CNC Machining Cost: How to Calculate and Reduce Its Cost?
How to calculate CNC machining cost? There are multiple factors involved in machining cost. Different machining types have different costs, among which cryogenic machining cost is relatively high. US Machining has reduced delivery time and cost without compromising quality by implementing proprietary production methods.
This article will explain the factors that increase the cost of CNC machining.
Also, what materials are available and affordable for the machine? For example, aluminum is easy to machine and costs $5-10 per pound. Likewise, steel costs $8-16 per pound. Stainless steel is expensive, ranging from $1.87 to $3.14 per pound.
Of course, plastics are slightly cheaper, with ABS ranging from $1 to $2 per pound. So this is just a basic idea.
In the following article, we will look at the cost analysis of CNC machined parts, such as design, production volume, and shop location.
1.Cost Factors in CNC Machining
CNC machining is affected by the type of CNC machine used and its capabilities, which affects its cost. Since different CNC machines excel at different tasks, their complexity is directly related to the cost of operation.
Milling machines excel at producing three-dimensional parts with a variety of features, such as grooves and even flat surfaces. They use multi-axis cutting tools that can safely remove material from the workpiece.
In contrast, lathes are specialized cutting devices that produce circular or cylindrical shapes. In addition, lathes rotate the workpiece while the cutting tool machines its exterior. In addition, the number of axes a CNC machine has affects the cost.
2.CNC Machining Cost Per Hour (Estimated)
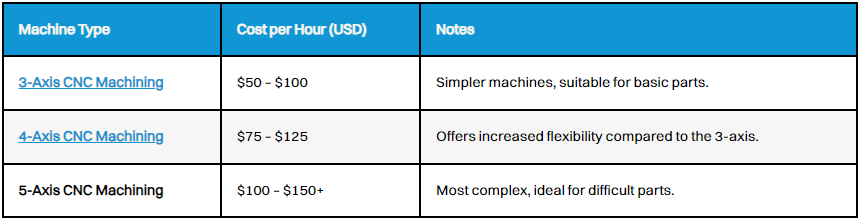
While simple 3-axis machines can only move the cutting tool in three directions, 5-axis machines offer the additional ability to rotate. This enables the tool to reach unique angles and eliminates the need for multiple setups.
While 5-axis machines offer greater room for customization, their rigidity comes with an additional cost compared to 3-axis machining processes.
3.Material Selection Impacts Overall Cost
The material you choose for your CNC machined parts can also have a surprising impact on the final cost.
There are two main reasons:
- Processing Choice
- Raw Material Cost
Think of the difference between carving wood and carving stone. Wood is easier to machine. This is the same with CNC machining. Different materials have different machinability characteristics. It refers to how easy they are to cut and shape with CNC tools.
The softer the material, the easier it is to machine, the less tool wear there is, and the faster the machining speed. Therefore, the cost of this material will be significantly reduced.
On the other hand, the harder the material, the more difficult it is to machine. The faster the tool wears, the slower the machining speed must be. This increases the overall cost of tool replacement and individual parts.
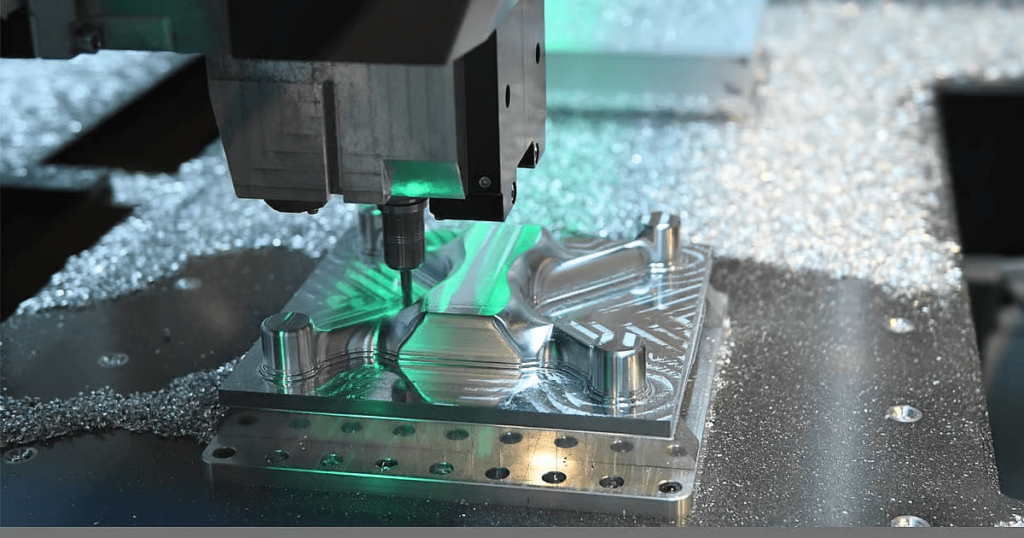
4.Raw material costs
In addition to machinability, the cost of the raw material itself directly affects the final machining cost. For example, the price of aluminum material is lower than that of stainless steel. This means that if machining factors are not taken into account, the cost of raw aluminum parts will be lower than that of stainless steel parts.
Although materials with high machinability such as aluminum are inexpensive, people will still tend to choose this material, but they must be selected based on appropriate conditions. Some applications require parts with lower machinability because they need to meet performance requirements such as strength or heat resistance.
Therefore, a good balance must be maintained between machinability, raw material cost, and the final performance of the part.
5.The impact of design on machining costs
The complexity of part design has a great impact on the final CNC machining cost.
The best way to understand this is this:
How long does it take to make a simple building block?
Obviously, carving a detailed sculpture is harder and takes more time. The same concept applies to CNC machining. Parts with complex geometry, with many features such as:
- Holes
- Pockets or slots
- Tight tolerances
All of these require more machining time and usually add significantly to the cost. Additionally, thin walls are a big problem. The minimum cutting diameter of CNC machining tools can make machining thin walls very difficult, if not impossible.
Without special techniques, it may require:
- Slower machining
- More setups
- And ultimately increased machining costs.
The good news is that you can control the impact of part complexity on cost to some extent. One major solution is Design for Manufacturability (DFM). This is a set of principles that seek to optimize designs for cost-effective CNC machining.
By designing your parts with DFM principles in mind, you can effectively reduce CNC machining costs in two ways:
- Simplify geometry – Choose the simplest possible shape for each part to reduce machining time.
- Minimize features – Minimize the number of holes or pockets, etc.
Design parts that are easier to machine and faster to machine. Reduce the number of features. Loosen tolerances as much as possible, as some dimensions may not require tight tolerances to meet system functionality.
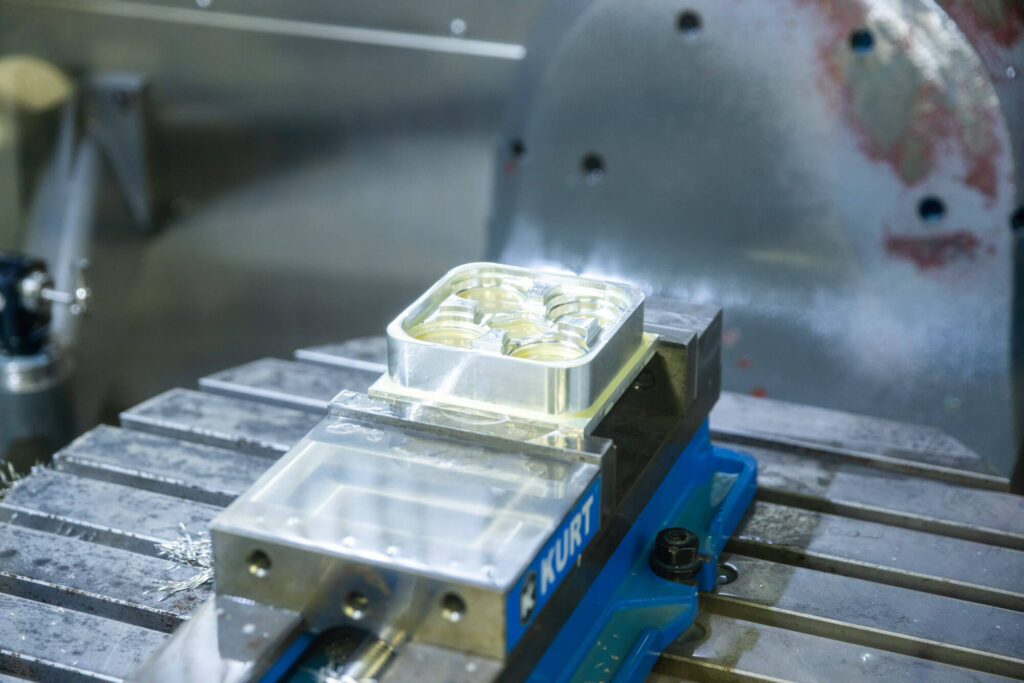
6.Production volume
The number of parts is one of the important factors that determine the cost per part. This dynamic depends on the principle of economies of scale. Similarly, economies of scale also play a role in CNC machining.
As mentioned above, every hour a CNC machine is run incurs a cost. By producing individual parts, the machine mainly produces these parts throughout the cycle.
- Machine run time
However, a machine that produces many parts at a time during the production cycle run will utilize the machine’s run time. In this way, the cost of running the machine is spread over the individual parts. This approach reduces the cost per part.
- Setup costs
The production cost can increase or decrease based on the production volume. Setup involves preparing the CNC machine to manufacture a specific part.
This includes:
- Cut path code creation
- Raw materials
- And tool calibration
However, there are recurring costs that are not related to production volume.
7.Finishing Options
Of course, not every type of machining from raw material to finished part involves CNC machining.
There are other steps that can be performed after machining to improve:
- Appearance
- Functionality
- Special properties of the part
These are called finishing operations. While they undoubtedly make the final part better, they also increase the overall cost. Each surface finishing operation requires an additional step in the production of the part. For example, additional labor, materials, and longer lead times increase the cost of machining.
8.Understanding Hourly Rates
First, you need to understand that hourly rates are not the only determinant of CNC machining costs.
Below is an overview of average hourly costs based on machine complexity.
3-axis CNC machining is generally simpler. The hourly cost is $50 to $100. 5-axis CNC machining costs are correspondingly higher than 3-axis CNC machining. These machines cost about $75 to $150 per hour.
Note: These costs are based on estimates. Actual costs may vary.
To check the final cost of CNC machining parts, consider the following checkpoints:
- Shop location
- Maintenance of the machine
- Operator experience
- The complexity of the specific project will affect the specific cost per hour.
Note that the hourly rate is only one factor that affects the total cost of the project. For example, the cost of machining a part for one hour using a 3-axis machine may be less than the cost of machining a more complex part.

9.How to calculate CNC machining costs?
I found it for you: You must be searching for a formula to calculate CNC machining costs. The actual situation is a little different. There is no one formula that can answer your question. However, you can get an idea from the following:
- CNC machining cost calculator
Estimated cost = (material cost + setup cost) + (machining time * hourly rate) + finishing cost
However, if you need a more accurate understanding of the machining cost, you should get an online quote.
For example, if you contact Yijin Hardware, you can get a free CNC machining quote by providing the following information:
- Part drawing
- Material specifications
- Required tolerances
- Required quantity
- Finishing requirements
10.Average cost of CNC machined parts: Specify material (per unit)
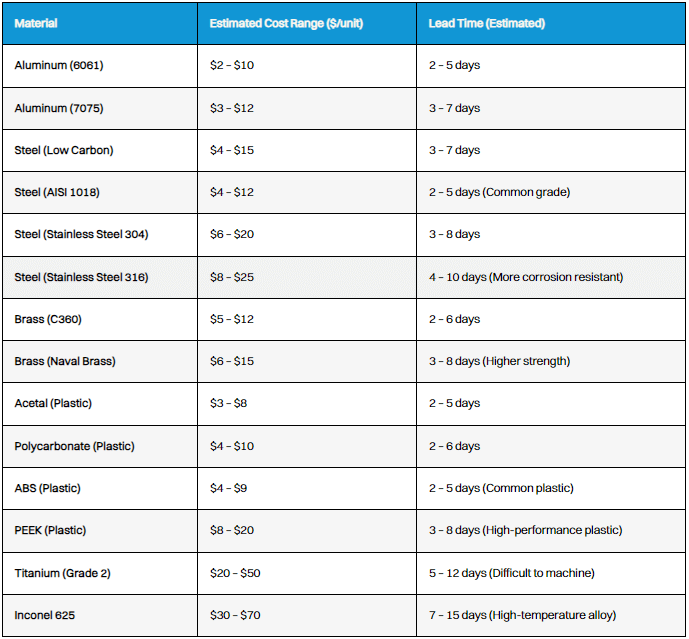
11.Cost saving strategies
CNC machining achieves unparalleled precision, but keeping costs reasonable is just as important. Fortunately, there are many strategies you can use to achieve cost-effective CNC machining. Among them is simplifying the geometry.
This means that you should ensure that:
- Your model has the fewest features
- Relax tolerances as much as possible
- The more you order at a time, the cheaper the price per unit.
You can also ensure that costs are kept down by getting quotes from other CNC machine shops. Again, quote comparisons can help you make the right decision.
12.Cost of CNC Cutting
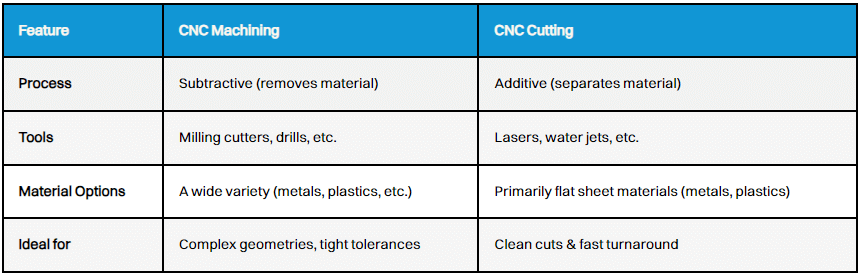
Both processes are computer-controlled and can provide parts of the desired shape, but the way they achieve this is very different. Therefore, it will be of great benefit to understand this difference. This way, you can easily choose the best way to save CNC machining costs.
13.Conclusion
To summarize the entire article, we come to the conclusion. There are several factors that are important for the final cost of CNC machining. Again, we have provided different tables to get an idea of the estimated cost. It will give you a rough idea. However, to get the most accurate price for machined parts, we recommend that you contact a reliable CNC machining company,xavier is your ideal choice. The Xavier team is well-equipped to provide high-quality CNC machining solutions. If you need more information or to discuss your machining needs with us, please feel free to contact us.