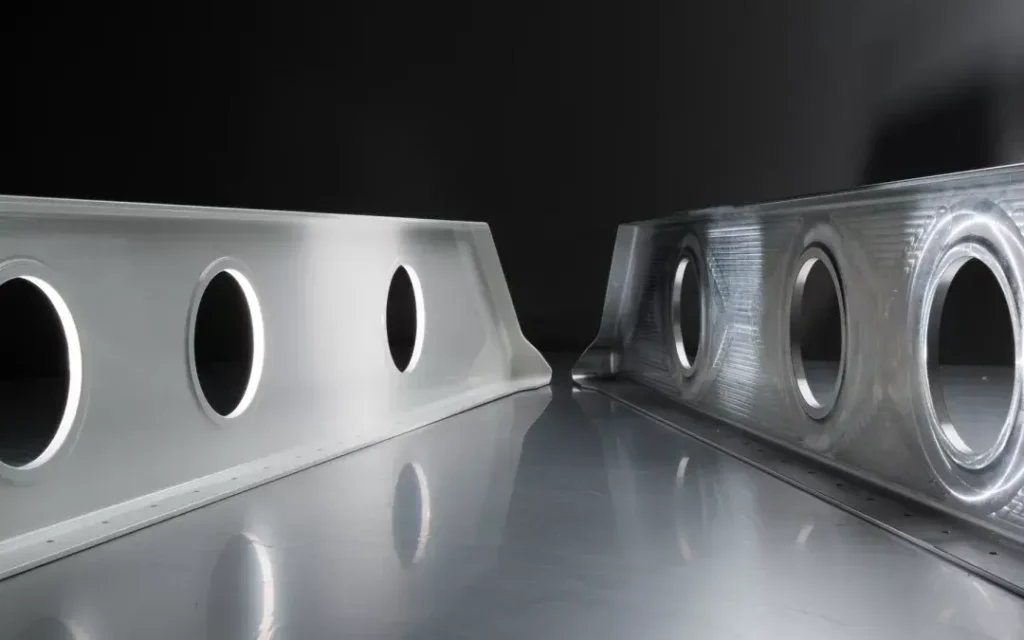
7.Reach new heights with Xavier’s cnc machining aerospace parts
For uncompromising precision, quality, and durability, you can trust Xavier to source, design, and machine the best materials for all your manufacturing needs. To learn more about our cnc machining aerospace parts, contact us today.