Introduction to CNC Machining Aluminum Parts
Over the years, CNC machining has revolutionized the manufacturing industry. With the advent of CNC machines, the production of high-precision metal parts has become more efficient, economical, and accessible. Aluminum alloys are one of the most commonly used materials in many industrial applications, including aerospace, automotive, medical, and military fields. Its unique properties, such as lightness, high corrosion resistance, and strength, make it an ideal material choice for many manufacturing projects.
In this blog post, we will explore various aspects of CNC machined aluminum parts, from design considerations to material selection, machining processes, and finishing options.
1.Design Considerations for CNC Machining Aluminum Parts
When designing parts for CNC machining, you must consider several factors that can affect the quality and performance of the final product.
1) Ensure the design is compatible with the capabilities of the CNC machine and the properties of the material
Aluminum alloys have different density, hardness, and machinability grades, which can affect cutting speeds, tool wear, and surface finish. You should also optimize the geometry of the part to reduce excessive material waste, minimize machining time, and ensure proper fixturing and clamping.
2) Tolerance requirements of parts
It refers to the degree of deviation from the design specifications that is allowed. The tolerance level of aluminum parts depends on their size, complexity, and application. For example, aerospace or medical device parts may require tighter tolerances than automotive or consumer electronics parts. You should clearly communicate the tolerance requirements with your machining supplier and consider the additional cost of achieving tighter tolerances.
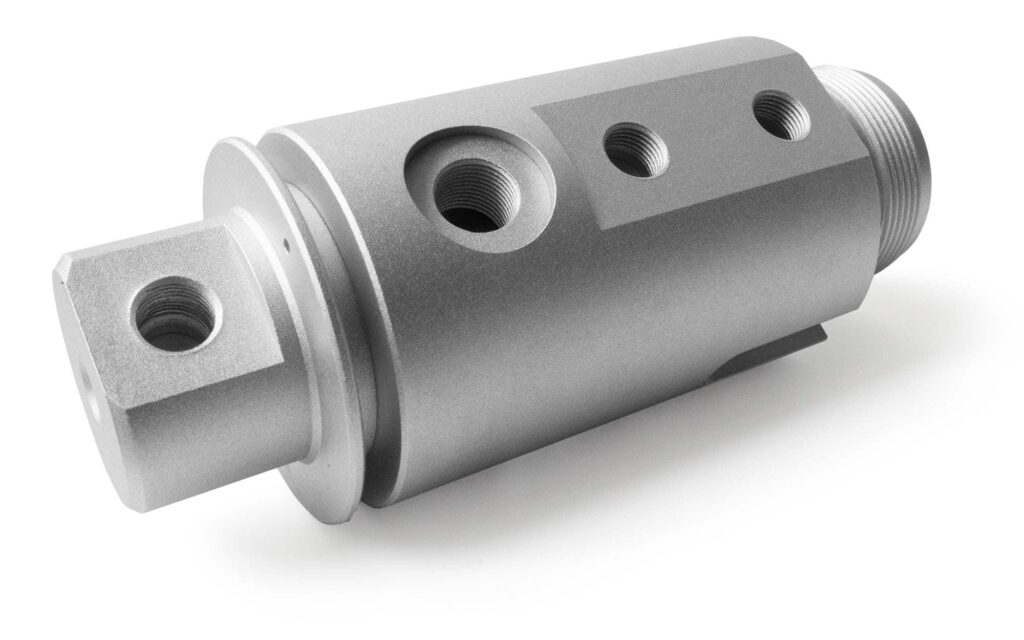
2.Material selection for CNC machining aluminum parts
Choosing the right aluminum alloy for your CNC machining project depends on several factors, such as the required strength, corrosion resistance, conductivity, and cost. The most commonly used aluminum alloys for CNC machining are 6061, 7075, and 2024. These alloys have good machinability and are readily available in various forms, such as bars, plates, and sheets.
- 6061 aluminum: is a widely used alloy with excellent corrosion resistance and weldability. It is commonly used in structural, automotive, and aerospace components where strength and weight are critical factors.
- 7075 aluminum is a high-strength alloy that is often used in the aerospace and defense industries, where durability and fatigue resistance are critical. It is also more expensive than other alloys, and its machinability is more challenging.
- 2024 aluminum is another high-strength alloy that is often used in critical aerospace and aircraft applications, such as wing skins and fuselages.
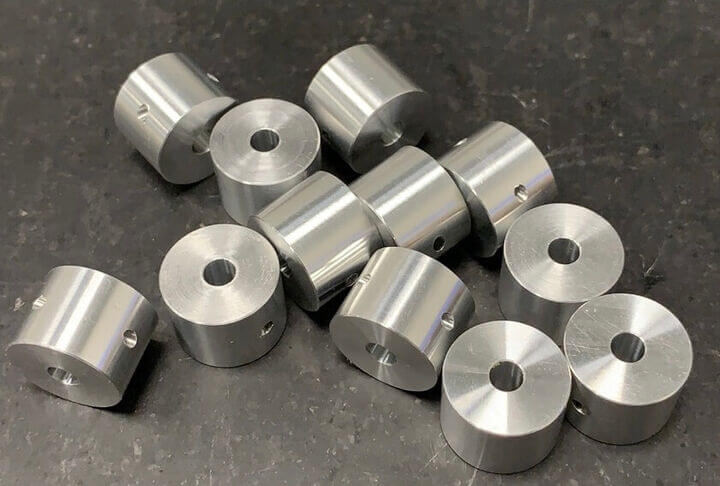
3.CNC machining processes for aluminum parts
CNC machining aluminum parts involves a variety of cutting, drilling, milling, and turning operations that require specific tools, feeds, speeds, and coolant flows. The most common CNC machining processes for aluminum parts are drilling, tapping, milling, and turning.
- Drilling involves drilling holes using special drill bits, which come in different shapes and sizes depending on the diameter and depth of the hole.
- Tapping involves creating threads on a hole using special taps that match the thread size and pitch.
- Milling involves cutting the surface of a part to remove material using a rotating cutting tool that moves along multiple axes. Turning involves spinning a part on a lathe and using cutting tools to shape the outside diameter, inside diameter, and length of the part.
4.Finishing Options for CNC Machining Aluminum Parts
After CNC machining aluminum parts, finishing operations may be required to improve their surface quality, texture, and corrosion resistance. The most common finishing options for aluminum parts are anodizing, powder coating, painting, and polishing.
- Anodizing involves an electrochemical process that forms a protective oxide layer on the surface of aluminum, making the part more durable and corrosion-resistant.
- Powder coating involves applying a dry powder to the surface of the part and then curing it in a high-temperature oven, resulting in a more consistent, scratch-resistant, and brighter surface.
- Painting involves applying a wet paint to the surface of the part, resulting in a more customizable and more aesthetically pleasing surface.
- Polishing involves buffing the surface of the part using special abrasive pads and compounds to achieve a shiny, smooth surface.
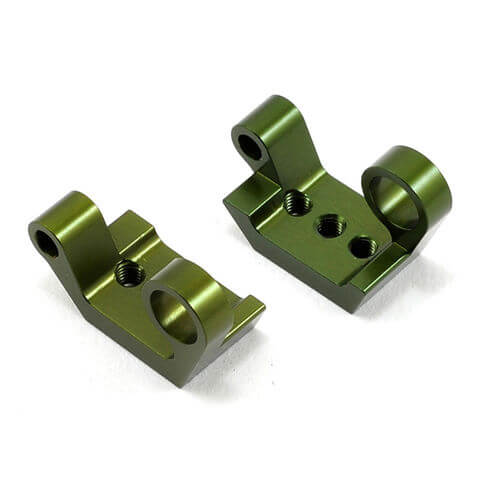
5.Conclusion
CNC machined aluminum parts require careful design considerations, material selection, machining processes, and finishing options to achieve the desired end-product quality and performance.
By working with a reliable machining supplier that has experience and expertise in CNC machining aluminum parts, you can optimize your production processes, reduce costs, and make your products more competitive in the market. We hope this comprehensive guide has helped you understand all aspects of CNC machining aluminum parts.