A Basic Introduction to CNC Machining of Polymers
This article explores CNC machining as a method for manufacturing plastic parts. It covers compatible materials, available post-processing operations, and compares polymer CNC machining to 3D printing.
CNC machining is a very versatile manufacturing process. In addition to being able to machine rigid materials such as metals and wood, it is also well suited to machining polymers. Plastics are machined in many ways similarly to all other materials. However, there are some key differences. These differences include the cutting tools, speeds and feeds, cutting fluids (primarily air), and the surface finish of the manufactured part.
1.Polymer CNC machining or 3D printing?
Many customers consider 3D printing to be a valid alternative to polymer CNC machining. There are certain factors you need to be aware of when choosing between these two manufacturing methods for a particular project.
1) Build size
The build size of CNC machining is much larger than that of 3D printing. Our partner network includes manufacturers with build sizes up to 1.625.6 x 812 x 965.2 mm for CNC machining, while 3D printing (FDM) has a build size of 600 x 900 x 900 mm. For making large parts out of plastic, CNC machining is superior.
2) Mechanical properties
Most 3D printing processes build parts layer by layer. As a result, the mechanical properties of the manufactured parts are affected. In many applications, this is not a problem. However, some applications require plastic parts to have excellent mechanical properties. CNC machining does not affect the mechanical properties of the machined parts, so the process is well suited for making plastic parts for applications that require good mechanical properties.
3) Dimensional accuracy
CNC machining offers better dimensional accuracy (up to ±0.025 mm). It offers tight tolerances and is ideal for holes, overhangs, bridges, and other difficult-to-print features.
4) Surface Quality
The machined surface roughness standard for polymer CNC parts is 3.2 μm, while 3D printing technologies such as FDM, SLS, HP MJF, etc. generally produce lower roughness.
5) Number of Parts
Due to its repeatability, speed, and dimensional accuracy, CNC machining is a better choice than 3D printing for large numbers of identical parts (>10). However, for prototyping and very complex parts, 3D printing may be a better solution.
6) Price
For prototyping and small numbers of parts, 3D printing is cheaper. However, for more than 10 identical parts, CNC machining is generally a cheaper option.
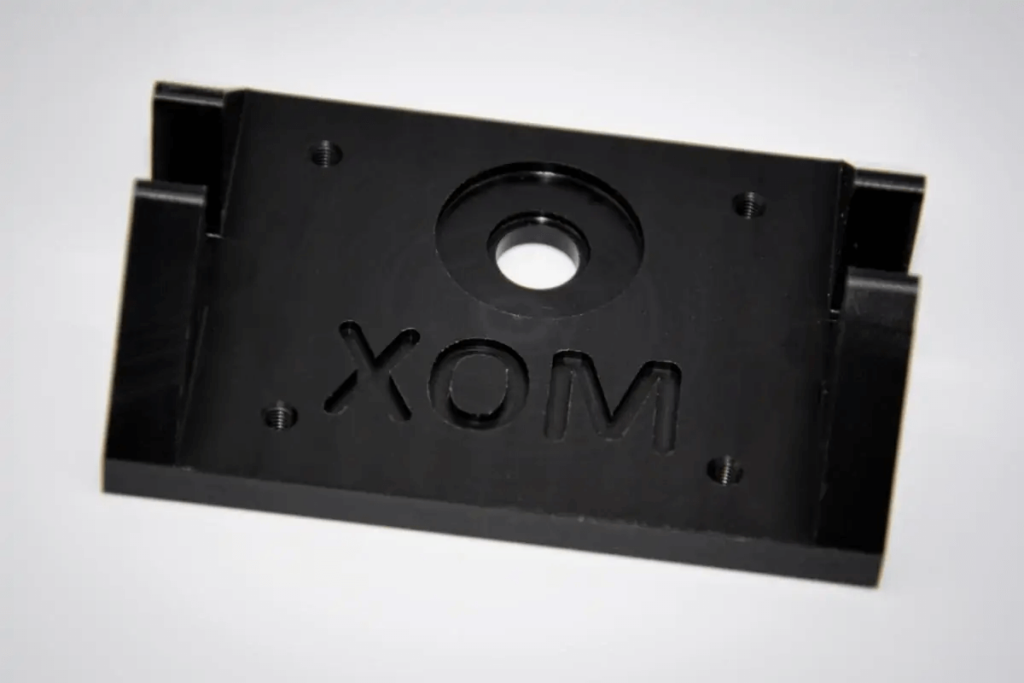
2.Materials
Here are some polymers that can be effectively machined and are available for instant quotes on our platform.
- Anti-lock Braking System
- Acrylic Fiber
- Polyoxymethylene / Polyoxymethylene / POM
- Nylon / Polycaprolactam
- PEEK / Polyetheretherketone
- Polytetrafluoroethylene / Teflon
- PC / Polycarbonate
- UHMW PE / Ultra-high Molecular Weight Polyethylene
3.Post-processing
CNC machining can produce parts suitable for post-machining. The standard surface roughness produced by the process is 3.2 μm. This can be as fine as 0.4 μm. However, post-processing may be necessary for a variety of reasons. These include improving the surface finish and improving aesthetics. The following are some post-processing operations that can be performed on CNC machined plastic parts.
1) Shot Peening
After machining, there may be some loose plastic threads remaining on the body of the part. Shot peening is used to remove these threads and produce a smooth surface finish.
2) Dyeing
Dyeing is a common operation used to change the color of a part. Dyeing is available in a variety of colors, but please note that some materials have more color options than others. See our Materials Guide for more information.
3) Painting
Painting is used to give mechanical parts a shiny finish. It can also improve certain physical properties, such as wear resistance.