Aluminum CNC Machining Basics
Aluminum is one of the most widely used metals in the manufacturing industry due to its excellent properties such as light weight, high strength, corrosion resistance and good machinability. CNC machining (short for computer numerical control machining) is a cutting-edge technology that has revolutionized the way aluminum parts are manufactured.
This comprehensive guide will take you through all aspects of CNC machining aluminum parts, from understanding the advantages of using aluminum to the intricacies of the CNC machining process, and provide you with valuable insights to help you make informed decisions when manufacturing aluminum parts.
1.Why choose aluminum for machining parts?
Aluminum is a versatile material that offers many advantages when it comes to machining parts. First, the lightweight nature of aluminum makes it an ideal choice for applications such as the aerospace and automotive industries where weight reduction is critical. In addition, aluminum has an excellent strength-to-weight ratio, allowing manufacturers to create strong and durable parts without compromising on weight. This feature also makes the transportation and installation of aluminum parts easier and more cost-effective.
Another notable property of aluminum is its corrosion resistance. Unlike other metals, aluminum naturally forms a protective oxide layer on its surface that prevents it from rusting or deteriorating when exposed to moisture or certain chemicals. This corrosion resistance makes aluminum parts ideal for applications in marine environments or in contact with corrosive substances.
In addition, aluminum has excellent thermal and electrical conductivity. This property makes it ideal for applications that require efficient heat transfer or conductivity, such as heat sinks, electrical housings, or components of electronic devices. Aluminum’s ability to quickly dissipate heat allows for better thermal management, preventing overheating and extending the life of the part.
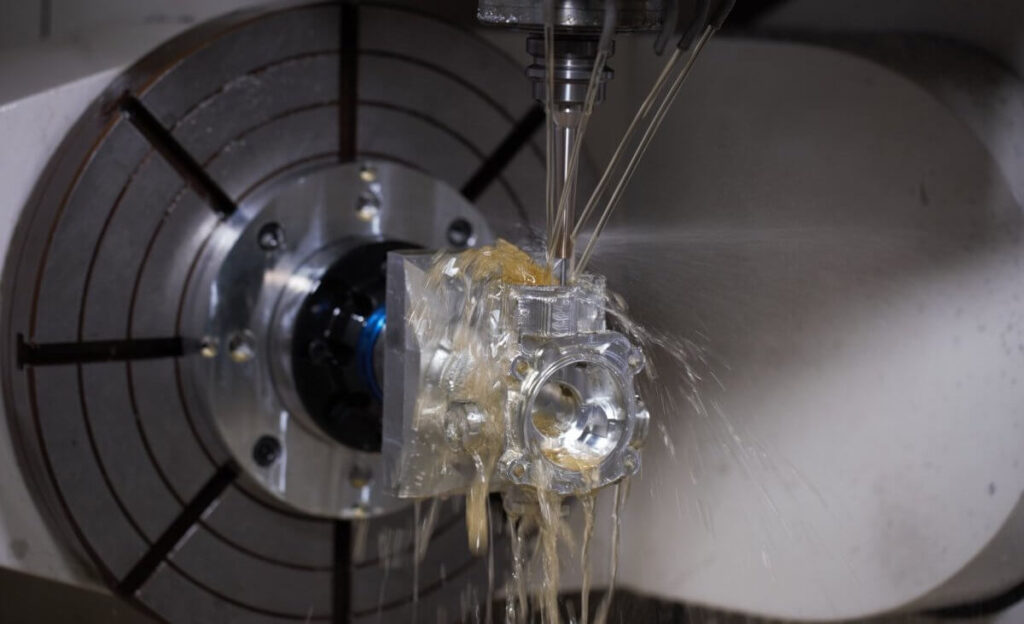
2.CNC Machining Process
CNC machining is a precise and efficient manufacturing process that uses computer-controlled machines to remove material from a workpiece to form the desired shape or form. The process involves a series of steps, including design, programming, setup, and machining.
1) Design
The first step in the CNC machining process is to design the part using computer-aided design (CAD) software. This involves creating a digital 3D model of the part, defining its dimensions, tolerances, and surface finish. The design is critical because it is the blueprint for manufacturing the aluminum part.
2) Programming
Once the design is complete, the next step is to program the CNC machine. This involves converting the 3D model into machine-readable instructions (called G-code). The G-code specifies the tool paths, feed rates, cutting speeds, and other machining parameters required to produce the desired part.
3) Setup
After programming, the CNC machine is set up by installing the appropriate cutting tools, fixtures, and workholding devices. The workpiece (usually a piece of aluminum or a sheet of aluminum) is securely clamped to the machine to ensure stability during machining.
4) Machining
Once setup is complete, the CNC machine begins the machining process. The cutting tool begins removing material from the aluminum workpiece, guided by the G-code instructions. This process involves milling, drilling, turning, and other machining operations to achieve the desired shape, size, and surface finish. During machining, an operator or the machine itself monitors the process to ensure accuracy and make any necessary adjustments.
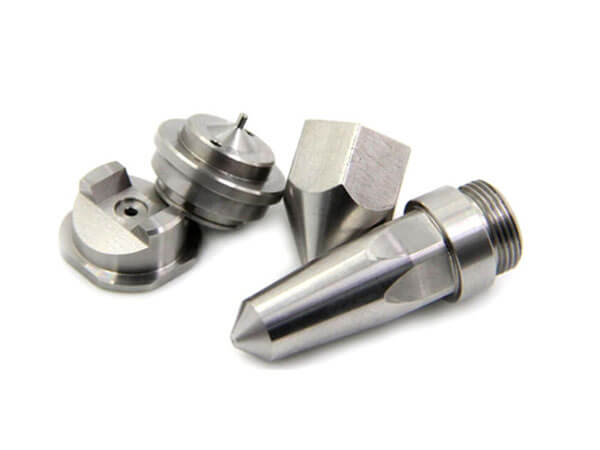
3.Advantages of CNC machining aluminum parts
When it comes to manufacturing aluminum parts, CNC machining offers a variety of advantages. These benefits include:
1) Precision
CNC machines are capable of achieving high levels of accuracy, making it easy to replicate tight tolerances and complex designs. This precision ensures that the final aluminum part meets all required specifications, minimizing the need for additional machining or manual adjustments.
2) Efficiency
Automation of the CNC machining process improves efficiency and productivity. CNC machines can run continuously around the clock with minimal supervision, which reduces manufacturing lead times and increases production. This efficiency enables manufacturers to meet tight deadlines and deliver products on time.
3) Versatility
CNC machines can perform a variety of machining operations, including milling, drilling, tapping, threading, and more. This versatility enables the production of complex aluminum parts with different shapes, sizes, and features from a single setup. This eliminates the need for multiple machines or setups, reducing time and costs.
4) Consistency
CNC machining ensures consistent and uniform results from batch to batch. Once the machining parameters are set, the CNC machine will consistently produce the same part with precise dimensions and surface finish. This consistency is critical for industries that require interchangeable parts or strict quality control.
5) Cost-effectiveness
Although the initial setup costs of CNC machining may be higher compared to traditional machining methods, CNC machining can save costs in the long run. The automation and efficiency of CNC machines reduce labor costs, minimize material waste, and reduce tooling costs. High accuracy and repeatability further reduce the need for rework or rejection, thereby improving overall cost-effectiveness.
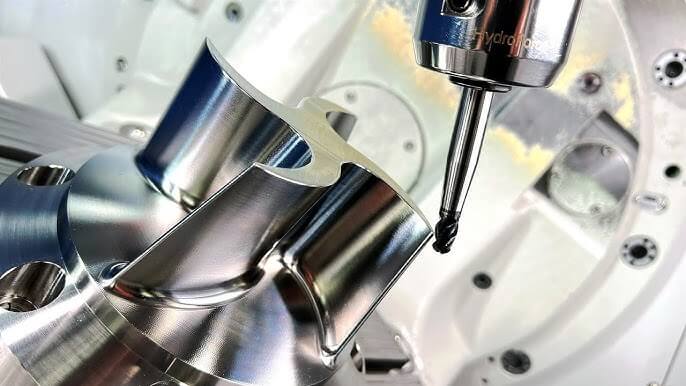
4.In Summary
Aluminum machining part technology is essential in various industries. Understanding the CNC machining process is essential. By selecting the appropriate technology for a specific application and clearly understanding the advantages of CNC machining aluminum parts, manufacturers can achieve high accuracy, efficiency, and quality in the aluminum machining process.