Optimizing Tooling and Machining Strategies for Aerospace CNC Machining
CNC machining has become an integral part of the aerospace industry, allowing for the precise manufacturing of complex parts and components. However, this process is not without its challenges. In this article, we will explore five common challenges faced in CNC machining aerospace parts and components, and discuss potential solutions to overcome them.
Challenges of CNC Machining Aerospace Parts
One of the main challenges in CNC machining aerospace parts is the need for high precision. Aerospace parts often require tight tolerances and complex geometries, which can be difficult to achieve. To meet this challenge, manufacturers must continually optimize their tooling and processing strategies. This includes using high-quality cutting tools and implementing advanced machining techniques such as multi-axis machining and high-speed machining. These strategies all help improve accuracy and reduce errors in the manufacturing process.
Another challenge in CNC machining aerospace parts is the complexity of the materials used. Aerospace components are often made from advanced materials such as titanium, stainless steel, and composites. These materials can be challenging to machine due to their hardness and tendency to generate heat. To overcome this challenge, manufacturers can use specialized cutting tools and cooling techniques. For example, using carbide or diamond-coated tools can improve tool life and reduce heat generation. Additionally, implementing coolant systems can help dissipate heat and prolong tool life.
Cost is another significant challenge in CNC machining aerospace parts. The aerospace industry is highly competitive, and manufacturers are constantly under pressure to reduce costs while maintaining quality. One solution to this challenge is to optimize the machining process to minimize material waste and reduce cycle times. This can be achieved through the use of advanced CAM software that can generate efficient tool paths and optimize cutting parameters. Additionally, implementing automation and robotics can help reduce labor costs and improve overall productivity.
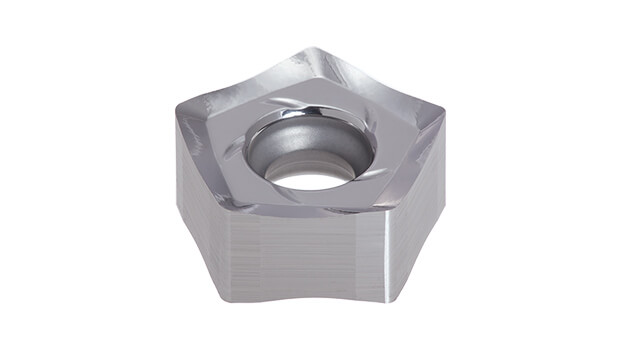
Maintaining tight deadlines is another challenge in CNC machining aerospace parts. The aerospace industry often operates on strict schedules, and any delays in the manufacturing process can have significant consequences. To address this challenge, manufacturers can implement lean manufacturing principles and streamline their production processes. This includes reducing setup times, implementing just-in-time inventory systems, and improving communication and coordination between different departments. By optimizing the workflow, manufacturers can ensure that parts are produced on time and meet the required specifications.
Lastly, quality control is a critical challenge in CNC machining aerospace parts. The aerospace industry has stringent quality standards, and any defects or deviations from specifications can have severe consequences. To overcome this challenge, manufacturers can implement rigorous quality control measures throughout the manufacturing process. This includes using advanced inspection techniques such as coordinate measuring machines (CMM) and non-destructive testing (NDT). Additionally, implementing statistical process control (SPC) can help monitor and control the machining process, ensuring that parts meet the required quality standards.
In conclusion, CNC machining aerospace parts and components comes with its fair share of challenges. However, by optimizing tooling and machining strategies, addressing material complexity, reducing costs, maintaining tight deadlines, and implementing rigorous quality control measures, manufacturers can overcome these challenges and ensure the production of high-quality aerospace components. With the continuous advancements in technology and manufacturing techniques, the aerospace industry can continue to rely on CNC machining for the precise and efficient manufacturing of aerospace parts and components.