CNC Machining Metal: How It Works and the Best Types of Metals
Metals, plastics, and composites are some of the engineering materials that can be chosen for part production when using Computer Numerical Control (CNC) machining. However, metals are the most widely used CNC engineering material across a variety of industries. Including magnet machining.
In this article, we will focus on machining processes for CNC machined metals, different metalworking operations, and typical metals suitable for CNC machining. Read on.
1.The Role of CNC Machining in Metal Part Manufacturing
In metal production, CNC machines and machining play a variety of roles. More precisely, they are used to perform several basic tasks, such as:
1) Metal Prototyping
A lot happens before a part is produced, from important steps like creating a CAD design to virtually testing and analyzing the design.
But in order to evaluate the functionality of a concept, manufacturers need a metal prototype. While there are many processes used in prototyping, manufacturers often need CNC machining to complete it quickly.
Using CNC machining for metal prototyping ensures repeatability and consistency. It also offers high precision and time-saving features while being cost-effective.
Another benefit of using CNC machining for metal prototypes is the versatility of the process, as it works with a wide range of metal and non-metal materials.
2) Small-batch production
Small-batch or small-volume CNC metal machining parts refers to the production of parts or products in small batches, usually ranging from 10 to 1000 pieces.
This is a method used by manufacturers to reduce the cost of metal production. Small-batch production reduces CNC machining costs and facilitates design changes without loss.
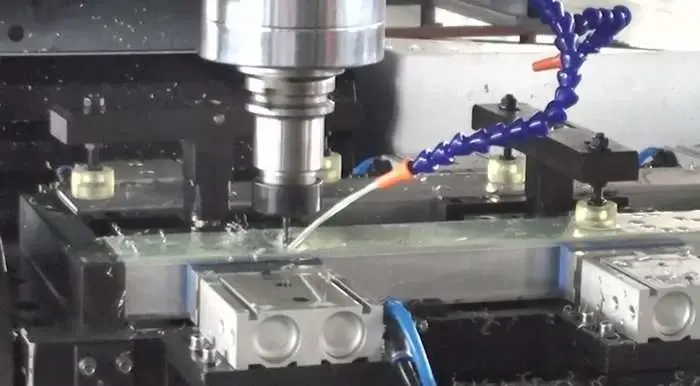
2.How does CNC machining metal work?
1) CAD design
The first step is to create a computer-aided design (CAD) in 2D or 3D format using CAD software. The software can render any part that meets the necessary technical specifications.
It must be remembered that the characteristics of the metal workpiece have a great influence on the design and results.
2) Programming
The CAD file then needs to be converted into a file format that is compatible with the computer numerical control (CNC) machine. Computer-aided manufacturing (CAM) software examines the CAD file and generates programming code.
The codes are broadly divided into two categories: machine code (M code) and geometry code (G code).
3) Machine setup
There are two steps required to set up a CNC machine. First, you need to make sure the machine is in good working order by doing a thorough inspection.
The next step is to securely attach the metal workpiece to the machine. After attaching the necessary equipment and parts, the metal workpiece can be inserted directly into the machine.
4) Machining the Metal Workpiece
After configuring the CNC machine, you can start the CNC program. The CNC program represents the core of the CNC machine’s functionality. It directs the machine’s movements and actions to produce the desired results, ensuring that the machined metal parts meet the manufacturer’s specifications.
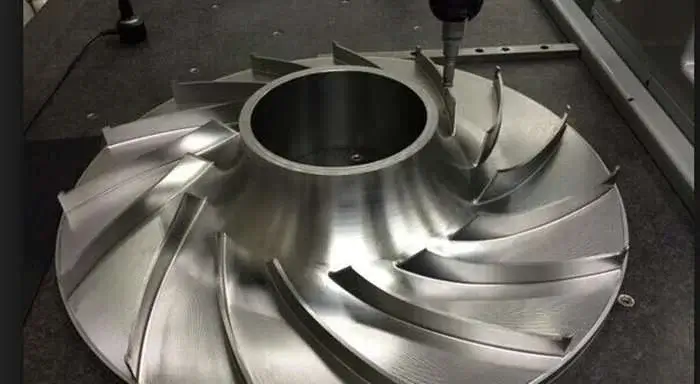
3.Common Types of Metals for CNC Machining
There are many types of metals and alloys used in the CNC machining of metals, but here we will only discuss the most common ones. They include:
1) Steel
Steel is one of the most popular metals used in precision CNC machining. It is an alloy that contains up to 2% carbon, iron, and various additional elements in varying proportions.
There are four main types of steel used in CNC machining: carbon, stainless steel, alloy, and tool. It is worth noting that these steel types have subcategories and grades. For example, stainless steel comes in grades 304, 316, 410, 430, and 2205.
Still, if your machine parts will be used in a humid climate, steel may not be the best metal choice as it can corrode easily.
2) Aluminum
Similar to steel, aluminum is popular for its applications in many different fields. However, aluminum’s corrosion resistance and lightweight properties set it apart. Typically, aluminum is 2.5 times less dense than steel and is less likely to break during CNC machining.
Common aluminum alloys used in CNC machining include 2024, 6061, and 7075. There are also some less common aluminum alloys used in CNC machining, including 3003 and 5052.
3) Brass
Zinc and copper are the two metals that make up brass. Brass is known for being stable, strong, moderately hard, and easy to machine. Unlike most soft metals used in CNC machining, brass alloys do not put unnecessary strain on machinery.
Unlike most soft metals used in CNC machining, brass alloys actually do not put unnecessary strain on machinery. There are several types of brass alloys used for CNC machining, including C360, C230, and C220.
Brass is susceptible to stress corrosion cracking, which can be a serious problem, especially in the presence of ammonia or ammonia solutions. To overcome this limitation, the workpiece must be heat treated during post-processing, such as annealing.
4) Copper
Copper is one of the metals frequently used in various industries, with excellent surface quality, strong electrical and thermal conductivity, and excellent machinability.
CNC machined copper parts are often used in circuit boards and electromagnets in the electronics and semiconductor industries. However, the main disadvantage of copper alloys is that they are easily corroded by sulfides, halogens, and ammonia-containing solutions.
5) Titanium
Titanium metal is a highly sought-after metal in many industries due to its excellent strength-to-weight ratio and corrosion resistance. In addition to being slightly more expensive, CNC titanium machined parts are of excellent quality. It is also suitable for almost all surface treatment techniques such as electrophoresis, powder coating, and sandblasting.
Titanium for CNC machining comes in different grades, including grades 1, 2, 3, 4, 11, and 12. These grades have different strengths, corrosion resistance, and formability.
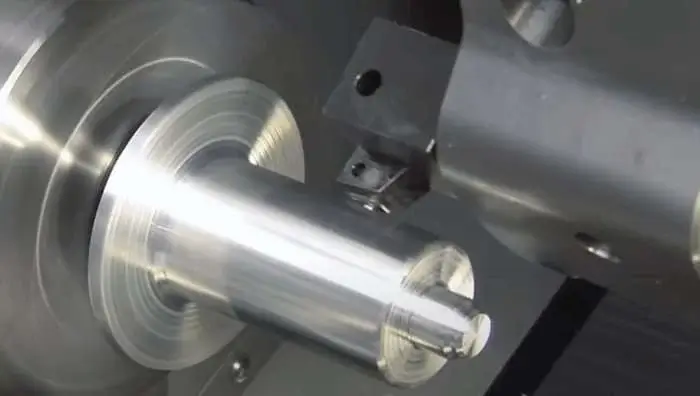
4.Different CNC Processes in Metalworking
Different CNC processes are used in metalworking. The most typical examples of CNC machining processes include:
1) CNC Milling
During the milling process, a rotating, multi-point CNC cutting tool is used to remove material from the workpiece. With CNC milling, the workpiece is usually fed into the cutting tool by the CNC machine in the same direction as the cutting tool is rotating.
The milling of a metal workpiece is a specific shape that requires a rotating, multi-point cutting tool. Chamfer mills, end mills, and spiral mills are milling cutters that can be oriented vertically or horizontally.
2) CNC Turning
CNC turning is an extremely precise subtractive machining method that works on the same principle as a lathe. The cutting tool is pressed against the rotating workpiece to remove material and provide the desired shape.
The turning center or lathe remains in place while the raw material rotates rapidly. The single-point cutting tool helps shape the material as the workpiece rotates along the axis motion of the dual CNC lathe. The input computer program controls the turning center or lathe, thus ensuring the manufacturing of high-precision parts.
3) CNC Drilling
The drilling process uses a multi-point drill bit to drill cylindrical holes in a metal workpiece. Furthermore, by feeding the rotating drill bit into the machine perpendicular to the surface of the workpiece, drilling creates vertically aligned holes with the same dimensions as the drill bit used for the operation.
For angular drilling operations, this involves specific machine settings and workpiece holding systems.
4) Electrospark Machining
Arc discharge, or EDM for short, is used in electrical discharge machining (EDM) to create micro-dimples, which can quickly achieve full cuts.
Sometimes also called spark machining, EDM is used in situations where precise tolerances and complex geometric patterns are required in hard materials. However, its application is limited to metal alloys as it requires the substrate to be conductive.
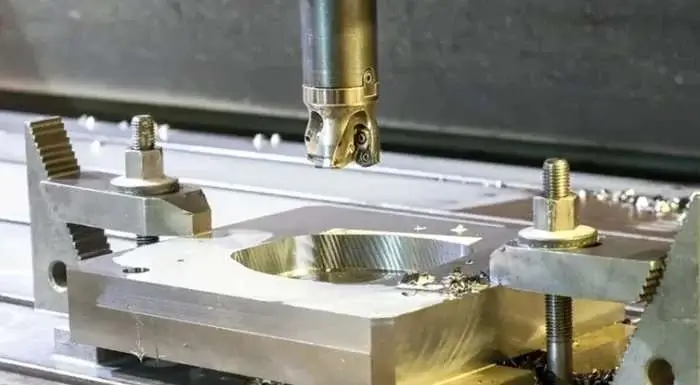
5.Advantages of CNC Machined Metal Parts
CNC machined metal parts have certain advantages that cannot be achieved with injection molded or 3D printed parts. These are some of the main advantages of machining metal parts.
1) Excellent Prototyping
Because metal machined parts can be made in one go, they are very useful and affordable for metal prototypes.
In addition, machining is faster than molding, so R&D teams can quickly cycle through multiple iterations of a project, then test and evaluate as needed before moving into production.
2) Part Quality Consistency
When manufacturing CNC metal machined parts, high standards can be achieved. Perhaps more importantly, customers can set tolerances that machinists must adhere to. This means that machine operators or machinists can spend time machining components and details with precise tolerances.
Although injection molds can produce parts with extremely tight tolerances, not every mold can maintain this standard. The tolerances achieved on parts produced early on are usually gone by the end of the mold’s life.
3) Part Strength
CNC machined metal is stronger than other manufacturing processes such as 3D printing, where materials are stacked on top of each other and may be weaker along one axis. This is because CNC machining is a subtractive process that involves making the desired part by cutting away material from a solid block, which creates a part with uniform strength.
In addition, CNC machined metal parts are generally stronger than molded parts. This is because most molded parts are mechanically limited due to the thin wall requirements.
4) Faster Lead Time
CNC machining is one of the fastest metal manufacturing processes available today, which reduces lead time. The manufacturing process is also very efficient, which helps to some extent in reducing lead time.
Because machining is a single-step process and CNC machining centers operate quickly, machined metal parts are easy to manufacture (in small batches), which reduces lead time and speeds up product launch.
5) Better Surface Finish
Metal machined parts are free of surface quality issues generated during the molding process, such as parting line blowout, jetting, and flow marks. Machined parts require only minimal post-processing to achieve extremely high surface quality standards.
In addition, machining produces a better surface finish than 3D printing, even without post-processing. Grinding or chemical treatment is necessary to smooth out any noticeable layer lines that 3D printing (especially FDM printing) may leave on the surface of the part. These layer lines are not present in machined items.
6) No Minimum Order Quantity (MOQ)
One of the main advantages of CNC machining metal is that it is able to produce parts with no minimum order quantity. Molded parts require the creation of metal molds, a labor-intensive operation that often costs tens of thousands of dollars.
On the other hand, since machined parts are cut directly from blank workpieces, it is affordable to order very small quantities or even one-off parts.
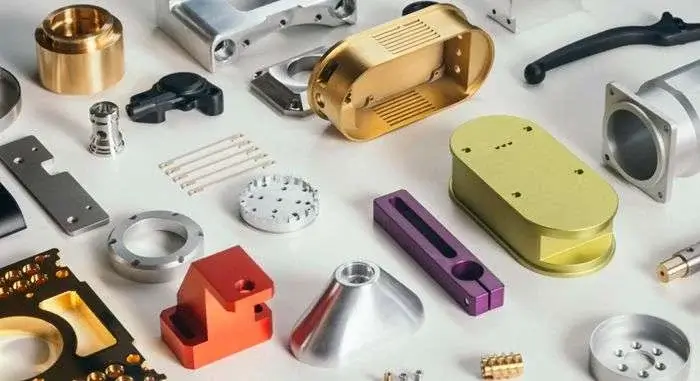
6.Surface Finishing Options for CNC Metals
After machining, metal parts can be treated to change the texture and appearance of their surfaces. Surface treatments can have practical or aesthetic purposes. Surface finishing options for CNC metals include:
- Anodizing
- Powder coating
- Sandblasting
- Aluminum oxide coating
- Black oxide coating
- Plating
- Passivation
- Brushing
- Polishing
7.Types of CNC Machines Used to Machining Metals
In modern metalworking equipment, there are various types of CNC machines. These include the following:
1) CNC Lathes
This machine manufactures metal parts by spinning a metal workpiece on a spindle. As the material turns, cutting tools are used to shape the part into the appropriate shape. They are perfect for producing symmetrical products with conical, spherical, or cylindrical geometries.
2) CNC Grinding Machines
Grinding machines grind materials by using a rotating wheel to grind or grind them into the desired shape. The tool rotates in place while the workpiece (usually mounted on the machine table) moves along the X, Y, and Z axes.
3) CNC Milling Machines
This type of CNC machine can achieve higher metalworking accuracy than manual machining. Cutting depth, angle, and direction changes can be programmed into CNC milling machines. CNC milling machines come in many types, including vertical, horizontal, and multi-axis milling machines.
4) CNC Drilling Machines
CNC technology can control complex drilling machines to ensure accurate drilling of holes in a variety of metal materials. Peck drilling, also known as interrupted cut drilling, is a systematic process for drilling holes in thick metals.
In addition, CNC turret drilling machines have a large number of drill bits and cutting tools mounted on the turret. Automation allows the tools required for drilling to be quickly and accurately positioned in place.
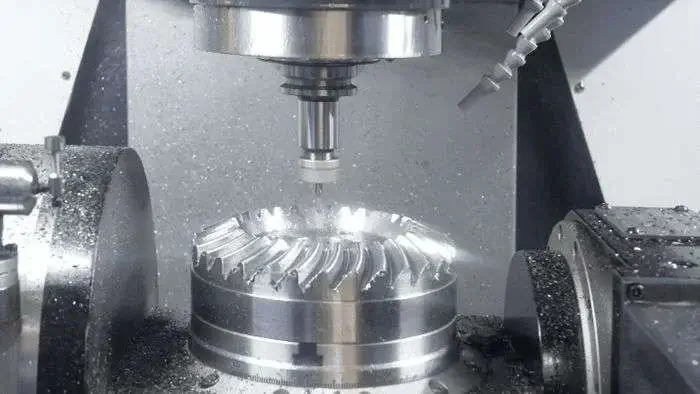
8.Various Applications of Metal CNC Parts
The precision, adaptability, and durability of metal CNC parts make them useful in a variety of industries. Let’s look at a few major industries where CNC machining is essential:
1) Aerospace Industry
Aerospace metal machining is essential to the industry. It ensures the precise manufacturing of metal aircraft parts, which is critical to safety. Engine mounts, landing gear components, fuel access panels, and fuel flow components are all examples of machinable aerospace parts.
2) Automotive Industry
The automotive industry often uses CNC milling machines for production and prototyping. Extruded metal can be milled into parts such as axles, gearboxes, valves, and cylinder blocks.
3) Defense Industry
CNC machining ensures precision and reliability in defense equipment. CNC is suitable for metal parts such as radar, weapons, and communication equipment.
4) Healthcare Industry
CNC machining is necessary for diagnostic tools, surgical instruments, and medical implants. For patient safety, CNC metal parts must be highly accurate and biocompatible.
5) Oil and Gas Industry
The research, improvement, and construction of pipelines all involve CNC metal machining. The company produces parts for drilling equipment, pumps, and valves.
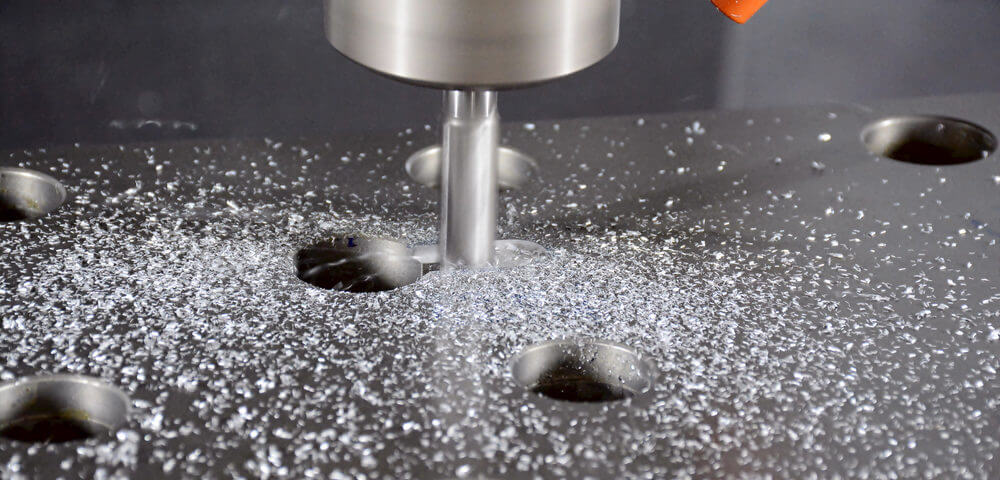
9.Conclusion
One of the most important aspects of the industrial sector is metal CNC machining, which provides precise results for a wide range of components. The power and flexibility of CNC machining metal ensures consistent results regardless of the scale of production and the type of metal used.
If you are looking for an experienced CNC machining manufacturer, Xavier is your ideal choice. The Xavier team is well-equipped to provide high-quality CNC machining solutions. If you need more information or to discuss your machining needs with us, please feel free to contact us.