The critical role of CNC machining in electric vehicles manufacturing
In today’s rapidly developing electric vehicles (EV) industry, CNC (computer numerical control) machining technology has become a key factor in improving performance, safety and sustainability. This article will take a deep look at the applications, advantages, challenges and solutions of CNC machining in electric vehicle manufacturing, as well as its impact on the future development of the automotive industry.
1.Application of CNC machining in electric vehicles
1.Battery components
The battery system, the heart of electric vehicles, relies on CNC machining technology to manufacture key components such as battery housings, battery holders, and thermal management systems. These components not only provide structural support, but also ensure thermal control and safety of the battery pack, which is the basis for the performance and safety of electric vehicles.
2.Motor components
Electric vehicles require powerful electric motors to drive, and CNC machining can be used to produce numerous motor components. These include motor housings, rotor shafts, stator assemblies, and heat sinks. These components are designed to maximize the power, efficiency, and durability of the motor system.
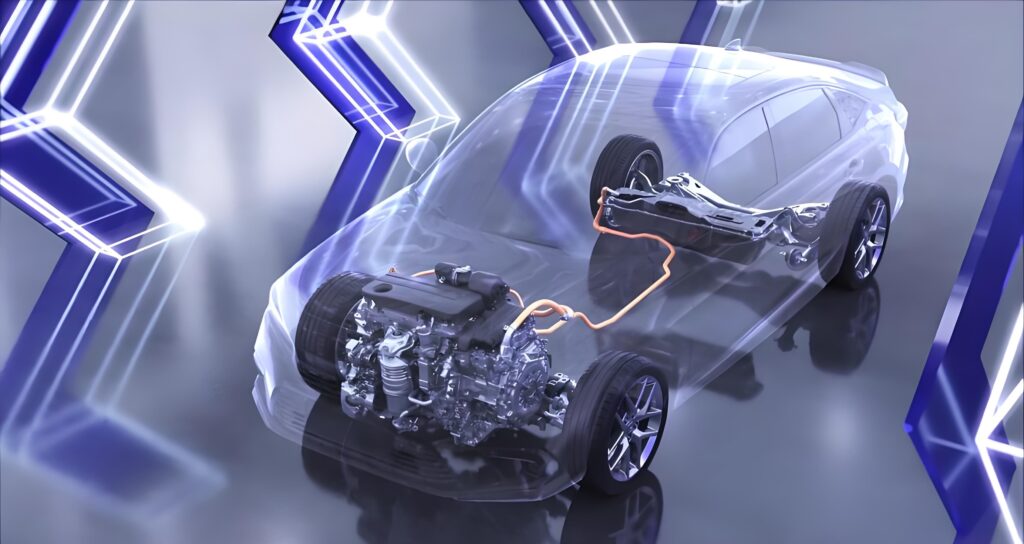
3.Charging infrastructure
CNC machining is used to produce charging infrastructure components such as charging connectors, sockets, and mounting brackets. These precision-machined parts are essential for convenient charging of .
4.Powertrain components
CNC machining plays an important role in manufacturing powertrain components of electric vehicles, such as transmission housings, differential gears, drive shafts, and transmissions. The efficient and reliable transmission of these components is key to the power output of electric vehicles.
5.Structural components
The structural components of electric vehicles, including chassis components, suspension components, and frame reinforcements, rely on CNC machining to achieve their precision design. These components are essential to the rigidity, stability, crash resistance, lightweight and energy efficiency of the vehicle.
6.Interior and Exterior
CNC machining can also manufacture interior and exterior parts of electric vehicles, such as dashboards, door handles, grille inserts and decorative accessories, enhancing the overall appearance and functionality of the vehicle and demonstrating the industry’s pursuit of design excellence.
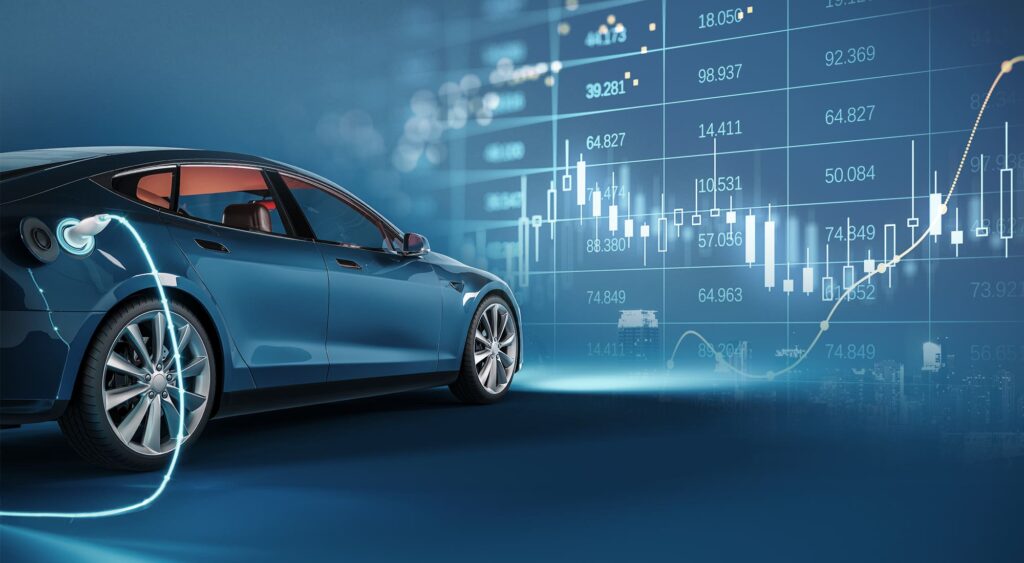
7.Regenerative Braking System
CNC machining technology also plays a key role in manufacturing components for electric vehicles regenerative braking systems, such as brake calipers, rotors, pads and brake discs. Precision machining of these components helps optimize braking performance, energy recovery and driving efficiency.
2.Advantages of CNC machining parts for electric vehicles
1.Precision
CNC machining has extremely high precision and accuracy, and can precisely control the size and shape of parts to ensure that the parts meet the strict tolerance requirements required for electric vehicles applications.
2.Versatility
CNC machine tools have strong machining capabilities and can produce parts of various complex shapes and geometries, which are widely used in the manufacture of various parts used in electric vehicles. Whether it is a body structure with unique curves and surfaces, or a delicate and complex internal electronic component mounting seat, CNC machining can easily handle it.
3.Efficiency
CNC machining has efficient production capabilities and can quickly produce parts while minimizing material waste. Through optimized machining programs and tool path planning, CNC machine tools can complete the machining of complex parts in a short time, improve production efficiency, and shorten the production cycle of electric vehicles.
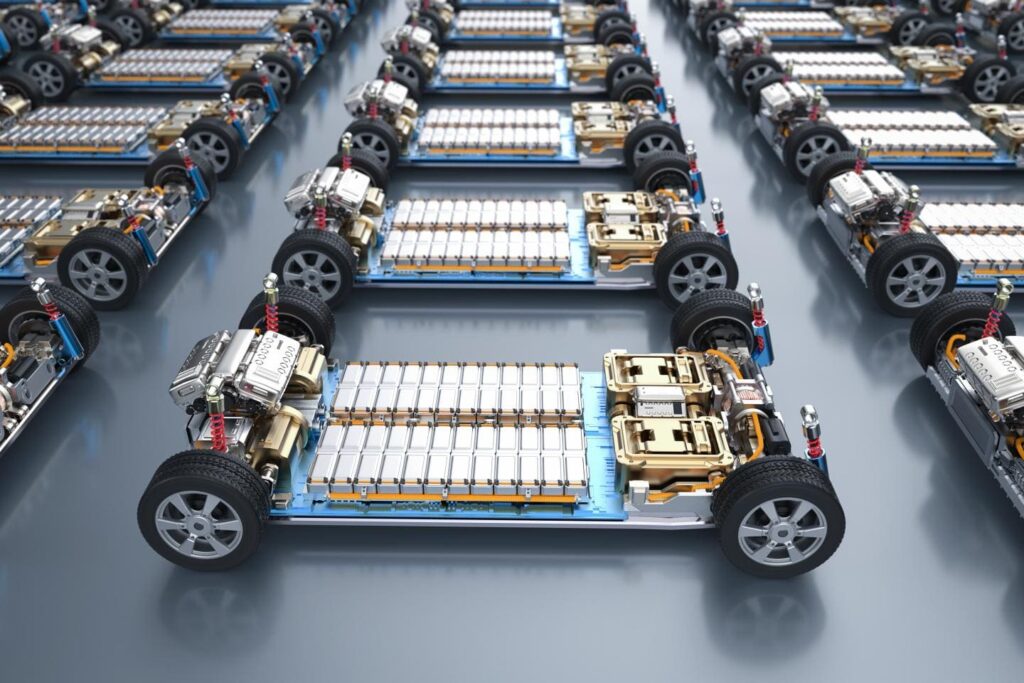
4.Customization
CNC machining allows parts to be customized according to the specific design requirements and performance standards of electric vehicles manufacturers. CNC machining can meet personalized needs and realize customized production of parts.
5.Material compatibility
A variety of materials commonly used in electric vehicle parts, such as aluminum, steel, and composite materials, can be processed on CNC machine tools. CNC machine tools can select appropriate tools, cutting parameters and processing technologies according to the characteristics of different materials to ensure the processing quality and performance of parts.
6.Scalability
CNC machining is easy to expand and is suitable for prototyping and mass production of electric vehicle parts. In the product development stage, CNC machining can quickly produce part prototypes for testing and verification, accelerating the product development cycle.
7.Consistency
CNC machining can ensure consistent quality and repeatability of parts from batch to batch. In electric vehicle manufacturing, the quality consistency of parts is crucial to the performance and reliability of the entire vehicle.
8.Cost-effectiveness
Although the initial setup cost of CNC machining is relatively high, in the long run, it can provide significant cost benefits through high production volume, reduced labor demand and reduced waste. High production volume can reduce the production cost per part, reduce labor demand and reduce labor costs, while reducing waste improves material utilization and further reduces total costs.
3.Challenges and solutions for CNC machining of electric vehicle parts
1.Material selection
Challenges: Electric vehicle parts are often made of advanced materials such as aluminum alloys, composite materials and high-strength steel, which are difficult to process.
Solution: Use advanced tools, such as special cutting tools and tool coatings designed for difficult materials; optimize machining parameters, adjust cutting speed, feed rate and cutting depth to adapt to material characteristics.
2.Component complexity
Challenges: Electric vehicle parts have complex shapes and tight tolerances, requiring precise machining capabilities.
Solution: Use advanced CAD/CAM software to program complex tool paths and optimize machining strategies; implement multi-axis CNC machining functions to machine complex features from multiple angles.
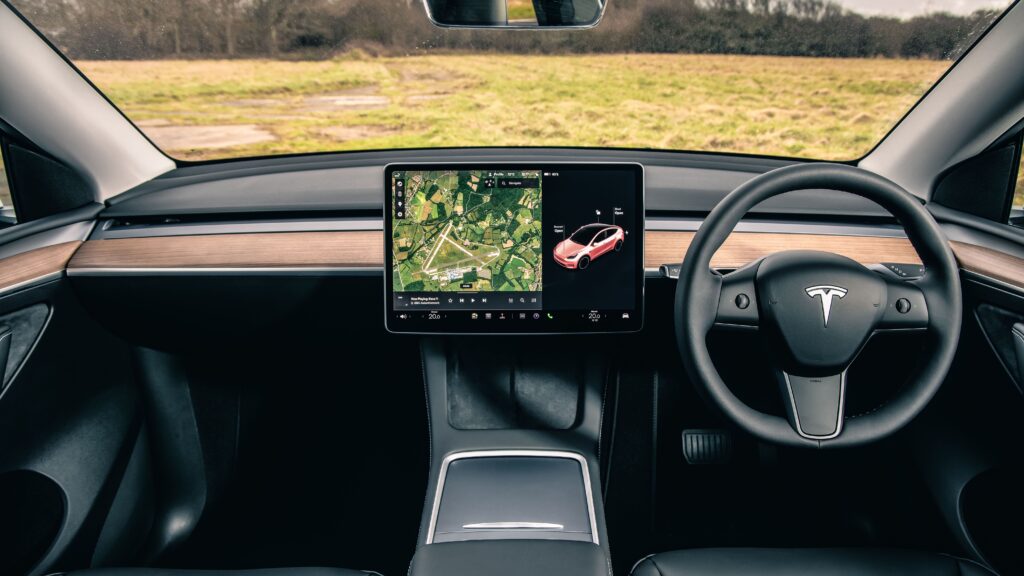
3.Thermal management
Challenges: Machining generates heat, which can easily lead to thermal deformation and dimensional inaccuracy of parts machined from materials such as aluminum.
Solution: Use efficient cooling systems to dissipate heat and maintain stable machining temperatures to reduce thermal deformation; use cutting tools with built-in cooling functions or external cooling methods to control tool temperature.
4.Environmental impact
Challenges: Electric vehicle manufacturers need to reduce the impact of production processes (including CNC machining operations) on the environment.
Solution: Adopt environmentally friendly processing practices, such as recycling metal scraps and using environmentally friendly cutting fluids; invest in energy-saving CNC machining equipment and technology to reduce energy consumption and carbon emissions.
5.Supply chain resilience
Challenge: Electric vehicle manufacturers rely on a global supplier network and face supply chain risks.
Solution: Diversify suppliers and source from multiple suppliers and regions; consider localized manufacturing and establish localized processing facilities or partnerships.
6.Quality assurance
Challenge: Electric vehicle parts must meet strict quality standards and performance requirements to ensure reliability and safety.
Solution: Use advanced testing technologies, such as coordinate measuring machines and non-destructive testing methods to ensure part size and integrity; establish a strong quality management system and process to continuously monitor and improve processing quality.
Summary
CNC machining technology plays an integral role in electric vehicle manufacturing, improving the performance and safety of electric vehicles while also promoting the sustainable development of the industry. As the electric vehicle industry continues to expand, CNC machining will continue to serve as a cornerstone of technological innovation, driving breakthroughs in automotive design, performance, and efficiency, paving the way for a cleaner, greener transportation future.
If you need an experienced CNC machining manufacturer, Xavier is your best choice. The Xavier team is well-equipped to provide high-quality CNC machining solutions to meet your personalized machining needs. Please feel free to contact us for more information or to discuss your machining needs.