The Role of CNC Machining in Automotive Component Manufacturing
The automotive industry is constantly evolving, introducing new technologies and manufacturing processes to improve the efficiency and quality of auto parts manufacturing.One such technology that has revolutionized the production of auto parts is CNC machining. CNC, or Computer Numerical Control, machining is a process that uses computer-controlled machines to shape and cut materials with precision and accuracy. In this article, we will explore the role of CNC machining in automotive component manufacturing.
The Key Role CNC Machining Plays in the Production of Auto Parts
CNC machining plays a crucial role in the production of auto parts due to its ability to produce complex shapes and high-quality finishes. The automotive industry demands parts that are not only functional but also aesthetically pleasing. CNC machines can achieve this by using advanced cutting tools and techniques to create intricate designs and smooth surfaces. This level of precision is essential for components such as engine parts, transmission systems, and suspension components, where even the slightest deviation can lead to performance issues.
One of the main advantages of CNC machining in automotive parts manufacturing is the ability to produce parts in high volumes with consistent quality. Because traditional manufacturing methods, such as hand machining or casting, often result in variations in size and finish. At the same time, this may also cause compatibility issues and increase rejection rates. CNC machines, on the other hand, can also reproduce the same design repeatedly, ensuring that each part meets the required specifications. This not only reduces waste but also increases overall productivity.
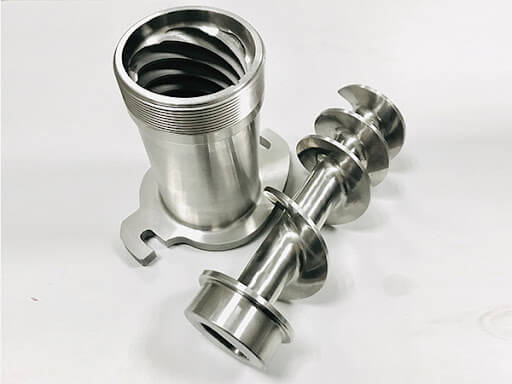
Another area where CNC machining excels in automotive component manufacturing is prototyping. Before a new car model is put into production, numerous prototypes need to be created and tested. CNC machines can quickly and accurately produce these prototypes, allowing engineers to evaluate their performance and make necessary modifications. This speeds up the development process and reduces costs associated with traditional prototyping methods.
Furthermore, CNC machining offers flexibility in terms of material selection. Auto parts need to withstand extreme conditions, such as high temperatures and vibrations. CNC machines can work with a wide range of materials, including metals, plastics, and composites, allowing manufacturers to choose the most suitable material for each component. This ensures that the final product is durable and meets the required performance standards.
In addition to its role in manufacturing auto parts, CNC machining also contributes to the overall sustainability of the automotive industry. CNC machines are designed to minimize material waste by optimizing cutting paths and reducing scrap. This not only reduces costs but also helps in conserving resources. Furthermore, CNC machines are energy-efficient, consuming less power compared to traditional manufacturing methods. This aligns with the industry’s efforts to reduce its carbon footprint and promote sustainable practices.
In conclusion, CNC machining has become an integral part of automotive component manufacturing. Its ability to produce complex shapes, consistent quality, and quick prototyping makes it an ideal choice for the automotive industry. With its flexibility in material selection and contribution to sustainability, CNC machining continues to play a vital role in shaping the future of auto parts production. As the automotive industry continues to evolve, CNC machining will undoubtedly remain at the forefront of innovation and efficiency.