Learn All About CNC Machining Drawings
CNC machining drawings are a reliable channel of information between manufacturers and product engineers. Machining abbreviations are a set of standardized symbols and abbreviations used on engineering drawings to represent common terms and phrases. These drawings often supplement digital CAD files, conveying additional details that are not easily represented by the part’s shape.
Product teams often deal with a subtype of technical drawings called engineering drawings in prototyping and manufacturing. It often contains basic information such as required materials and surface finishes, part information, and 2D and 3D views of the part from multiple angles, including dimensions and tolerances.
This guide dives into the basics of machining drawings, their importance, and the essential elements of CNC machining drawings. You’ll also learn why you need to prepare technical drawings when sourcing parts, and the importance of precision and accuracy in these drawings.
1.What are technical CNC machining drawings?
Technical or machining drawings clearly and accurately express design ideas generated using computer-aided design (CAD) software. Machining drawings often include all necessary materials, basic dimensions, and measurements as a framework for the machining process. CAD software also helps incorporate complex shapes, intricate details, and multiple angles precisely into product designs.
In addition, technical CNC machining drawings are critical to the engineering, construction, and manufacturing industries, which require high accuracy and precision.
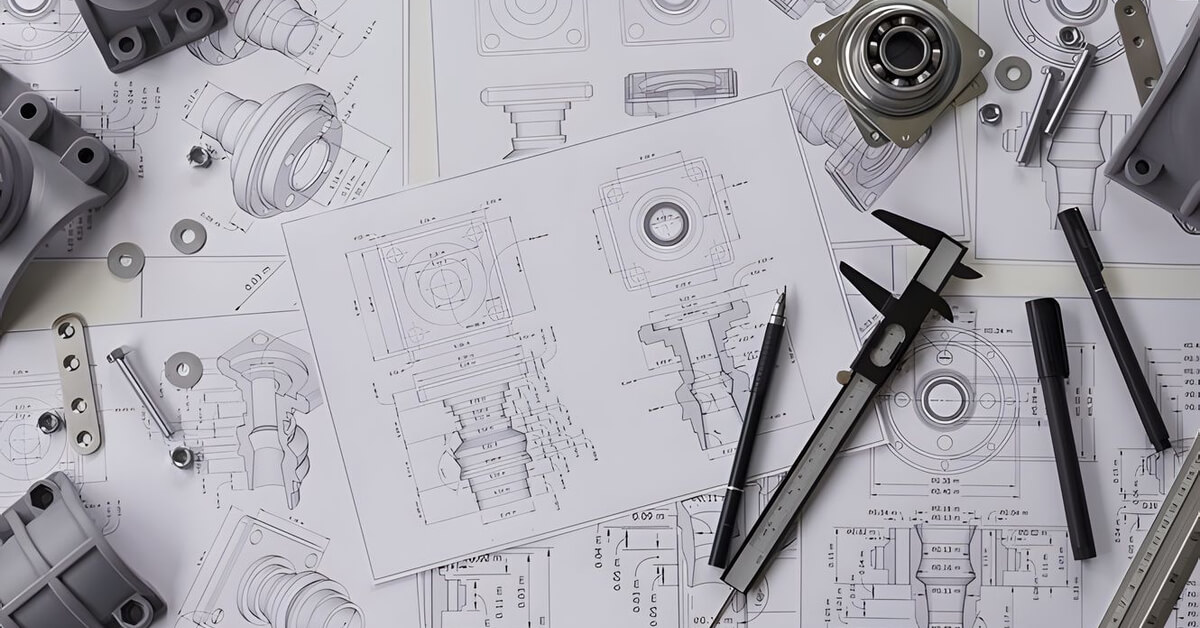
2.Basic Structure of a Technical CNC Drawing
Often, CNC machining drawings require different tools and methods to effectively create accurate diagrams, blueprints, and other visual representations of mechanical designs.
Here are some of the basic components of CNC technical drawings:
1) Title Block
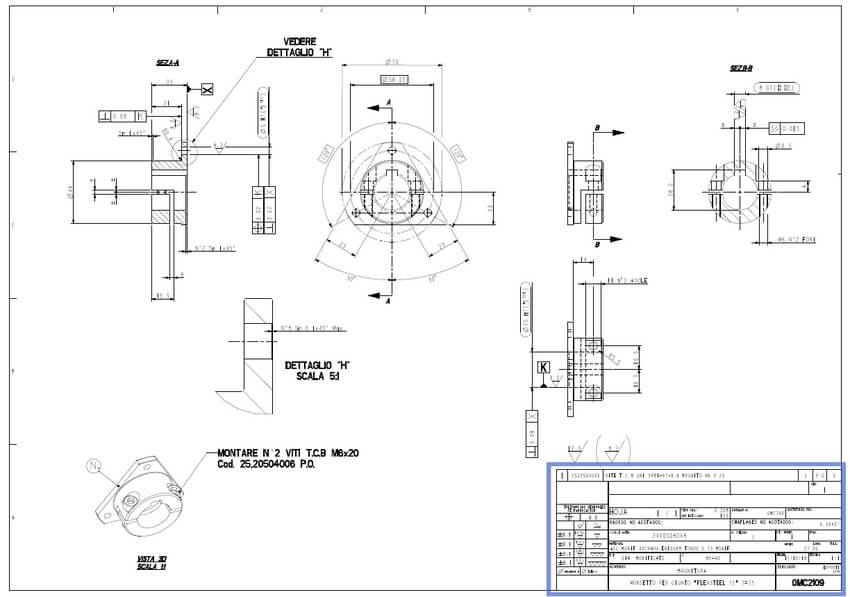
The title block provides relevant information, such as the author, title, date, and other key details about the CNC drawing. This aspect of machining drawings also includes the scale of the drawing, which is essential to ensure the accuracy of dimensions and measurements.
The information in the title block is critical to CNC machining projects, as the most insignificant errors in measurements can have a huge impact.
In addition, you can add additional notes and specifications to further aid in the interpretation and use of machining drawings.
2) Detailed Views
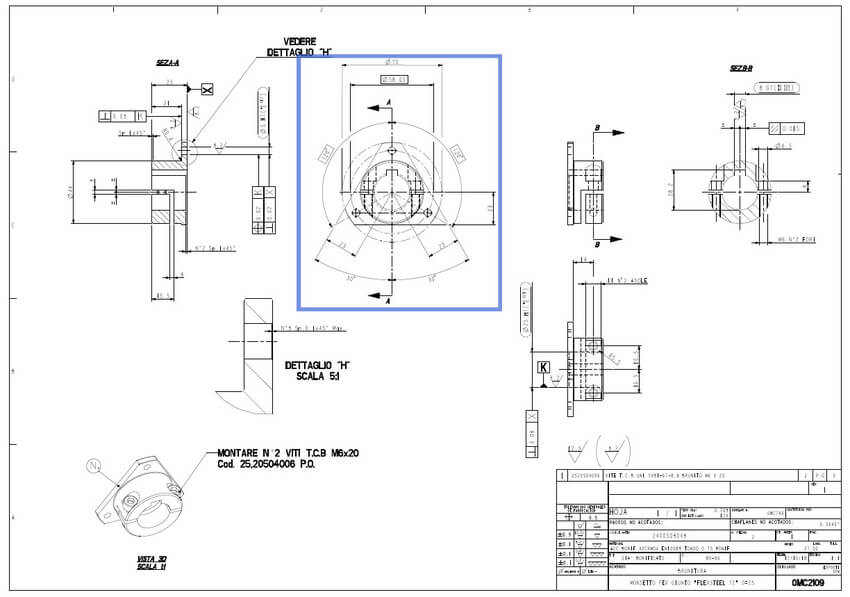
These views provide a closer look at specific features of a part or assembly, providing important information about tolerances, dimensions, and surface finish.
Since precision is critical to CNC machining, detail views allow machinists and product engineers to ensure the accuracy of every detail of the part and ensure that it meets standards.
Detailed views facilitate clear communication between product manufacturers and designers, ensuring that everyone is working toward the same goal. By adding detailed views to machining drawings, product designers can ensure that their parts are produced and meet specifications without any errors.
3) Coordinates
Coordinates are groups of letters or numbers that correspond to specific points on a plane or grid. There are two main types of coordinates that product designers typically use to make accurate and detailed designs in CNC machining drawings. These include polar coordinates and Cartesian coordinates.
Polar coordinates represent the position of an object in terms of angles and distances, while Cartesian coordinates determine the position of an object in terms of vertical and horizontal lines. These coordinates are key to machining drawings and can clearly and concisely express design ideas.
4) Isometric View
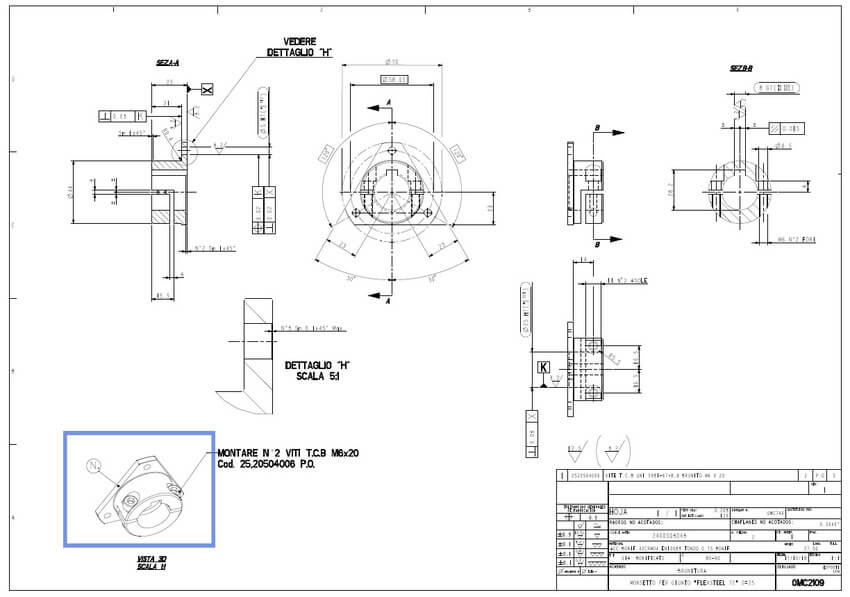
This view allows you to present your product design in 3D on a 2D description. Isometric views are very useful in situations where accuracy is critical. It helps to better understand how interlocking components assemble or fit perfectly and how they function in a larger structure or assembly.
Isometric views help save time and reduce possible errors during CNC machining. It is an essential tool in modern manufacturing because it can convey technical details and spatial relationships at the same time.
5) Orthogonal Views
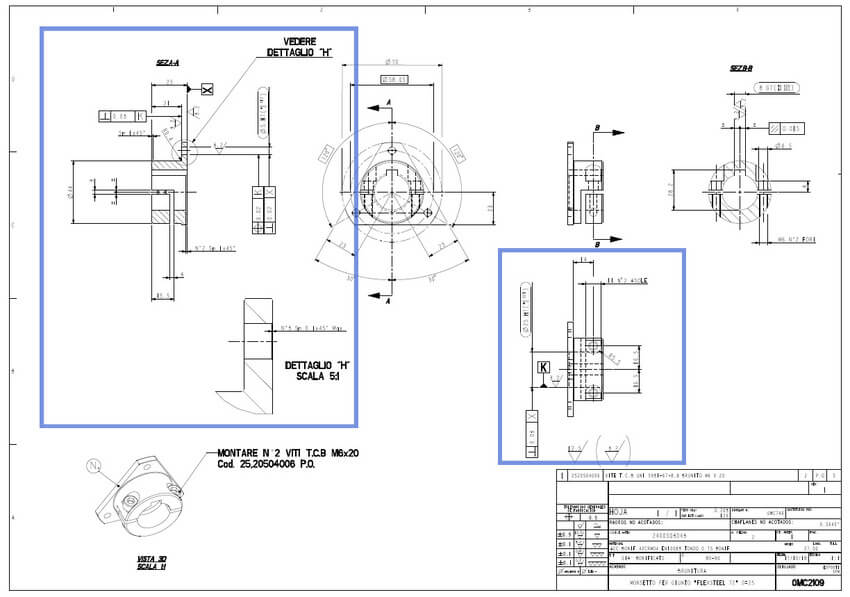
Orthogonal views provide front, side, and top views of three-dimensional objects. These views are essential for accurate CNC machining design drawings. Without these views, product designers and engineers would have a hard time communicating the critical dimensions and shapes for producing precision parts.
Likewise, these views provide important information about the location of different design features, such as slots and holes, and the overall dimensions of the machined component. CNC machines can manufacture complex parts with high accuracy and consistency using detailed orthogonal views.
6) Section Views
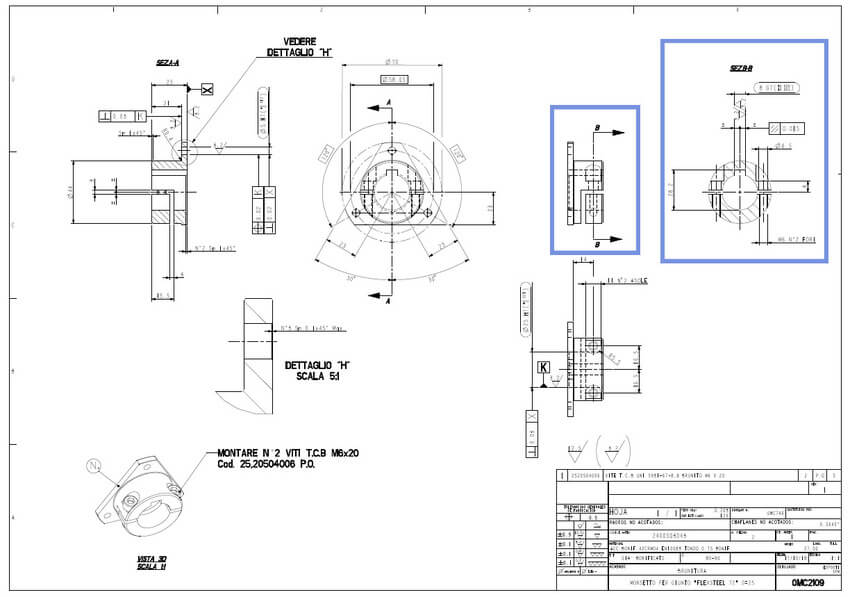
Section views help provide a better understanding of the inner workings of a part, which is essential to ensure that the part is machined accurately and efficiently. It depicts a cross-section of the part at key points to help identify potential design flaws or imperfections that could affect the function of the component.
These views help optimize the machining process and ensure that the final product meets all specifications. However, when you include section views in your machining drawings, product engineers and machinists can work together to produce high-quality, precision parts that exceed expectations.
7) Notes to Manufacturers
When drawing CNC machining drawings, it is important to include relevant instructions from the manufacturer. This helps them create the desired component accurately because it contains critical information not included in the blueprint, such as required materials, tolerance specifications, surface finish requirements, and other special instructions.
It is usually represented by symbols rather than text, such as surface finish symbols, indicating specific finishing requirements. Also, be sure to specify the number of parts required and the production schedule.
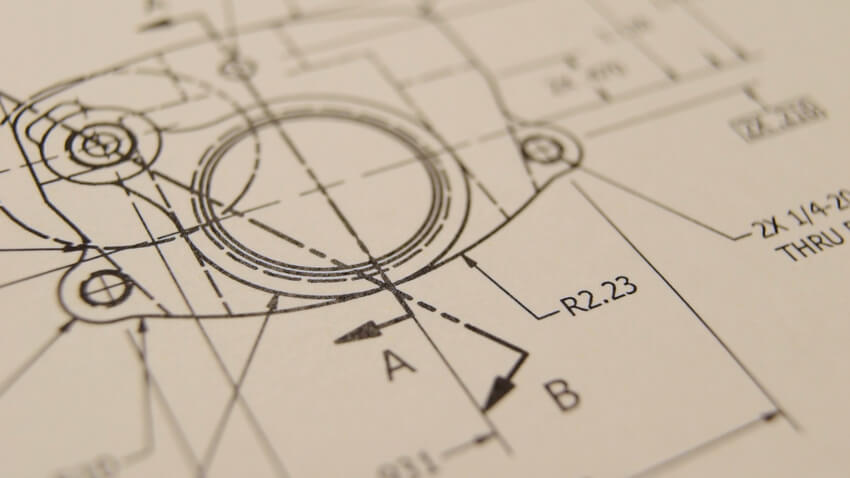
3.A Step-by-Step Guide to Preparing Machining Drawings
CNC machining drawings are the foundation of any machining process. Understanding the structure of CNC machining drawings is essential.
Here is a step-by-step guide:
Step 1: Define the most critical views and place related orthogonal views in the center of the drawing, leaving enough space between views to show dimensional details. Also, do not use redundant hidden lines to avoid cluttering and messing with the drawing.
Step 2: If the part has complex internal features and areas that are difficult to dimension, add section views or detailed views. Section views provide 2D projections that can better view complex dimensions and hidden features that may not be obvious from the outside.
Step 3: Add construction lines in all views. These construction lines typically include center marks and center mark patterns (used to indicate the center location of circular patterns or holes) and center lines (used to show axes or symmetry planes).
Step 4: Add critical dimensions to the drawing and make sure dimension lines and graphics are clearly specified on the drawing and do not cross each other.
Step 5: Specify the size, location and length of all threads. Consider using hole callouts instead of dimensioning all aspects of the hole. It specifies the diameter and depth of the hole in the case of countersunk or counterbore holes, including the depth of these features.
Step 6: Add tolerances for features that require more accuracy than standard tolerances.
Step 7: Fill in the title block and make sure all critical information and requirements beyond standard practice are listed in the additional notes. So export the drawing as a PDF file and attach it to your order when you are ready.
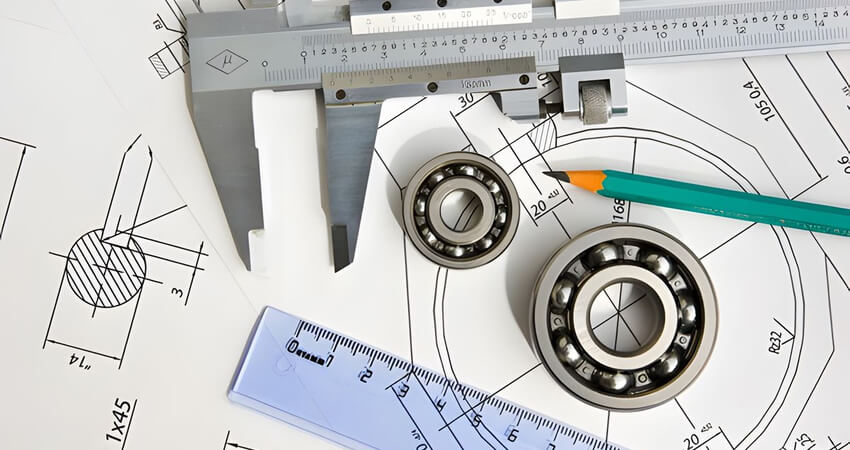
4.Why do you prepare technical drawings when sourcing parts?
Engineering or technical drawings are at the heart of product manufacturing. They have been around for centuries before the recent advent of digital manufacturing technology.
These drawings provide essential information such as technical information and engineering design during the machining of a product. Technical drawings are used in CNC machining to manufacture accurate parts, reduce costs and improve communication between machinists, product designers and manufacturers.
Before the advent of computers, technical drawings were the main reference point for manufacturers. Today, however, product teams can design a part on a computer and share it with a CNC machine, which will manufacture the item, without having to create a technical drawing.
But why do manufacturing projects require technical drawings? Here are some reasons why manufacturing work requires technical drawings:
1) Verification
Machining or technical drawings help verify the details of the CAD file, giving product manufacturers confidence that they can manufacture the product precisely to specification. If the CAD file matches the machining drawing exactly, there are no errors in the design.
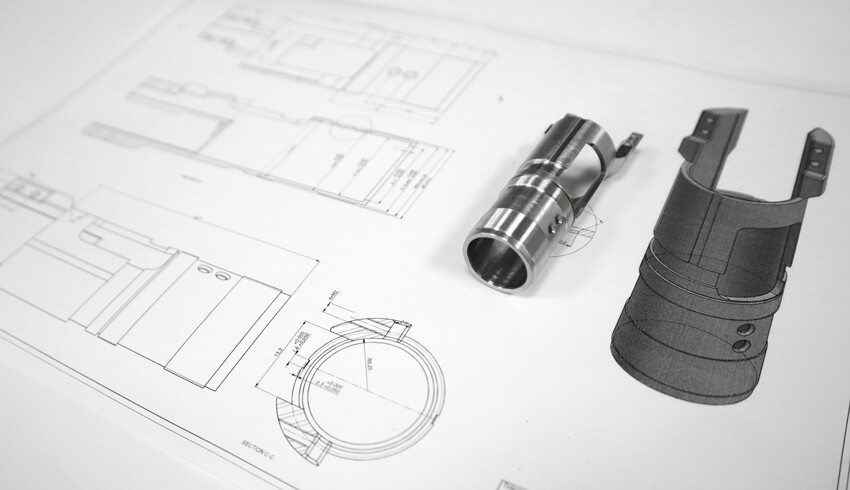
2) Quick Reference Point
Most product manufacturers prefer to receive technical documentation in the form of digital files because technical drawings can be used as a reference for checking after the part is completed. These drawings help evaluate various aspects of the part, including its value, geometry, and potential cost.
5.Additional Information
Technical drawings provide a lot of additional information that is not included in the CAD file. Technical drawings may often contain other relevant details, such as material specifications for a specific component, internal or external threads, specific feature tolerances, and individual surface finish requirements.
1) Legal Instruments
Machining drawings have a legal function. These CNC technical drawings are included in the purchase order; therefore, they are part of the contract. Therefore, if the manufacturer fails to deliver the part exactly as per the specifications, the drawings show that the design has not been achieved. At the same time, the manufacturer is free from liability as long as they adhere to the submitted drawings.
2) Global Recognition
Technical drawings are the only internationally recognized means of communicating engineering instructions. There is no confusion, ambiguity, or potential complexity that could affect the success of the project.
6.Why is Precision and Accuracy in Machining Drawings Critical?
Since CNC machining drawings communicate the design of the part between the manufacturer, designer, and engineer, errors that would cause the machined part to not meet the required specifications are not allowed.
Here are the reasons why precision and accuracy are key to technical drawings in the machining industry:
1) Reduce Waste
Machining parts that do not meet the required specifications can waste material, time, and effort. Accurate technical drawings ensure that the product is properly machined, which reduces waste. Therefore, this reduces the need to rework parts, which can be costly.
2) Meet Quality Standards
Manufacturers can meet stringent quality standards with accurate, precise technical drawings. Manufacturing parts to the required design specifications also helps avoid errors or defects that could cause failures and ensures that the machined parts function properly.
3) Ensure product functionality
When the details on the technical drawings are accurate, machinists can easily manufacture parts that function as expected. Any deviation from the required specifications will cause potential problems on the production line and the part will not function properly.
4) Common standards for machining drawings
Machining and engineering drawings follow different recognized standards. These standards guide the presentation of technical drawings and promote effective communication between all parties.
The American Society of Mechanical Engineers designates its drawing standards as Y14.5 and Y14.5M. The International Organization for Standardization recommends the use of ISO 8015 for engineering drawings and ISO 128 for technical drawings. ISO 128 follows the ISO document and provides general rules for the execution of technical drawings, which are applicable to machining drawings in the fields of mechanical engineering, shipbuilding, architecture, and construction.
7.How to add threads to machining drawings
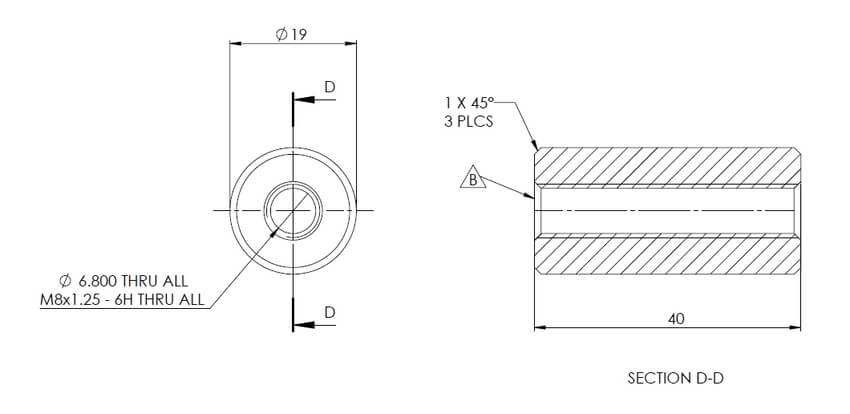
If your part contains threads, the threads must be indicated and defined on the CNC machining drawing. You should define these threads by indicating standard thread sizes (such as M4x0.7) rather than diameter sizes.
Be sure to provide detailed thread callouts to clarify the drawing and allow for the specification of pilot holes and threads of varying lengths.
- The first operation is to specify the thread type, size, and pitch.
- Define the thread specification using appropriate symbols or notes. These symbols usually consist of a triangle with parallel lines inside, indicating the V-groove of the thread. The pitch of the thread is usually indicated next to the symbol.
- Ensure that the line is placed in the proper location and is accurately proportional to the rest of the drawing.
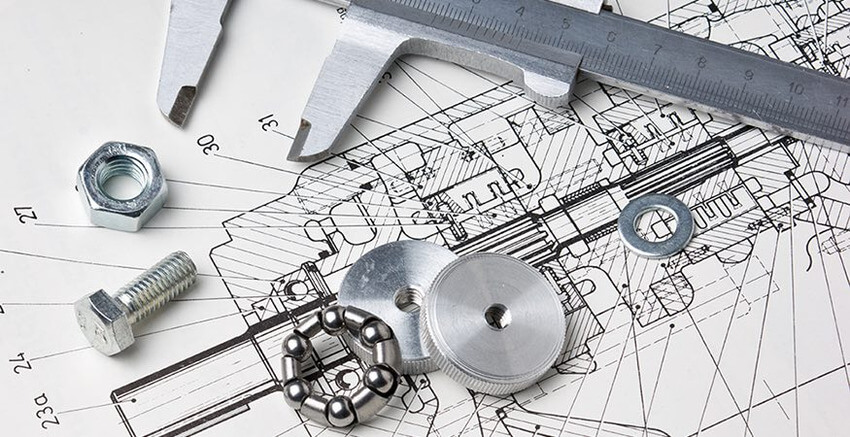
8.How to add hole callouts in CNC technical drawings?
Adding hole callouts in technical drawings is essential for producing detailed and accurate manufacturing documentation. A typical hole callout provides detailed information about the size and location of a hole in a specific part.
Follow these steps when adding hole callouts in technical drawings:
- Identify the holes that need to be detailed.
- Draw a centerline through the middle hole and draw an arc to represent the perimeter of the hole.
- Label the holes with relevant hole callouts according to the standards and specifications of the project.
- Make sure to include key features such as tolerances, diameters, and hole depths.
9.How are tolerances specified on machining drawings?
Tolerances are expressed using various formats on the main orthogonal views. These machining tolerances specify the acceptable range of deviations in the numerical value of a specific part dimension.
Tolerances are especially important for complex features that interact with other components in an assembly. They often have different formats and apply to any dimension on a CNC machining drawing. For example, bilateral tolerances are the most straightforward and are symmetrical around the basic dimension. Single-sided tolerances have upper and lower limits in technical drawings.
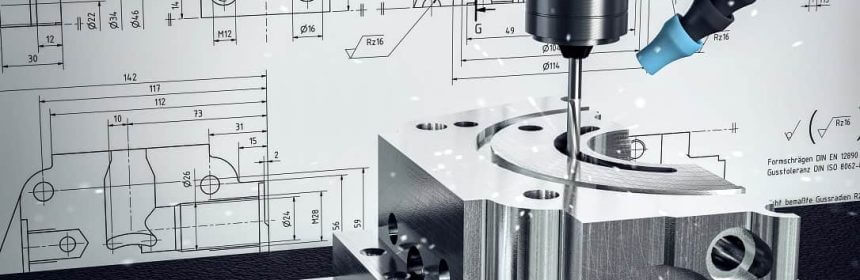
10.What is Geometric Dimensioning and Tolerancing in Technical Drawings?
Geometric Dimensioning and Tolerancing (GD&T) is an advanced system used by manufacturers and product designers to clearly indicate and communicate machining tolerances.
These symbols and specifications in machining drawings share the required design specifications, ensuring that manufacturers build parts according to customer preferences. GD&T symbols typically include roundness, flatness, straightness, parallelism, position, and perpendicularity. Traditional dimensioning is often confusing as dimensions can be easily misinterpreted between machinists and product designers.
Hence, GD&T is essential for precision CNC machining as it helps produce parts with the highest accuracy and precision. GD&T provides clear guidance for measuring and creating parts within the allowed tolerances, eliminating any guesswork. As a result, it ensures optimal efficiency in the production process, ensuring fewer errors and defects in CNC machined parts.
11.Considerations when preparing technical drawings
Here are helpful tips to consider when compiling an ideal machining drawing that a machine shop will be able to decipher at a glance:
- Use standard templates ISO, ASTM, and DIN as they are the most commonly used templates and are understood by manufacturers and machinists worldwide.
- Place orthogonal projections in the center of the drawing, leaving enough space to accommodate dimensions.
- Consider adding section views to your machining drawings to show hidden features or complex components.
- Use different types of construction lines and dimensions to communicate different design features. For example, dashed lines make hidden features more obvious to machinists.
- Add tolerance values to all critical components and design features such as holes and threads.
- Include additional information or instructions that may help the manufacturer complete the project.
- Make sure to export the finished technical drawing in PDF format and share it with the manufacturer. Modern machine shops allow you to upload drawings to their website while they provide a quote for your manufacturing project.
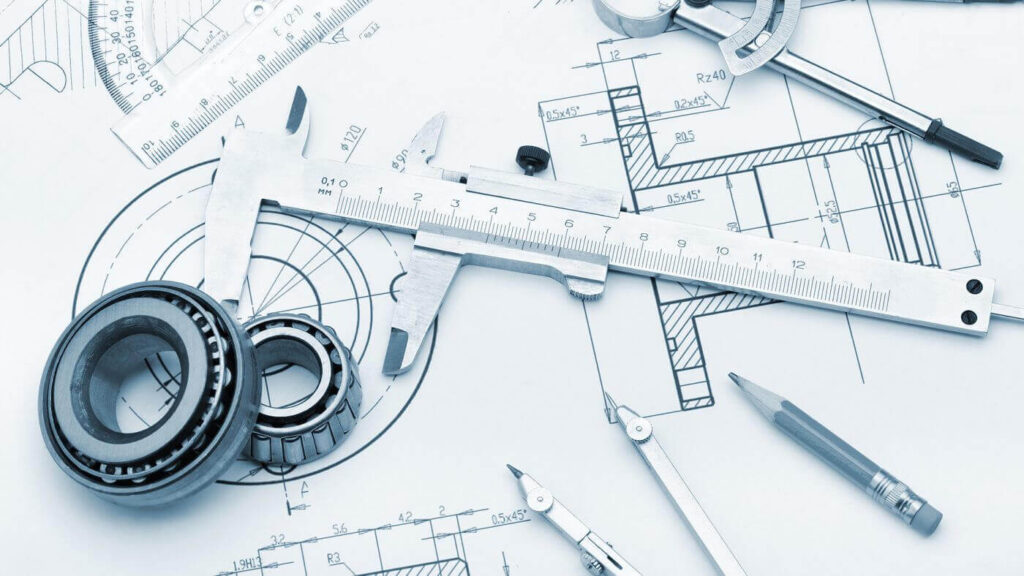
12.Conclusion
Machining drawings are generally good practice in the product manufacturing industry. It is a core quality control mechanism that enables machinists and inspectors to produce parts precisely to the customer’s specifications.
However, there are different technical or engineering drawings, each of which serves a different purpose in the product design and manufacturing process. Therefore, understanding these machining drawings helps ensure that the dimensions of the product are not misinterpreted at any stage.